Thanks to it being a laser-safe material, Mylar® is often used to make high-quality stencils with laser engraving and cutting. Read on to learn how.
What is Mylar?
Mylar®—a trade name owned by Dupont—is a grade of biaxially-oriented polyethylene terephthalate (PET) film. It’s usually made into thin sheets of different thicknesses via extrusion or casting (most commonly the former), and is available as a clear film, or in a range of colors. It’s often used to make stencils—sewing, etching, art, solder—and other applications, including:
- Airbrushing and painting
- Scrapbooking
- Cardmaking
- Quiltmaking guides
- Custom product labels and tags
- Architectural model making
- Lamp shades
- Other artwork
Stencil Laser Engraving and Cutting
Stencils are basically templates for making multiple exact replicas of a shape or pattern onto a surface. The cut-out parts of a stencil are the design, so when ink or paint is applied, the holes allow the paint to go through and create the pattern while the rest of the stencil material acts like a mask to keep the rest of the surface unpainted. Apart from single-use stencils, where good old, budget-friendly cardboard will suffice, most stencils need to be made from durable and flexible materials… like Mylar!
Thin metals, cardboard, and other plastics can also be used. Acrylic, for example, is a rigid plastic that can be either clear or colorful, and is often used for engraved awards or signs—but it can only be used on flat surfaces. If the stencil has to come in contact with chemicals or needs to be welded afterward to create more complex designs, polypropylene is used. Metal, while durable and long-lasting, is harder for entry-level cutters to zap through, so is typically reserved for industrial machines. Mylar offers all the benefits of the mentioned materials and more—it’s flexible, durable, resistant to chemicals, and easy to cut with most CO₂ lasers, which is why it’s chosen for stencils. But not all Mylar sheets are suitable for laser cutting; for best results, these should be between 4–10 mils thick, and uncoated (unless the coating is laser-cutter safe).
While there are many ways to make a stencil, laser engraving/cutting is quick, easy, and highly repeatable—which is why it’s rapidly becoming the go-to method. Stencil-making is a relatively niche laser-cutting application; it’s more commonly used for industrial jobs. However, it follows all the same basic laser-cutting principles. Laser cutters produce impressively clean design edges, so the stencil comes out with excellent quality and, ultimately, produces beautifully precise artwork. It’s also an easy process because laser cutters—even low-power, entry-level machines—can cut through thin plastic sheets effortlessly.
How to Laser Engrave/Cut Mylar Stencils
After you’ve designed the stencil and are ready to make it, the next step—and arguably the most important— is adjusting the machine’s settings.
Recommended Settings
The best laser cutter power and speed settings for Mylar depend on the specific machine you’re working with, as well as the material’s thickness. You’ll also need to consider the machine’s focus height (although most of them offer automatic settings), and how many times you need to go over it for a complete cut.
Below you’ll find the general recommended settings for cutting Mylar sheets with a CO₂ laser cutter. The last row provides specific settings for the Glowforge Pro, which, while also a CO₂ laser, has its own built-in software that automatically adjusts the settings.
Use | Thickness | Power and Speed | Passes | Focus Height | Notes |
---|---|---|---|---|---|
Use Presentation | Thickness 5 mil / 0.125 mm | Power and Speed 8W at 120 mm/s | Passes One | Focus Height Auto (manual if needed) | Notes Cut quickly to avoid overheating/curling |
Use Presentation Parts | Thickness 8–14 mil / 0.203–0.356 mm | Power and Speed 30–40% on a 40W laser (12–16W) at 15–50 mm/s | Passes May need more than one | Focus Height Manual (better precision) | Notes Slow speed and high power for clean edges (especially for thicker materials) |
Use General | Thickness 4 mil / 0.1 mm | Power and Speed 25–40% on a 40W laser (10–16W) at 100–200 mm/s | Passes One | Focus Height Auto (manual if needed) | Notes At least 30W is recommended for clean cuts |
Use General | Thickness (Glowforge Pro or similar) 4 mil / 0.1 mm | Power and Speed 25W at 200–250 mm/s | Passes One (second if needed) | Focus Height Auto or manual | Notes Trial runs are recommended before final cutting |
Recommended Settings for Cutting Mylar
Process Steps
Once you’ve got your settings in check, the process entails the following three simple steps:
- Converting the design image into vector format, which can be done with free software, i.e., Inkscape (you could also use designs that already come in vector format, like SVG, DXF, or AI, as these extensions make it easier to convert the edges into paths for the laser cutter to follow).
- Securing the Mylar sheet to the base of the machine's cutting bed completely flat (any raised areas can mess up the edges).
- Once it’s cut, you can take the stencil off the cutter and put it to use!
Laser Cutting Mylar with Solder Paste
Mylar and laser cutters also come together to make stencils for applying solder paste on the tiny surface mount device (SMD) parts on a circuit board—something that’s practically impossible to do with a standard soldering iron. In more professional settings, a steel or Kapton stencil is used, but this is a good budget alternative. Here are the steps:
- The planned positions and shapes of how the components will fit on the circuit board are extracted to a CAD file format (i.e., .dxf) so that the laser cutters software can read it and make the cutting instructions. These must account for the width of the laser’s cutting path.
- The CAD file is converted into a set of instructions in the language that the laser cutter can understand: G-code.
- The machine cuts the small solder pad openings from a sheet of stainless steel or a polyimide film, or the areas can be vaporized by engraving at a suitably high power.
- Once the cut is complete, the Mylar sheet is aligned with the circuit board (the fact it’s see-through makes this much easier).
- With the stencil in place, solder paste is spread over it, filling in the cut-out areas.
- The SMD parts can then be placed onto the board and soldered into place.
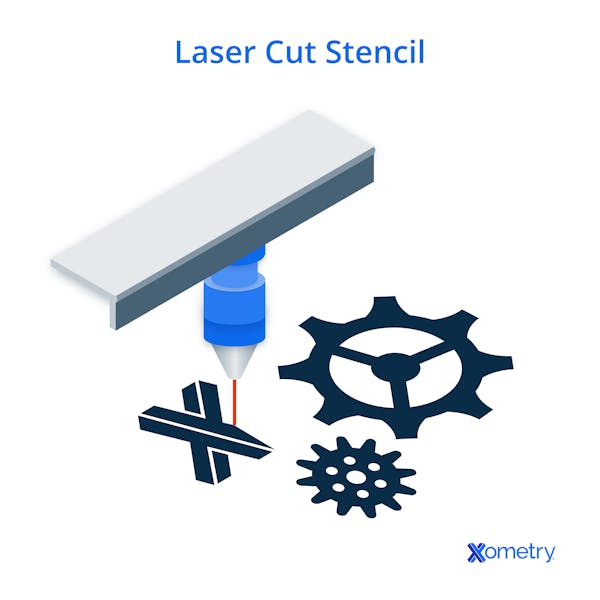
FAQs on Mylar and Stencil Laser Engraving/Cutting
What’s the difference between ‘general’ and ‘presentation’ laser-cut Mylar parts?
General quality stencils don’t really need to have high-quality cosmetic finishes, meaning they can be made at higher speeds and at lower costs—particularly useful for one-off applications. You’d still want your general-use stencils to have crisp edges for a clean transfer, so a balance of cutting speed and power is important to avoid excessive melting or incomplete cuts.
Why does the sheet thickness affect the required laser cutter power?
Cutting at too low a power on thicker Mylar sheets can result in incomplete separation of the plastic, while cutting at too high a power level on thin sheets will give you a ragged edge as the increased energy input will melt the cut path instead of vaporizing it. So, the thicker the material, the more laser power needed to cut it—although reducing the speed could help, too.
Which laser-cutting machine is best for Mylar?
In general, the CO2 laser cutters are the type best suited to Mylar. We recommend the following models:
- Glowforge Pro: A 40 W model—one of the most popular on the market—with excellent and high build quality and a large user base.
- OM Tech: A low-cost option available in a range of laser powers, the 40 W is recommended for stencil cutting.
- Flux Beamo: A good mid-range machine with a 30 W max power; can make high-quality stencils and is reasonably priced, too.
How Xometry Can Help
To learn more about making stencils with Mylar and laser cutting/engraving, get in touch, and one of our representatives will guide you in the right direction. We also offer a whole bunch of manufacturing services in addition to laser cutting, like CNC machining and, our forte, 3D printing. Your free, no-obligation quote is just a click away.
Copyright and Trademark Notice
- Mylar® is a trademark of DuPont Teijin Films™
Disclaimer
The content appearing on this webpage is for informational purposes only. Xometry makes no representation or warranty of any kind, be it expressed or implied, as to the accuracy, completeness, or validity of the information. Any performance parameters, geometric tolerances, specific design features, quality and types of materials, or processes should not be inferred to represent what will be delivered by third-party suppliers or manufacturers through Xometry’s network. Buyers seeking quotes for parts are responsible for defining the specific requirements for those parts. Please refer to our terms and conditions for more information.
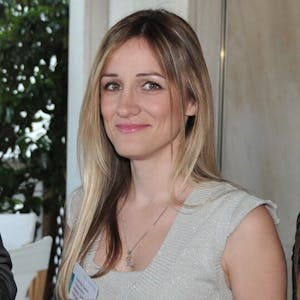