The ASTM C39/C39M standard describes how to test concrete cylinders for compressive strength. Specimens for the concrete cylinder test are obtained either by casting and curing them for testing, or by drilling cores out of already-poured concrete in place. Performing compression tests on concrete cylinders of standardized size and shape offers important information about the strength of the concrete mixture, which aids in design planning and quality control during the construction phase.
This article will discuss the key aspects of ASTM C39/C39M concrete cylinder testing, its significance and procedures, and the factors influencing the compressive strength of cylindrical concrete test specimens.
What Is Concrete Cylinder Testing?
The concrete cylinder compression test is a common process for determining the compressive strength of concrete. During this test, concrete specimens shaped like cylinders are subjected to progressively higher compressive loads until they break. The results can help engineers and builders verify that the concrete satisfies certain requirements for durability and structural integrity by providing valuable insights into the strength of the material. In addition to enhancing overall safety and the lifespan of structures, this ensures that concrete used in construction projects can handle the demands made on it.
Why Is Compressive Strength Important in Concrete Engineering?
Compressive strength is important in concrete engineering because it provides information that is useful in ensuring that the concrete meets design specifications and complies with safety regulations.
Concrete structures are subjected to dead loads (the weight of the structure itself), live loads (such as people and passing vehicles), and environmental loads (such as wind, earthquakes, water pressure, and temperature changes). Understanding the compressive strength of concrete ensures that structures can support these loads without failure, guaranteeing their safety and durability.
Engineers rely on accurate assessments of compressive strength to design buildings and infrastructure capable of withstanding the demands placed upon them. This test ensures that the concrete being used satisfies the desired criteria. It is also an essential quality control tool for constructions previously designed with specific concrete capabilities.
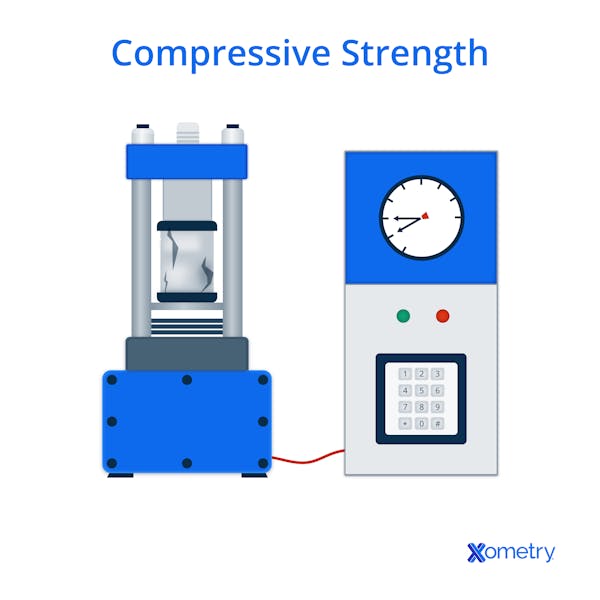
How Are Cylinder Concrete Specimens Prepared?
A methodical procedure is used to obtain representative cylinder concrete examples. To start, a sample is taken from the rotating drum truck mixer to make sure the concrete mix has received all of the water. Samples are taken from the central region of the load several times during the discharge process to ensure consistency. After that, within fifteen minutes, the gathered samples are blended to produce a composite sample. The composite sample is then quickly utilized to shape cylinders following predetermined protocols. Concrete is carefully poured into the cylinder molds using a scoop. The size of the mold determines the number of layers and rodding process.
After each layer is placed, it is uniformly rodded to distribute the roddings throughout the depth. The outside of the mold is tapped lightly to remove air voids, and the surface is leveled using a tamping rod, handheld float, or trowel. Mold caps are installed, and the cylinders are transferred to an initial curing place where they are stored at temperatures between 15.55 and 26.66 °C for up to 48 hours, with measures taken to prevent moisture loss.
Following initial curing, the cylinders undergo final curing within 30 minutes of being removed from the molds. During final curing, the cylinders are placed in a wet environment at a controlled temperature of 23.05 ±3.5°C until they are ready for testing.
This meticulous process ensures the integrity and accuracy of the cylinder concrete specimens for subsequent testing and analysis. Concrete cylinder specimens are prepared through casting in controlled laboratory conditions, on-site casting in the field, or extraction of cores from existing structures.
ASTM C31/C31M is the standard for casting specimens, while ASTM C42/C42M is the standardized procedure for extracting sample cores from structures.
Is ASTM C39/C39M Universal for All Concrete Industries?
ASTM C39/C39M is not universal for all sectors of the concrete industry. While it provides standard procedures for testing the compressive strength of concrete cylinders or cores, it is limited to concrete with a unit weight exceeding 800 kg/m³. This restriction may exclude certain lightweight concrete mixes from being tested using this standard.
Additionally, ASTM C39/C39M specifies the application of compressive axial loads to molded cylinders or cores until failure, which might not be applicable or suitable for all types of concrete structures or applications. Therefore, while ASTM C39/C39M is widely recognized and utilized in many concrete industries, it may not be universally applicable to all concrete materials and scenarios.
What Methods Are Used To Test Compressive Strength in Cylindrical Specimens?
Methods used to test compressive strength in cylindrical specimens include:
- ASTM C39/C39M Standard Test Method for Compressive Strength of Cylindrical Concrete Specimens: This method involves loading cylindrical concrete specimens in a compression-testing machine until failure occurs.
- BS EN 12390-3:2009 Testing Hardened Concrete: Compressive strength of test specimens: Similar to ASTM C39/C39M, this method specifies procedures for testing the compressive strength of cylindrical concrete specimens.
- ACI 363.2R-11 Guide to Quality Control and Assurance of High-Strength Concrete: This guide provides recommendations for testing high-strength concrete, including procedures for testing the compressive strength of cylindrical specimens.
- IS: 516-1959 Methods of Tests for Strength of Concrete: This Indian standard specifies a method of conducting compression tests on cylindrical specimens.
What Factors Influence Concrete's Compressive Strength?
Factors influencing concrete's compressive strength include:
- Raw Material Quality: The quality of the cement, aggregate, and sand affects concrete strength.
- Water/Cement: Proper ratio ensures optimal hydration and bonding.
- Compaction: Adequate compaction reduces voids and enhances cohesion.
- Temperature: Optimal curing temperature (10°C to 25°C) promotes strong bonds without excessive porosity.
- Curing: Proper curing with high humidity (85–90%) and adequate time (up to 28 days) allows concrete to achieve the desired strength.
- Age: Concrete strength increases over time due to continued hydration and structural development.
What Do Compression Test Results Reveal About Concrete Quality?
Test findings provide important details regarding the quality of the concrete, such as its compressive strength, which is a measure of its overall capacity to support loads. A high compressive strength denotes low void fraction and well-bonded concrete, indicating superior quality and structural integrity. On the other hand, low compressive strength can indicate improper mix proportions, inadequate compaction, or inadequate curing, exposing possible flaws and durability problems in the concrete. Furthermore, the results of compression tests may help engineers and contractors adjust the composition or processing conditions of the concrete mix to enhance quality and ensure the durability of the concrete structure.
What Are the Applications of Compressive Strength Tests?
Applications of the compressive strength test include:
- Quality Control in Construction: Ensuring concrete meets specified strength requirements for structural integrity.
- Material Selection: Determining suitable concrete mixes for different construction projects based on strength characteristics.
- Structural Design: Providing data for engineers to design safe and efficient concrete structures.
- Construction Monitoring: Assessing in-situ concrete strength during construction to ensure compliance with design specifications.
- Rock Testing: Analyzing the maximum compressive stress of rock samples to design structures and understand rock strata behavior.
What Is the Standard for Compressive Strength Testing?
There is no single global standard for compressive strength testing of concrete. However, the ASTM C39/C39M standard, titled “Standard Test Method for Compressive Strength of Cylindrical Concrete Specimens,” is commonly used in the construction industry, particularly in the United States.
This document provides guidelines for the compression testing of cylindrical specimens of concrete to determine their compressive strength. It specifies the equipment, specimen preparation(covered in related standards such as ASTM C31/C31M for casting and curing), testing conditions, and calculation methods to ensure consistent and accurate results.
ASTM C39/C39M is widely recognized and used in the construction industry to assess the quality and performance of concrete materials, aiding in the design and construction of safe and durable structures.
How Is Compressive Strength Calculated?
As per ASTM C39/C39M/C39M, the computation of a cylindrical concrete specimen's compressive strength is carried out by dividing the greatest load applied to the specimen during the test by the cross-sectional area of the test sample.
The cross-sectional area is calculated by averaging the measurements of the diameters of the top and bottom surfaces of the cylinder. This method ensures an accurate representation of the specimen's geometry, allowing for consistent and reliable calculations of compressive strength. By following the standardized procedures outlined in ASTM C39/C39M/C39M, engineers and technicians can obtain measurements of concrete strength, facilitating informed decisions in construction and structural design projects.
What Is the Highest Possible Compressive Strength of a Concrete?
Under laboratory conditions, concrete can achieve a compressive strength exceeding 200 MPa, far surpassing the typical maximum of 50 MPa to 60 MPa for conventional concrete. This requires using high-strength aggregates, a low water-to-cement ratio, silica fume, superplasticizers, and special curing methods such as heat curing or autoclaving.
Six-inch cubes can reach compressive strengths well above 100 MPa within 28 days, depending on curing techniques and mix design.
Standardized compressive strength measurements are typically based on cylindrical specimens, which may yield slightly lower results than cubes.
The difference in compressive strength between different high-strength concretes can be attributed to variations in mix design, curing conditions, and aggregate quality. Achieving 200 MPa or more requires advanced material science approaches, such as incorporating nano-silica, optimized particle packing, and extreme pressure compaction.
Advancements in technology, such as reactive powder concrete (RPC), nano-engineered additives, and improved curing techniques like autoclaved curing, may further push the limits of concrete compressive strength in the future.
What Other Tests Can Be Done on Concrete?
Other tests for concrete include:
- Flexural Strength Test: Determines the ability of concrete to resist bending or flexural stresses. This test is crucial for pavements and beams.
- Splitting Tensile Strength Test: Evaluates a concrete specimen's ability to resist indirect tensile forces. A cylindrical specimen is subjected to axial compressive loading, causing tensile stress along the vertical plane. The test measures the force required to cause splitting failure, providing insights into concrete's tensile strength.
- Water Absorption Test: A sample is dried to a constant mass and then submerged in water for a predetermined amount of time. After surface drying, a second weigh-in is conducted, after which the weight gain expressed as a percentage of the initial weight is computed. This percentage represents the absorption rate, indicating the ability of the concrete to absorb water.
- Abrasion Resistance Test: Determines the resistance of concrete surfaces to abrasion, wear, and surface deterioration due to mechanical action
- Permeability Test: Measures the ability of concrete to resist the passage of water, chemicals, or gases.
- Chloride Ion Penetration Test: Evaluates concrete's resistance to chloride ion penetration, which can cause corrosion of steel reinforcement bars. This is commonly conducted using the Rapid Chloride Permeability Test (RCPT) per ASTM C1202.
Summary
This article presented ASTM C39/C39M, explained it, and discussed its importance. To learn more about ASTM C39/C39M, contact a Xometry representative.
Xometry provides a wide range of manufacturing capabilities and other value-added services for all of your prototyping and production needs. Visit our website to learn more or to request a free, no-obligation quote.
Disclaimer
The content appearing on this webpage is for informational purposes only. Xometry makes no representation or warranty of any kind, be it expressed or implied, as to the accuracy, completeness, or validity of the information. Any performance parameters, geometric tolerances, specific design features, quality and types of materials, or processes should not be inferred to represent what will be delivered by third-party suppliers or manufacturers through Xometry’s network. Buyers seeking quotes for parts are responsible for defining th
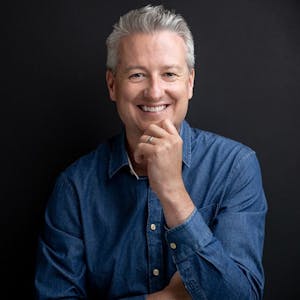