A spotface is a flat-faced, notionally cylindrical but very shallow hole that is larger in diameter than the hole that it is concentrically cut into. It is cut to impose a flat landing surface for contacting/mating parts, such as washers or fastener heads. The primary reasons for spot-facing holes are:
- To provide a flat landing/clenching surface for fasteners, washers, and lock-washers on an otherwise rough or uneven-surfaced part.
- To provide the same flat landing surface on an otherwise curved surface of a part.
While spot-facing and counterboring of holes are geometrically identical operations, the spotface provides a flat landing surface, where the counterbore fully recesses the flat-faced fastener fitted to the hole so treated. This article will further discuss spotface holes, how to drill one, how to choose the right tap, as well as the applications and uses of a spotface hole.

How To Drill a Spotface Hole
Spotface holes are rarely made by hand. Spot-facing cutters exist, with a cylindrical peg to locate into the drilled hole before cutting. Although, more often, spot-facing is performed on a mill or CNC machine.
Choosing the Right Tap for a Spotface Hole
Where the hole to be spot-faced is formed/drilled through to the other side of the part, the tap required for threading such a hole is a taper or middle type. These two forms of tap have the initial threads ground away, allowing the tap to enter the hole and correctly center from the start of tapping/thread cutting.
For a through hole, the selection of taper or middle taps depends on the depth of the hole to be tapped. There must be enough total length of unaltered tap and shank combined to allow the tap to penetrate deeply enough to complete the thread through the part.
Where the hole is blind, tapping requires a two-stage operation. The thread is initiated with a taper or middle tap and then completed with a bottoming tap to the required depth. The choice between taper and middle taps is driven by the blind hole depth; where its use is possible, the taper tap gives a softer and more certain start to the thread cutting. But, if the taper excludes effective (full depth) cutting as it is longer than the blind hole is deep, it is necessary to use a middle tap.
Applications and Uses of Spotface Holes
The purpose of spot-facing a hole is to provide a smooth, perpendicular/flat landing for a component to be fixed down to the surface. Such a component may be a post/standoff held down by a threaded fastener, or a fastener holding other parts on the reverse side of the spotface.
In either case, the spotface serves the purpose of providing a flat landing onto a controlled and precise surface. It imposes both flatness and precision onto otherwise imprecise or unsuitably shaped parts.
Spotface Hole Size Charts
There are no universal standard charts that define spot-facing of parts. It becomes the responsibility of the designer and/or machinist to correctly size both the diameter and the net depth of the spotface operation to suit the needs of the part.
In general, spot-facing is sized to be larger than the part that is designed to land upon it. It should have sufficient depth to ensure a fully annular flat surface, removing all curvature or roughness from the landing surface.
Larger companies such as Boeing have design manuals (BDM-1327) that specify the nominal diameter of the spotface as the matching size of the cutter to be used (to reduce unnecessary machine time). As a guide, the appropriate diameter is approximately the flat seat diameter required, plus 2x the corner radius of the cutter. The ASME Y14.5-2009 guide for sizing a spotface specifies it as equal in diameter to the required diameter with no safety allowance for radii.
What is the Callout Symbol of a Spotface Hole?
The ISO drawing callout symbol for a spotface hole is a subset of the callout for a counterbore, with the letters SF superimposed:

The callout symbol for a spotface hole.
Spotface Holes vs. Counterbore Holes
Spotface holes are blind or through holes that have had a perpendicular and flat-faced shallow shoulder cut at the material face. This design provides a high-quality surface on otherwise rough-surfaced parts or provides a perpendicular landing surface on otherwise curved-surface parts.
Counterbore holes serve the purpose of concealing fastener heads that have flat lower faces and apply to:
- All types of heads for drives used for rotating threaded fasteners, such as: external hex, internal hex, Phillips, crosshead, Torx, pin Torx, and slot.
- All flat-bottomed threaded fastener head types such as: pan, button, cap, hex, and washer hex.
- Wide variety of knock-down joint fasteners that are not threaded, such as quarter-turn locks and push nuts.
- Various rivet types such as pop, peened, and push rivets.
You can see both types of holes in the diagram below:
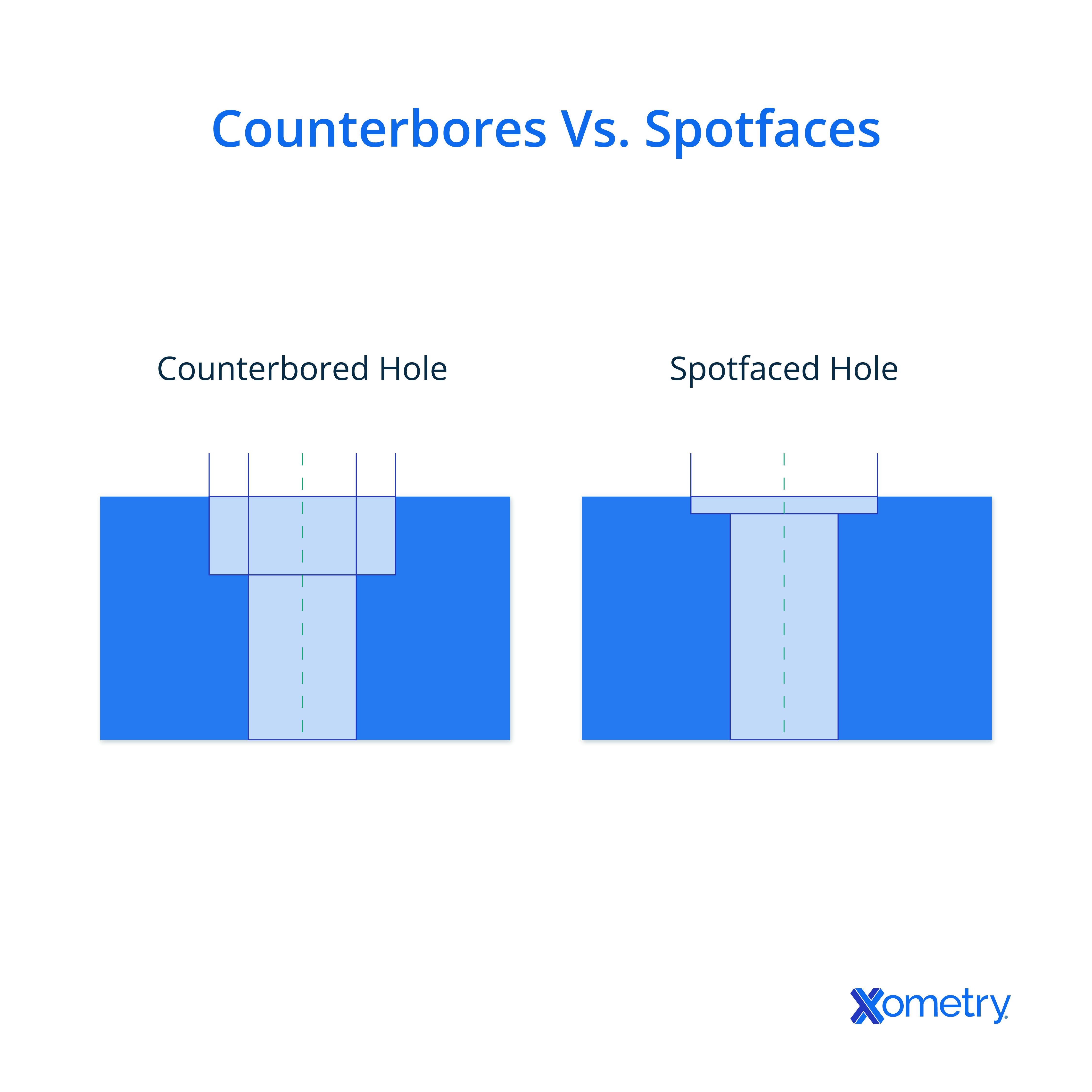
What Are the Other Main Types of Holes in Engineering?
The five most important and commonly employed (other than spotface) types of holes in engineering are:
- Through Hole: A parallel-sided hole of any diameter cut through a part.
- Blind Hole: A parallel-sided hole of any diameter, cut into a part but not penetrating to the other side. Blind holes retain the end shape of the cutter that made them, such as a twist drill (118 or 135° included angle conical tip), the ball-ended mill (hemispherical tip), end mill (flat, square tip), Forstner bit (flat, perpendicular cutter face with a tapered center spike for location), or auger (flat, perpendicular cutter face with a tapered, threaded center spike for location).
- Counterbore Hole: A flat-bottomed, cylindrical opening of larger diameter than the hole, cut at the outer face of a blind or through hole, whose diameter and depth are defined to fit a particular fastener head, or a family of fastener heads, or according to ANSI and ISO standards.
- Countersunk Hole: A conical cut at the outer face of a blind or through hole, whose diameter and angle are defined to fit a particular fastener head, or a family of fastener heads.
- Tapped Hole: A through or blind hole that has had part or all of its length cut such that thread results, expanding the effective diameter by cutting the thread features into the wall of the hole.
Summary
This article presented spotface holes, explained what they are, and discussed when to best drill this type of hole. To learn more about spotface holes, contact a Xometry representative.
Xometry provides a wide range of manufacturing capabilities, including CNC machining and other value-added services for all of your prototyping and production needs. Visit our website to learn more or to request a free, no-obligation quote.
Disclaimer
The content appearing on this webpage is for informational purposes only. Xometry makes no representation or warranty of any kind, be it expressed or implied, as to the accuracy, completeness, or validity of the information. Any performance parameters, geometric tolerances, specific design features, quality and types of materials, or processes should not be inferred to represent what will be delivered by third-party suppliers or manufacturers through Xometry’s network. Buyers seeking quotes for parts are responsible for defining the specific requirements for those parts. Please refer to our terms and conditions for more information.
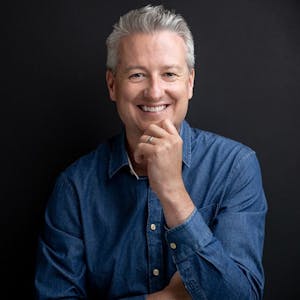