Laser cutting of polyimide involves using a focused laser beam to cut or engrave the material with high precision. Laser cutters use a focused beam of light to process materials like polyimide. CO2 lasers are particularly effective, though the required power varies with material thickness. For example, a CO2 laser with a power of 30 watts is capable of cutting polyimide films as thin as 25 µm and beyond. The optimal settings for cutting polyimide will also depend on the type of laser being used. For example, a 30-watt CO₂ laser may be effective for cutting polyimide film, though optimal speed settings vary by machine and material thickness. Also, take into account the focal length of the laser when cutting polyimide.
When cutting polyimide, it is important to use the correct type of lens. The lens should have a low focus depth to minimize the amount of material heated by the laser. The best way to determine the optimal settings for cutting polyimide is to experiment with different settings and see what works best for your specific material. Kapton® is a well-known brand of polyimide film often used in laser cutting and engraving applications. Kapton is thermally stable up to approximately 400 °C and is used in a variety of applications requiring high-temperature resistance, chemical resistance, and electrical insulation. This article will discuss how to laser cut and engrave extruded polyimide, cast polyimide, and more.
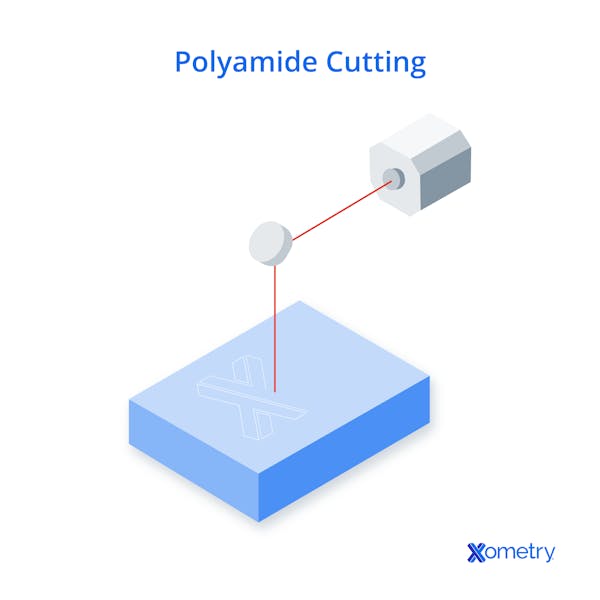
How To Laser Cut and Engrave Extruded Polyimide
Laser cutting and engraving extruded polyimide is a popular way to create precision parts and products. Extruded polyimide is a versatile material that can be laser-cut and engraved to create a variety of shapes and sizes. Below are the steps required to laser cut and engrave extruded polyimide:
- Select the appropriate laser cutting and engraving settings.
- Position the extruded polyimide on the cutting bed.
- Begin laser cutting and engraving according to the desired settings.
- Remove the finished product from the cutting bed.
How To Laser Cut and Engrave Cast Polyimide
Despite its many advantages, cast polyimide can be difficult to work with using traditional methods such as machining or stamping. However, laser cutting and engraving are ideal solutions for processing this material. The steps below outline the best practices for laser cutting and engraving cast polyimide:
- Prepare the Material for Laser Processing: Cast polyimide is sensitive to scratches and other surface imperfections. To ensure optimal results, it is important to start with a clean, smooth surface. Any dirt or debris on the material can interfere with the laser beam’s energy distribution, potentially reducing cut quality and precision.
- Select the Appropriate Laser Settings: The ideal laser settings will vary depending on the specific application and the type of cast polyimide being used. In general, lower laser power settings help minimize heat-affected zones and reduce the risk of charring or material degradation.
- Adjust the Focus of the Laser Beam: The focus of the laser beam plays a critical role in the quality of the cut or engraving. For best results, slightly defocusing the beam can lower energy density at the surface, reducing the chance of charring or thermal damage.
- Perform a Test Cut or Engraving: Before starting the actual project, it is always a good idea to perform a test on a small scrap of material. This will allow you to fine-tune the laser settings and ensure you are getting the results you desire.
- Begin Cutting or Engraving: Once you are happy with the test cut or engraving, you can begin the actual project. For best results, it is important to work slowly and carefully to avoid damaging the material.
- Finish Up: After the cutting or engraving is complete, it is important to remove any debris from the surface of the cast polyimide. Use a soft brush to remove any loose particles, or a lint-free cloth to wipe away any residual dust.
What Are the Differences Between General Part and Presentation Part Cutting for Polyimide?
The terms “general part” and “presentation part” are used to describe the internal and external structure of the material. General parts are parts that don't require a cosmetic finish, and aesthetics aren't very important in sections such as the internal parts. For polyimide, routine care is necessary to achieve the correct dimensions and specifications. On the other hand, presentation parts are parts that have polished edges for presentation purposes, such as the external or exposed parts. For presentation parts, using lower power settings and ensuring the surface is clean can help achieve smoother, more visually appealing edges.
What Is the Best Cutting Speed for Presentation-Grade Polyimide?
Laser cutting polyimide can be done at a range of speeds, with the optimum speed depending on the type of laser used and the type of polyimide. Cutting speed impacts the depth and quality of the cut. Higher speeds reduce exposure time, resulting in shallower, less defined cuts. Slower speeds allow for deeper cuts but may increase the risk of thermal damage. The best way to determine the optimum speed for laser cutting polyimide is to experiment with different speeds and different types of polyimide to see what gives the best results. When it comes to speed, there is no one-size-fits-all answer, as the optimum speed will vary depending on the laser used and the type of polyimide.
What Is the Best Power Setting for General-Use Polyimide?
When it comes to laser cutting polyimide, the best power setting to use is in the range of 20–40 watts. This range of power will provide the best results in terms of cutting speed and quality. Excessive power may lead to charring or discoloration, while insufficient power can reduce cutting efficiency and edge quality. The optimum speed for laser cutting polyimide will vary depending on the type of laser used. For example, CO2 lasers will typically operate at a higher speed than fiber lasers. Additionally, the type of polyimide being cut will also affect the optimum cutting speed. For instance, polyimide films typically require a higher cutting speed than polyimide tapes.
What Is the Best Setting for Laser Cutting Polyimide?
The best settings for laser cutting polyimide are those that create a clean, smooth cut with minimal charring or burning. When setting up your laser cutter, it is important to consider the power of the laser, the speed at which it moves, and the focus of the beam:
- Power: Laser power directly affects cutting capability; higher power levels can penetrate thicker polyimide sheets, but must be managed to avoid overheating or material degradation.
- Speed: Cutting speed influences both precision and heat exposure. Faster movement reduces heat buildup but may lead to incomplete cuts, especially in thicker sections.
- Focus of the Laser Beam: The Beam focus determines the energy concentration at the cut point. A tight focus enables high-precision cuts but increases the risk of surface charring if not properly adjusted.
What Are the Common Mistakes Made When Laser Cutting Polyimide?
The wrong settings can easily damage the material. A well-designed part is also crucial for a successful cut. Those who don't have a good understanding of the laser-cutting process are more likely to make mistakes. Some common mistakes made when polyimide cutting with a laser are:
- Not accounting for the material's properties.
- Not using the proper cutting settings.
- Not having a well-designed part.
- Not having a good understanding of the laser-cutting process.
- Not knowing how to properly handle and store polyimide.
What Are the Best Tips for Beginners When Laser Engraving Polyimide?
When starting laser engraving polyimide, there are a few key tips to keep in mind to get the best results.
- Begin with a low-power, slow-speed setting to reduce the risk of overheating or warping the polyimide.
- Use a tightly focused beam and apply multiple low-intensity passes when necessary to preserve surface quality.
- Ensure all laser operations are well-ventilated to safely extract fumes.
What Is the Best Laser Cutter for Polyimide?
The most common laser for polyimide is the CO₂ laser, due to its strong absorption by organic polymers and ability to produce clean cuts. For ultra‑fine precision, especially in Kapton® or thin polyimide films, UV lasers (≈355 nm) may be superior, offering minimal heat-affected zones. Fiber lasers exist but are generally less suitable for polyimide compared to CO₂ or UV systems.
How Does the Thickness of a Polyimide Sheet Affect the Power Requirements of a Laser Cutter?
Thicker polyimide sheets require higher laser power and slower cutting speeds to fully penetrate. Since polyimides sublimate at around 750 °C, lasers with sufficient wattage—but not excessive—can cleanly cut thin films without burning. Thicker sheets, however, may produce wider kerfs and longer processing times.
What Are the Polyimide Projects for Laser Cutting?
Polyimide projects for laser cutting include:
- Prototyping and custom parts for electronics
- Precision mechanical components
- Coating and insulation for optical fibers
- Components for medical devices
- Decorative elements and wearable electronics
- Art and sculpture
- Signage and branding
- Packaging and product display in prototyping
What Are the Alternatives to Polyimide for Laser Cutting?
There are several good alternatives to polyimide for laser cutting, depending on the application. Some of them include, but are not limited to:
- Kevlar®: Aramid fiber, known by the brand name Kevlar, is often used in applications requiring high strength and low weight. It also laser-cuts cleanly, with edges that self-seal due to heat, eliminating fraying.
- PEEK: Polyetheretherketone is another high-performance polymer with good heat resistance and mechanical strength. It is often used in medical implants and other applications in which biocompatibility is important.
- Ultem®: Polyetherimide is another common alternative to polyimide. It has good heat resistance and stiffness, though it may char slightly during laser cutting, depending on the application.
Common FAQs on Polyimide Laser Engraving and Cutting
Is Nylon the Same as Polyimide?
No, nylon is not the same as polyimide. Nylon is a synthetic thermoplastic polymer, while polyimide is a synthetic aromatic polymer. They differ in terms of both chemical structure and properties. Nylon is strong, durable, and has a high melting point, while polyimide is resistant to high temperatures and has excellent electrical insulation properties.
What Is the Difference Between Delrin® and Polyimide in Laser Cutting?
Delrin is a homopolymer acetal, while polyimide is a synthetic thermosetting polymeric material. Both materials have excellent resistance to abrasion and chemicals. They also have good dimensional stability and low moisture absorption. Laser cutting of these materials is possible, but there are some differences that should be considered:
- Delrin has a lower melting point than polyimide, which means that it can be cut more easily with a laser.
- Delrin is less likely to char or discolor when cut with a laser, while polyimide may discolor slightly.
- Delrin has a higher thermal conductivity than polyimide, which means that heat generated by the laser will be conducted away from the cut surface more quickly.
What Is the Difference Between Polyimide Cutting and Polyamide Cutting?
Polyimide and polyamide are both plastics used in a variety of applications, but they have different properties that make them suitable for different tasks:
- Polyimide offers superior heat resistance compared to polyamide, retaining structural integrity at temperatures above 250 °C, at which point polyamide begins to degrade.
- Polyamide provides good wear resistance and toughness, although polyimide often surpasses it in tensile strength and stiffness. This property makes it a good choice for applications in which the material will see a lot of use.
- Polyimide is highly resistant to solvents, acids, and other harsh chemicals, making it suitable for chemically aggressive environments. Polyamide offers moderate chemical resistance but is more susceptible to degradation in strong acids and bases.
What Is the Difference Between Kapton and Polyimide?
Kapton is a specific brand of polyimide film developed by DuPont™. While polyimide refers to a broad class of high-temperature polymers, Kapton was the first commercially available polyimide film and remains widely used in electronics and aerospace.
Summary
This article presented laser engraving and cutting polyimide, explained what it is, and discussed the different settings and uses cases for it. To learn more about laser cutting with polyimide contact a Xometry representative.
Xometry provides a wide range of manufacturing capabilities, including sheet cutting and other value-added services for all of your prototyping and production needs. Visit our website to learn more or to request a free, no-obligation quote.
Copyright and Trademark Notices
- DuPont™, Kevlar®, and Kapton® are trademarks or registered trademarks of the DuPont de Nemours Company.
- Delrin® is a trademark of DuPont Polymers, Inc.
- Ultem® is a registered trademark of SABIC Innovative Plastics IP BV (formerly GE Plastics).
Disclaimer
The content appearing on this webpage is for informational purposes only. Xometry makes no representation or warranty of any kind, be it expressed or implied, as to the accuracy, completeness, or validity of the information. Any performance parameters, geometric tolerances, specific design features, quality and types of materials, or processes should not be inferred to represent what will be delivered by third-party suppliers or manufacturers through Xometry’s network. Buyers seeking quotes for parts are responsible for defining the specific requirements for those parts. Please refer to our terms and conditions for more information.
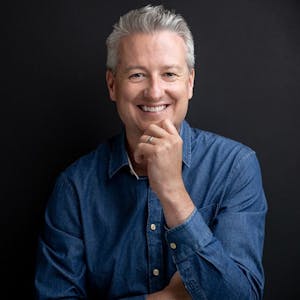