Blanchard grinding works in much the same way other grinding processes do. It uses an abrasive to remove material. Blanchard's unique ability can remove material faster than other precision grinding methods. This article will discuss Blanchard grinding, its applications, suited materials, how it works, advantages, and disadvantages.
What Is Blanchard Grinding?
Blanchard grinding is a process used to remove a large amount of material from one side of a piece of stock. The name Blanchard Grinding comes from the Blanchard Grinding Company of Cambridge during the early 20th century. Blanchard grinding is used because it is much more efficient at removing material than precision grinding. Precision grinding will be used to achieve a dimensional tolerance of less than 0.001”.
How Does Blanchard Grinding Work?
Blanchard grinding secures a ferrous workpiece with magnets (or a non-ferrous workpiece with tool holders) to a rotating table.
Above the workpiece, an abrasive wheel is mounted on a spindle in the vertical position. During grinding, both the workpiece and the abrasive wheel spin in opposite directions. After the two pieces have made contact and grinding is complete, a distinctive crosshatch pattern remains on the ground surface.
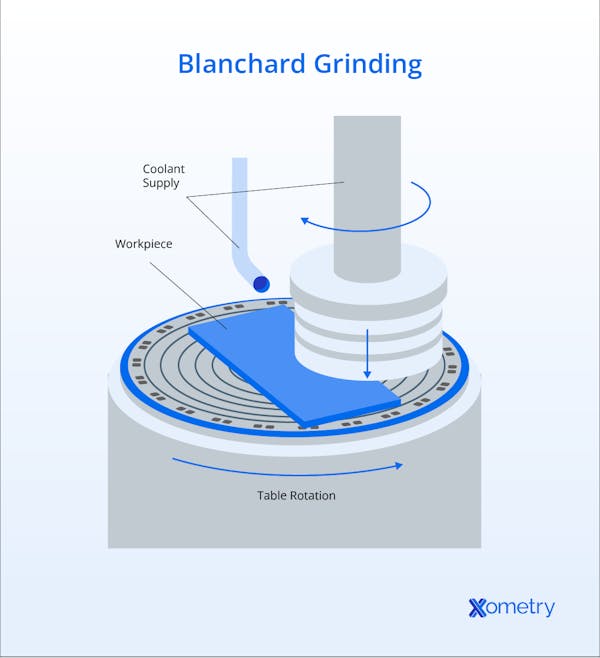
What Are the Different Applications of Blanchard Grinding?
Blanchard grinding can be used on both ferrous and non-ferrous materials. Below is a list of applications in which Blanchard grinding can be used:
- Mold and die tooling.
- Plate stock.
- Large castings and forgings.
- Large stampings.
- Rotary tables.
What Are the Advantages of Blanchard Grinding in Metalworking?
There are a few advantages as to why an organization might use Blanchard grinding in metalworking over other methods. Some of these advantages are listed below:
- Speed: It is fast at removing large amounts of material. This can be useful when shaping a material ready to go through precision grinding.
- Cost-Effective: The speed at which a Blanchard grinder removes material makes it more cost-effective than other methods.
- Works Well on Large Parts: This is best suited to removing large amounts of materials from large surface areas.
How Does Blanchard Grinding Compare to Other Surface Grinding Methods?
Blanchard is most commonly compared to surface grinding. Surface grinding is a term used to describe a grinding method that creates a high level of accuracy, such as horizontal or vertical surface grinding. Surface grinding is used when a high-quality surface finish and dimensional tolerance of less than 0.001” is required. However, Blanchard grinding is necessary for applications in which the removal of a large amount of material is required.
What Materials Are Suited for Blanchard Grinding?
There are a wide variety of metals that are well-suited for Blanchard grinding. Metals that are ferrous are easier to grind as they can be held in place by an electromagnetic table, whereas non-ferrous materials need a special tool to hold the work in place. Some examples of materials that can be ground using Blanchard grinding are:
- Bronze
- Steel
- Aluminum
- Stainless steel
- Cast iron
- Tool steel
- Copper
What Tools and Equipment Are Used in Blanchard Grinding?
There are very few tools used in Blanchard grinding apart from the grinding machine itself. The machine consists of a large rotating table which is usually magnetic, used for holding the work. The Blanchard grinder has a moveable head that moves and lowers a spinning grinding wheel into contact with the workpiece as the magnetic table is spinning. Blanchard grinding may require some basic hand tools to fix and remove workpieces to and from the spinning table.
What Are the Common Disadvantages of Blanchard Grinding?
There are a few disadvantages of Blanchard grinding, including:
- Precision: It is less precise than other precision grinding methods. This is why most grinding processes start with Blanchard grinding and finish with a different grinding technique.
- Surface Finish: Leaves a distinctive crosshatched scratched surface behind. This surface would not be ready for surface treatments such as a protective coating or paint and may reduce the stress tolerance of the part.
- Grinding Geometry: The process is only able to grind flat surfaces and cannot complete the same work that a cylindrical or jig grinder could.
To overcome the lack of precision and low-quality surface finish Blanchard provides, organizations can use a more precise grinding method to finish the job. However, for more complex geometries than a flat surface, Blanchard grinding would have to be avoided altogether.
What Are the Safety Concerns of Blanchard Grinding?
There are a few safety concerns regarding Blanchard grinding. Some common hazards include: the risk of entanglement, etc. usually associated with a spinning grinding wheel, parts of the wheel breaking and flying toward operators, cuts from metal burrs, or inhalation of grinding dust. To avoid these risks, operators should receive proper training and personal protective equipment such as goggles and gloves. The machine should have guards (especially around the wheel), and coolant should be used to capture any dust particles.
How Important Is Blanchard Grinding for Precision Applications?
Blanchard grinding is not important for precision applications as it cannot grind parts to high dimensional tolerance. However, Blanchard grinding is important for the efficiency of grinding large amounts of material in a timely manner.
What Industries Benefit Most From the Use of Blanchard Grinding?
The industries that benefit the most from the use of Blanchard grinding are:
- Aerospace
- Construction
- Automotive
- Paper industry
- Oil & gas
Are There Any Environmental Considerations in Blanchard Grinding?
Yes, there are environmental considerations to be made when Blanchard grinding. Blanchard grinding specifically isn't bad for the environment but grinding in general raises concerns. There are two concerns, the first is that grinding machines use a high amount of power and are very inefficient at converting the power they use into work. Investing in new and more modern equipment will help remedy this, as well as save an organization money on its energy bill. Secondly grinding creates lots of very fine particles which can contaminate the local air, water, or land. To prevent this, ventilation and coolant units with filtration must be used.
Can Blanchard Grinding Be Combined With Other Machining Processes for Better Results?
Yes, Blanchard grinding is often used as a first process to achieve parallelism with a wide tolerance and poor surface finish quickly. After that, a more precise grinding process can be used to improve the tolerance and surface finish issues. Post-Blanchard-grinding-surface grinding may be used to create a finer tolerance, however other grinding methods such as center grinding or form grinding are not used as they are only used for parts with curved geometry and Blanchard grinding is for flat surfaces.
What Skills Are Required for Successful Blanchard Grinding Operations?
To successfully operate a Blanchard grinder there are a few requirements. Training on the operation of a Blanchard grinder is key. The ability to operate a vertical spindle and magnetic chuck is also required. The operator must be able to read engineering drawings and sketches, as well as perform inspections on surface finishes and dimensional tolerances. Finally, Blanchard operations are never carried out in isolation, so the ability to hand over work to the next stage of production is key to success.
How Does Blanchard Grinding Impact the Durability and Longevity of Machined Parts?
By grinding metal, the surface of the metal is hardened. However, grinding has been shown to have little to no effect on the fatigue life of metal parts. So the durability and longevity of machined parts are unchanged.
Are There Any Limitations of Blanchard Grinding?
Yes, Blanchard grinding does have its limitations. For one, it only works for flat parts with no geometrical features other than holes. Another limitation is the precision and surface finish that Blanchard grinding can produce.
What Is the Difference Between Blanchard Grinding and Centerless Grinding?
Blanchard grinding and centerless grinding are two very different processes. Blanchard grinding creates flat parts, to a low tolerance, with a poor surface finish, all while holding the workpiece in place. In centerless grinding the work is not held in a single place but instead is pinched between an abrasive wheel and a regulating wheel. Centerless grinding creates tight tolerances, and high-quality surface finishes and creates cylindrical workpieces including bars, tubes, and round tapers.
Summary
This article presented Blanchard grinding, explained it, and discussed its various applications and best-suited materials. To learn more about Blanchard grinding, contact a Xometry representative.
Xometry provides a wide range of manufacturing capabilities, including machining and other value-added services for all of your prototyping and production needs. Visit our website to learn more or to request a free, no-obligation quote.
Disclaimer
The content appearing on this webpage is for informational purposes only. Xometry makes no representation or warranty of any kind, be it expressed or implied, as to the accuracy, completeness, or validity of the information. Any performance parameters, geometric tolerances, specific design features, quality and types of materials, or processes should not be inferred to represent what will be delivered by third-party suppliers or manufacturers through Xometry’s network. Buyers seeking quotes for parts are responsible for defining the specific requirements for those parts. Please refer to our terms and conditions for more information.
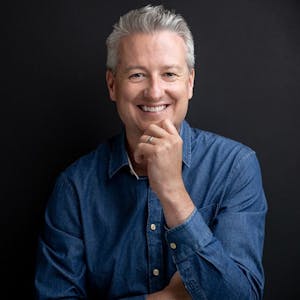