Electrical Discharge Machining (EDM) is a nonconventional machining process used primarily for tasks that would be unachievable with conventional methods. It uses electricity to erode the surface of conductive materials. Since no tool physically contacts the workpiece, EDM can maintain fine surface finishes even on intricate and delicate parts. The technique is broken down into die, wire, and drilling subtypes. EDM can be used to create turbine and compressor discs, hip and knee implants, pacemakers, die molds, and microelectronics.
This article will discuss EDM, how it works, its types, and its real-world applications.
What Is Electrical Discharge Machining?
Electrical Discharge Machining, also referred to as spark machining, is an alternative to traditional machining that uses thermal rather than mechanical forces to remove material. Specifically, a hot electrical spark is what removes material from the workpiece. EDM only works on materials that are electrically conductive such as brass, aluminum, and steel.
The erosive properties of electricity were discovered in 1770 by Joseph Priestly. However, EDM was not invented until 1943 when two soviet scientists, B. Lazarenko and N. Lazarenko, used electricity to machine conductive materials.
How Electrical Discharge Machining Works
EDM works by using a soft electrode — commonly graphite — to generate a spark between the electrode and the target area. It causes a portion of the machined part to vaporize. The temperature of the sparks ranges between 14,500 and 21,500 ºF. The melted and vaporized particles of metal are carried away from the machined area by a dielectric fluid such as oil.
This common principle is applied to all three types of EDM: die-sinking EDM, wire EDM, and hole-drilling EDM. In die EDM, the electrode is pre-formed in the shape of the desired cut and employed to cut that specific geometry. The same principles apply to wire EDM, but the wire electrode acts in the same way as a wire cheese cutter. In hole-drilling EDM, a pulsing electrode is used to create small and deep holes with no burrs.
Most conductive materials can be machined using the EDM process. Among the few exceptions to this rule are the high-grade nickel alloys which are often used in aerospace. However, specialized electrode materials and carefully selected machining speeds can sometimes allow nickel alloys to be machined this way.
The Principle of Electrical Discharge Machining (EDM)
EDM works on the principles of thermal erosion and vaporization. By sparking electricity from the electrode to the machining surface, EDM devices are able to erode and vaporize metal which is then removed from the area using a dielectric fluid.
Key Components and Tools Involved in Electrical Discharge Machining
The key components and tools involved in EDM are listed below:
- Electrodes: Electrodes come in the form of wires, dies, or tubes.
- Guides: Referred to as ferrules, these are made of ceramic and used to guide the electrode to the workpiece.
- Dielectric Fluid: Fluids cool the electrode and workpiece and circulate eroded metal away from the machined area.
- Current Supply: The electrode must be supplied with enough electricity to spark and erode the metal.
Different Types of EDM
There are three types of EDM, as listed below. Each one uses different tools to perform cutting operations.
- Die-sinking EDM (also known as conventional EDM, cavity-type EDM, or ram EDM)
- Wire-cutting EDM
- Hole-drilling EDM
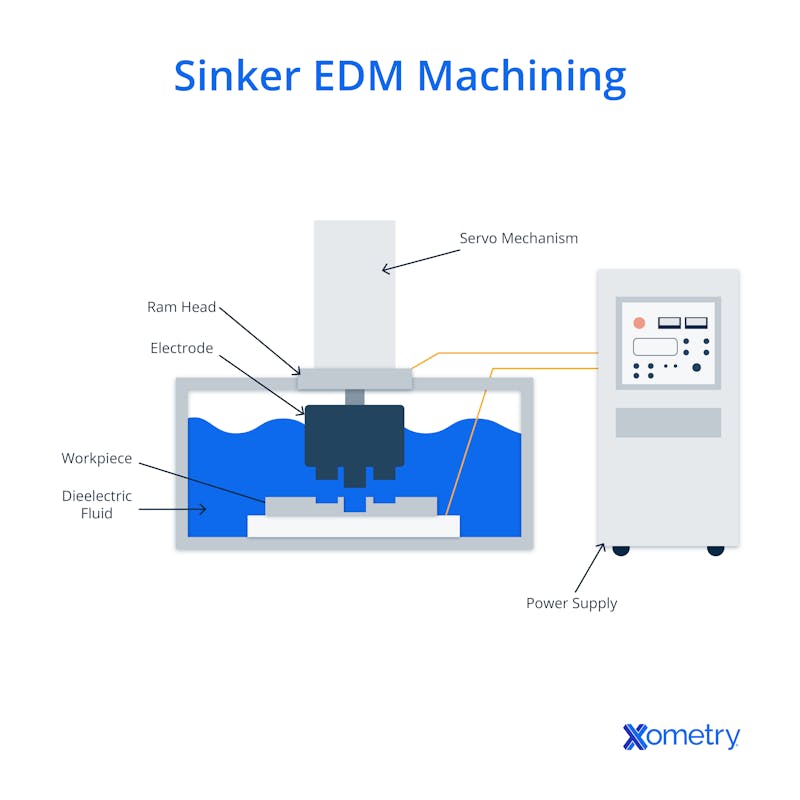
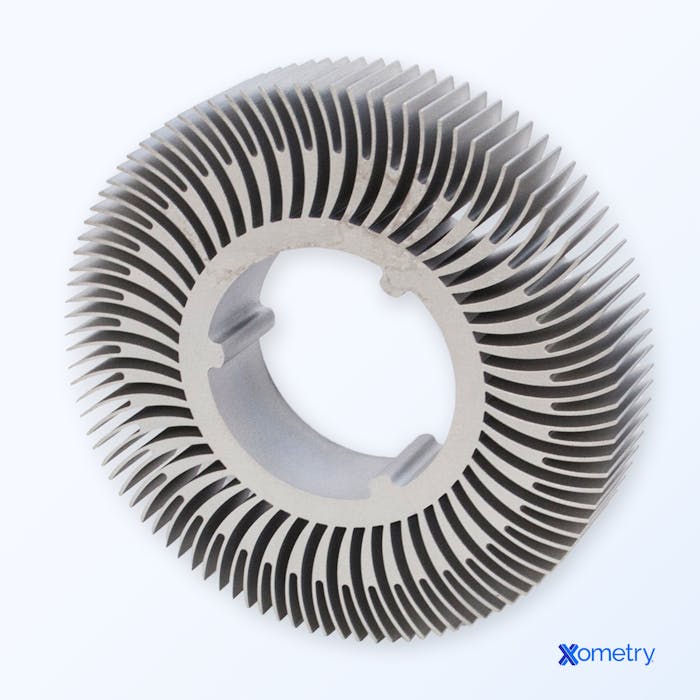
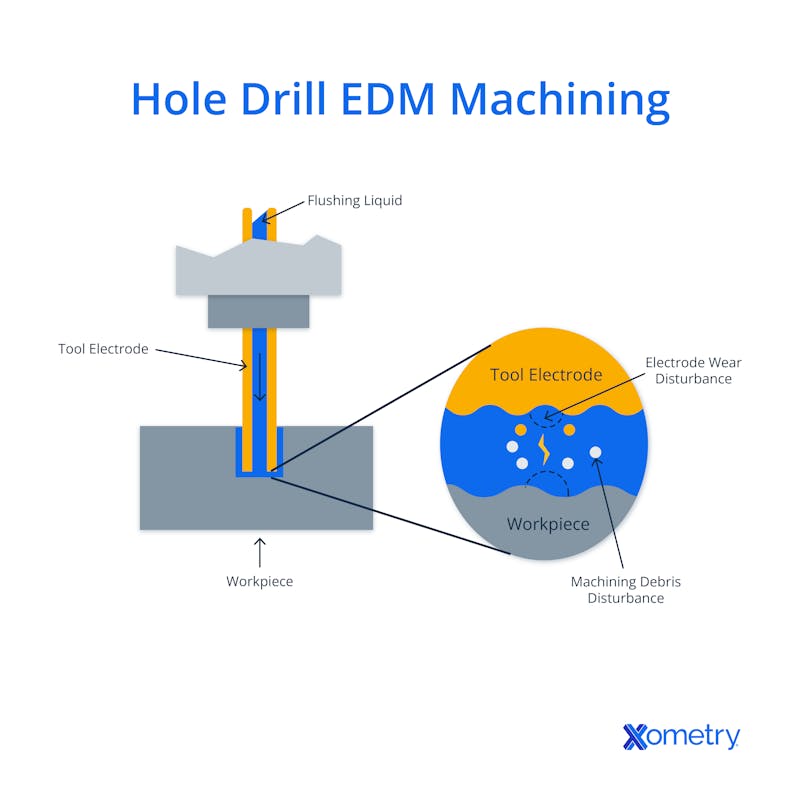
Sinker EDM machining diagram
Primary Applications of Electrical Discharge Machining in Industry
EDM is used to achieve things that conventional machining either can’t match in terms of quality or can’t achieve at all. Some of the applications of EDM are:
- Drilling small holes.
- Mold and die production.
- Removal of broken tools in workpieces.
- Creating burr-free medical equipment.
- Producing turbine discs for aerospace applications.
Advantages of Using EDM for Material Removal
There are many advantages to be found in the EDM process. EDM is usually used to machine parts that can't be made with conventional machining. Some of the advantages of EDM are:
- It can cut complex shapes, very deep holes, and undercuts which cannot be machined with other conventional machining methods. EDM has the added advantage of not creating burrs.
- The process is not affected by the hardness of the material and will cut through hard metals just as easily as soft metals.
- No marks get left behind unless the EDM is carried out too fast and the surface is left with a “blasted” texture.
- The precision can easily be fine-tuned. Tolerances of +/- 0.0002” are typically possible.
- Since there is no contact between the electrode and the workpiece, it imparts little to no force during machining. This allows very thin and delicate parts to be machined.
Disadvantages of Using EDM for Material Removal
Despite the wonders of EDM, there are also disadvantages to be aware of, such as:
- The machines cannot remove large amounts of material quickly, which slows the whole machining process. It’s hard to achieve high throughput with EDM.
- This is an energy-intensive process, which is not good for a company's carbon footprint. Unless electricity can be sourced in a sustainable way, some organizations will be required to find an alternative to EDM.
- The time and electricity demands translate into expensive operating costs.
- The process is limited to conductive materials only. Even some conductive materials like high-grade nickel alloys are hard to machine this way.
When To Use EDM
EDM is only used for parts whose designs demand tight tolerances, good surface finishes, undercuts, or other complex machining features. Some examples of where EDM is used include: cutting extrusions, rotary forms, or sharp internal corners, drilling micro holes or curved holes, engraving hard materials, or removing broken tools or fasteners from workpieces.
How EDM Differs From Traditional Machining Processes
The main difference in principle between EDM and traditional machining is that EDM doesn’t make contact with the workpiece, but instead uses electrical sparking to remove material. This gives the resulting part a better surface finish with impressive dimensional tolerances. It can also allow for otherwise impossible undercuts. Traditional machining processes, however, are cheaper and faster. One exception to this is grinding, which takes longer to remove material than EDM.
Types of Materials That Can Be Machined Using Electrical Discharge Machining
EDM can be used to machine virtually any conductive material without too many challenges. EDM does not work with non-conductive materials like glass, ceramics, plastics, wood, or composites. The workpiece material itself acts as part of the spark’s circuit, so it must conduct electricity. Materials that can be EDM machined include:
- Brass
- Aluminum
- Steel
- Copper
- Nickel
- Tungsten
Safety Considerations When Operating EDM Equipment
The main risks when operating EDM machines come from electricity. Not only is it dangerous to be close to the electrode due to the risk of electric shock, but all metal parts must be properly grounded to protect against electrocution. The circulation of dielectric fluid also needs to be monitored during EDM operation. Without it, EDM can create flammable gasses which pose a fire risk and are harmful to inhale.
Challenges Associated With EDM Technology
There are a number of challenges facing EDM technology. A few of the most significant ones are listed below:
- As a machining process, EDM uses a large amount of electrical energy. With the push to reduce carbon footprints, industries will try to find other machining methods if energy consumption cannot be reduced.
- The complexity of the machining process means the talent pool of technicians able to successfully carry out EDM operations is small. It may be hard to attract and retain experts.
- EDM units are often limited in the size of the parts they can work on. While they are perfect for small and intricate parts, they are not so accommodating for large work pieces.
Common Problems in EDM
There are a range of challenges that EDM machinists can face. One common problem is electrode wear. If an electrode tapers due to wear, the altered dimensions will be reflected in the machined surface. The distribution of electrode discharge can also be problematic. Sparks recurring in the same place can cause unequal material removal, so manufacturers need to use a discharge pulse control technology to control the distribution of electrical charge. Contaminated dielectric fluid can also attract a higher number of sparks in localized areas, so fluid must be continuously circulated.
Real-World Examples of Products Manufactured Using EDM
Examples of the industries that use EDM and the parts they create are listed below:
- The medical industry uses EDM to create implant devices including pacemakers, cochlear implants, and neurostimulators. EDM has also been used on hip implants, spinal fixtures, and dental implants like: crowns, bridges, and abutments.
- In the aeronautical industry, EDM is used to machine high-grade nickel alloys for use in turbine discs, compressor discs, and stator vanes.
- The manufacturing industry uses EDM to produce plastic die molds and extrusion dies and to perform die sinking.
How Xometry Can Help
Xometry provides a wide range of manufacturing capabilities including CNC machining, 3D printing, injection molding, laser cutting, and sheet metal fabrication. Get your instant quote today.
Copyright and Trademark Notices
- Inconel® is a registered trademark of Special Metals Corporation
Disclaimer
The content appearing on this webpage is for informational purposes only. Xometry makes no representation or warranty of any kind, be it expressed or implied, as to the accuracy, completeness, or validity of the information. Any performance parameters, geometric tolerances, specific design features, quality and types of materials, or processes should not be inferred to represent what will be delivered by third-party suppliers or manufacturers through Xometry’s network. Buyers seeking quotes for parts are responsible for defining the specific requirements for those parts. Please refer to our terms and conditions for more information.
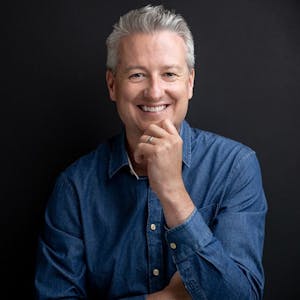