Plasma cutting and flame cutting are two thermal cutting techniques that are capable of cutting many kinds of metals, including steel. While they have this capability in common, these two techniques differ.
The first major difference shows in their working principle. Plasma cutters use plasma, which is created by combining an electrical arc with ionized gas. Flame cutters, on the other hand, cut materials by means of an open flame fed by oxygen and a fuel source. These methods also differ in terms of ideal application, accuracy, speed, and more. Flame cutters are mainly used to cut thicker materials but are limited to carbon-containing metals, whereas plasma cutters are faster, more accurate, and ideal for cutting thin, conductive sheet metals. This article will compare plasma vs flame cutting, taking a closer look at their differences, applications, working principles, and more.
What Is Plasma Cutting?
Plasma cutting is a thermal cutting process that uses an electrical arc and ionized gas to produce a plasma jet that slices through conductive materials. The plasma arcs can cut at temperatures of up to 30,000°C and can produce high-quality cuts very quickly.
How Does Plasma Cutting Work?
A plasma cutter propels a stream of plasma, or highly energized ionized particles, into an electrically conductive work material. Typically, a compressed gas, such as air, nitrogen, oxygen, or argon, is forced through a thin nozzle at high speeds to form the plasma stream. The best plasma gas will depend on the material being cut and may be a blend of gasses. That gas flow is then energized using an electric current produced using a tungsten electrode. This ionizes the molecules, converting the gas into a plasma arc. The workpiece is connected to the torch’s electrical circuit using a grounding clamp. It gets cut by the plasma arc by first melting it, and then blowing the molten metal away.
Some form of plasma cutting software must direct the cutting machine for mechanized cutting applications. Most fabricators and manufacturers use CAD/CAM nesting software for this purpose since they typically have the most capabilities and features. In some circumstances, CNC software can be used to design individual components or small batches. Virtually every part of the plasma cutting procedure can be controlled and automatically set up by some CAD/CAM nesting software.
What Are the Advantages of Plasma Cutting?
The main advantages associated with plasma cutters are listed below:
- It is a much faster and more efficient method than flame cutting.
- Can cut most metals that are electrically conductive, whereas flame cutters are primarily limited to steel and cast iron. Plasma cutters are also great for metals like: copper, aluminum, steel, and titanium.
What Are the Disadvantages of Plasma Cutting?
Plasma cutters do have some disadvantages. These include:
- They cannot cut through thick materials the way flame cutters can. This process should not be used to cut materials that are more than a few inches thick.
- The material that you want to cut must be conductive to form part of the plasma cutter’s electrical arc.
What Is Flame Cutting?
Oxy-fuel cutting, or flame cutting, is a thermal cutting technique. It uses oxygen and a fuel source (called oxy-fuel) to produce a flame that is hot enough to burn through different materials. The main advantage is that flame cutters can slice through thick materials. However, this technique can only be used on metals that contain carbon, or more specifically: carbon steels, cast irons, and low-alloy steels.
How Does Flame Cutting Work?
Flame cutting works by using a neutral flame (one that is neither oxidizing nor reducing) from the torch's jet to heat the metal to its ignition temperature. This is done without melting it before the cutting process begins. When that temperature is attained, the machine intensifies the flame by releasing a second stream of oxygen through the central jet. An additional level of precision can be achieved by using a trigger to control the central jet. This extra burst of intense heat then penetrates the material.
What Are the Advantages of Flame Cutting?
This technique has some advantages over its competitors. Flame cutters:
- Can cut metal items up to two feet thick.
- Are relatively cost-effective.
- Are portable and easy to operate, making them ideal for fieldwork.
What Are the Disadvantages of Flame Cutting?
The disadvantages of flame cutters include:
- They are limited in terms of the materials that can be cut. Users are limited to cutting carbon steel, cast iron, and alloy steel.
- Material edges frequently come out looking imperfect thanks to a thin, irregular coating of re-solidified metal (the decarburized layer). Depending on the application, this portion may need to be cut or ground away after the primary cut is complete. The surrounding material may also be affected by the intense heat in the heat-affected zone, necessitating post-cut treatment to prevent future hardening and cracking.
Which Is Better, Plasma Cutting or Flame Cutting?
Selecting the best cutting tool for you will depend on multiple factors: your desired accuracy, the type of material that you’d like to cut, and the thickness of the material. Plasma cutters can be used on all types of conductive metals but are limited in terms of thickness. However, they produce more accurate cuts due to a smaller kerf size (the slit or notch made by the device). Flame cutters, on the other hand, perform well on thick workpieces, but are limited to metals that contain carbon. Flame cutters leave you with larger kerf sizes and may create distorted edges.
Difference Between Plasma Cutting and Flame Cutting in Terms of Machine Used
In terms of the machines themselves, plasma cutting devices are generally more advanced and require more sophisticated control systems than flame cutting machines. Plasma cutters are typically more expensive than flame cutters, but they offer greater precision and speed and can cut a wider range of materials. Flame cutting machines, on the other hand, are simpler and less expensive, making them more accessible options for smaller-scale cutting operations. Flame cutters are also more portable — no power supply is required, after all — making them ideal for on-the-go applications and fieldwork.
Difference Between Plasma Cutting and Flame Cutting in Terms of Cost
Plasma cutting operations are typically more expensive than their flame cutting counterparts for a number of reasons. The plasma-cutting machine itself is much more expensive than an average flame cutter. Plasma devices can range anywhere from $850-1,700 whereas flame cutters typically range between $230-500. Plasma cutters can be expensive to run on small projects. However, they are more efficient on the whole; they produce less material waste and work faster than flame cutters resulting in reduced labor costs.
Another thing to consider is the cost of consumables. Plasma cutting typically requires compressed air or an inert gas such as nitrogen or argon as well as electrodes, nozzles, and other parts that may need to be replaced periodically. Plasma cutters also demand a lot of electricity, which can get expensive. Flame cutting, on the other hand, requires only fuel gas and oxygen, which may be less expensive than the gasses used in plasma cutting.
Difference Between Plasma Cutting and Flame Cutting in Terms of Materials Used
Plasma cutters and flame cutters are both able to cut metals. However, plasma cutters can only cut conductive metals and flame cutters are limited to carbon-containing metals (cast iron, carbon steel, and low-alloy metals).
Difference Between Plasma Cutting and Flame Cutting in Terms of Cutting Process
Plasma cutting uses a plasma torch, which is essentially an electrically conductive gas that is energized to a high temperature and forced through a small nozzle. The resulting plasma stream can reach temperatures of up to 30,000°C. This makes it capable of cutting through a wide range of metals, including steel, aluminum, and copper. Plasma cutting machines use a high-frequency electrical arc to ionize the gas and create the plasma stream, which is then focused onto the metal workpiece.
By comparison, flame cutting uses a torch that burns a fuel gas — typically acetylene or propane — along with oxygen to create a flame. The flame heats the metal to its ignition temperature. At that point, a high-pressure stream of oxygen is directed onto the metal, causing it to oxidize rapidly and melt away. Flame cutting is a common method for cutting thicker metals and is particularly effective on carbon steel.
Difference Between Plasma Cutting and Flame Cutting in Terms of Cutting Quality
Plasma cutting uses a high-velocity jet of ionized gas (plasma) to melt and cut through the metal. It can achieve high cutting speeds and can operate on a wide range of metals, including: steel, stainless steel, aluminum, and copper. Plasma cutting produces a narrow, precise cut with minimal kerf width (the amount of material removed during cutting) and minimal heat-affected zone (the area of metal that is affected by the heat of the cutting process).
Flame cutting, on the other hand, uses a more familiar flame. It’s usually fueled by oxygen and a fuel gas such as acetylene or propane. It heats the metal to its ignition temperature and then blows away the molten metal with a jet of oxygen. Flame cutting is a slower process than plasma cutting and is generally used for thicker materials. The heat from the flame can cause distortion and a wider kerf. Additionally, the heat-affected zone can be more significant.
Difference Between Plasma Cutting and Flame Cutting in Terms of Accuracy
Plasma cutters are usually more accurate than flame cutters due to their small kerf size and heat-affected zones.
Difference Between Plasma Cutting and Flame Cutting in Terms of Speed
Plasma cutters are able to achieve high cutting speeds due to the temperature and velocity at which the plasma jet is expelled from the nozzle. Plasma can be used to cut through a wide range of metals like steel, stainless steel, aluminum, and copper at speeds of up to several meters per minute. The cutting speed depends on the thickness of the metal being cut, the device’s amperage, and the quality of the plasma arc.
By contrast, flame cutting is a slower process than plasma cutting due to the lower temperature of the flame and the lower velocity of the jet of oxygen. Flame cutting devices can cut through thicker materials than plasma ones but do so at a slower speed. The cutting speed depends on the thickness of the metal being cut, the type of fuel gas involved, and the oxygen flow rate.
Difference Between Plasma Cutting and Flame Cutting in Terms of Thickness
A flame cutter, or oxy-fuel torch, is ideal for mild steel that’s more than 1 inch thick. Typically, its cutting capacity can range from ⅛’’ to 22’’ in thickness and sometimes even more. However, these systems are limited mainly to carbon steel. Plasma cutters, on the other hand, can operate on a wider material range but are very limited in terms of metal thickness. A plasma cutting system is ideal for cutting sheet metals with thicknesses of 3/16’’ or less.
Difference Between Plasma Cutting and Flame Cutting in Terms of Versatility
By and large, plasma cutting is more versatile than flame cutting in its ability to cut a wider range of materials and shapes. However, flame cutters are portable which makes them more versatile in the field.
Difference Between Plasma Cutting and Flame Cutting in Terms of Application
Though plasma cutting and flame cutting are both considered to be thermal cutting methods, they differ greatly in terms of ideal applications. A flame cutter is ideal for mild steel over 1 inch thick whereas plasma cutters are best for sheet steel with a thickness of 3/16’’ or less. Plasma cutters are popular choices for projects that require a high degree of accuracy, such as in the manufacturing of aerospace components, automotive parts, and signage. Flame cutters, on the other hand, are more affordable and portable and are widely used in industries such as shipbuilding, steel fabrication, and construction.
Which Should you Choose, Plasma or Flame Cutting?
The best cutting tool will vary on a case-to-case basis. Plasma cutters are ideal for conductive metals that are thin but require precise cuts. Flame cutters, on the other hand, are ideal for mild steel over 1 inch thick as long as the cut can accommodate some minor dimensional inaccuracies.
Summary
This article presented plasma vs. flame cutting, explained what they are, and discussed the differences between each thermal cutting technique. To learn more about plasma cutting and flame cutting, contact a Xometry representative.
Xometry provides a wide range of manufacturing capabilities, including sheet cutting and other value-added services for all of your prototyping and production needs. Visit our website to learn more or to request a free, no-obligation quote.
Disclaimer
The content appearing on this webpage is for informational purposes only. Xometry makes no representation or warranty of any kind, be it expressed or implied, as to the accuracy, completeness, or validity of the information. Any performance parameters, geometric tolerances, specific design features, quality and types of materials, or processes should not be inferred to represent what will be delivered by third-party suppliers or manufacturers through Xometry’s network. Buyers seeking quotes for parts are responsible for defining the specific requirements for those parts. Please refer to our terms and conditions for more information.
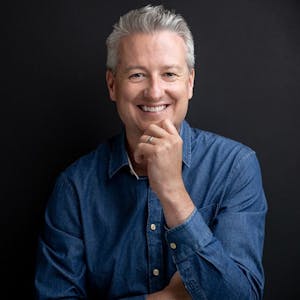