3D printing technology has completely changed the aerospace industry by offering a quick, flexible, and affordable method to produce complex parts. Using successive layers of material, a 3D printing (or additive manufacturing) device creates three-dimensional objects from digital models. Numerous aerospace parts, such as brackets, ducts, turbine blades, and engine components, can be produced using this technology. Due to its capacity to quickly produce high-quality, customized parts, 3D printing technology has become more common in the aerospace sector in recent years.
3D printing has advanced over time. Where once 3D printers could only create rough prototypes, they are now able to make extremely intricate and precise components. The use of 3D printing in aerospace manufacturing has many advantages. First of all, it enables the manufacture of lightweight parts that are durable enough to withstand the harsh conditions of flight. By doing away with the need for tooling and assembly, printers also cut down on lead times and production costs. This article will examine the development and application of 3D printing technology in the aerospace industry.
How Is 3D Printing Technology Used in Aerospace Parts Manufacturing?
Aerospace manufacturers use 3D printers to create intricate geometries, cut down on waste, and speed up prototyping. They enable manufacturers to design lightweight, high-strength parts. NASA, SpaceX, and Airbus are just a few of the aerospace organizations that produce parts using 3D printing technology.
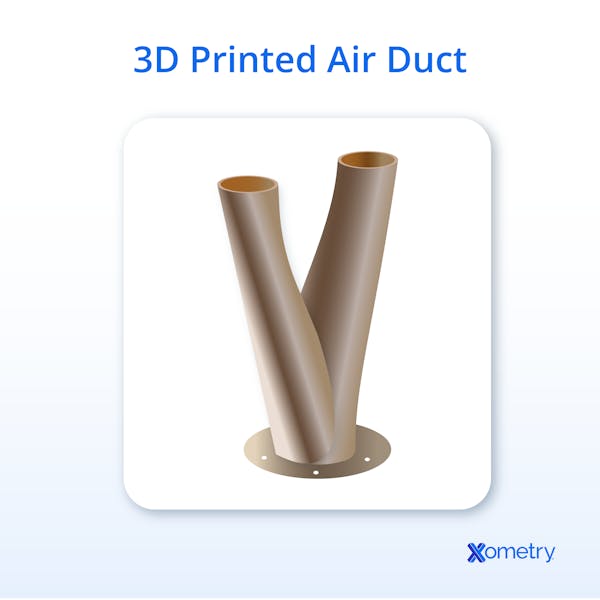
How Has 3D Printing Technology Evolved Over Time?
Since its invention in the 1980s, 3D printing technology has steadily advanced. Its primary purpose at first was rapid prototyping of components and models. Thanks to developments in technology and materials, 3D printers can now turn out end-use parts. The ability to produce lighter and more intricate aircraft parts using 3D printing has increased in recent years as printers have become more available and affordable.
What 3D Printing Technology Is Used for Manufacturing Aerospace Parts?
Selective laser sintering (SLS) is a popular 3D printing technique for producing aerospace parts. SLS creates 3D objects layer-by-layer by selectively melting and fusing powdered materials such as metal alloys or thermoplastics. SLS is a popular option for manufacturers of airplane parts because it can form strong, durable parts that nonetheless include intricate details. Fused deposition modeling (FDM) and stereolithography (SLA) are other common 3D printing technologies in aerospace manufacturing.
What Are the Benefits of Using 3D Printing To Manufacture Aerospace Parts?
The advantages of 3D printing aerospace components include:
1. Weight Reduction
3D prints help you reduce part weights, which is essential for reducing carbon dioxide emissions and fuel consumption. As a result, efficiency and payload capacity both improve. Combined with generative design software, the potential for complex 3D printed parts is nearly limitless. Simply put, 3D printing is a practical and efficient solution for aerospace producers who want to lighten their aircraft and boost performance.
2. Material Efficiency
By using only the amount of material required to fill the part’s final volume, 3D-printed designs cut down on waste. Compared to conventional subtractive manufacturing techniques, 3D printing minimizes waste by only adding material where it is needed. The layer-by-layer production method makes this possible. Also, the modern variety of 3D printable materials, including engineering-grade thermoplastics and metal powders, enable a wider array of sophisticated aerospace applications.
3. Minimal Volume Production
3D printing is an affordable solution in the aerospace and defense sectors, where low-volume production of complex parts is commonplace. Complex geometries thus don’t demand expensive specialty tooling. 3D printing lowers manufacturing costs and accelerates the production process while preserving accuracy and quality even in small production runs.
4. Consolidation of Parts
Part consolidation is a major advantage of 3D printing. This can be doubly helpful in the aerospace industry since consolidating multiple parts into one typically means reducing both weight and complexity. Not only does consolidation make assembly and maintenance easier, but it also simplifies the supply chain and raises the aircraft's general efficiency.
5. Repairs and Maintenance
Repair and maintenance applications for 3D printing are particularly advantageous. Given that an aircraft typically lasts 20 to 30 years, it must undergo maintenance, repair, and overhaul (MRO) to remain safe and efficient. By adding material to damaged surfaces, metal 3D printing technologies like direct energy deposition (DED) allow you to restore and repair expensive components like turbine blades. This procedure is quick and economical, minimizing the downtime needed for repairs.
For more information, see our guide on Everything You Need to Know About 3D Printing.
How Has 3D Printing Changed the Manufacturing Process of Aerospace Parts?
Rapid prototyping, customization, and cost reduction made possible by 3D printing have revolutionized aerospace manufacturing. Complex aerospace parts can take months to produce using conventional manufacturing techniques, but some of these structures can be printed in mere hours. Additionally, 3D printing makes it possible to build complex geometries and lightweight structures, improving performance and fuel efficiency. And since printers can be located nearly anywhere, you may also cut out the time and expense of shipping.
What Materials are Used to 3D Print Aerospace Parts?
Aircraft and spacecraft demand high-performance, climate-resistant materials. It’s not uncommon to see materials like these in an aerospace 3D printing shop:
- Titanium Alloys: Strong, lightweight, and remarkably resistant to corrosion.
- Inconel®: Used in jet engines and turbine blades because it is heat-resistant and long-lasting.
- Aluminum Alloys: Lightweight and versatile; commonly found in structural components.
- Carbon Fiber Composites: High stiffness, low thermal expansion, impressive strength, and lightweight.
- Stainless steel: corrosion-resistant and durable; commonly used in fasteners, landing gear components, and actuators.
These materials are perfect for aerospace applications because of their high strength, long lifespan, and temperature resistance.
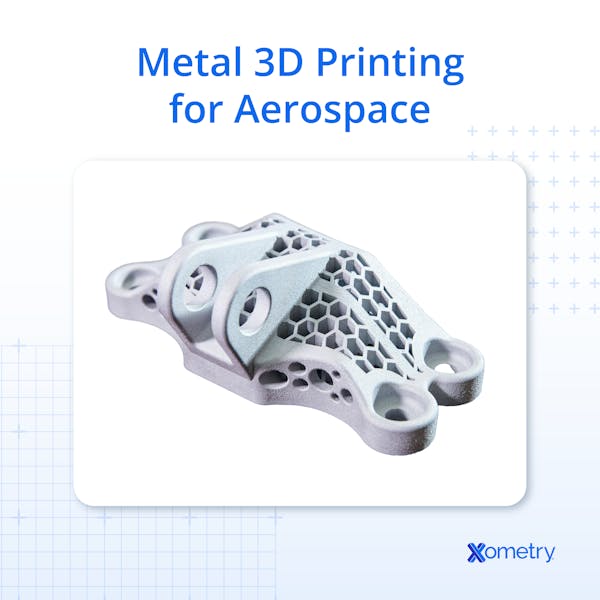
How Are the Quality and Strength of 3D Printed Aerospace Parts?
The printing technology, material properties, and design considerations are just a few of the variables that affect the strength and quality of 3D-printed aerospace parts. Recent years have seen successful 3D-printed engine parts, wing components, and cabin interior components. The accuracy and control provided by 3D printing technology have made it clear that 3D-printed airplane parts can match or even exceed conventionally manufactured components in terms of strength and quality.
How Do 3D Printing Aerospace Parts Impact Costs and Timelines?
The use of 3D printing in the manufacture of aerospace parts can significantly impact both costs and timelines. Compared to conventional manufacturing techniques, 3D printing is less wasteful and often faster. Additionally, it enables greater design flexibility, which can lead to components that are lighter and more effective. That, in turn, may reduce costs and improve production times.
What Are Examples of Successful 3D-Printed Aerospace Parts?
There are numerous instances of successful 3D-printed aerospace components. For instance, printed metal brackets from Airbus are 35% lighter and 40% stiffer than conventional brackets. For its 787 Dreamliner, Boeing developed 3D-printed titanium components. SpaceX prints the SuperDraco rocket engines for its Dragon spacecraft, and NASA has begun printing rocket engine components as well. All these successful additive aerospace parts make it clear that 3D printing can reduce weight, enhance performance, and streamline production.
What Is the Position of 3D Printing in Developing Next Generation Aerospace Technologies?
Cutting-edge aerospace technologies now rely heavily on 3D printing. The technology has made it possible to produce lightweight, complex parts that are stronger and more durable than their conventional counterparts. This significantly reduces fuel consumption and maintenance expenses. Major aerospace firms like Boeing and Airbus have already incorporated 3D printing into their manufacturing procedures, demonstrating the technology's potential to revolutionize the sector. The technology will likely become more and more important as future aviation components and aerospace systems are developed.
What Is the Future of 3D Printing Technology for The Aerospace Industry?
In the aerospace sector, 3D printing technology has a bright future. 3D printing is the best option to manufacture parts in small quantities because it doesn’t demand specialized tooling. Not only that, but it allows for high-precision, complex geometries to be made without long lead times. Lightweight printed parts can lower emissions and fuel consumption.
Can Aerospace Parts Be 3D Printed?
Yes, aerospace parts can be 3D printed. Indeed, 3D printers are becoming critical to modern aerospace part production. Complex geometries that are challenging to manufacture using traditional methods are often easy to print. The technology can reduce part weight, which directly impacts the performance and fuel efficiency of aircraft and spacecraft. Airbus and Boeing are two businesses that have already committed heavily to 3D printing aerospace components.
Does Nasa Use 3D-Printed Aerospace Parts?
Yes, NASA has been 3D printing aerospace components since the 1990s. They’ve been able to lower costs, boost efficiency, and speed up the manufacturing process thanks to recent improvements in 3D printing. They have even printed rocket engines.
Summary
This article presented 3D printing technology for aerospace parts, explained what they are, and discussed their benefits and evolution over time. To learn more about 3D printed aerospace parts, contact a Xometry representative.
Xometry provides a wide range of manufacturing capabilities, including 3D printing and other value-added services for all of your prototyping and production needs. Visit our website to learn more or to request a free, no-obligation quote.
Copyright and Trademark Notices
- Inconel® is a registered trademark of Special Metals Corporation
Disclaimer
The content appearing on this webpage is for informational purposes only. Xometry makes no representation or warranty of any kind, be it expressed or implied, as to the accuracy, completeness, or validity of the information. Any performance parameters, geometric tolerances, specific design features, quality and types of materials, or processes should not be inferred to represent what will be delivered by third-party suppliers or manufacturers through Xometry’s network. Buyers seeking quotes for parts are responsible for defining the specific requirements for those parts. Please refer to our terms and conditions for more information.
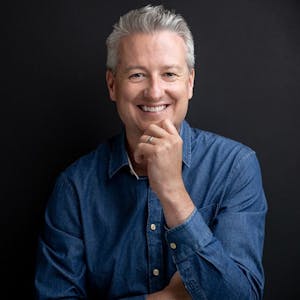