Controlled-fracture laser cutting is a technique developed specifically for hard, brittle materials like ceramics and glass. Such materials cannot easily be cut with other, more common laser cutting techniques, like laser fusion cutting. Laser fracture-controlled cutting techniques can cut ceramics with better-cut quality and higher perpendicularity on the cut edge as opposed to other manual techniques like scoring and mechanical breaking.
This article will describe how controlled-fracture laser cutting works, how it differs from other more traditional techniques, and what materials can be cut using this method.
What Is Laser Fracture-Controlled Cutting?
Fracture-controlled laser cutting refers to a process developed to cut hard, brittle materials like glass and ceramics. Instead of melting or vaporizing the material, this process induces thermal stresses in the material to force the development of a controlled crack extending from the top to the bottom of the workpiece. Fracture-controlled laser-cutting requires far less energy to cut hard, brittle materials than other laser-cutting processes.
How Does Laser Fracture-Controlled Cutting Work?
Two main controlled-fracture laser cutting techniques have been developed. The first method consists of laser heating a small area of material along the intended cut path. The material tries to expand, but it is held in place by the surrounding cold material, which puts it into a state of compression. After the laser moves on, the material cools and contracts away from the score line, leaving residual tensile stresses. These stresses are sufficient to initiate and then propagate a crack all the way through the thickness of the brittle material.
The second method is better suited for thick alumina (>10 mm), in this case, a two-laser system is used. The first is a highly focused fiber laser, which scores the material. Next, an unfocused CO2 laser applies enough thermal energy onto the scored line to initiate a crack. The cutting speed is limited to 1.5 mm/s. The scoring laser and the heating laser each only need 50 W of power to be effective. In contrast, standard fusion laser-curing techniques would require a 500 W laser to cut the same thickness, and the cut edge would be of comparatively poor quality, with multiple microcracks.
The cracking process goes through three stages: crack initiation, stable crack growth, and then finally unstable crack growth. At the end of this process, a clean cut is formed with a fraction of the energy that would be needed to cut through the material relying only on high-temperature lasers.
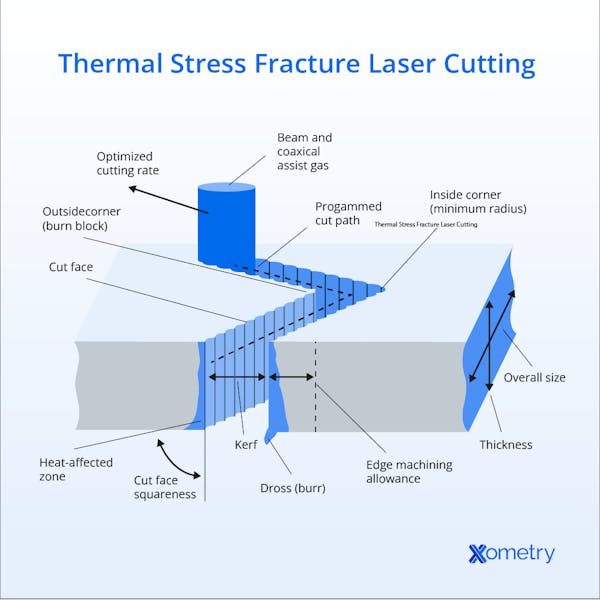
What Sets Fracture-Controlled Cutting Apart From Other Cutting Methods?
Laser fracture-controlled cutting was specifically developed for the cutting of hard brittle materials like ceramics or glass. Fracture-controlled laser cutting does not melt or vaporize through the entire material thickness to separate materials along a desired path. Instead, it only heats the surface of the material. This induces thermal stresses that cause the material to fracture through its thickness along the beam's line of travel. Fracture-controlled laser cutting is not suitable for plastics or metals, which are better cut using standard vaporization and fusion laser cutting techniques.
What Materials Can Be Cut Using Laser Fracture Control?
Fracture-controlled cutting is best suited to hard and brittle materials. For this reason, ceramics and glass are the materials that can most benefit from this technique. Some common materials are listed below:
- Silica Glass
- Alumina
- Zirconia
- Silicon Carbide
- Silicon Wafers
- Ruby
- Porcelain
What Kind of Laser Is Used for Laser Cutting With Fracture Control?
Fracture-controlled cutting refers to the technique of splitting brittle materials with lasers. Several different types of lasers can be used, including CO2 lasers and Nd:YAG (fiber lasers). In applications where thicker sheets are to be cut, a dual laser system is used. A focused fiber laser is used to score the material; thereafter, an unfocused CO2 laser applies thermal energy to the scored area to initiate a crack.
What Are The Laser Fracture-Controlled Cutting Machines?
Fracture-controlled cutting can be performed with any laser. However, this cutting method is very energy efficient and can be performed with low-power lasers on the order of 60 W. The most common types of lasers are listed below:
- CO2: CO2 lasers are the type most commonly used for fracture-controlled cutting. The lower power variants used for this cutting process are relatively inexpensive.
- Nd:YAG: Nd:YAG (or fiber) lasers are also used for fracture-controlled laser cutting. These machines are generally more expensive than CO2 lasers but do not require as much maintenance. High pulse-rate fiber lasers are used to cut material like glass using controlled fracture techniques but are limited to sheets as thin as 1 mm, and only require a laser with a power of 5 W.
- Combination: In some cases both Nd:YAG and CO2 lasers are used for fracture-controlled laser cutting. The fiber laser will score the material with a high-focus beam, and an unfocused CO2 laser will pass over the score line to initiate a crack.
What Is the Process of Laser Fracture-Controlled Cutting?
The laser fracturing process depends on the precise control of laser power and cutting speed to control the development of a crack. The three steps in the crack formation process are listed below:
- Fracture Initiation: The laser applies heat to the material. This causes compressive stresses to develop due to the localized heating near the laser, the material expands and presses into the surrounding cool material. This induces residual tensile stress as the material cools once the laser has moved onward. This concentrated tensile stress causes a crack to initiate in line with the direction of travel of the laser.
- Stable Fracture Growth: Once the crack has initiated it begins following the laser as the area behind the laser cools and cracks through the thickness of the material. This crack lags behind the laser.
- Unstable Fracture Growth: During this stage, the crack grows almost instantaneously from the surface of the material straight through, creating a clean line of separation in line with the laser's direction of travel.
Which Industries Can Benefit From Using Fracture-Controlled Laser Cutting?
Fracture-controlled laser cutting is primarily used on ceramics and other brittle, hard-to-process materials. It is used in all industries that make use of these materials. Some typical industries include semiconductor manufacture, MEMS (microelectromechanical sensors), aerospace, automotive, and medical sectors.
Is Fracture-Controlled Laser Cutting Faster Than Other Methods?
No, fractured-controlled laser cuts do not take less time than other cuts made by other techniques. In most cases, fracture-controlled laser cutting is a relatively slow process compared to other laser cutting processes. Controlled-fracture laser cutters typically operate at around 10 mm/s in order to effectively control the initiation and growth of the crack. Fusion and vaporization laser cutting techniques typically cut at hundreds of mm/s.
Does Fracture-Controlled Cutting Require High Laser Power?
No, the laser power in fracture-controlled laser cutting is typically much lower than in fusion-based laser cutting methods. This is because the laser applies a very small and precise amount of energy, solely for the purpose of creating localized thermal stresses on the surface. These stresses initiate the crack growth which splits the material. Fusion cutting requires enough energy to melt all the way through the thickness of the material. Ceramics have very high melting points, and applying enough energy to melt through them can cause thermal stresses radiating away from the cut line, which can cause microcracking near the cut edge. The laser power used in fracture-controlled laser cutting can be around 50 W.
Is the Cutting Speed for Fracture-Controlled Cutting Fast?
No, the cutting speed for fracture-controlled laser cutting is typically very slow (less than 10 mm/s in most cases). The reason for this is that the crack growth needs to follow the laser beam. If the speed is too high, that could result in the crack stopping or moving in the wrong direction.
Summary
This article presented fracture-controlled laser cutting, explained what it is, and discussed when to use this laser cutting method best. To learn more about fracture-controlled laser cutting, contact a Xometry representative.
Xometry provides a wide range of manufacturing capabilities, including sheet cuttin and other value-added services for all of your prototyping and production needs. Visit our website to learn more or to request a free, no-obligation quote.
Disclaimer
The content appearing on this webpage is for informational purposes only. Xometry makes no representation or warranty of any kind, be it expressed or implied, as to the accuracy, completeness, or validity of the information. Any performance parameters, geometric tolerances, specific design features, quality and types of materials, or processes should not be inferred to represent what will be delivered by third-party suppliers or manufacturers through Xometry’s network. Buyers seeking quotes for parts are responsible for defining the specific requirements for those parts. Please refer to our terms and conditions for more information.
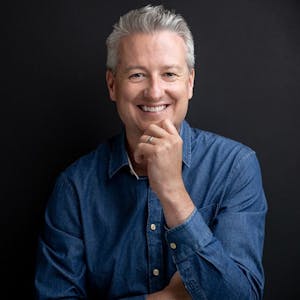