The hot runner system is one of the most recent advancements in plastic injection molding, and has pretty much taken over from cold running systems. Let’s look at exactly what these systems are, how they work, and where and what they’re used for.
What is Hot Runner Injection Molding?
The hot runner system works by injecting the plastic into the mold through a heated system called a manifold, which keeps the plastic melted. It’s different from the old cold runner system method where plastic flows through cold runners (a series of disposable plastic channels), and then has to be cooled and removed after each cycle. There’s no waste from hot runners, so the cycle time is much faster.
Hot runners offer better control, and the process eliminates many of the arduous steps necessary in other plastic injection molding methods that require cold runner systems to work. They allow the molten plastic to flow better in the mold and basically make the whole process quicker, smoother, and more efficient.
How it Works
The big selling point of hot runners is that they heat the entire runner system with an adjustable temperature controller so that the plastic stays in liquid form as it moves through the mold. It’s made of three main parts: a heated barrel that keeps the plastic hot, a manifold that shares out the molten plastic, and nozzles that show the plastic the way to the mold cavities. These all work together to keep the plastic hot until the cavities are all filled up. It’s then allowed to cool and set in the shape of the mold.
Hot running injection molding systems are known for producing better quality parts thanks to their ability to keep a consistent temperature.
Types
There are three different types of hot runner systems:
Hot tip: This system uses a hot tip at the end of the front of the nozzle, and a cooling mechanism to precisely control and adjust the temperature at the gate (the point where the plastic enters the mold). It’s ideal for small to medium-sized parts with gate diameters around 0.5–2.0mm and can be used with many different plastic materials.
Sprue: This system is better for medium to large parts. It has a larger passage — a sprue — for the plastic to flow through and get to the mold gate at a lower pressure. It has a low shear rate (how quickly the layers of plastic move past each other as they flow) which leads to much less stress and reduces the chances of the part warping or deforming. With sprues, the gate is bigger than the one used in hot tips, so the parts might be left with more prominent gate marks, meaning it’s best for parts that don’t have to have a certain neat appearance, like structural components.
Valve gate: This uses a needle with movement—from either mechanical, pneumatic, or hydraulic pressure—to control the nozzle’s opening and closing so that you can precisely control the flow of plastic. The result is a smooth cavity, so there are no defects or weld marks. This type is used for larger parts that need loads of gates that can be controlled one at a time.
Applications
Hot running injection molding systems are used in many industries, just some of which you’ll find in the table below, along with what it’s used to make.
Industry | Applications |
---|---|
Industry Automotive | Applications Interior and exterior parts, engine components |
Industry Packaging | Applications Bottle caps, lids, closures, containers with minimal waste |
Industry Medical | Applications Medical device parts, syringes, inhalers, surgical instruments, IV components |
Industry Consumer goods | Applications Mass production of electronics, toys, household appliances |
Industry Industrial | Applications Connectors, valves, gears, enclosures |
Hot Runner Injection Molding Applications
Advantages | Disadvantages |
---|---|
Advantages Cost savings: In the long run, it’s a more cost-efficient option as it offers reduced waste and better productivity. | Disadvantages Higher cost: They’re more expensive to buy than cold runners so be prepared to invest. |
Advantages Reduced waste: There are no runners to remove after each cycle so waste is cut right down. | Disadvantages High maintenance: Looking after these systems takes a lot of time and effort. |
Advantages Less chance of damage: It’s easy to reduce heat to the hot runner nozzle to prevent faulty parts. | Disadvantages Extra heating: To work, they need extra heating elements/sources, something that can also increase operating costs. |
Advantages Faster production: Once the system heats up, it’s ready to go and doesn’t need any prep time for the next injection, so cycle times are brought down quite a bit. | |
Advantages Cleaner parts: No extra plastic waste means the parts come out clean and don’t get in the way of other machines like robots or conveyors. There’s less chance of flash (excess plastic around the edges), too. | |
Advantages Compatible with delicate materials: It’s efficient use of heat makes it easier to work with materials that have very specific temperature requirements. | |
Advantages Less mold stress: They need less force to inject the plastic into the mold, meaning less stress on the mold and the machine holding it. |
Pros and Cons of Hot Runner Injection Molding
Hot Runner vs. Cold Runner Injection Molding
As we covered above, the main difference between hot and cold running systems is that hot runners keep the plastic molten inside the system, so there’s no need for extra material like runners, but cold runners let the plastic cool and harden, which means they need to be removed later (read: more waste). These differences can be seen in the image below.
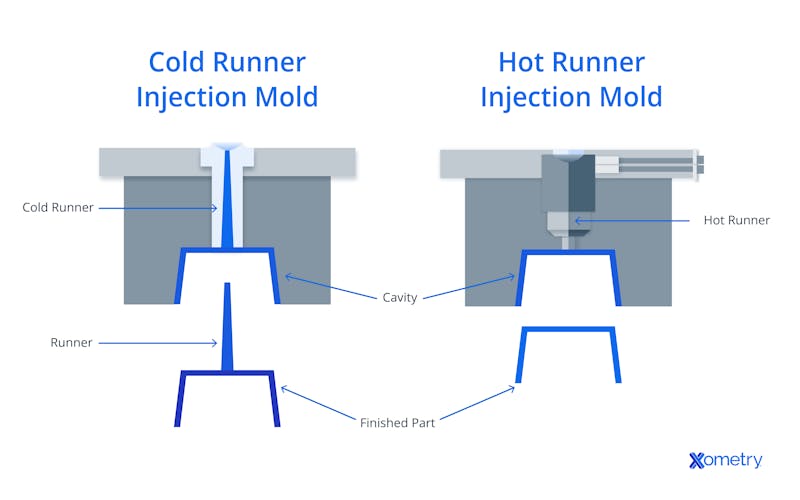
Hot running injection molding systems are able to keep the temperature consistent and allow you to control it, too. This makes them ideal for delicate materials that can’t survive really high heat. They can also make more detailed parts that are smooth and aesthetically pleasing (so they don’t have to be relegated to structural, i.e., hidden, uses). They might be more expensive to purchase, but they can churn out large amounts quickly with hardly any waste — they practically end up paying for themselves.
Choosing a Hot Running Injection Molding System
Not all hot running injection molding systems are the same, although, admittedly, they do look similar. Each one has its own unique needs, so to choose the right one, you’ll need to involve the hot runner manufacturer in the design process from the start. Also, different projects will likely need different hot runner configurations so the system you choose will need to match your needs, i.e., the type of material you’re molding and the color you want. The main things to watch for are the nozzle hot tip’s material and shape, and the size of the gate which will depend on things like the part’s weight, wall thickness, and the material’s quality.
How Xometry Can Help
Xometry provides a wide range of manufacturing capabilities including CNC machining, 3D printing, injection molding, laser cutting, and sheet metal fabrication. Get your instant quote today.
Disclaimer
The content appearing on this webpage is for informational purposes only. Xometry makes no representation or warranty of any kind, be it expressed or implied, as to the accuracy, completeness, or validity of the information. Any performance parameters, geometric tolerances, specific design features, quality and types of materials, or processes should not be inferred to represent what will be delivered by third-party suppliers or manufacturers through Xometry’s network. Buyers seeking quotes for parts are responsible for defining the specific requirements for those parts. Please refer to our terms and conditions for more information.
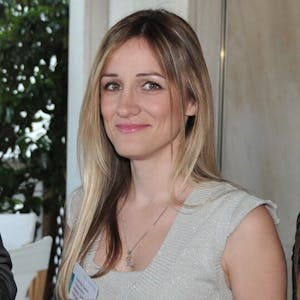