A laser cutter is a machine that uses a high-energy focused laser beam to cut into various plate or sheet materials to create 2-dimensional parts for both hobbyist and industrial applications. Typical materials include wood, steel, and some plastics.
Laser is an acronym for “Light Amplification by Stimulated Emission of Radiation” which describes the physics involved with generating laser light. While the fundamental physics of lasers remains unchanged, there are three common implementations of this technology: CO2, Fiber, and Nd:YAG lasers.
This article will describe in detail how a laser beam is generated and directed to the material for cutting, while also explaining the differences between the various laser cutting technologies.
The Laser Cutting Process
A laser cutter works by directing a very small-diameter, high-energy light beam vertically down onto a sheet or plate of material to cut it into a 2-dimensional profile by moving the laser in the X and Y directions along the machine bed. This beam melts or burns through the material in a pattern determined by a set of computer-generated instructions called G-code. A high-pressure stream of gas is sometimes used to blow the molten material out of the bottom of the material being cut. This process is done so that the waste material does not remain in the cut area and solidifies after the beam has moved on. In other cases, the laser beam simply vaporizes the material. The method of generating the laser beam differs between technologies, but in principle, they all follow the steps listed below:
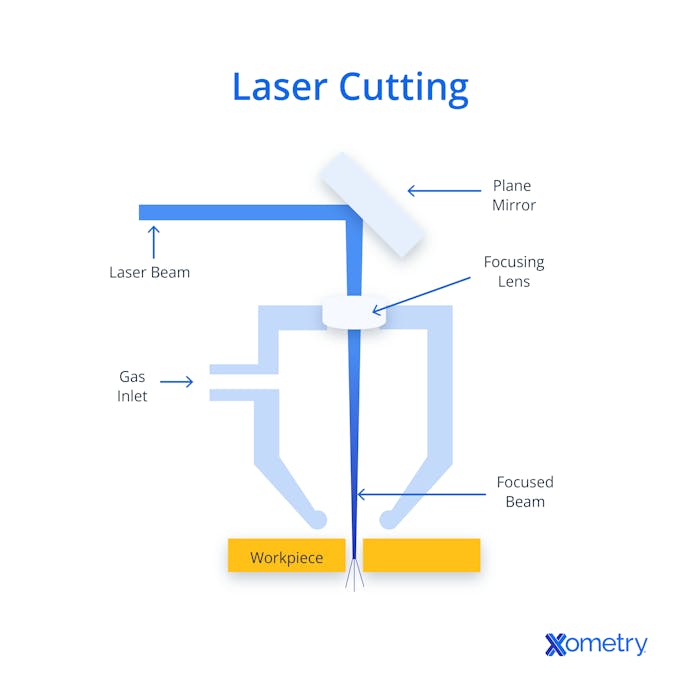
Step 1: Generation of G-code File
Before any cutting is performed, the G-code needs to be generated for the cutting job. G-code is a set of machine-readable instructions that tell the machine where to move the laser cutting head. The operator can generate the instructions by hand for simple shapes. More-complex shapes require CAM (computer-aided manufacturing) software to automatically generate this G-code from a supplied CAD (computer-aided design) file. This G-code must then be sent to the machine over a Wi-Fi connection or using a USB drive.
Step 2: Laser Beam Generation
The laser beam is generated inside the resonator. Different laser technologies use different mediums to generate the laser. However, the physics of beam generation is the same for the different laser technologies.
When an electron is stimulated by a photon it absorbs its energy to move to a higher energy state. An exact amount of energy from a photon is required to energize an electron to a specific energy state. This process is known as stimulated absorption.
The electron will decay to a lower orbital after a very short period of time. This decay is caused by small fluctuations in the quantum vacuum that cause it to fall back into a lower energy state. On decay, it will emit a photon. This process is known as spontaneous emission.
Spontaneous emission of a photon cannot be used to create a laser beam as the emitted photons will be incoherent as they move off in random directions. They will also drop down to the ground state too quickly. Lasers get around this issue by making use of materials with a metastable state. This process allows the electron to remain in a semi-excited state for longer when compared to the timescale involved with spontaneous emission (i.e. milliseconds vs. nanoseconds).
When a photon interacts with an already excited electron in its metastable state, it can cause the electron to fall back down into a lower energy orbital. When the electron does this, a photon is released with the same properties as the photon that initially perturbed it (i.e. same frequency, phase, and polarization). This process is called stimulated emission and is the mechanism used to create a laser beam. Once the process starts, it causes a cascade of photons to be released that then travel down the tube.
Step 3: Laser Amplification
When the initial phase of spontaneous emission occurs, the photons will shoot off in random directions. However, some will be perpendicular to the two mirrors on either end of the laser medium. This situation creates two light waves (one traveling left and one traveling right in the medium) which creates a standing wave consisting of constructive and destructive interference. When these standing waves are produced, this is referred to as resonance. The intensity of the light increases to the point where the semi-reflective mirror will allow some light through it, generating a coherent beam of laser energy. The remaining light continues to reflect in the laser medium to continue the stimulated emission of photons. Different laser technologies produce lasers with different wavelengths.
Step 4: Beam Direction and Focusing
As the beam exits the laser medium after amplification, it is directed either through a fiber optic cable (in the case of a fiber laser) or via a series of mirrors (for CO2 and Nd:YAG lasers). The beam is directed down into the sheet material through a lens that focuses the laser energy into a very small diameter to create a localized high-energy point. Note that the laser only has a single focus point of high intensity; the entire beam does not have the same cutting intensity. The difference in intensity is the reason why laser cutters are limited in the thickness of material they can cut, as the laser intensity drops off above and below the focus point.
Step 5: Material Cutting
Once the beam has been focused, it will begin to melt or vaporize the material. In the case of non-melting materials, like wood, the laser will burn through the material. With metals, the laser beam will melt the material, and a high-pressure jet of gas will blow the molten material away from the cut. The gas can either be inert nitrogen or argon or it can be oxygen which is used to accelerate the cutting process of steel.
Methods and Techniques of Laser Cutting
In general, a laser cutter is designed to focus energy to a small point to vaporize or melt a material. However, the method with which this energy is delivered can differ. Listed below are some of the common forms of laser cutting:
Fusion Cutting
Fusion cutting works by using a high-pressure jet of an inert gas like argon or nitrogen to blow out the molten material from the cut created by the laser beam. An inert gas is used so that it does not react with the molten metal. The inert gas also behaves as a shielding gas for the molten edge.
Flame Cutting
Not to be confused with oxy-acetylene cutting, laser flame cutting makes use of oxygen to assist with the cutting process by creating an exothermic oxidation reaction that helps reduce the laser energy requirements. The oxygen is also used to physically blow molten material from the cut. This process is also referred to as reactive laser cutting.
Remote Cutting
Remote cutting also referred to as sublimation or vaporization cutting, is used on very thin or sensitive materials. There is no gas used during cutting and the laser is typically moved using a galvo scanner that directs the laser with a series of mirrors. The laser vaporizes or ablates the material instead of gas blowing it away. Remote cutting can be extremely quick on thin material.
Thermal Stress Fracture
Thermal stress fracture cutting is a technique used to cut material by inducing stress in the base material. An example would be a method employed to cut aluminum nitride where an unfocused beam is used to melt a very thin layer of material on the surface of the part to form aluminum oxide. Aluminum oxide and the base aluminum nitride have different thermal expansion ratios and as the materials cool down at different rates, this causes a stress field that cracks the part along the laser line.
Stealth Dicing™
Stealth Dicing™ is a cutting technique used to place the focal point of the laser inside a material. The laser creates a modified layer internal to the wafer (typically in the production of semiconductors). Once the wafer has been cut, it is expanded using a flexible membrane to cause cracks to propagate through the wafer to separate the individual chips that were internally cut in the material. This technique is mainly used to cut silicon wafers and is preferred to other techniques like diamond wheel cutting which produce inferior chips and require coolant during cutting.
Vector Cutting
Vector cutting is a type of laser cutting used on parts that are made up of clean lines. An example of this would be business advertisement signs. Typically the laser cuts straight through the material.
Laser Rastering
Laser rastering is the most commonly used technique when it comes to engraving an image onto the surface of a material. It works by taking a bitmap image as input and then turning that image into a set of instructions for the laser cutter which then burns the image into the base material.
Types of Lasers Used in Laser Cutting
When it comes to laser cutting applications there are generally three types of lasers used. CO2 lasers make use of CO2 mixed with other inert gases as the lasing medium, whereas solid-state fiber and Nd:YAG lasers make use of a crystal as the lasing medium. The operating principle of these different lasers is fundamentally the same.
CO2 Lasers
A CO2 (carbon dioxide) laser consists of a tube with CO2, helium, and nitrogen gas enclosed within. Nitrogen and helium are included to increase laser efficiency. The nitrogen acts as a temporary store for energy that can then be passed on to the CO2 molecule as soon as it releases a photon. The helium, on the other hand, bleeds off any remaining energy from the CO2 molecule via kinetic energy transfer after it has released a photon, allowing it to accept energy from the nitrogen molecule.
On one end of the tube, there is a fully reflective mirror. The mirror at the other end is only partially reflective. The gas in the tube is ionized by a strong electric field which generates light by exciting the electrons in the CO2 molecules to a higher energy state, thereby generating a photon. When a photon passes near an atom in the excited state it causes that atom to release a photon. These photons then bounce off the two mirrors until there are enough collected photons to pass through the semi-reflective mirror. The temperature in the tube must be kept low for optimal efficiency; as such the tube is cooled with a low-temperature gas or liquid. In some systems, the gas is recycled to reduce running costs.
CO2 lasers have a wavelength of 10600 nm and are good, general-purpose lasers that can cut a wide range of materials as well as sheet and plate metals. However, CO2 lasers do struggle with materials with high thermal absorption and materials that are highly reflective.
Some common CO2 machines are the Glowforge® Plus for hobbyists or the Kern LaserCELLfor professional use.
Fiber Lasers
Fiber lasers make use of a dosed fiber optic cable as the lasing medium. A fiber laser beam is generated by pumping photons into one end of a quartz or boron silicate glass core fiber optic filament. These photons travel along the fiber optic filament until they reach the area that has been dosed with a rare earth element. Typical elements include neodymium, yttrium, erbium, or thulium. Each of these rare earth elements will produce a laser with a different wavelength when excited by the photons. The light is then amplified by making use of fiber bragg gratings. These gratings have the same function as the reflective and semi-reflective mirrors used in Nd:YAG and CO2 lasers and reflect the light back and forth causing a cascade of photons to be generated. Once the intensity reaches a certain point, the light can pass through the grating in the form of a high-intensity coherent beam of light. Like other lasers, a fiber laser also makes use of gas to assist with blowing molten material out of the path of the laser beam or to assist with cutting.
The generally shorter wavelength of fiber lasers means higher absorption, i.e. better for reflective materials and generates less heat during cutting. This is why fiber lasers are well suited to cutting reflective materials as well as materials that are good thermal absorbers like copper or gold.
The flexibility of the fiber optic cable means that a fiber cutting head can be easily mounted to a 6-axis robot arm, for example, without the need for multiple mirrors to direct the laser as would be required for a CO2 or Nd:YAG laser. Fiber lasers have higher electrical efficiency when compared to CO2 lasers.
One of the best industrial fiber lasers is the Trumpf TruLaser Series 1000.
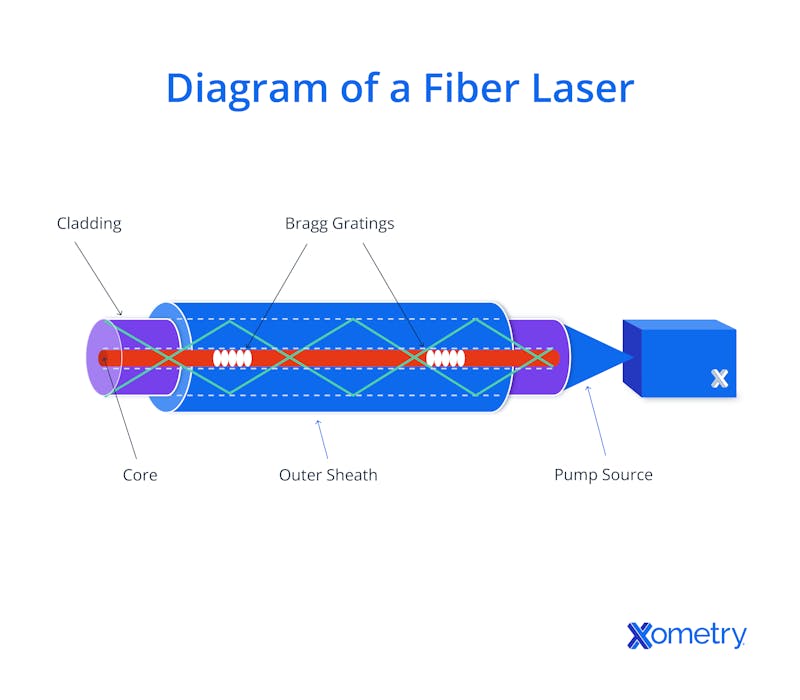
Nd:YAG/Nd: YVO Lasers
An Nd:YAG laser makes use of a neodymium (Nd) doped yttrium aluminum garnet crystal (Y3Al5O12). The doping replaces some yttrium ions (+- 1 %) with Nd3+ ions. This crystal is placed between two mirrors, one fully reflective and one semi-reflective. The pumping photon source is a xenon/krypton flash tube or a series of laser diodes. In the case of Nd:YAG crystals, the pumping source supplies photons that raise the energy level of the neodymium ions. The ions then decay to release a cascade of photons that generate a coherent laser beam after being reflected between the mirrors. Once a beam of coherent high-intensity light with a frequency of 1064 nm is generated, it is directed to the cutting head using mirrors and is finally focused to a point using a lens on the cutting head. Nd:YVO lasers make use of neodymium-doped vanadate crystals (YVO4) and operate in the same way as Nd:YAG lasers. However, Nd:YVO lasers have improved power stability, do not generate as much heat, and can produce more pulses per second.
Nd:YAG lasers have better beam quality and higher power density when compared to fiber lasers, making them ideal for marking and etching. However, Nd:YAG lasers have much higher operating costs and single-digit energy efficiencies.
An example of an Nd:YAG laser cutting machine is the Finecut 300.
Common Uses of Laser Cutting
Laser cutters employ a versatile manufacturing technology that is used in a range of applications as listed below:
- Sheet Metal Cutting: Laser cutters are widely used to cut both sheets and plates in a wide variety of materials including metals, plastics, and wood.
- Engraving: Laser cutters can be used to mark almost any material. Lasers can be used to add serial numbers to manufactured parts or for more artistic applications like wood marking.
- Laser Welding: Laser welding is a method used to precisely weld two metals or thermoplastics together using a laser beam instead of an electrical arc.
- Tube Cutting: Laser machines with a rotational axis can be used to cut complex profiles on hollow sections.
Advantages of Laser Cutting
Laser cutting is a widely adopted manufacturing technology. Listed below are some of the key advantages that make laser cutters such a popular manufacturing technology:
- Versatile Materials: Laser cutters can process almost any material. The thickness of material that can be cut with a laser cutter depends heavily on the laser power, the laser technology, and the material being cut.
- Limited Post-processing: Parts that have been laser cut do not require significant post-processing. However, in some cases, like cutting metal, cut edges may need to be deburred as there may be some slag attached to the cut edge.
- Narrow Cuts: Lasers can be focused on very tight beams, meaning that cut widths can be very thin (as small as 0.1 mm) depending on the material and the thickness.
- High Precision: Laser cutters do not experience any loads on the laser cutter head as is the case with other technologies like CNC routers. As such, laser cutters are very precise and accurate.
- High Speed: Laser cutters can cut out 2D profiles very quickly. Cutting soft materials like plastic can be done at high speeds.
- Automated: Laser cutters are highly automated. Some machines can even place raw material on the cutting bed and unload parts with limited human interaction.
- Tooling Costs: Unlike CNC machining, laser cutters do not make use of a wide range of tools. There is no tool wear due to friction as the laser cutter head does not contact the raw material.
- No Workholding: Laser cutters do not require clamps or other workholding equipment during cutting. Material can simply be placed on the cutting bed and will not move during the cutting process.
Disadvantages of Laser Cutting
Despite its many advantages, laser cutting still has some limitations as described below:
- High Power Consumption: Laser cutting consumes a lot of power, especially technologies like CO2 laser cutting.
- Limited Thickness: Due to the physics of focusing a laser beam into a high-intensity point, laser cutters are limited in how thick they can cut. They are generally limited to plate and sheet materials with a maximum thickness of up to 25 mm. While thicker material can be cut, this is not commonly done by standard fabrication shops.
- Dangerous Fumes: When cutting some materials like wood or plastic, dangerous combustion fumes can be generated that must be vented.
- Expensive Maintenance: Some laser technologies (such as CO2) consider the laser tube as a wearing item that must be replaced—at great expense.
- High Initial Cost: The initial capital investment of laser cutters is high. In some cases, cheaper technologies like flame cutters or plasma cutters may be better suited.
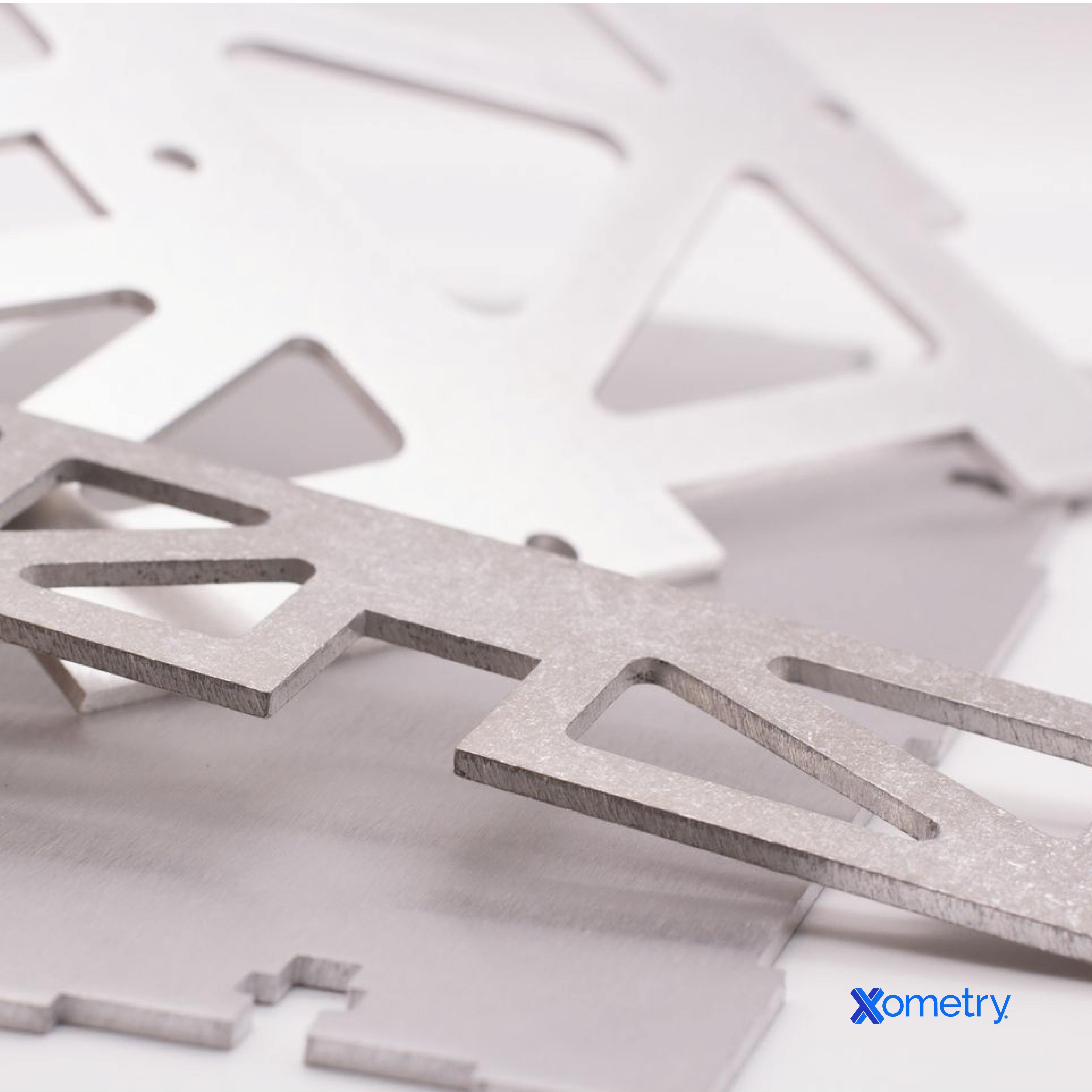
Common Laser Cutting Materials
Laser cutters can be used to cut a wide range of materials. Some of the most commonly cut materials are listed below:
Acrylic (PMMA)
Acrylic produces a smooth cutting edge but an exhaust system is required due to the flammable vapors generated. The gas pressure must be set so that it blows away the vapors while also cooling the cut edge to solidify it. Excessive air pressure will distort the cut edge while it is still molten. Acrylic is also known by the trade name of Perspex® or by its chemical name polymethyl methacrylate.
Carbon Steel/Mild Steel
Carbon steel is a term used to describe a wide range of steels with varying amounts of carbon as their main alloying element. Mild steel is also another type of carbon steel with a carbon percentage of less than 0.3 %. The higher the carbon content the stronger the steel. High-power lasers can cut up to 20–25 mm plate thickness.
Stainless Steel
Stainless steel is classified as a steel alloy containing chromium and/or nickel as its main alloying elements. Stainless steels are resistant to a wide range of chemicals. Stainless steels are readily cut on any laser cutting technology. However, fiber lasers are better suited for cutting stainless steel.
Aluminum
Aluminum is a blanket term used to describe a range of aluminum alloys with different alloying elements and applications. Aluminum has a good strength-to-weight ratio and as such is often used in aerospace applications. Aluminum is a reflective material when melted, making it relatively difficult to cut. While it is possible to cut aluminum with a CO2 laser, it is better to make use of a fiber laser for aluminum cutting.
Brass
Brass is an alloy of copper and zinc with some secondary alloying elements. Brass is corrosion resistant, electrically conductive, and has low friction. Typical applications include low-friction bushes and electrical applications.
Wood
Wood is readily cut with relatively low power (150–800 W) CO2 lasers. However, it is important to have an exhaust system as smoke is generated when laser cutting wood. Natural woods have a grain structure which can result in inconsistent finishes when engraving or cutting. Hardwoods and softwoods can be laser cut.
Hardboard
Hardboard is similar to MDF (Medium Density Fiberboard) but is denser, making it a stronger, more robust choice. The wood fibers are bonded with an adhesive. During cutting, this glue is vaporized. This releases dangerous fumes which require the use of an exhaust system. Hardboard is homogenous, meaning that cutting and engraving are consistent.
Cork
Cork is a soft wooden material that comes from the bark of the cork oak tree and is often used as shoe inserts, non-slip coaster bases, and pinboards. Cork can be laser cut and engraved very easily.
Leather
Leather is a hard-wearing, strong natural material used for shoes, belts, and wallets. Leather can be easily laser-cut and engraved and has high perceived value, especially when used to create personalized laser-cut items. There are also synthetic versions of leather called faux leather. However, some of these may contain PVC which produces corrosive vapors when laser cut.
Felt
Felt is a low-cost, non-woven fabric that is difficult to hand cut but cuts very easily with a laser cutter. Felt can be used for garments, decorative patches, and place mats. It is recommended to use 95–100 % wool felt, as synthetic felt is often made from acrylic and cuts very poorly.
Materials To NOT Cut in a Laser Cutter
Not all materials can be laser cut, and some materials can even produce harmful gases when cut. Listed below are some materials that should not be laser cut:
- Laminated Fiberglass: The glass fibers and epoxy tend to cut poorly. As such this material should not be cut.
- HDPE (High-Density Polyethylene): HDPE will tend to melt rather than vaporize, making it a poor material to laser cut.
- Polystyrene and Polypropylene Foam: These foams tend to catch fire when laser cut.
- ABS (Acrylonitrile Butadiene Styrene): ABS will tend to melt instead of vaporizing and will also generate toxic cyanide gas during cutting.
- PVC (Poly Vinyl Chloride): PVC produces chlorine gas when cut with a laser. This causes corrosive damage to the optics and laser cutting equipment.
- Polycarbonate (PC): Polycarbonate sheets thicker than 1 mm tend to catch fire when cut and will also discolor.
To learn more, see our guide on the Types of Bad Materials for Laser Cutting.
Dangers of Laser Cutting
Like most industrial machinery, laser cutters present some dangers as listed below:
- Burning: Laser cutting of some materials, like wood, can result in burning if not done correctly.
- Toxic Gas: Some materials will release toxic or corrosive fumes when cut.
- Eye Damage: When trying to cut very reflective materials, there's a chance the laser beam can be reflected into the eyes. This can cause severe eye damage.
- Sharp Cut Edges: A laser cutter can potentially produce sharp cutting edges. These can cause severe cuts if not deburred or handled correctly.
Xometry provides a wide range of manufacturing capabilities including CNC machining, 3D printing, injection molding, laser cutting, and sheet metal fabrication. Get your instant quote today.
Copyright and Trademark Notices
- Perspex® is a trademark of Perspex Distribution Ltd
- Glowforge® is a trademark of Glowforge Inc. CORPORATION DELAWARE
- Stealth Dicing™ is a trademark of Hamamatsu Photonics
Disclaimer
The content appearing on this webpage is for informational purposes only. Xometry makes no representation or warranty of any kind, be it expressed or implied, as to the accuracy, completeness, or validity of the information. Any performance parameters, geometric tolerances, specific design features, quality and types of materials, or processes should not be inferred to represent what will be delivered by third-party suppliers or manufacturers through Xometry’s network. Buyers seeking quotes for parts are responsible for defining the specific requirements for those parts. Please refer to our terms and conditions for more information.
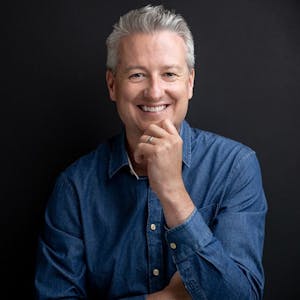