Lasers can cut, engrave, etch, and make identifying marks or decorative patterns on a variety of materials. Both hobbyists and businesses can leverage the capabilities of lasers to produce personalized trinkets and gifts, expand their brands, or improve the traceability of their fabricated parts. Figure 1 below is an example of laser engraving metal:
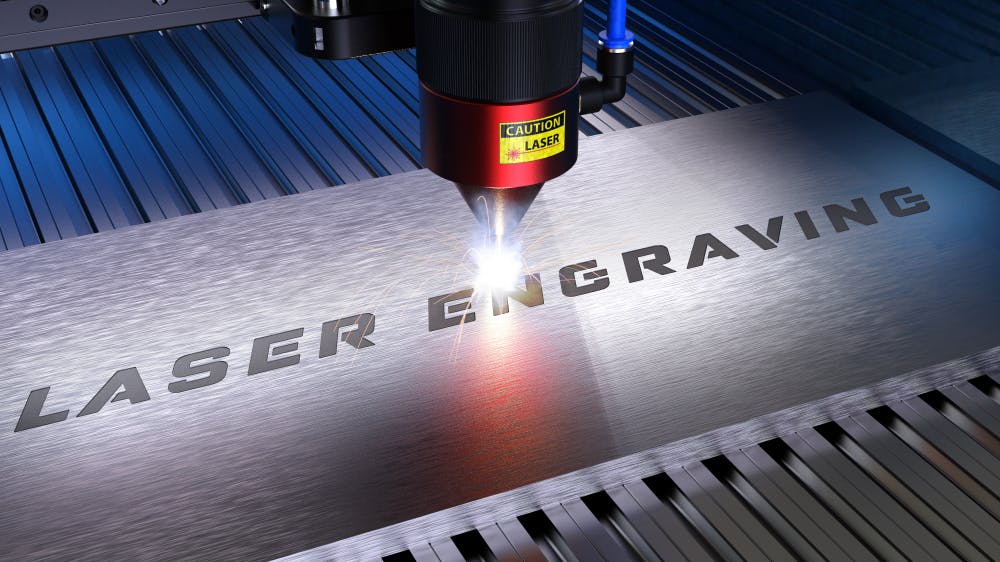
Laser engraving on metal.
Image Credit: Shutterstock.com/Thomas Soellner
Engraving metals with lasers can present a few special challenges. A metals' high vaporization temperatures and reflectivity demand higher laser power and energy density delivery to the metal surface to achieve the desired effects. It is important for users to be familiar with the properties of their raw work materials in order to select the right process approach and laser settings. Listed below are the five main steps to follow for successful laser engraving of metals:
1. Select the Material You Wish To Work With
Manufacturers don’t typically select materials based on their ability to be engraved, but rather on other characteristics, such as: tensile strength, thermal expansion properties, or corrosion resistance, that enable the material to satisfy a particular purpose. Laser engraving can work on a variety of metals, but some metals are inherently easier to engrave than others. The difficulty of laser engraving a particular metal largely depends on the material’s vaporization temperature and its reflectivity. Higher vaporization temperatures require higher power lasers or multiple passes of the laser to successfully complete the engraving. Reflectivity affects the ability of a metal to absorb energy from the laser so it can be heated to its vaporization temperature. These two factors can greatly impact the engraving’s quality and the efficiency of the engraving process.
2. Choose the Applications for Which You Want To Use Laser Engraving
Having selected a metal, the user can then determine what laser engraving applications are feasible using that material. Metal laser engraving can be used to create elaborate gifts and decorations, branding items such as business logos and graphics, and part traceability features such as bar codes, QR codes, unique device identifiers (UDI), and serial numbers.
3. Determine Whether the Part Requires Radial Engraving
Radial engraving is the act of laser engraving on a curved or rounded surface. If you try to laser engrave a curved surface using techniques developed for flat surfaces, your design, as marked on the part, will be distorted. To avoid this, you will need a special rotary attachment to spin the part, presenting a locally "flat" area to the laser beam. In some cases, it is possible to compensate for a gently curved surface using laser software.
4. Configure the System To Carry Out Engraving
Once the user has decided on an application and a metal, the next step is to configure the laser system for the selected metal. Check the laser manufacturer's operating manual for basic set-up instructions and recommended settings. The appropriate laser energy density, focal point, and cut speeds must now be established. Some metals, like titanium, have higher vaporization temperatures than other metals like aluminum. Therefore, users should ensure that their laser is powerful enough to heat the metal as quickly as possible to vaporize the material away.
Additionally, some metals, like copper and stainless steel, are more reflective than others, like aluminum. Sprays and pastes that can temporarily dull a metal workpiece's surface can be applied to reduce reflectivity. It can also increase the ability of the metal material to absorb energy from the laser. Users can also opt to use fiber lasers that emit shorter wavelengths in the violet and ultraviolet range as highly reflective materials often reflect longer, red and infrared wavelengths emitted by CO2 lasers. Properly configuring the laser settings, having the right type of laser, and adequately preparing the workpiece material are key to a successful metal engraving.
5. Use Proper Safety Precautions Before Engraving
Prior to starting an engraving task, users should take the appropriate safety precautions. The list below shows the most important safety considerations for laser engraving metal:
- Ensure that all users are trained in the use of the laser engraving system.
- Keep a fire extinguisher nearby.
- Use an exhaust system to evacuate fumes that result from the laser engraving process.
- Wear the appropriate laser safety glasses to prevent laser radiation from damaging eyes. The right type of protection depends on the class of laser in use.
- Check that all safety features indicated in the manufacturer’s operating manual are followed.
What Is Laser Engraving?
Laser engraving is a method of creating long-lasting deep marks on a material by vaporizing and removing the material in a desired pattern. The process makes shallow cuts into a part to create pictures, patterns, logos, barcodes, and serial numbers — among other things. Laser engraving can be used on a wide variety of materials including: metals, ceramics, glass, wood, leather, and paper. The process has seen widespread adoption in hobbyist, small commercial, and mass manufacturing environments because of its versatility and ability to create permanent marks.
What Are the Best Laser Engraving Machines for Metal?
Fiber lasers are the best type to use for engraving metals. They emit the shorter blue, violet, and ultraviolet wavelengths that are most easily absorbed by metals. Absorbing more energy makes the engraving process more efficient. CO2 lasers emit radiation primarily in the red and infrared wavelengths, which are largely reflected by most metals. This makes engraving with CO2 lasers extremely difficult. The process will require the use of a metal marking spray or paste to reduce reflectivity and enhance energy absorption.
What Types of Metals Can Be Laser Engraved?
Both ferrous and non-ferrous metals can be laser engraved. Listed below are some examples of metals that can be engraved:
- Various grades of steel including alloyed, stainless, and high-speed steel
- Aluminum and anodized aluminum
- Copper and brass
- Titanium
- Coated, nickel-plated, and galvanized metals
- Precious metals like gold and silver
How Does Laser Engraving Work in Metals?
Metal laser engraving is the process where a laser heats a particular surface area of a metal workpiece to extreme temperatures to vaporize the material away. In doing so, shallow cuts (as deep as 0.020”) are made into the part. Laser engraving cuts in metal are clean and precise because the material is vaporized away and no residual material remains in the cut area. Engravings are also wear-resistant and permanent because features are made below the surface of the part.
What Materials Are Needed To Laser Engrave Metal?
Certain materials and equipment are required to efficiently and effectively laser engrave metal. These materials are listed below:
- A laser system powerful enough to laser engrave metal (preferably a fiber laser system)
- Laser safety goggles
- Metal marking spray or paste (only if not using a fiber laser system)
- Isopropyl (rubbing) alcohol for cleaning
- A soft cloth
- Fire extinguisher
How Long Does it Take To Laser Engrave Metal?
The amount of time it takes to laser engrave a metal workpiece can range from a few seconds up to several minutes. The time will depend on the size of the engraving, the workpiece material, and the power of the laser. Larger engravings will plainly take longer to engrave than small engravings. Additionally, materials that have higher vaporization temperatures such as titanium will take longer to engrave than metals with lower vaporization temperatures like aluminum. This is because more power and time are required to sufficiently heat the metal.
What Is the Difference Between Laser Cutting and Laser Engraving in Metal?
Unlike laser engraving, where only shallow cuts are made into the metal part, laser cutting is the process of through-cutting a metal part with a laser. Metal laser cutting requires more power than metal laser engraving. Additionally, metal laser cutting is a slower process than engraving.
Summary
This article presented the steps needed to laser engrave metal, explained what they are, and discussed what each step entails. To learn more about laser engraving metal, contact a Xometry representative.
Xometry provides a wide range of manufacturing capabilities, including sheet cutting and other value-added services for all of your prototyping and production needs. Visit our website to learn more or to request a free, no-obligation quote.
Disclaimer
The content appearing on this webpage is for informational purposes only. Xometry makes no representation or warranty of any kind, be it expressed or implied, as to the accuracy, completeness, or validity of the information. Any performance parameters, geometric tolerances, specific design features, quality and types of materials, or processes should not be inferred to represent what will be delivered by third-party suppliers or manufacturers through Xometry’s network. Buyers seeking quotes for parts are responsible for defining the specific requirements for those parts. Please refer to our terms and conditions for more information.
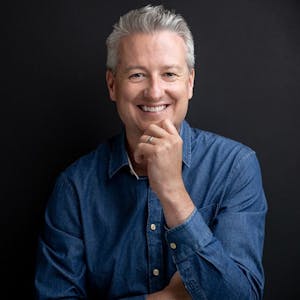