Ever since lasers burst onto the manufacturing scene in the ‘60s, they’ve come in handy for everything from cutting and welding to 3D printing. They’re also widely used in engraving and etching machines by hobbyists and major manufacturers alike. Both laser etching and engraving can make intricate patterns and jazz up or personalize things like pens, jewelry, and nameplates, and it can be a common go-to for brand logos and motifs. But their usefulness isn’t limited to aesthetics. These methods are used for marking permanent traceable part identifiers, like serial numbers, QR codes, and barcodes, in very high resolution (even on the smallest of parts).
Part identification is actually a government safety regulation to help figure out the causes of failures or accidents. Parts that need to be labeled include drive shafts, engine blocks, and brake discs, to name just a few in the automotive sector, and in aerospace, it could be electrical circuit boards, landing systems, turbine blades, and hardware like bolts. Interestingly, in the medical industry, tools and other important items like forceps, scalpels, catheter connections, tubes, and implants are also marked so that they can be clearly identifiable.
Just a quick clarification before we go into the differences between laser engraving and laser etching: these are not forms of laser marking. Marking labels the parts with a low-powered laser and doesn’t change the part’s material. In both engraving and etching, the material’s surface is permanently marked—in that it’s deformed—and can’t be scratched off. Now that’s out of the way, let’s get to it. In this article, you’ll learn about these two laser techniques, how they work, and how they’re different from one another.
What is Laser Engraving?
The laser in a laser engraving machine makes shallow cuts by vaporization. In this method, excess material is removed to make the complex patterns and designs required. The process needs a very high laser power to reach the required temperature for vaporization.
What is Laser Etching?
Similarly, laser etching also removes material to make the markings, but instead of vaporizing it, the workpiece is melted where necessary. The laser causes the material to expand at the point of focus, and this leaves a raised mark that can be seen and felt with your fingers. It doesn’t go as deep as to cut the workpiece, but just enough to mark it. Below is a diagram of how this process works.
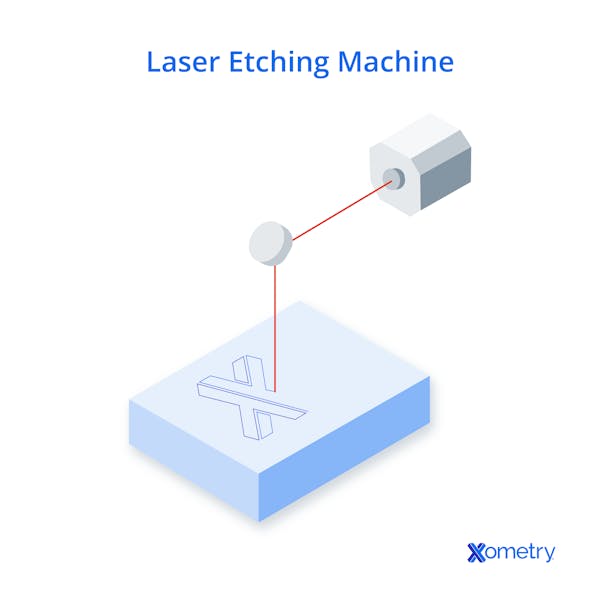
In addition, laser etching has fewer power requirements and less energy density than laser engraving (melting is a lot more cost-effective than vaporizing, in both high and low production volumes), and is also a lot quicker. Here’s a picture of laser-engraved parts made by the Xometry team.
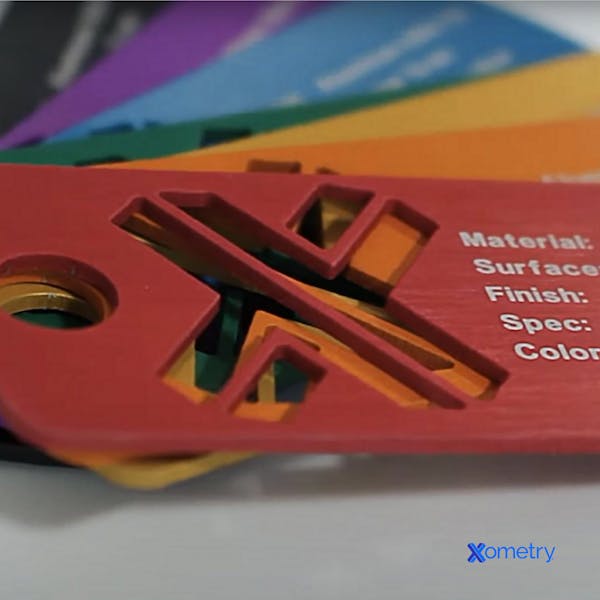
Factor | Laser Engraving | Laser Etching |
---|---|---|
Factor Process | Laser Engraving Vaporization | Laser Etching Melting |
Factor Cut depth | Laser Engraving Up to 0.020 inch (varies with laser system’s power rating) | Laser Etching About 0.0001 inch |
Factor Cost (production, volume) | Laser Engraving More expensive | Laser Etching More cost-effective |
Factor Versatility | Laser Engraving Many different materials, but higher power requirements and slower process | Laser Etching Broader range of materials, quick production, low energy usage |
Factor Output durability | Laser Engraving Long-lasting and wear-resistant markings as these are cut deeper | Laser Etching Lower, markings are only produced at surface level |
Factor Power requirement | Laser Engraving Higher | Laser Etching Lower |
Laser Engraving vs. Etching
It’s worth noting that the cut depth can vary depending on the laser system’s power rating, energy density, and the material properties (i.e., its reflectivity). Wood, leather, and other organic materials are easier to etch or engrave because they’re not reflective so can readily absorb the lasers’ energy. Metals and other inorganic materials that tend to be reflective could make these processes a little more challenging.
Vaporization/Melting Temperatures of Common Metals
In the below table, you’ll find the vaporization and melting temperatures of some common metals used with laser engraving and etching. As you’ll see, vaporization temperatures are much higher than melting temperatures—sometimes twice as high. The table only covers metals but both processes can also be used on wood and leather (as briefly mentioned above), as well as different types of plastic.
Material | Laser engraving (vaporization temperature) | Laser etching (melting temperature) |
---|---|---|
Material Cast iron | Laser engraving (vaporization temperature) ~5,072°F | Laser etching (melting temperature) ~2,372°F |
Material Aluminum | Laser engraving (vaporization temperature) ~4,352°F | Laser etching (melting temperature) ~1,220°F |
Material Carbon steel | Laser engraving (vaporization temperature) ~4,892°F | Laser etching (melting temperature) ~2,552–2,732°F |
Material Stainless steel | Laser engraving (vaporization temperature) ~4,892–5,432°F | Laser etching (melting temperature) ~2,732°F |
Material Titanium | Laser engraving (vaporization temperature) ~5,972°F | Laser etching (melting temperature) ~3,038°F |
Vaporization/Melting Temperatures of Common Metals
How Xometry Can Help
If you’re thinking about laser engraving or etching, but aren’t sure which to go for, reach out to a Xometry rep who will be glad to assist you. The choice largely depends on what type of part you’re making and what it will be used for. If the decision is mainly down to your budget, then laser etching is the more cost-effective route, and it uses much less energy than laser engraving, too. It’s also a much faster process because the laser doesn’t have to cut the material very deeply.
In addition to these two laser processes, we have a wide range of manufacturing services to offer for many prototyping and production needs. If you already have your designs at the ready, you can also get a quick and totally free quote by uploading them to the Xometry Instant Quoting Engine®.
Copyright and Trademark Notices
- Boss Laser™ is a registered trademark of BOSS LASER.
- Muse® is a registered trademark of FSL.
- Beamo® is a registered trademark of FLUX.
Disclaimer
The content appearing on this webpage is for informational purposes only. Xometry makes no representation or warranty of any kind, be it expressed or implied, as to the accuracy, completeness, or validity of the information. Any performance parameters, geometric tolerances, specific design features, quality and types of materials, or processes should not be inferred to represent what will be delivered by third-party suppliers or manufacturers through Xometry’s network. Buyers seeking quotes for parts are responsible for defining the specific requirements for those parts. Please refer to our terms and conditions for more information.
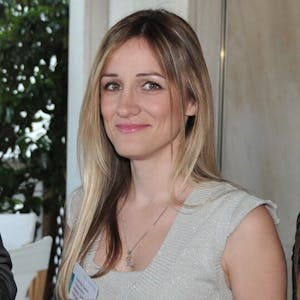