Additive manufacturing, also known as 3D printing, is a cutting-edge manufacturing process revolutionizing industries worldwide. It involves building objects additively, layer by layer, using digital models, unlike traditional subtractive methods, which remove material.
Additive manufacturing enables the creation of complex geometries that are challenging or impossible to achieve with conventional techniques. Moreover, it offers a wide range of material compatibility, including plastics, metals, ceramics, and composites, providing flexibility in material selection for diverse applications. Additive manufacturing offers opportunities for the development of creative, new products, as well as improved efficiency in material usage.
This article will discuss what additive manufacturing is, its process, uses, materials, advantages, and disadvantages.
What Is Additive Manufacturing?
Additive manufacturing (AM), also known as 3D printing, revolutionizes fabrication by constructing objects layer by layer, guided by 3D digital computer models. Unlike subtractive methods such as machining, which carve away material from a solid block, AM adds material gradually to form the desired shape. This innovative approach grants unparalleled design freedom, allowing for intricate geometries and customization.
AM encompasses various techniques, each offering unique advantages. Filament deposition involves melting and extruding thermoplastic materials through a nozzle, while laser sintering utilizes a laser to fuse powdered materials layer by layer. Additionally, stereolithography employs ultraviolet lasers or LCD screens to solidify light-curable liquid resin into precise shapes.
Historically, AM has seen applications in diverse industries, including aerospace, automotive, healthcare, and consumer goods. Initially used for rapid prototyping, it has evolved to include production-grade components. However, the layer-by-layer fabrication can lead to potential weaknesses at interfaces, necessitating careful design considerations.
One of AM's greatest strengths lies in its customization capabilities, allowing for tailored solutions to meet specific needs. From personalized medical implants to intricate architectural models, AM empowers designers and engineers to bring their visions to life with precision and efficiency.
Who Invented Additive Manufacturing?
Chuck Hull is often credited as the pioneer of additive manufacturing due to his invention of stereolithography. However, the concept of layer-by-layer fabrication predates his work. The roots of additive manufacturing can be traced back to the 1970s. During this time, researchers and engineers began exploring various techniques for building objects layer by layer. One notable precursor to modern additive manufacturing is the work of Hideo Kodama, a Japanese researcher.
Kodama's 1981 paper detailed the UV solidification of photopolymers for 3D object fabrication, setting the groundwork despite limited commercial follow-through at the time. Carl Deckard, with advisor Joseph Beaman, pioneered selective laser sintering (SLS) at the University of Texas at Austin in the mid-1980s, fusing powdered materials with lasers, advancing additive manufacturing.
When Did Additive Manufacturing Start?
The commercialization of additive manufacturing began in the mid-1980s with Chuck Hull's invention of stereolithography. In 1986, Hull was granted a patent for this system, leading to the formation of his company, 3D Systems Corporation. Subsequently, in 1988, 3D Systems Corporation released the first commercial 3D printer, the SLA-1.
Around the same time, a 3D inkjet printer was developed in a skunkworks project at Exxon, although commercialization of this technology didn't occur until 1991. This early phase of commercialization saw the emergence of companies like 3D Systems Corporation and the introduction of processes such as stereolithography and inkjet printing to the market.
This breakthrough laid the groundwork for subsequent additive manufacturing techniques and technologies. Over the years, additive manufacturing has evolved significantly, with advancements in materials, processes, and applications.
What Is the Process of Additive Manufacturing?
The process of additive manufacturing involves several steps:
- Start by creating a digital 3D model using a CAD program. Save the design in the STL file format, which contains object geometry. Import the STL file into the slicer software to slice the model and generate print paths. Adjust printing parameters such as material type and speed for optimization. Convert the sliced model into G-code, the language understood by 3D printers. Finally, send the G-code to the printer, instructing it to print the object layer by layer.
- Prepare the 3D printer by calibrating temperature, speed, and layer height settings, and downloading the G-code file to the printer.
- Load the selected material into the additive printing device. Materials that can be used for 3D printing include composites, plastics, metals, ceramics, paper, and even biological materials like cells or proteins.
- Begin printing. The printer will interpret the G-code instructions for each successive layer, depositing or curing material in the exact location where it is needed for that layer.
- Ensure proper bonding between layers. This may simply happen as part of the printing process in some techniques, such as fused deposition modeling (FDM), but for others, a separate sintering or curing step may be needed.
- Allow the printed object to proceed without interruption as each layer is built up.
- Perform needed finishing tasks, including support removal, which may be necessary for designs with overhangs or complex geometries where supports are used during printing to prevent sagging or deformation. Additionally, surface refinement, machining, or additional curing may be required to achieve the final product.
- Apply any final finishing touches or treatments as needed, such as painting, plating, or assembly with other components.
What Are the Uses of Additive Manufacturing?
Today, additive manufacturing is an integral part of the product fabrication process in many industries. It has several possible uses, including:
- It facilitates the quick and cost-effective production of prototypes for design verification, functional testing, and concept validation.
- It allows for highly customized and personalized products, such as medical implants, dental prosthetics, and consumer goods.
- Additive manufacturing enables the production of intricate geometries that are difficult with traditional methods. In aerospace, turbine blades with internal cooling channels improve engine efficiency. In medicine, personalized implants fit individual anatomies, promoting faster healing. Automotive components benefit from lightweight, complex designs that enhance performance.
- It facilitates small-batch or customized manufacturing without expensive tooling, enabling agile manufacturing and reducing inventory costs.
- It is utilized in the medical sector for manufacturing custom implants tailored to patients, prosthetic devices, anatomical replicas for surgical preparation and instruction, as well as surgical guides to assist in procedures.
- It is used for prototyping, tooling, and producing lightweight components with improved strength-to-weight ratios and customization options.
- 3D printing can be utilized in educational institutions and research facilities for teaching, experimentation, and exploring novel applications in various disciplines.
- Offers opportunities for sustainable production by reducing waste, energy consumption, and carbon emissions.
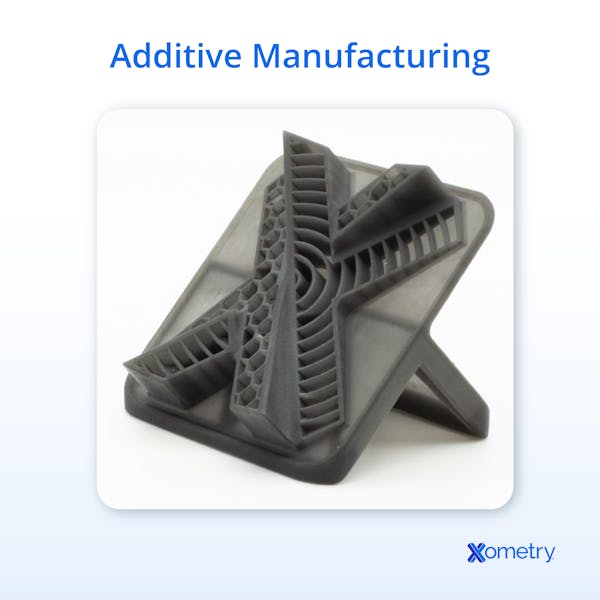
Category | Materials |
---|---|
Category Plastics | Materials Thermoplastics (e.g., PLA, ABS, PETG), thermosets (e.g., resins), flexible polymers (e.g., TPU, TPE) |
Category Metals | Materials Stainless steel, aluminum, titanium, Inconel®, cobalt-chrome, copper |
Category Ceramics | Materials Alumina, zirconia, silicon carbide, porcelain, glass-ceramics |
Category Composites | Materials Carbon fiber-reinforced polymers (CFRP), glass fiber-reinforced polymers (GFRP), metal matrix composites (MMC), ceramic matrix composites (CMC) |
Category Biomaterials | Materials Hydrogels, bio-inks, cell-laden materials, bioresorbable polymers |
Category Wax & Wax-Like Materials | Materials Investment casting patterns, sacrificial molds, dental wax |
Category Sand & Binders | Materials Sand casting molds and cores can be printed with the use of binder materials |
Category Food Materials | Materials Chocolate, sugar, dough, meat substitutes |
Table 1: Common Materials Used in Additive Manufacturing
What Are the Different Types of Additive Manufacturing?
Some common different types of additive manufacturing include the following:
- Fused Deposition Modeling (FDM): Operates by liquefying plastic filaments and depositing them incrementally in layers to construct objects. The material is deposited in a predetermined pattern based on a three-dimensional digital design to create the desired object.
- Selective Laser Sintering (SLS): Utilizes a high-power laser to selectively fuse powdered materials into solid layers, typically polymers or metals. The powdered material is spread evenly across the build platform. The laser selectively sinters or melts the powder according to the required shape of the current cross-sectional layer of the design. After each layer is sintered, the build platform descends, a new layer of powder is spread, and the process is repeated until the object is fully formed.
- Stereolithography (SLA): Employs a vat of liquid photopolymer resin that is selectively cured by a UV laser to build layers. The UV laser traces the cross-section of the virtual design on the surface of the liquid resin, causing it to solidify. Once a layer is completed, the build platform moves down, and a new resin layer is spread over the previous one. SLA is known for its high resolution and ability to produce intricate details, making it suitable for applications requiring fine features and smooth surface finishes. mSLA (masked stereolithography) is commonly used in consumer-grade systems and uses an LCD screen rather than a laser to cure each layer.
What Are the Advantages of Additive Manufacturing?
Some advantages of additive manufacturing include:
- Facilitate rapid prototyping by significantly reducing the time and cost of producing prototypes. Design changes can be implemented quickly and easily, accelerating product development and shortening time-to-market. Companies can quickly validate concepts, test functionality, and gather feedback early in the design process, leading to more efficient product development and innovation.
- It gives designers more freedom, making it possible to make complicated shapes and structures that would be hard or impossible to make with conventional means. Designers can quickly iterate designs and customize products without the constraints of tooling or machining limitations, leading to innovative and optimized designs.
- It uses fewer resources than traditional methods because it only consumes the raw material needed to make the item, leaving behind less waste. Complex geometries can be optimized for material usage, reducing material consumption and lowering production costs. Additive manufacturing also allows for production on request and localized manufacturing, which cuts down on the need for large stockpiles, extra transportation, and storage, which helps the environment and saves resources.
What Are the Disadvantages of Additive Manufacturing?
Some disadvantages of additive manufacturing include:
- Often has a limited range of possible materials compared to traditional manufacturing processes. While the range of available materials is expanding, certain specialized materials, such as high-performance alloys or ceramics, may be challenging to process with additive techniques.
- Parts may require additional post-processing to achieve the desired surface finish, dimensional accuracy, and mechanical properties. Depending on the printing technique and material used, parts may exhibit visible layer lines or surface defects that necessitate smoothing, sanding, or coating.
- The processes can be slower than traditional manufacturing methods, particularly for large or complex parts. The layer-by-layer nature of additive manufacturing can result in longer production times, especially for high-resolution or intricate designs, which may hinder its suitability for mass production or time-sensitive applications.
How Does Additive Manufacturing Differ From Traditional Manufacturing Methods?
Additive manufacturing differs from traditional manufacturing methods primarily in the process used to create objects. Additive manufacturing builds objects layer by layer from digital designs using materials such as plastics, metals, ceramics, or composites. It involves depositing material only where needed, allowing for complex geometries, customized designs, and reduced material waste.
Traditional manufacturing methods typically involve subtractive processes, removing material from a solid block to create the desired shape. Processes like milling, turning, drilling, and casting are commonly used in traditional manufacturing. Traditional methods often require extensive tooling, fixturing, and machining operations, resulting in longer lead times and higher material waste.
Furthermore, additive manufacturing offers advantages in terms of design flexibility, rapid prototyping, on-demand production, and customization. In contrast, traditional manufacturing methods may excel in mass production, high-volume manufacturing, and yielding specific material properties. Overall, additive manufacturing represents a paradigm shift in manufacturing by enabling new possibilities for design, production, and efficiency.
Is Additive Manufacturing the Same as 3D Printing?
Yes, additive manufacturing is the same as 3D printing. The terms “additive manufacturing” and “3D printing” are often used interchangeably to describe building objects layer by layer from digital designs. Both terms refer to the same underlying technology, in which the material is added incrementally to create a three-dimensional object.
What Is the Difference Between Additive Manufacturing and 3D Printing?
The primary differences between additive manufacturing and 3D printing are:
- Terminology: "Additive manufacturing" is a broader term encompassing several techniques and processes for building objects layer by layer from digital designs. "3D printing" is often used interchangeably with additive manufacturing, though historically it referred to lower-end or consumer-grade systems such as those using fused filament fabrication (FDM) or inkjet-like deposition. In industrial contexts, "additive manufacturing" is preferred for its technical and standardized implications.
- Scope and Applications: Additive manufacturing includes industrial-scale processes like selective laser sintering (SLS), stereolithography (SLA), and electron beam melting (EBM), which are used in various industries for prototyping, tooling, and production of end-use parts. 3D printing, on the other hand, is often associated with smaller-scale desktop printers used for rapid prototyping, educational purposes, and hobbyist projects.
- Precision and Materials: Industrial additive manufacturing processes typically offer higher precision and accuracy, and a more comprehensive range of materials than consumer-grade 3D printers. While 3D printing may be limited to plastics and low-cost materials, additive manufacturing encompasses materials such as metals, ceramics, composites, and even biomaterials.
- Complexity and Cost: Additive manufacturing systems used in industrial settings are more complex and expensive than consumer-level 3D printers. Industrial-scale additive manufacturing machines often require specialized training, maintenance, and infrastructure to operate effectively, whereas 3D printers are generally more accessible and user-friendly.
Summary
This article presented additive manufacturing, explained it, and discussed its various applications. To learn more about additive manufacturing, contact a Xometry representative.
Xometry provides a wide range of manufacturing capabilities, including 3D printing and other value-added services for all of your prototyping and production needs. Visit our website to learn more or to request a free, no-obligation quote.
Copyright and Trademark Notices
- Inconel® is a registered trademark of Special Metals Corporation.
- FDM® is a registered trademark of Stratasys Inc.
Disclaimer
The content appearing on this webpage is for informational purposes only. Xometry makes no representation or warranty of any kind, be it expressed or implied, as to the accuracy, completeness, or validity of the information. Any performance parameters, geometric tolerances, specific design features, quality and types of materials, or processes should not be inferred to represent what will be delivered by third-party suppliers or manufacturers through Xometry’s network. Buyers seeking quotes for parts are responsible for defining the specific requirements for those parts. Please refer to our terms and conditions for more information.
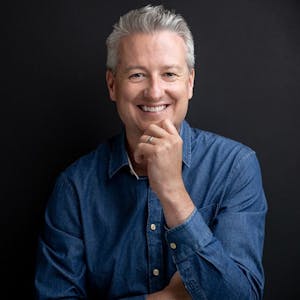