Laser engraving is a process used to mark materials with a laser beam. It is used in the automotive, medical, and manufacturing industries while also being extensively used for artistic or aesthetic applications. In most cases, engraving is used because of its ability to produce durable, high-contrast markings. It's a common request from Xometry customers.
This article will describe what laser engraving is, how it works, and what materials are easiest to engrave.
What Is Laser Engraving?
Laser engraving is a noncontact process that can create easily visible markings on a variety of materials by making use of a laser beam. It can reproduce highly intricate designs due to the fact that the beam is focused to a spot size of as small as a few microns depending on the focal point settings. Laser engraving is often used to produce artistic designs, signboards, industrial labels, and personalized apparel. The laser engraving process produces high contrast between the engraved and unengraved portions of a design, as can be seen in Figure 1 below:
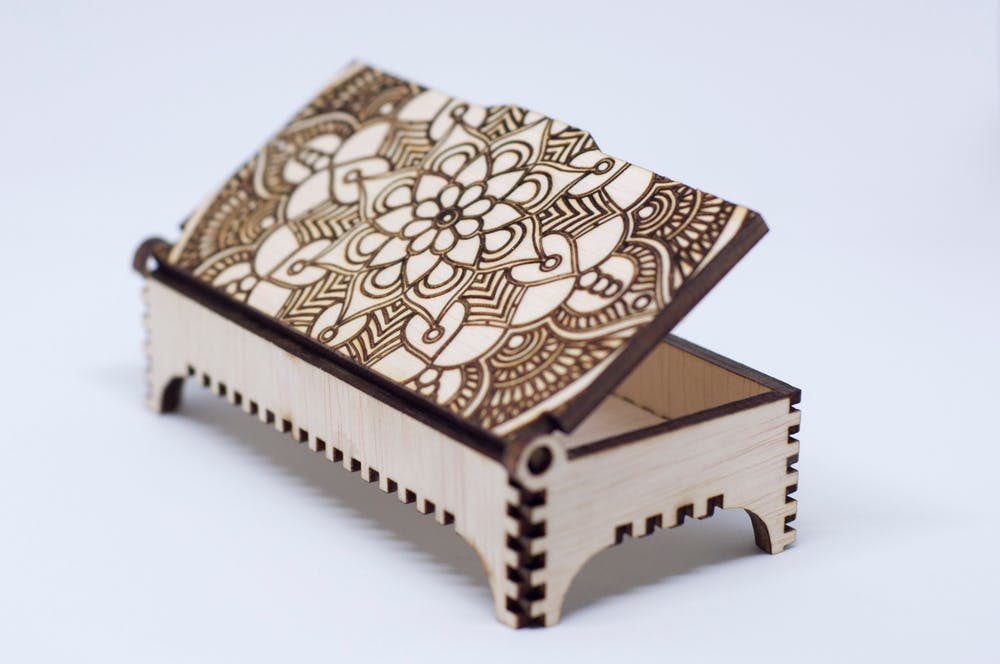
Laser engraved wooden box.
Image Credit: Shutterstock.com/Fairuzee Ramlee
Laser engraving is most commonly performed with either a CO2 or a fiber laser. Both of these lasers can produce high enough energy densities to engrave a design on a target surface by vaporizing and removing material in a controlled pattern. Fiber lasers are more effective at engraving metals since most metals readily absorb their wavelength. CO2 lasers are better suited for engraving nonmetals such as plastics, stone, and wood since these materials better absorb their wavelength.
How Laser Engraving Works
Laser engraving produces an embossed pattern on a material’s surface through the precise application of high levels of heat by means of a laser beam. The path, power, and speed of the laser beam are controlled by a computer program. The laser can generate very high energy densities, which can remove material from the surface of a material in the exact pattern required. Depending on the settings and programming of the laser, the resulting pattern may leave behind a pattern raised from its surroundings (convex), a pattern depressed into the surface (concave), or a darkened area essentially flush with the surface.
The process by which the laser removes material may be melting + vaporizing, direct sublimation from solid to gas, or, more generally, ablation. Ablation can refer to any erosive process that removes material from a substrate. In the field of laser engraving, it usually refers to material removal resulting from short pulses of laser energy. This energy briefly heats atoms on the surface into a plasma, generating shockwaves that eject small particles from the surface along the desired path. The laser power needed to engrave a particular material depends on several factors:
- Reflectivity: Reflective materials such as metals require higher laser power because not all of the laser energy is absorbed for heating.
- Density: The denser a material, the more molecules must be heated above a temperature threshold to mark the material. This requires more heat and, therefore, more laser power.
- State Transition Temperatures: The higher the melting, sublimation, and plasma generation temperatures of a material, the more laser power is required to heat a unit of material to the required condition for engraving.
Laser engraving services like ours at Xometry are used wherever durable, high contrast, mechanically durable markings are required, including the automotive, medical, electronics, and aerospace industries. Typical applications can include: durable signage, product marking, artistic engraving for commemorative items, and PCB (printed circuit board) marking. The engraving process is also employed to remove material from rusted metal parts.
Key Types of Laser Engraving
Laser engraving can generally be broken down into three categories: laser ablation, concave engraving, and convex engraving. These are described in more detail below:
1. Laser Ablation
Laser ablation refers to the mechanism by which the material is removed during laser engraving. When a laser beam interacts with the material at a specific power level, it instantly heats up. The addition of heat is rapid enough that the surface does not have time to transition from solid to a liquid but instead is directly vaporized. At higher laser intensities, the ablated material is converted into plasma. Due to the creation of fumes during the process, sufficient fume extraction is required. Laser ablation can be used for both concave and convex engraving techniques.
2. Concave Engraving
Concave engraving refers to a laser engraving technique that makes use of laser ablation in order to remove material in the shape of a desired pattern or design. This process produces a design that is indented relative to the surface of the surrounding, untouched material.
3. Convex Engraving
Convex engraving refers to a laser engraving technique that also makes use of laser ablation to remove material. Unlike concave engraving, convex engraving does not directly engrave the design but instead engraves all the areas around the outline of the design. This produces an embossed design that is raised above the surrounding engraved areas.
Common Materials That Can Be Laser Engraved
Laser engraving can be performed on a wide range of materials, provided the laser is powerful enough to vaporize the material. Listed below are some common materials used for engraving:
- Marble and Granite: Marble and granite are often engraved for items like tombstones or awards. They produce excellent contrast between the design and background when engraved.
- Stone and Brick: Stone and brick are often engraved for artistic products.
- Wood: Wood is easily engraved due to its low ablation point and low cost. It is a popular choice for hobbyists and is used for signs and artistic designs.
- Glass: Glass engraving is typically performed on awards and trophies. It can also be used to artistically mark wine glasses and other glass crockery.
- Acrylic: Acrylic is a highly transparent plastic that is used as a lighter and cheaper substitute for glass. It is also used for awards and trophies.
- Metal: Metal parts are typically engraved for permanent and durable part identification.
- Cardboard and Paper: Cardboard and paper can be engraved with very low-power laser engravers. They are used for creating artistic items like commemorative or congratulatory cards.
- Fabric: Fabrics are engraved to give clothing an artistic, distressed look. This process is often used on the denim material used to make jeans.
- Leather: Leather is typically engraved for personalized consumer items like wallets, belts, and shoes.
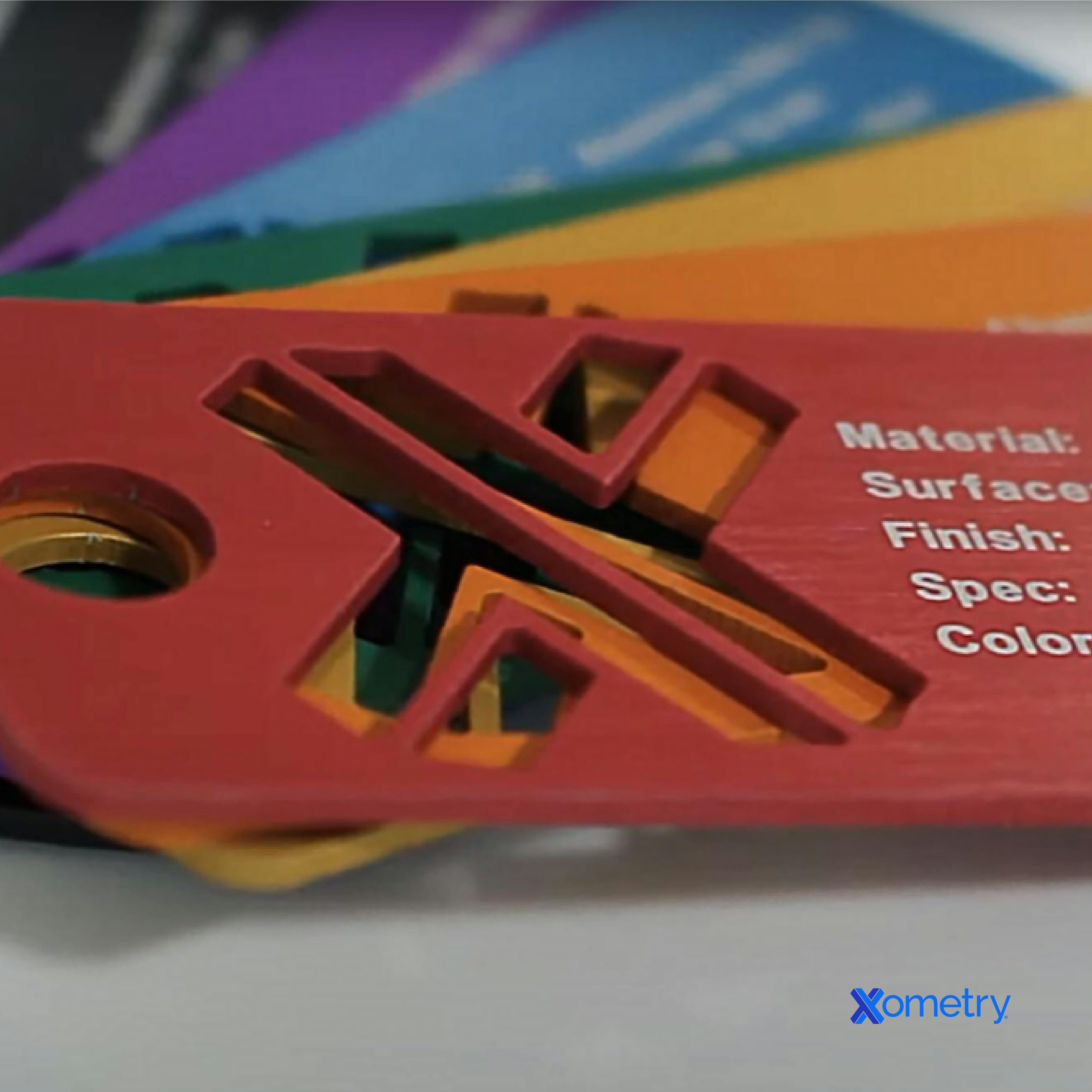
Steps in the Laser Engraving Process
Laser engraving is a multi-step process, as described in detail below:
- Prepare the Design: Convert the design into a format that can be read by the laser cutter CAM (computer-aided manufacturing) software. This is usually a .dxf file or some other vector-based format. Some CAM packages can directly convert image formats into laser paths. The laser power, speed, and the number of passes are selected in this CAM software.
- Select the Material: The types of materials that can be engraved depends on the type and power of the available laser engraver.
- Fixture the Workpiece: Place the material into the laser engraver and ensure that it cannot move during processing.
- Create a Safe Work Environment: Ensure that there is sufficient ventilation and that the correct protective eye goggles are used.
- Engraving: Some laser engraving machines will automatically focus the laser. However, in some cases, this must be done manually prior to engraving.
- Finishing: Once the part is complete, it can be removed from the machine and cleaned.
Xometry provides a wide range of manufacturing capabilities, including sheet cutting, CNC machining, injection molding, and more for all of your prototyping and production needs. Get your instant quote today.
Copyright and Trademark Notice
- Teflon™ is a registered trademark and a brand name (Teflon ®) owned by Chemours (formally DuPont)
Disclaimer
The content appearing on this webpage is for informational purposes only. Xometry makes no representation or warranty of any kind, be it expressed or implied, as to the accuracy, completeness, or validity of the information. Any performance parameters, geometric tolerances, specific design features, quality and types of materials, or processes should not be inferred to represent what will be delivered by third-party suppliers or manufacturers through Xometry’s network. Buyers seeking quotes for parts are responsible for defining the specific requirements for those parts. Please refer to our terms and conditions for more information.
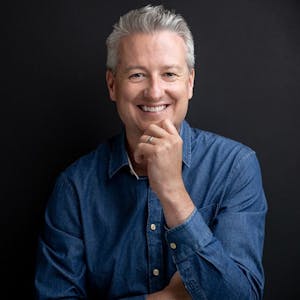