Xometry Capabilities Navigator
From prototyping to production, our network of over 10,000 suppliers has the capacity for all of your manufacturing projects. Select a capability below to explore how Xometry can bring your big ideas to life. Explore all of our capabilities.
Machining and Turning
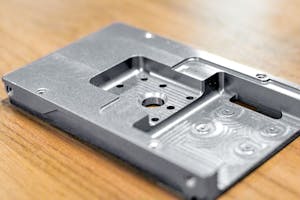
Custom Online CNC Machining Services
Thermoplastic Additive Manufacturing / 3D Printing
Fused Deposition Modeling (FDM) 3D Printing Service
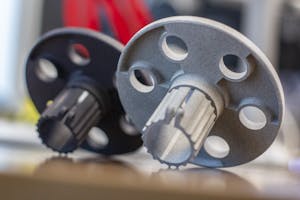
HP Multi Jet Fusion (MJF) 3D Printing Service
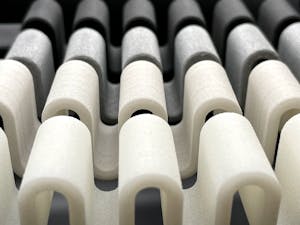
Selective Laser Sintering (SLS) 3D Printing Service
Resin Additive Manufacturing / 3D Printing
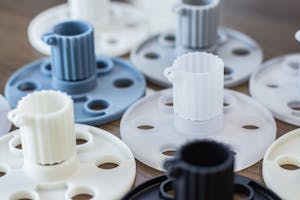
Stereolithography (SLA) 3D Printing Services

PolyJet 3D Printing Service
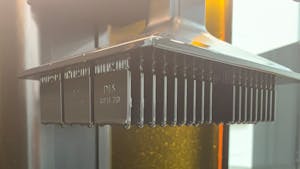
Carbon Digital Light Synthesis™ (DLS™) 3D Printing Service
Metal Additive Manufacturing / 3D Printing
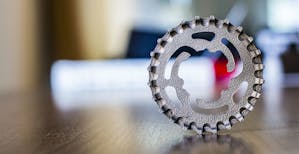
Direct Metal Laser Sintering (DMLS) 3D Printing Service
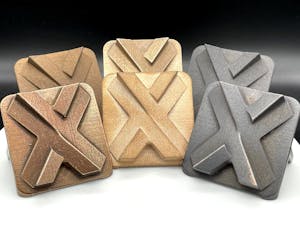
Metal Binder Jetting 3D Printing Service
Sheet Metal and Tube Cutting and Bending Services
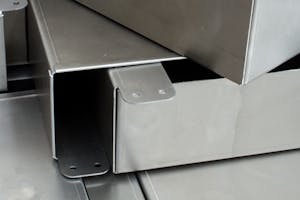
Sheet Metal Fabrication Services
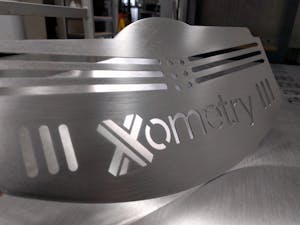
Laser and Sheet Cutting Services
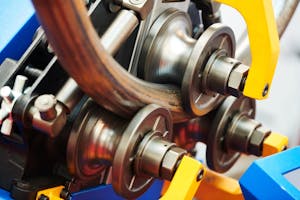
Tube Bending Services
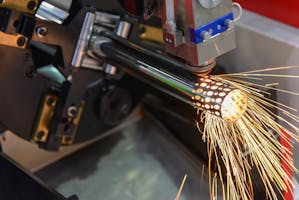
Laser Tube Cutting Services
Plastic Molding, Casting, and Production
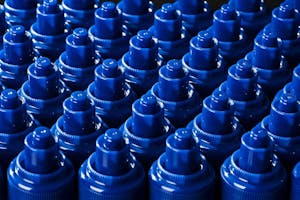
Custom Plastic Injection Molding Service
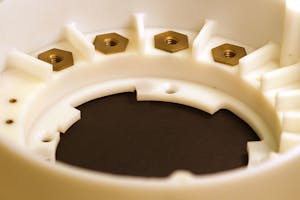
Urethane and Silicone Casting Services
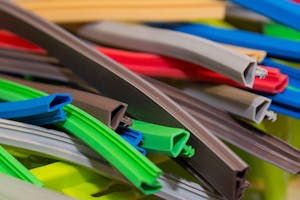
Custom Plastic Extrusion Services
Metal Casting, Stamping, and Production
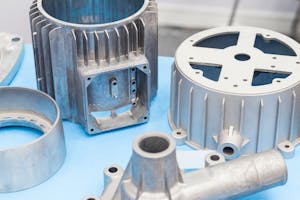
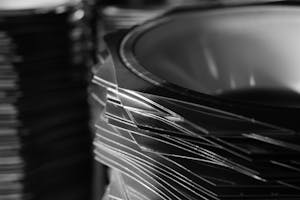
Metal Stamping Services
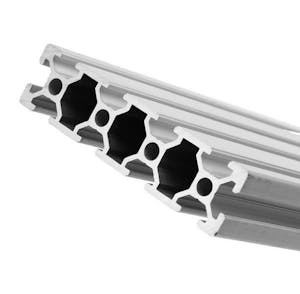
Metal Extrusion Services
Value-Added, Turnkey Solutions
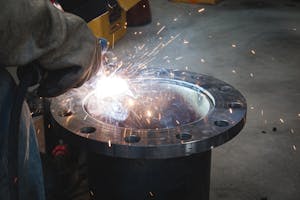
Custom Online Weldment Services by Xometry
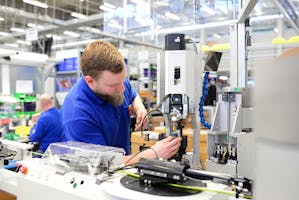