The coatings on industrial items are often integral to their material protection measures. Some of the most common industrial forms are resilient epoxy coatings, versatile polyurethane coatings, and advanced polysiloxane coatings. As an engineer or maintainer, you must understand how industrial coatings enhance the durability and performance of different surfaces.
In this article, we’ll explore the multi-faceted world of coatings, focusing on six essential types found across several sectors.
1. Epoxy Coating
A rugged protection barrier known as an epoxy coating results from the mixing of epoxy resin and hardener. This is a two-component system that generates a chemical reaction when mixed. The result is a hard and durable film. Once they set, epoxies are strongly adhesive and serve as excellent glues.
While costly to apply, epoxy coatings often compensate with their long-term durability. A gallon of the two-part chemical costs $30-100 depending on the brand, quality, and quantity. Epoxy coatings are used extensively in the industrial, marine, and architectural fields in particular.
Though very effective, the item’s surface must be prepared well to get ideal results. Prolonged exposure to UV light can cause yellowing, chalking, and surface degradation over time. By and large, though, epoxy is a durable and versatile option.
2. Polyurethane Coating
Polyurethane coating is a protective formulation derived from polyurethane polymers. Once set, this coating becomes firm but durable. It resists abrasion and provides moderate impact resistance, though it is less effective against heavy or sharp impacts.
The price of polyurethane coating varies based on formulation, pretreatment, and application methods. It usually falls between $40 and $150 per gallon.
A polyurethane coating presents remarkable abrasion resistance properties that make it suitable for surfaces that are subjected to excessive mechanical forces. Its elasticity allows it to accommodate thermal expansion and minor flexing without cracking. The disadvantage, however, is that the surface layer yellows with time. Nevertheless, polyurethane is quite common in the automobile, flooring, and marine sectors
3. Polysiloxane Coating
Polysiloxane is a very strong, waterproof polymer. This type of coating is made of polymers that form successive layers of tight films, making it highly resistant to environmental factors. Polysiloxane coating costs vary significantly depending on formulation, substrate treatment, and application methods. Presently, they cost between $50 and $200.
Polysiloxane coating has its advantages, including superior weather resistivity, ultraviolet stability, and chemical resistance, which makes it suitable during harsh conditions. These properties make it ideal for demanding industries such as aerospace, marine, and infrastructure. Despite their superior resistance, polysiloxane coatings demand careful attention during application.
4. Zinc-Rich Coating
A zinc-rich coating is a corrosion-resistant protective layer made, in large part, of zinc particles that act as sacrificial protection for the substrate. This coating works on the principle that zinc is more reactive than the underlying metal, so it corrodes sacrificially in place of the underlying steel when exposed to moisture and oxygen. The cost of zinc-rich coating is determined by aspects such as zinc content, mode of application, and the binder involved. It is presently sold for between $20 and $50 per gallon.
Zinc-rich coatings offer excellent corrosion resistance, making them ideal for harsh environments. Unlike many others, its sacrificial protection endures even if the coating is scratched. Zinc-based coatings are common in industries that emphasize corrosion protection, such as marine, oil and gas, and infrastructure. The only con is the relative complexity of surface preparation and application.
5. Alkyd Coating
Alkyd is a versatile coating that is formed from alkyd resins, making it hard enough for changing climatic circumstances. This coating reacts with oxygen to form a film when exposed to moisture, air, and UV light. Alkyd coating is priced based on the type of resin, method of application, and surface preparation. Most such resins cost between $10 and $30 per gallon.
Alkyd coatings adhere well to many basic materials and work fine both indoors and outdoors. They see use in sectors like construction, automotive equipment, heavy machinery, and metal fabrication. Among the cons is the propensity for alkyd coatings to fade with age or long-term exposure to solar rays.
6. Metalized Coating
With metalized coating, you get a high-end protective layer made up of resilient metallic particles. Its efficacy depends on the reflecting and blocking qualities of the metal particles to protect the substrate against corrosion, UV rays, and excessive heat. The price of metalized coatings fluctuates depending on the type of metal, application process, and substrate preparation. They range between $80 and $250 per gallon.
Metalized coatings provide corrosion protection, durability, and reflectivity. They can be applied to such products as car parts or machines. The reflective character of this material can improve thermal management by reflecting solar radiation, potentially reducing heat buildup. Even though metalized coatings perform well, they’re not a cure-all and won’t work with all surface types.
What Are Things to Consider When Choosing Industrial Coatings?
While selecting industrial coatings, keep a few considerations in mind:
- Substrate Type: Choose an adhesive and protective coating based on the substrate material, be it metal, concrete, or wood. Coatings react differently to various substrates, and each substrate’s demands are unique. As an example, metals typically require anti-corrosive coatings, while concrete often needs moisture, chemical, and abrasion resistance.
- Environmental Conditions: Determine your item’s exposure to conditions like changing weather, temperature fluctuations, ultraviolet radiation, or caustic chemicals. Limit your coating options to those that defend against your expected conditions. That will keep both your coating and the underlying material intact longer.
- Application Method: Keep in mind practical considerations such as ease of application, drying time, and curing conditions. Some types of layers need special equipment or multiple applications. Allow sufficient time in your processes to avoid delays and wasted resources.
- Performance Requirements: Specify up front the corrosion, abrasion, impact, and other resistance factors that you expect. Each coating has its peculiar properties. The definition of specific needs will help you choose a coating that meets your goals.
- Cost Considerations: Assess the total cost, including material cost, application expenses, and any projected maintenance costs in the future. Some of these coatings are expensive but are highly durable and sustainable, leading to lower overall costs over time.
What Is the Best Type of Industrial Coating?
The best industrial coating depends upon the particular application requirements. Polyurethane coatings are popular for their abrasion resistance, chemical resistance, and flexibility, making them suitable for heavily used surfaces. They are also flexible enough to accommodate thermal expansion and contraction without cracking. Polyurethane coatings are versatile by nature, with applications ranging from automobiles to flooring to marine industries.
Nevertheless, your choice of the optimal industrial coating depends on different variables such as substrate types, ambient circumstances, and expected performance. Although polyurethane coatings are good for many conditions, other coatings might be more fitting for some applications. Evaluate your needs carefully before choosing one.
What Is the Coating Used for Steel?
Hot-dip galvanizing is one of the most common methods for protecting steel against corrosion. This process involves dipping steel into molten zinc, creating bonds that are extremely resistant to corrosion. Galvanized coatings are highly efficient as they provide steel with robust and long-lasting protection against rust and corrosion.
The reason steel is so often galvanized stems from the coating’s long lifespan and minimal maintenance requirements. Even when the coating is scratched or damaged, the zinc layer continues to provide sacrificial protection for the underlying steel.
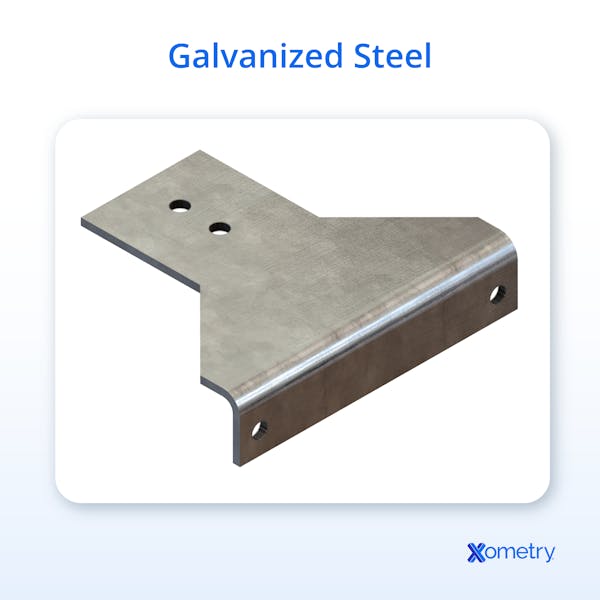
What Are Industrial Coatings?
Industrial coatings are specialized materials meant to protect, decorate, or add functionality to the materials they cover. The reason for applying these coatings is primarily to protect surfaces from corrosion, abrasion, chemicals, or UV radiation.
Industrial coatings are important in fields such as manufacturing, construction, automotive, aerospace, marine, and infrastructure. Without proper protection, the surface materials would deteriorate under harsh environmental pressures. The coatings are meant to prevent degradation and extend the lives of exposed surfaces. They are thus important damage-prevention mechanisms.
What Are the Advantages of Coating?
A protective coating layer can be beneficial for your industrial equipment for several reasons:
- It forms a protective layer between metal surfaces and corrosive substances like water and other chemicals.
- It protects surface integrity from traffic or abrasive attacks.
- Some coatings are resistant to chemical exposure, which is very important in industrial settings where equipment comes into contact with corrosive substances.
- The right coating can protect surfaces from degradation or discoloration caused by UV rays.
- Coatings often enhance the look of surfaces, resulting in a better visual appeal.
- Some variants are specialized for extreme temperatures and are thus important in regions with variable weather conditions.
- You can create a barrier that prevents water from penetrating the surface and causing rot or decay.
- Smooth-coated surfaces are easy to clean and maintain.
- It improves durability.
What Are the Disadvantages of Coating?
While coatings offer numerous advantages, they also come with certain drawbacks, such as:
- Proper application is complex and requires adequate surface preparation as well as specialized application techniques.
- Both the coating material and application process can be expensive, which can make it hard on the budget.
- Some coating formulations can include VOCs (volatile organic compounds) such as solvents that release harmful gases like formaldehyde or other hydrocarbons, which can impact air quality and the environment.
- Major impacts or abrasive conditions can damage most coatings, negating their functionalities.
- Surface adhesion can be tricky depending on the substrate type or application conditions.
- Some formulas take a long time to cure, meaning the equipment will remain unavailable until it is fully dry.
- Color fading is likely to occur in any coatings that are subject to UV rays.
- Not every coating is compatible with every material, so you must research compatibility ahead of time.
- Some coatings are only effective for a certain range of temperatures.
Is Coating Worth It?
Yes, it’s well worth coating your equipment. Coating provides corrosion protection, durability, and environmental shielding that typically outweigh the drawbacks. Though expensive up front, high-quality coatings can yield substantial savings down the line by prolonging material life and reducing repair frequency.
In addition, coatings enhance both the appearance and functionality of the surface. Applying suitable coatings to a structure will extend its durability and improve its performance.
Is Coating Expensive?
It depends. Costs are based on the kind of coating, the extent of the project, the pre-treatment of the surface, and the application method. High-performance coatings are often the most difficult to apply.
However, when you consider the longer functional lifespan, reduction in maintenance demands, and better overall performance, the payoff is very often worth the pain of applying a good coating. Consider the entire lifecycle in your cost-benefit analysis before making a decision.
What is the Difference Between Coating and Paint?
Paint is a type of coating, but not all coatings are paints. In practical terms, though, paints and coatings are usually viewed as different things. Here are a few key points that differentiate mere paint from higher-performance coatings:
- Composition: One of the main purposes of paint is to add color, while many coatings are not meant to do so. Protective coatings are instead optimized for protection and adhesion, so their formulation may include urethane, epoxy, metals, and other chemicals not found in ordinary paints. By contrast, paints are often optimized to be easy to apply, so in addition to their pigments, they often contain thinners and simpler binding agents.
- Purpose: Coatings may have beautifying effects, but their primary goal is to prevent corrosion, hinder degradation, and improve performance. Paints offer some protection, but their top priority is usually appearance.
- Thickness: Paints are typically made to be thin and runny to cover large areas in a thin layer. Most industrial coatings are thicker. The specific thickness varies based on the coating’s formulation and purpose.
- Application Area: Industrial coatings are primarily used in sectors like automotive, aerospace, marine, construction, and heavy industry, but they can occasionally be applied in commercial and architectural projects as well. Paints (except some specialty industry versions) are meant for broader use. They find their way onto construction materials, artwork, interior decor, toys, and much more.
- Functionality: High-end coatings have specific purposes such as corrosion deterrence, chemical resistance, and fire protection. They are custom-made to counter particular environmental threats. Meanwhile, manufacturers mostly make paints for their aesthetic value. Paint offers protection largely as a side benefit rather than a primary goal. Base your choice of paint or coating on your particular application’s needs, aesthetics, and functionality.
Summary
This article presented types of coatings, explained each of them, and discussed the best uses for each coating. To learn more about types of coating, contact a Xometry representative.
Xometry provides a wide range of manufacturing capabilities and other value-added services for all of your prototyping and production needs. Visit our website to learn more or to request a free, no-obligation quote.
Disclaimer
The content appearing on this webpage is for informational purposes only. Xometry makes no representation or warranty of any kind, be it expressed or implied, as to the accuracy, completeness, or validity of the information. Any performance parameters, geometric tolerances, specific design features, quality and types of materials, or processes should not be inferred to represent what will be delivered by third-party suppliers or manufacturers through Xometry’s network. Buyers seeking quotes for parts are responsible for defining the specific requirements for those parts. Please refer to our terms and conditions for more information.
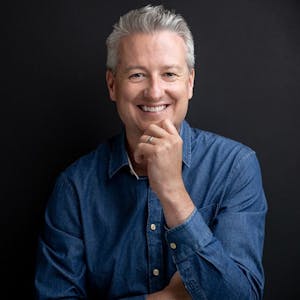