Plasma Cutting Service
Custom Plasma Cutting for Prototyping and Production Part Fabrication | Free Standard Shipping on All US Orders | Subject to availability. Xometry doesn't guarantee that we can provide this service at any given time.
Custom Plasma Cutting Service
Xometry's custom, online plasma cutting service offers a cost-effective on-demand fabrication solution for your sheet metal needs. Thanks to our Instant Quoting Engine, we can provide instant pricing for any size fabrication run from low-volume prototyping to high-volume production. Xometry also offers a laser cutting service and a waterjet cutting service.
You can get an instant quote from a 3D CAD file or DXF file in our Instant Quoting Engine.
Xometry's Powerful DXF Quoting Tools
When it comes to sheet, we can't be beat. The Xometry Instant Quoting Engine is equipped with various features to ensure your sheet cutting quotes are quickly generated, straightforward, and unbeatable. In addition to 3D CAD, one of the most commonly used formats for plasma cut parts are 2D DXF. We made sure to include extensive features and support for the format. Below are a few of the key elements we've incorporated to offer you the most optimal DXF quoting experience for your flat plasma cut parts:
- Automatic DXF File Repair -- Common issues found in DXF files are automatically fixed when detected.
- 2D DXF File Viewer -- Our built-in vector based DXF viewer makes it quick and easy to review your uploaded designs.
- Simple Material Selections -- Only see the sheet thicknesses applicable to your chosen material through easy to use drop-down menus.
- Nested DXF File Support -- Upload a single pre-nested DXF file containing multiple components to consolidate your line items and receive discounted family pricing.
Xometry's Sheet Cutting Service
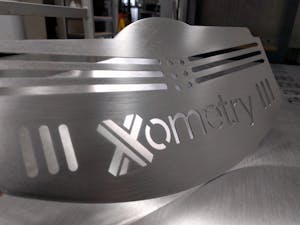
Laser and Sheet Cutting Services
Plasma Cutting Materials
Aluminum | Copper | Steel |
---|---|---|
Aluminum Aluminum 5052 | Copper Copper 101 | Steel Stainless Steel 301 |
Aluminum | Copper Copper C110 | Steel Stainless Steel 304 |
Aluminum | Copper Copper 260 (Brass) | Steel Stainless Steel 316/316L |
Aluminum | Copper | Steel Steel, Low Carbon |
Additional materials are available upon request!
Standard Sheet Thicknesses
Available Finishes
Standard
Minimal post-processing or treatment on parts is done.
Anodized (Type II or Type III)
Type II creates a corrosion-resistant finish. Parts can be anodized in different colors—clear, black, red, and gold are most common—and is usually associated with aluminum. Type III is thicker and creates a wear-resistant layer in addition to the corrosion resistance seen with Type II.
Powder Coat
This is a process where powdered paint is sprayed onto a part which is then baked in an oven. This creates a strong, wear- and corrosion-resistant layer that is more durable than standard painting methods. A wide variety of colors are available to create the desired aesthetic.
Chem Film (Chromate Conversion Coating)
Provides corrosion resistance and good conductivity properties. Can be used as a base for paint. Can leave surface yellow/gold.
Custom
Don’t see the finish you need? Submit an RFQ and we’ll look into a finishing process for you.
Available Types Of Plasma Cutters
2-Axis
This is the most common and conventional form of a plasma cutter and operates like any traditional CNC sheet metal fabrication tool, producing flat profiles with straight edges. These plasma cutters are best for cutting large parts from thick material quickly and are more cost-efficient than CNC laser cutters for the same work.
3-Axis
This type of CNC plasma cutter adds in an additional axis of rotation which allows the cutting tool to tilt and cut edges at an angle. This is extremely useful for cutting chamfers, countersunk holes or angled edges as part of weld preparation, which saves on secondary operations such as grinding or machining helping reduce overall cost.
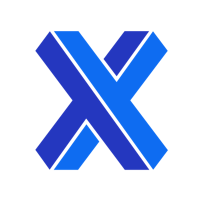
Ready to get started on your plasma cutting quote?
Free shipping available for domestic plasma cutting orders ; learn more!
Applications of Plasma Cutting
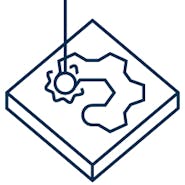
Blank Preparation
Plasma cutting can build near net shapes of conductive metals, making it perfect for material preparation.
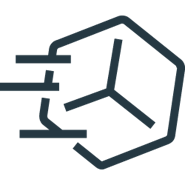
Rapid Prototyping
The range of plasma cutter materials available, low cost per unit, and speed of production makes waterjet a great option for prototyping.
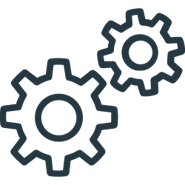
End-Use Production
Large format cutting, vast material options, and high throughput have made plasma cutting a favorable technology for end-use parts.
Advantages of Plasma Cutting
Durability
Similar to CNC machining, sheet metal processes produce highly durable parts well-suited for both functional prototypes and end-use production.
Scalability
All sheet metal parts are built on-demand and with lower setup costs compared to CNC Machining. Depending on your needs, order as little as a single prototype up to 10,000 production parts.
Material Selection
Choose from a variety of sheet metals across a wide range of strength, conductivity, weight, and corrosion resistance.
Rapid Turnaround
Combining the latest cutting, bending, and punching with automated technologies, Xometry provides instant sheet quotes and completed parts often within a week.
Plasma Cutting General Tolerances
Description | General Tolerance |
---|---|
Description Distance Dimensions | General Tolerance For features of size (Length, width, diameter) and location (position, concentricity, symmetry) + 0.125", -0.000 is typical. Material length and thickness may affect tolerances. |
Description Thickness Dimension | General Tolerance Thickness tolerances are determined by the material blank. |
Description Minimum Recommend Part Size | General Tolerance 1.000" |
Description Minimum Feature Size | General Tolerance 2X material thickness with a minimum of 1.000" |
Description Kerf (slit size) | General Tolerance Approximately 0.50" |
Description Edge Condition | General Tolerance Plasma edge will have vertical striations and be tapered. Upper edges may have a rounded area with top splatter. |
Please check out Xometry's Manufacturing Standards for more information on tolerances per process. Unless we have agreed to other tolerances in your Quote, we will work to achieve and hold the tolerances noted.
Design Guide: Laser and Sheet Cutting
An Overview of the Plasma Cutting Process
The Basics Of Plasma Cutters
Plasma cutting, or plasma arc cutting, uses an accelerated jet of hot plasma to cut through electrically conductive materials. Plasma cutters are the fastest way to cut through gauge material up to 6" thick and are more cost-efficient to run than high-powered CNC laser cutters. Plasma cutters do their best work on large sheet metal parts, versus CNC laser cutters which are better at more detailed work and creating holes — something plasma cutters struggle with.
How Plasma Cutters Work
When energy and heat are applied to a gas, the molecules travel faster and collide more violently, turning the gas into a plasma. Using compressed air or other inert gas, the plasma is accelerated out of the plasma torch toward the workpiece where it completes an electrical arc with the conductive workpiece. Similar to Electrical Discharge Machines, plasma cutting machines use electricity to melt and cut the workpiece.
Why Use Plasma Cutting For Your Parts?
Plasma cutters are a good all-around sheet metal fabrication tool, though they lack the material cutting diversity of waterjet cutters and don’t have the precision of laser cutters. For larger sheet metal parts, plasma cutting machines are more cost-efficient than CNC laser cutters and can cut thicker materials easily. Plus, they are easy to operate and can cut at high speeds while maintaining precision.
Sheet metal offers a cost-effective way to fabricate product device panels, boxes and cases for a variety of applications. We build enclosures of all styles, including rackmounts, “U” and “L” shapes, as well as consoles and consolets.
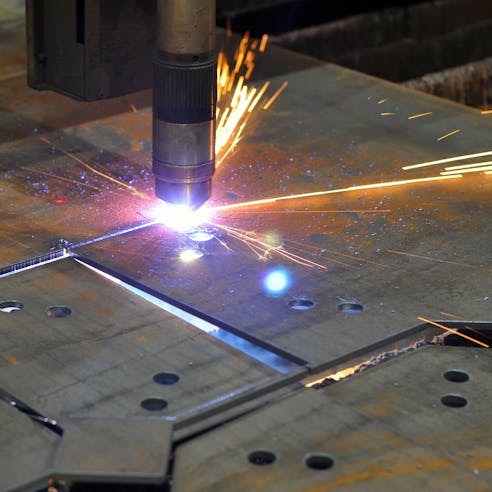
Why Choose Xometry for Plasma Cutting?
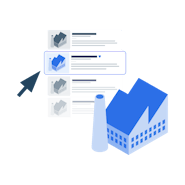
Endless Options
Choose from millions of possible combinations of materials, finishes, tolerances, markings, and certifications for your order.
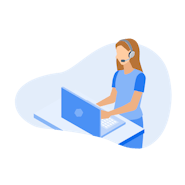
Easy to Use
Get your plasma cut parts delivered right to your door without the hassle of sourcing, project management, logistics, or shipping.
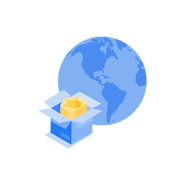
Vetted Network
We are ISO 9001:2015, ISO 13485, IATF 16949:2016, and AS9100D certified. Only the top shops that apply to become Suppliers make it through our qualification process.