Laser ablation is the scientific term for the removal of material. It uses a high-power continuous or pulsed laser which causes highly localized and intense heating. It is mainly used in the medical industry for implant surface preparation and in the aerospace and automotive for bonding/coupling surface preparation, to name a few. This article will define laser ablation, discuss how it works, its applications, and the materials that can be used.
What Is Laser Ablation?
Laser ablation is the process whereby a laser is used for the controlled removal of matter from a component or material surface. This is central to most industrial laser applications and can be used for laser marking. For example: applying images to parts, removing contaminants and coatings from surfaces, altering the surface roughness of a part, and cutting through a component.
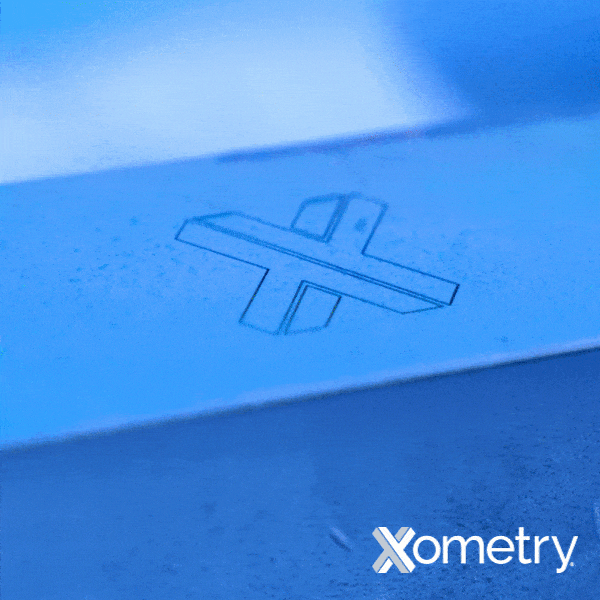
What Is the Process of Laser Ablation?
Laser ablation works by impinging a high-energy beam onto the surface and triggering the localized volatilization, vaporization, or charring of the target material. This process can be carried out in an open atmosphere if oxidation is not an issue. It can also be carried out in an inert atmosphere (such as: argon, argon CO2, and nitrogen) to minimize oxidation. It can be carried out in a vacuum for extreme control, and experimental work in laser ablation under water has demonstrated some benefits.
The nature and depth of penetration depend upon the refractive index of the target and the wavelength of the laser light. For materials with some limited transparency at the laser's main frequency, the light will penetrate to a limited depth. For materials with no such transparency, the effect will be entirely at the surface. Where transparency is high, the beam may pass through or dissipate in sufficient depth of material that the energy concentration will be too low for ablation to take place.
The energy from the beam creates a powerful electric and highly localized field within the target. The free electrons that this releases from the target atoms collide with the bulk, transforming the energy into heat. At highly controlled energy levels, this can result in just localized heating. At higher levels, the laser energy will melt but mostly not vaporize the target—a result that can be employed for laser welding and laser texturing. Laser ablation occurs when the energy levels are high enough to vaporize and/or char the target. At these energy levels, a plasma cloud is formed. This cloud expands and cools rapidly, causing explosive ejection of volatilized material.
What Are the Materials That Can Be Used for Laser Ablation?
Laser ablation is a technique that has a wide range of applications and can be carried out in most materials, including polymers, metals, and composite materials. Examples are listed below:
- Polymethyl methacrylate (acrylic, PMMA)
- Polystyrene (PS)
- Polyimide (PI)
- Polyethylene terephthalate (PET)
- Polycarbonate (PC)
- Polyethylene (PE)
- Polytetrafluoroethylene (Teflon, PTFE)
- Polyetheretherketone (PEEK)
- Polydimethylsiloxane (PDMS)
- Stainless steel
- Titanium
- Copper
- Resin-bonded carbon fiber
- Resin-bonded kevlar
Metals generally respond well to laser ablation. The energy levels can be tuned to differentially remove surface coatings. This leaves the bulk unaffected, erodes the metal itself, or alters the surface properties by melting with near-zero removal. Composite materials, on the other hand, can be surface treated by laser ablation to increase surface energy and roughness to enhance bonding. For more information, see our guide on Materials Used for Laser Cutting.
What Are the Examples of Laser Ablation?
Laser ablation is an increasingly applied scientific and industrial tool, used for a range of high- and lower-precision applications. Some examples are:
- Manufacture of microfluidic channels in drug delivery systems—ablation in metals, glass, and plastics.
- Micro drilling of diamond for precision gas leakage channels in instruments.
- Serial number, barcode, and brand marking on metal and plastic components.
- Laser ablation hugely improves bone growth and adhesion to dental implants. This level of texturing can be precisely and repeatedly created using laser ablation.
- Laser ablation with tightly controlled nano-structure feature sizes can reduce the adhesion of bacterial contaminants. At the same time, the adhesion to patient tissues is enhanced.
- Laser ablation can provide high-quality keying surfaces. This feature enhances the coupling of overmolding of composites and polymers onto aluminum, stainless steel, and titanium parts, metal composites that are increasingly used in aerospace, and automotive components.
- Laser ablation of various metals is used to make metal and metal oxide nanoparticles.
- Laser ablation is used for shaping and adjusting conductors in microelectronics.
Figure 1 below is an example of using laser ablation in dental application:
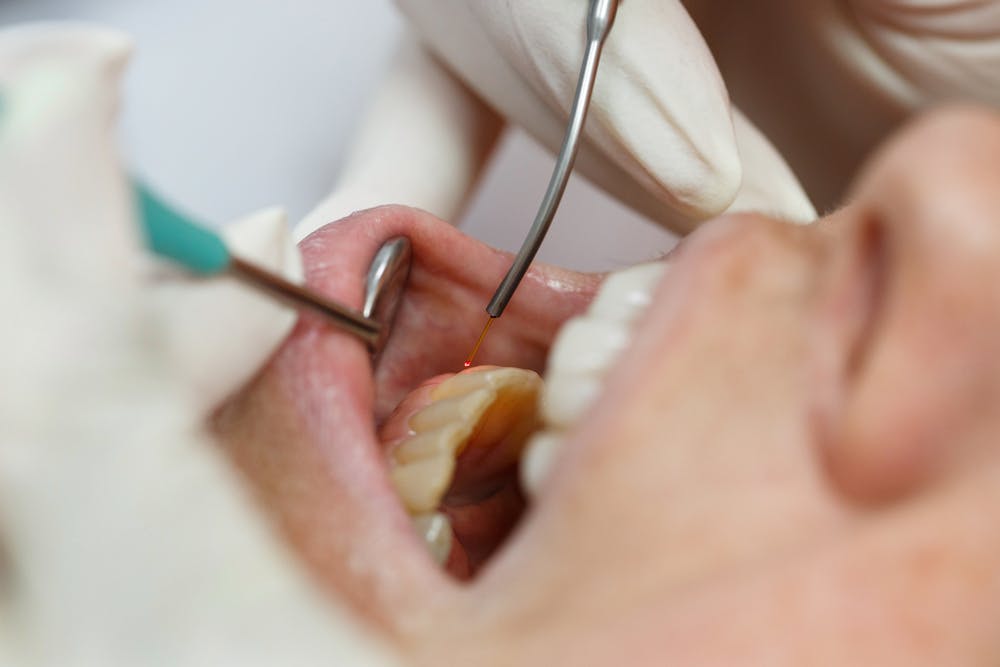
A dental laser in use.
Image Credit: Shutterstock.com/zlikovec
What Are the Industries That Use the Laser Ablation Method?
Forms of laser ablation are widely used in various industries, including:
- Medical: Implant surface preparation for tissue adhesion and anti-bacterial properties.
- Aerospace and Automotive: Bonding/coupling surface preparation and serial number marking.
- Plastics and Composites Manufacture: Surface preparation of metals and composites prior to overmolding and bonding.
- General Engineering: Component repair and precision cleaning.
- Microelectronics: Conductor and insulator sculpting.
How To Use Laser Ablation?
The process of using laser ablation depends on the application. In general, laser ablation encompasses a sliding scale of energies and effects. Examples of how it is used, depending on the energy levels, are listed below:
- Lowest Energy Levels: Laser ablation can be used to detach and remove surface contaminants such as: oils, paint, oxide residues, and residual plating, all without affecting the substrate.
- Higher Energy Levels: The target can be the substrate itself, melting but minimally removing material. This is on the margin between laser welding (fusing the surface to restore cracking), laser texturing, and laser ablation.
- Slightly Higher Energy Levels: The preponderance can move from melting to vaporizing, allowing surfaces to be modified by ablation and fusing.
- Highest Energy Levels: The surface can be aggressively removed and deep features drilled/cut. This sits on the margin of laser cutting, but the method can be used for ablation and sculpting.
Is Laser Ablation a Type of Laser Cutting?
Yes, laser ablation is a type of laser cutting, although the difference is in degree. The process of ablation and cutting is the same—the melting/vaporization/charring of the target material to remove it, in a precise fashion. A “cut” generally penetrates through a blank to allow external and internal feature shaping in the Z axis by material removal. Ablation generally influences the surface and limited Z depth, while excising no entire pieces from the blank.
Is There a Laser Ablation Machine?
Yes, there is a laser ablation machine. There are various styles and types of laser ablation machines. These range from the re-defining of a benchtop laser cutter as an ablation machine; through large, automated (and often custom) equipment in medical, dental, aerospace, and automotive production plants; to scientific instruments used for the study of the process and for the manufacture of ablated components and/or ablated material as a functional outcome.
What Is the Difference Between Laser Ablation and Engraving?
Laser engraving is a form of, and application of, laser ablation. A machine used as a laser engraver ablates material from a target, to deliver a required surface structure.
Laser ablation is more than engraving, in that it uses a piece of specialist equipment (other than basic laser cutters applied to engraving). It often uses exotic lasers and very high pulse frequencies to deliver high-precision energy control in ways that a laser cutter cannot. For more information, see our guide on Laser Engraving.
Summary
This article presented laser ablation, explained what it is, and discussed the process and examples. To learn more about laser ablation, contact a Xometry representative.
Xometry provides a wide range of manufacturing capabilities, including sheet cutting and other value-added services for all of your prototyping and production needs. Visit our website to learn more or to request a free, no-obligation quote.
Disclaimer
The content appearing on this webpage is for informational purposes only. Xometry makes no representation or warranty of any kind, be it expressed or implied, as to the accuracy, completeness, or validity of the information. Any performance parameters, geometric tolerances, specific design features, quality and types of materials, or processes should not be inferred to represent what will be delivered by third-party suppliers or manufacturers through Xometry’s network. Buyers seeking quotes for parts are responsible for defining the specific requirements for those parts. Please refer to our terms and conditions for more information.
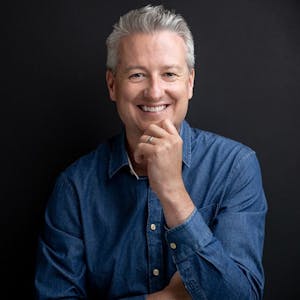