Design Tip #1: Avoid Sharp Internal Corners
Don’t forget to add a radius to sharp internals corners. This is one of the most common design mistakes with CNC machining; End-mills and cutting tools are round, making it impossible for them to create a perfectly sharp internal corner without expensive secondary processes.
Speaking about internal radii, keep them about 30% larger than the cutting tool’s radius to improve how fast that feature can be cut. You should also aim for a radius-to-depth ratio of 1 to 4; and, when in doubt, remember that larger internal radii are always better–and less expensive to produce.
Are you trying to fit a rectangular peg in a rectangular hole? Use a relief cut to make a dogbone feature for a snug fit.
Design Tip #2: Avoid Deep Pockets
Internal pockets or cavities should follow a width-to-depth ratio of 1 to 6 or shallower. Deep and narrow pockets add risk to the machining process and can cause issues like deflection, tool breakage, and make it difficult to evacuate the metal shavings and chips produced by the cutting process.
Note that round drilled features can go as deep as a 1 to 10 drill width-to-depth ratio, but make sure to allow relief at the bottom for drill tips.
Design Tip #3: Be Mindful of Thread Depth
Threads and tapped holes are some of the most common features we see with CNC parts. A common design mistake is calling out threads that are much deeper than they need to be. Deep threads increase manufacturing time, add a higher risk of tool breakage, and generally do not add much strength after the first couple of turns.
A simple rule for standard threaded holes is to make the thread depth twice as deep as the hole diameter. For example, half an inch of depth would be sufficient for a ¼-20 thread. We also recommend adding an unthreaded length of at least half the hole diameter for threads in blind holes to allow for tool leads and chip evacuation.
Design Tip #4: Watch Out for Thin Walls!
Excessively thin walls are not only weaker, but they can also add significant risk and costs to machining. Thin areas become less rigid, which makes it harder to hold precise dimensions, and defects from machining vibrations, like chatter or breakthroughs, are more likely to occur. Risk increases significantly if the thin wall is deep or a cantilever.
You can avoid these problems by keeping walls at least thirty thousandths thick, and double that for plastics.
Design Tip #5: Part Marking
Adding part marking is a great way to identify a part and its revision. We recommend using engraving, which can be done during machining operations, wherever possible. Sans-serif text works best in at least a 20-point font size. Avoid raised or embossed markings whenever possible because we have the machine around the text versus just the text itself – which can skyrocket the price of that feature.
If you are adding a finish-like color anodize to your part, we recommend laser marking to produce high-contrast text or logos accurately and at low costs. Other methods like ink stamping or silkscreen can create detailed markings with more color choices.
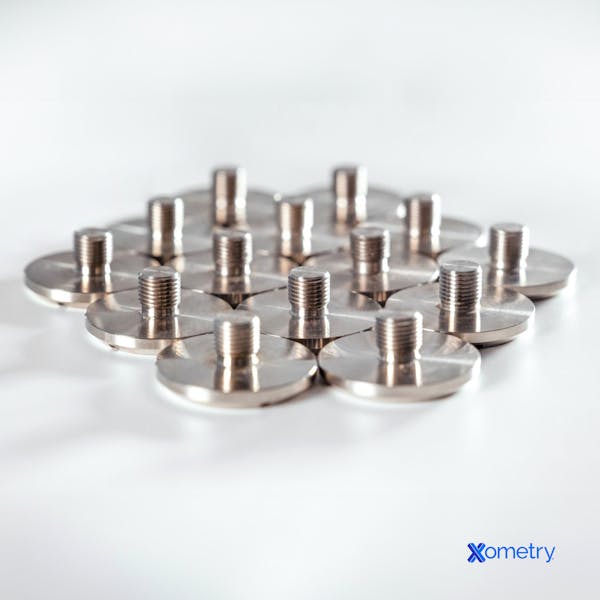
Want More Design Tips?
Check out Xometry’s CNC Design Guide and head to the Xometry Instant Quoting Engine® to get instant pricing and lead times for CNC machined parts today!
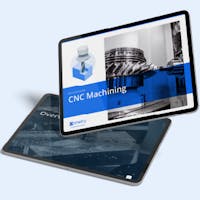
CNC Machining Design Guide
