You might wonder how intricate drill bits and rounded tool handles get their shapes. It’s all thanks to a machining process called taper turning, which is key to manufacturing angled, cylindrical, and tapered objects.
With this style of turning, a lathe can carefully shape a wide range of materials into smooth, tapered pieces in various angles. At Xometry we may use this particular process to create finished products that are not only precise and functional but look good too. Here’s what you should know about taper turning, including how it works, the types of methods you can learn, and the materials and applications.
What is Taper Turning?
Taper turning gradually reduces the diameter of a cylindrical piece of material, giving it a conical or tapered shape. The machinery you’ll need for this kind of process is a lathe, which has a cutting tool that’ll whittle the workpiece into the angled shape you desire.
This is a great process if you’re looking to craft ramps and cylindrical shapes. The taper itself can either be external or internal, and what you choose will depend if you’d like the thread within a tool or object or on the exterior. Taper turning isn’t limited to one method, as you’ll find below. There are actually five common types you can choose from.
How Does it Work?
You’ll need a lathe to perform taper turning and first begin by clamping your material down between centers. Then, mount your cutting tool and position it near the workpiece. You’ll set the angle you desire and as the lathe spins the workpiece, the cutting tool will zero in and shave away material down into the taper you need. It’s important you control the speed, angle, and feed rate so you’re not left with a part or component that has the wrong dimensions or a ragged finish. If you don't have the capabilities or machinery, Xometry has a plethora of CNC turning services that can get the job done.
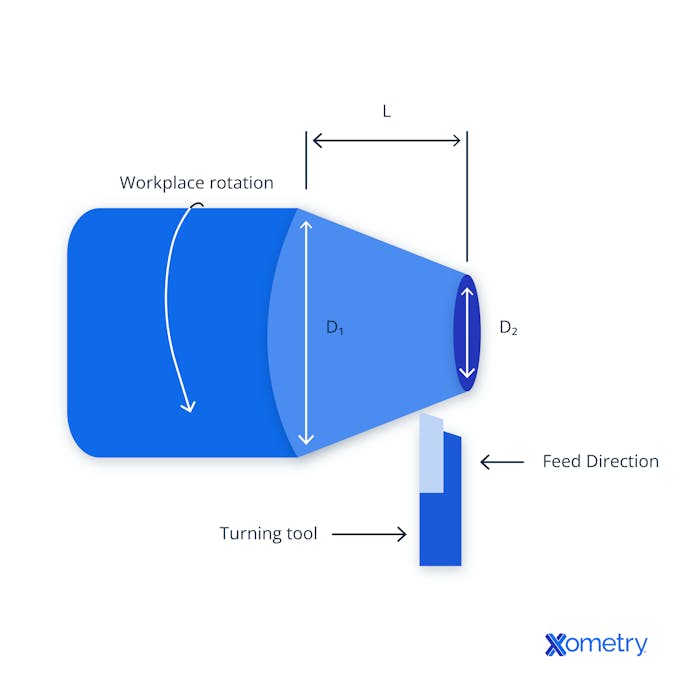
Materials Used
Xometry can taper turn a wide range of materials, including:
- Aluminum
- Alloy steel
- Carbon steel
- Stainless steel
- Titanium
- Brass
- Copper
- Composites
- Plastics, including thermoplastics and thermosets
Types of Taper Turning Methods
Here are the types of taper turning methods you can use with a lathe:
1. Form Tool Method
This is one of the simpler methods for taper turning, but one that you can really only create short tapers with. You’ll use a broad-form tool that moves into your material half the taper angle you want. It’s a slower process that kicks up quite a bit of vibration and needs heavy force from the operator in order to shave the metal off. The reason why you can only create shorter tapers is because longer ones might extend past the cutting tool, which means you can’t accurately or properly cut them down.
2. Combining Feeds Method
This method is a cut above, and requires you to have more advanced taper turning skills. You’ll adjust the longitudinal and cross feeds to create a diagonal path that the cutting tool will follow. This creates a very accurate taper when done correctly that can happen on a manual or CNC lathe, but you need to be aware and well-trained in this method for clean and precise results.
3. Compound Rest Method
If you need a high level of control over the angle, you’ll find it with the compound rest method. With it, you can create short and steep cones with accurate measurements. While your material is held in the chuck and rotated on a specific axis, the compound rest will direct the cutting tool.
4. Taper Turning Attachment Method
As it sounds, you’ll use a special attachment accessory that has a guide bar for this method of taper turning. Adding this into the mix when you’re working with a lathe gives you more options when it comes to size, depth of the cut, and angle.
5. Tailstock Set Over Method
Shallow taper angles are tricky to finesse, which is why you’d want to rely on the tailstock set over method if this is the kind of finish you’re after. For extremely gradual angles, you can move the piece up or down, only adjusting the workpiece’s rotation axis by half for a less severe angle.
Types of Holding Tapers
Here are the differences between the two types of tapers and why you’d select one over the other.
1. Self-Holding Tapers
These taper angles are what you’ll need if you require stability and very little movement when taper turning. Self-holding tapers stay put during the process and are securely wedged in, giving very little wiggle room when you’re aiming to create products that connect effortlessly and interlock with precision.
2. Self-Releasing Tapers
When you need to quickly load, release, and reload material into the lathe, self-releasing tapers are a good choice. Unless a drawbar is present, these won’t remain locked in place, which makes them easier to swap in and out in comparison to a self-holding taper.
Industries That Use Taper Turning
Taper turning is a popular choice if you’re in manufacturing, aerospace, automotive, engineering, or construction industries, as its precision helps create reliable parts that fit and function well. You may also choose taper turning as a method if you want to lower the weight of an object without decreasing its strength and structural integrity.
For instance, you can create engine components, landing gear, and control surfaces for aircraft, which, of course, need tapered parts that are sleeker and more aerodynamic. When it comes to cars and other automobiles, you can use taper turning to make axles, tie rods, and parts for the suspension, all of which will meet safety requirements. In construction, you’ll find taper turning useful for crafting parts for heavy machinery and structures for buildings.
Accuracy and Timeframe
Taper turning can be a very accurate technique if you do it correctly and select the right method depending on the angle, size, and gradient of taper you need. You’ll want to keep your machine well-maintained and receive training or train up workers in the particular method needed for the products you’re looking to make.
You may also be wondering how long taper turning takes, but this, again, is highly dependent on what you’re crafting. If you’re working on one or two lathes, doing form tool method turning, the production time is going to be much slower than a larger manufacturing facility that’s running lines of CNC lathes. You can take the guesswork out of timeframes with the help of the Xometry Instant Quoting Engine®, which will return an instant price and lead time for CNC-turned parts.
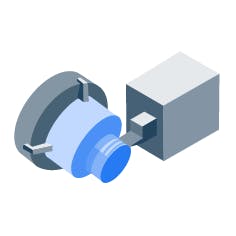
Advantages and Disadvantages
When you’re comparing taper turning to other methods, here are the advantages and disadvantages to keep in mind:
Advantages
- Material options: You can use a variety of different materials in your lathe for taper turning, from metals to wood to plastics.
- It’s a precise process: Taper turning has various techniques you can choose from, which allow you to create precise and accurate tapers on your products.
- Interesting shape options: With taper turning, you can create conical and tapered shapes. These aren’t always options with other turning and milling methods.
- Advanced capabilities: The end products you can create with taper turning often fit perfectly together, are perfectly aligned, or offer self-locking functions.
- Lighter but strong: You can maintain the structural integrity of a produce while still lightening its overall weight with taper turning.
- Replaces other methods: You can use taper turning in place of more complex (and often more complicated) processes, like threading and specialized contour machining.
Disadvantages
- High costs: Taper turning can be more expensive for your business as you’ll need specialized equipment.
- Machining is hard on tools: You’ll find this method really wears down on cutting tools.
- More wasteful: Taper turning leaves you with more scraps, chips, and waste than other processes.
- Slower than other machining methods: Simpler techniques, like the form tool method, won’t be as fast and your efficiency will be lower than it would if you were working with a different machining method.
- Vibration can cause flaws: The erratic vibrations that come from certain lathes and methods may be, at best, an annoyance for you or worst case cause errors in the finished product if it’s not handled well.
- Made for large quantities: Taper turning might be too expensive or not worth your time and energy if you only require small production runs.
- Limited taper angles: There is a maximum and minimum on the number of angles these machines can create. It all depends on the type of lathe and accessories you have. You may find you’ll need another machining method to get the necessary angle.
Applications for Taper Turning
You can use taper turning for various products across all sorts of industries. Here is a small selection of applications:
- Tool handles
- Shafts
- Drill bits and reamers
- Pins and dowels
- Rudders for ships
- Aircraft landing gear struts, engine parts, and control surfaces
- Automotive parts like axles and suspension parts
- Flanges and couplings
- Prosthetic components
Taper turning is a helpful technique when you’re interested in creating tapers, angles, and tapered cylindrical shapes. It provides durable components and parts with precise measurements that don’t lack in quality or structural integrity, which you may find useful in aerospace, construction, engineering, and medical industries.
How Xometry Can Help
Xometry offers a host of CNC machining services, including turning services like taper turning. Best of all, if you upload your 3D CAD to the Xometry Instant Quoting Engine® we can provide instant pricing and lead times for dozens of materials. We can also handle anything from one-offs to production quantities.
Disclaimer
The content appearing on this webpage is for informational purposes only. Xometry makes no representation or warranty of any kind, be it expressed or implied, as to the accuracy, completeness, or validity of the information. Any performance parameters, geometric tolerances, specific design features, quality and types of materials, or processes should not be inferred to represent what will be delivered by third-party suppliers or manufacturers through Xometry’s network. Buyers seeking quotes for parts are responsible for defining the specific requirements for those parts. Please refer to our terms and conditions for more information.
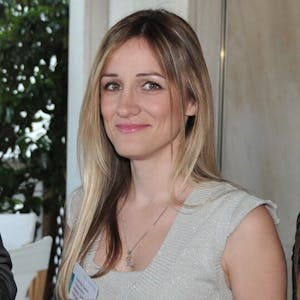