Plastic 3D Printing Service
Plastic Prototypes and Production Parts in as Fast as 1 Day |
Free Shipping on All US Orders | International prototype pricing includes tariffs.
Plastic 3D Printing with Xometry
Plastic 3D printing is one of the fastest and most cost-effective methods available for the iterative design, prototyping, and production of custom parts with Xometry. Rather than the material being removed from stock, as with subtractive manufacturing processes such as CNC machining, 3D printing works by repeatedly layering small amounts of plastic to build a design from the ground up. This is done by providing the 3D plastic printers with a three-dimensional digital design file, commonly referred to as a computer-aided design (CAD) file. Once you have a CAD file for your design, there are a number of different 3D plastic printing methods that can be used to create your parts. Xometry uses industrial additive manufacturing to print parts in a variety of engineered polymers, from transparent prototypes to flame-retardant plastics used in aerospace.

Thermoplastic 3D Printing
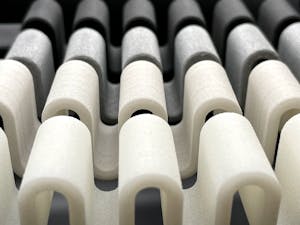
Selective Laser Sintering (SLS) 3D Printing Service
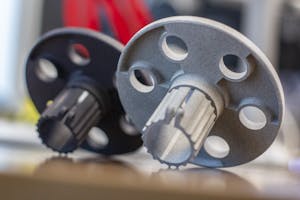
HP Multi Jet Fusion (MJF) 3D Printing Service
Fused Deposition Modeling (FDM) 3D Printing Service
Resin 3D Printing
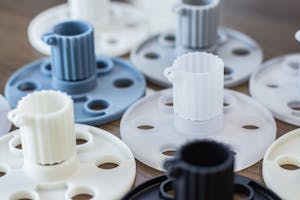
Stereolithography (SLA) 3D Printing Services

PolyJet 3D Printing Service
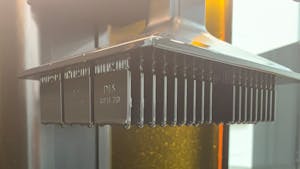
Carbon Digital Light Synthesis™ (DLS™) 3D Printing Service
Ready to get started on your custom Plastic 3D Printing quote?
Free shipping available for domestic 3D printing orders ; learn more!
Applications of Plastic 3D Printing
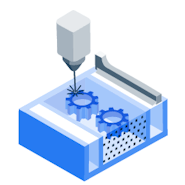
Concept Models
The speed and versatility of plastic 3D printing let product developers create physical snapshots of their designs through the iterative process.
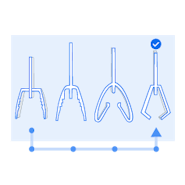
Rapid Prototyping
Plastic 3D printing can be used to create fully-functional plastic prototypes, complete with moving parts, as well as all-in-one assemblies.

Direct Digital Manufacturing
The high accuracy and consistency of plastic 3D Printing make it an ideal way to build large quantities of discrete or customized parts.
Advantages of Plastic 3D Printing
- Precision: We use the latest generation of 3D printing technologies to meet demanding tolerances
- Scalability: Whether it is one, or thousands, Xometry has the 3D printing capacity to meet your needs and lead time
- Durability: With engineered materials like nylon, polycarbonate, or even ULTEM, 3D printed plastic parts are tough and functional
- Rapid Turnaround: Get parts in as quick as 1 business day
- Complex Geometries: 3D printing can create complex parts without increased costs
- Low Cost: 3D printing is inexpensive and has no minimum order quantities
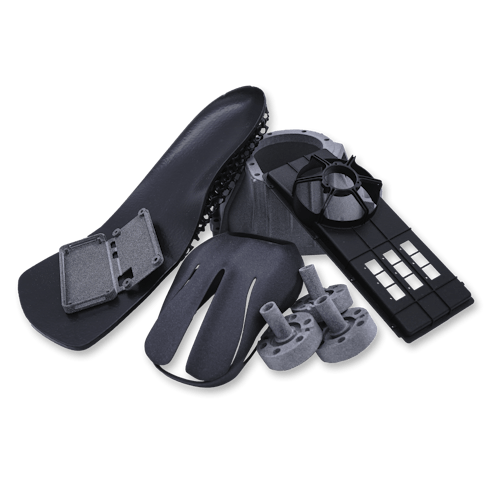
Why Choose Xometry for Plastic 3D Printing?
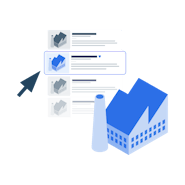
Endless Options
Choose from millions of possible combinations of materials, finishes, tolerances, markings, and certifications for your order.
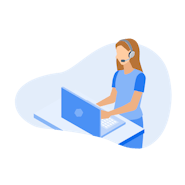
Easy to Use
Get your parts delivered right to your door without the hassle of sourcing, project management, logistics, or shipping.
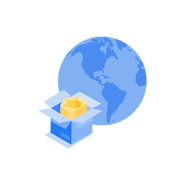
Vetted Network
We are ISO 9001:2015, ISO 13485, and AS9100D certified. Only the top shops that apply to become Suppliers make it through our qualification process.