Milling machines can be used to carry out a range of operations, all designed for different purposes. Face milling is a specific milling machine operation used to create flat surfaces with a fine surface finish on a workpiece.
This article will discuss what face milling is, its definition, process, tools, and operations.
What Is Face Milling?
Face milling is a process used to cut material from the top face of a workpiece. Face milling is done using a milling machine or a machining center and typically uses tools such as shell mills, fly cutters, or specialized face mills. All of these tools achieve a similar result, which is to remove material from the top surface of a workpiece. Shell mills are one of the most common tools used to create parallel surfaces or achieve fine surface finishes.
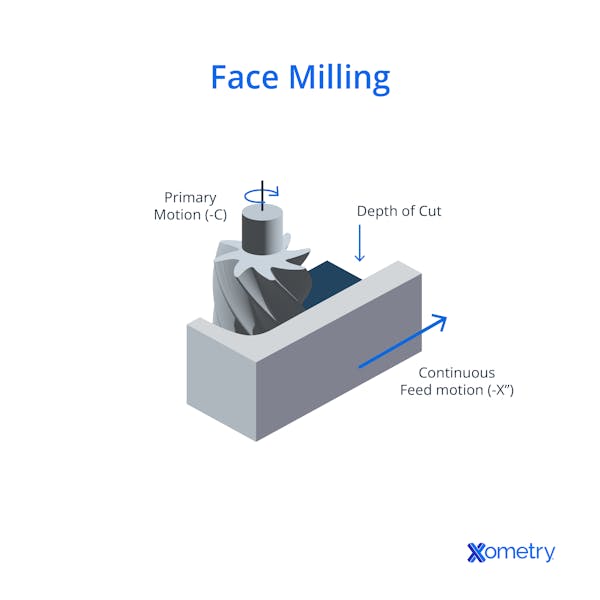
What Is Face Milling Used For?
Face milling is primarily used to create a flat face on a workpiece. While creating a flat face can be achieved with other processes, face milling is the quickest way to create one. Milling is also used to create a fine surface finish when compared to other machining methods.
What Is Face Milling Also Called?
Face milling is sometimes informally associated with the term 'shell milling' when a shell mill tool is used, though the standard term for the operation remains 'face milling.' Face milling and shell milling are interchangeable if the milling tool being used is a shell tool, whereas face machining is used when referring to the broader machining process.
What Are the Features of a Face Milling Cutter?
A face milling cutter consists of an arbor, a cutting head, two keys, a retaining bolt, and the cutting tips. The arbor is used by the machine to hold the tool. The retaining bolt screws through the center of the cutting head and the arbor. The two keys prevent the cutting head and arbor from rotating separately, and the tips are used as the cutting surface. The inserts are the most critical parts of any face milling cutter and can be changed for different materials and geometries depending on the application.
How Does Face Milling Differ From the Other Types of Milling?
There are many functions of milling, and each serves a different purpose. For example, one type of milling is peripheral milling. Peripheral milling is similar to face milling as it is used to create a flat surface and remove material quickly. However, in peripheral milling, the side of the milling tool is used as the cutting edge. Peripheral milling is able to remove a larger amount of material per unit of time due to having a larger cutting surface in contact with the workpiece. Other forms of milling include chamfer, profile, and shoulder, which are all used to create different forms of geometry. On the other hand, face milling is used to create a flat surface.
How Does the Face Milling Process Work?
There are four main steps to the face milling process, which are listed and described below:
1. Arrange the Workpiece
Fasten the workpiece to the machine table, typically using a vise. Centering the workpiece in the vise helps ensure uniform clamping, stability during cutting, and complete tool coverage of the top surface. Parallels may be required to raise the workpiece to the correct height within the vise and to ensure it sits level with the machine table.
2. Place the Milling Machine
The cutting tool’s position must be adjusted in the Z-direction to ensure the correct depth of cut is achieved. The spindle axis must be perpendicular to the surface of the workpiece to ensure a consistent and accurate cut, though this is standard in most milling setups.
3. Set the Feed Rate and Spindle Speed
Set the feed rate and spindle speed for the desired application before machining. The feed rate and spindle speed will depend on the material being cut, the depth of the cut, the width of the cut, and the size and material of the milling cutter. As a rule of thumb, harder materials, deeper cuts, or larger cutters generally require slower spindle speeds and feed rates to avoid tool wear or chatter.
4. Perform Machining
The final step is to carry out the machining. For a Computer Numerically Controlled (CNC) machine, once the G-code instructions have been uploaded to the milling machine, the machine can operate independently of the operator. For manual milling machines, the operator will position the tool in line with the work and set the feed speed and spindle speed. The machine can then cut the top face of the workpiece at the desired speed.
How Long Does the Process of Face Milling Take?
The time taken to face mill a workpiece will depend on the size of the workpiece and the feed rate of the machine. The feed rate depends on factors such as the depth of cut, width of cut, tool material, cutting speed, spindle speed, and the number of cutting edges on the tool. Most face milling operations are finished within a matter of minutes, though actual times can vary significantly. The approximate time required to face mill a part can be calculated using the formula:
Tc = L/vf
Where:
Tc = Machining time
L = Length of the cut
vf = Feed rate
For example, if the total length of the cut is 700 mm and the feed rate is 900 mm/min, then:
Tc = 700/900
Tc = 0.778 min = 47 seconds
What Is the Cutting Speed of Face Milling?
The cutting speed in face milling varies depending on both the workpiece material and the type of cutting tool material used. A list of different cutting materials and their cutting speeds in m/min are listed in Table 1 below:
Cutting Tool Material | Cutting Speed (m/min) |
---|---|
Cutting Tool Material High-speed steel | Cutting Speed (m/min) 30–50 |
Cutting Tool Material Cemented carbide | Cutting Speed (m/min) 60–100 |
Cutting Tool Material Ceramics | Cutting Speed (m/min) 300–600 |
Cutting Tool Material Cubic boron nitride | Cutting Speed (m/min) 300–600 |
Cutting Tool Material Diamond | Cutting Speed (m/min) >800 |
When To Use Face Milling?
Face milling is used to remove material from the surface of a workpiece and to create a high-quality surface finish, often with minimal need for post-processing. The face milling process can create a finer surface finish due to the tool geometry, overlapping cutting paths, and the ability to use multiple inserts with precise cutting edges. Face milling can also be used to create a flat surface on a workpiece.
What Are the Materials That Can Be Used for Face Milling?
Cutting tools with different materials are used for different purposes. Tool materials such as polycrystalline diamond (PCD), carbide, and cermets are used for high-speed cutting applications. In contrast, high-speed steel can be used for general face milling applications. Both ceramic and carbide tools are used in face milling, with ceramics suited to high-speed machining of hard materials, and carbide favored for versatility and good surface finish across many materials. All of these materials are significantly harder than the metals they are cutting which ensures the tool cuts the workpiece, not vice versa.
How Does the Choice of Materials Affect Face Milling Effectiveness?
The type of material used for the cutting surface of the tool affects both the lifespan of the tool and its optimal cutting speeds. Carbon steel tools are inexpensive but lose hardness rapidly at temperatures above 250°C, making them unsuitable for most modern milling operations except for low-speed applications on soft materials. This means carbon steels are not as fast or efficient as other materials. High-speed steel is alloyed carbon steel which improves the cutting speed and therefore efficiency of the tool. Stellite is a cobalt-chromium alloy known for wear resistance and high-temperature strength. Though less common today due to the rise of carbide tools, it is still used in some heavy-duty or specialized face milling applications.
How To Choose the Right Face Milling Tools?
There are two main categories of face milling tools—rough mills and finishing mills. Rough mills create a rougher surface finish but are able to remove material faster, and finishing mills are used to create a finer surface finish and a closer tolerance. Listed below are some tips on choosing the right face milling tools:
- Material: On the lower end are tool steels. Regular carbon steels are typically too soft for most milling operations, while high-speed steel (HSS) is inexpensive and suitable for general-purpose milling but wears more quickly than advanced tool materials. In the mid-range are high-speed steels alloyed with cobalt or coated with materials like titanium nitride, which improve wear resistance and cutting performance. High-end materials used for face milling include cemented carbide, which has a high wear resistance and high cutting speeds.
- Diameter: The tool diameter is a simple parameter. The larger the tool, the faster the material can be removed. Generally, face milling tool diameters are larger than the workpiece so that the cut can be made in one pass.
- Coating: Coating can affect the cutting speed and life span of the tool. One example of a coating is titanium nitride; however, as well as increasing the lifespan, this also increases the price point. Coatings can also reduce the friction of the cutting tool, which reduces the need for lubrication.
- Flutes: Flutes are cutting channels in the tool. An increase in the number of flutes allows for a higher feed rate per revolution, though chip evacuation becomes more challenging, especially in softer or gummy materials. However, it also reduces the space for the swarf to escape during cutting.
- Angle: The angle of the helix of the cutting edge affects the cutting speed. Steeper helix angles are suitable for soft metals, and shallower angles are suitable for harder materials including steel.
What Are the Right Tools for Face Milling?
There are three main tools for face milling, as discussed below:
1. End Mills
End mills are ideally suited for creating intricate finishes on a workpiece due to their cutting edge. This cutter has multiple teeth along the cutting edge, which enables it to create various designs. End mills are somewhat similar in appearance to a drill. However, a drill can only cut axially, whereas an end mill can cut in all directions. This tool can be used to create aesthetically pleasing designs.
2. Shell Mills
Shell mills are a popular choice for face milling. They are ideal for producing consistent surface finishes thanks to their multiple teeth with replaceable inserts. This design allows efficient material removal, especially on large, flat surfaces. While they can be used on hard materials, the effectiveness depends on factors like insert material, cutting speed, and machine rigidity.
3. Fly Cutters
Fly cutters are a type of tool used for face milling. They are a tool that has only one cutting edge and one insert. This tool is ideally suited for producing fine finishes without a high consumption of power. It is most commonly used for softer materials.
How Does the Choice of Tool Affect Face Milling Quality?
The quality of the finished product is directly affected by the choice of tool used in face milling. The choice of tool dictates the axial depth of the cut of the material and the cutting force while machining.
What Are the Different Types of Face Milling Operations?
Below are four types of face milling operations, each with its specific purposes:
1. General Face Milling
General face milling is the standard process for creating flat surfaces and is suitable for a wide range of materials and setups. A tool with a 45° entering angle is typically used, offering a good balance of cutting force distribution and surface finish.
2. Heavy-Duty Face Milling
Heavy-duty face milling is used to remove large volumes of material from large workpieces and requires robust machines with high spindle power. Tools with higher entering angles, such as 60°, are often preferred because they direct cutting forces more axially, improving stability and allowing for higher feed rates.
3. High Feed Milling
High feed milling uses shallow depths of cut combined with very high feed rates. Tools with a low entering angle, typically around 10°, are used to reduce radial forces and enable faster feed without compromising tool life or stability.
4. Finishing With Wiper Inserts
Wiper inserts are designed to improve surface finish without reducing feed rate. They allow for higher feed per tooth while maintaining a fine finish, which is especially useful in high-productivity applications.
What Are the Applications of Face Milling?
Face milling is primarily used to produce flat surfaces and improve surface finish. Common applications include:
- Leveling or surfacing the top face of a workpiece.
- Squaring up blocks or parts before additional machining.
- Preparing surfaces prior to further operations like pocket milling or drilling.
- Removing minimal amounts of material to achieve dimensional or aesthetic precision.
What Are the Advantages of Face Milling?
The advantages of face milling include:
- Produces smooth and consistent surface finishes.
- Can be used on a wide range of materials, including metals, plastics, and composites.
- Capable of relatively high feed rates, especially with modern insert cutters.
- Helps reduce chatter when using properly balanced tools and proper cutting parameters.
- Offers a balance of radial and axial cutting forces, depending on tool geometry (e.g., lead angle).
- Reduces corner breakout compared to more aggressive cutting methods.
- Can reduce entry impact if proper lead angles and entry techniques are used.
- May reduce radial load on spindle bearings depending on cutter geometry and machining parameters.
What Are the Disadvantages of Face Milling?
Face milling has some disadvantages, including:
- Cannot machine internal corners or features with steep vertical sidewalls.
- Burring or chipping may occur on the exit point of the cutter, especially on harder materials or if feed/speed is not optimal.
- Large face mill diameters may lead to clearance issues with fixturing or nearby features on the workpiece.
- The lead angle of the cutter limits the maximum axial depth of the cut in a single pass.
Is Face Milling Considered Expensive?
Face milling may involve higher initial tool costs compared to simpler milling operations due to specialized cutter designs. However, face mills are versatile and suitable for a wide range of materials, including composites, plastics, and metals. Despite higher initial tool costs, face mills offer long-term value due to their versatility and efficiency.
Can You Bore With a Face Mill?
Yes. Face mills can perform interpolated boring operations, though they are not typically used for drilling. With a face mill, you can mill a surface and then cut a large-diameter bore with the same tool. Interpolated toolpaths using face mills can be effective for rough boring large holes. Advances in cutter design and CNC software have expanded the ability of face mills to machine complex hole features.
What Is the Difference Between Face Milling and Peripheral Milling?
Face milling and peripheral milling are two of the most common types of milling operations and are extremely similar in how they operate. The difference between them is their suitability for fabricating features and their setup. For example, peripheral milling uses the side of the cutter, which is parallel to the workpiece surface, to remove material along its edges. Face milling removes material using the cutting edges on the face of the tool, perpendicular to the workpiece surface. Face milling is better suited for pieces that need a fine surface finish.
What Is the Difference Between Face Milling and Shell Milling?
A shell mill has multiple inserts on the outer edge and cutting teeth. This enables it to balance the cutting forces to have precise control over the amount of material that is removed by the cutter at high speeds. This allows for high-quality and consistent surface finishes on the workpiece. Shell mills are a type of face mill; the difference lies in tool design, not the operation itself. Face milling refers to the operation, and shell mills are commonly used for it.
What Is the Difference Between Face Milling and End Milling?
Face milling and end milling are among some of the most common types of milling procedures. Each uses a different type of cutter—one uses an end mill, and the other uses a face mill. The main difference between these two cutters is that an end mill uses both the sides and the end of the cutter, whereas a face mill only uses horizontal cutting. End mills can cut both axially and radially, making them more versatile for 3D profiling than face mills. Face mills typically have cutting inserts on both the face and the periphery of the tool body, optimized for machining flat surfaces.
Summary
This article described face milling, explained its process, tools, operations, and discussed its applications and advantages. To learn more about face milling, contact a Xometry representative.
Xometry provides a wide range of manufacturing capabilities, including casting and other value-added services for all of your prototyping and production needs. Visit our website to learn more or to request a free, no-obligation quote.
Disclaimer
The content appearing on this webpage is for informational purposes only. Xometry makes no representation or warranty of any kind, be it expressed or implied, as to the accuracy, completeness, or validity of the information. Any performance parameters, geometric tolerances, specific design features, quality and types of materials, or processes should not be inferred to represent what will be delivered by third-party suppliers or manufacturers through Xometry’s network. Buyers seeking quotes for parts are responsible for defining the specific requirements for those parts. Please refer to our terms and conditions for more information.
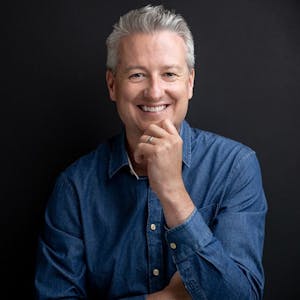