Direct laser metal sintering (DMLS) has been used by many manufacturers since the late 1990s to make complex metal parts that can’t easily be produced with the likes of stamping or extrusion. This 3D printing process is complex in and of itself, but it’s also a unique technology that’s hard to find an alternative for when it comes to specific components. Whether you’re considering having your own products printed through DMLS, or simply just intrigued by the concept, read on to find out all about this manufacturing method.
What Is Direct Metal Laser Sintering?
DMLS is a form of 3D printing, and it uses powder-bed fusion technology to work. It shoots a high-powered fiber laser beam at a single layer of metal powder, which then fuses together onto the previous thin layers. It continues this process until the metal part is fully printed.
You might be wondering where the “sintering” part comes in, as it doesn’t seem to occur. This is actually a misnomer that happened after the translation of DMLS. In Germany (where this tech was created), it was called Direktes Metall-Laser-Schmelzen, schmelzen meaning “to melt.” When translated into English, the “S” became sintering, but because of this slight confusion, you’ll sometimes find this process called direct metal laser melting.
How It Works
Now that you get the gist, we’re going to get more into the nitty gritty of the DMLS process. The start of the process involves the fiber laser beam, which can have up to 1,000 W of power. It begins scanning the cross-section of a part layer and starts melting the powder particles together.
While there is often one laser beam, some machines have the capacity to shoot out four beams at a time, which quadruples how quickly the process moves along. Usually, a DMLS printer will scan and laser at a speed of around 7 m/s.
Once the first layer is finished, the bed moves down, and another layer of metal powder is put down. Then, the system will fill the printing chamber with an inert gas to prevent the part from oxidizing during the rest of the printing process. After this takes place, the melting of the next layer occurs until the part is complete.
The quality and accuracy of the print comes down to how good the laser and optical components of the printer are. Normally the focal point is between 40 to 100 microns in diameter—which means the smallest feature you can get is 40 microns.
In the picture below, you can get a good idea of how a DMLS printer looks and what components are featured.
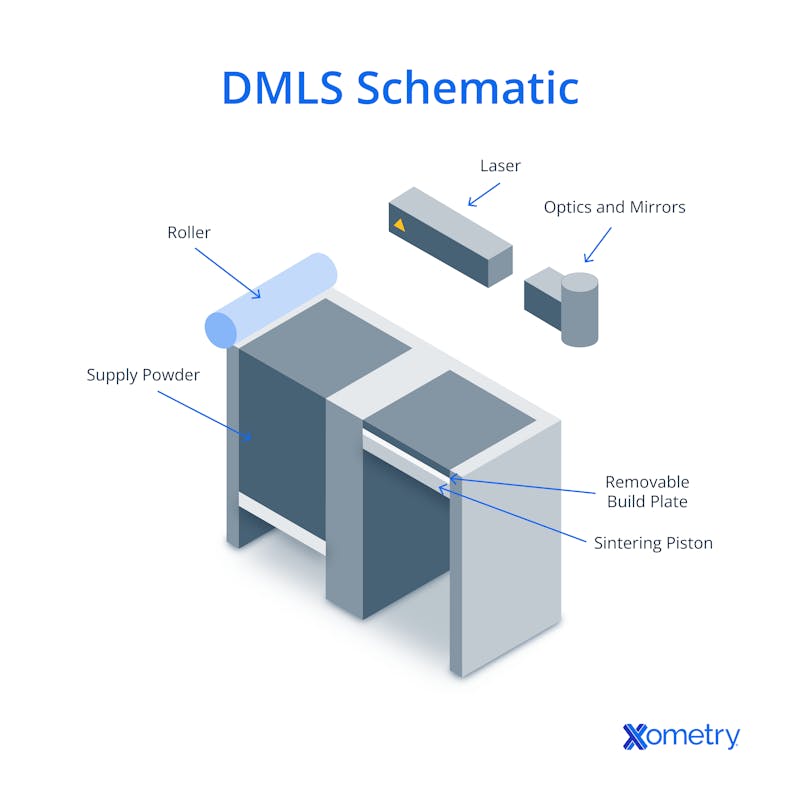
Materials for Printing
There are plenty of different materials you can choose for your DMLS prints. We’ve laid out the most commonly seen choices below:
- Aluminum alloys (AlSi10Mg): This material is also used in casting, but it’s great for DMLS builds that are designed to have thin walls and fine features. Its good mechanical and thermal properties also make it a popular choice.
- Inconel 718: This trademarked superalloy is made of nickel and is popular for aerospace uses because of its great corrosion resistance and strength at high temperatures.
- Titanium (Ti6Al4V): This alloy is great for uses like implants because it’s biocompatible and has excellent corrosion resistance and mechanical properties.
- Stainless steel (316L): You’ll find this popular steel used for DMLS printing, too. Because of its great corrosion resistance, it often gets turned into parts of acid-producing facilities and other industrial applications.
- Copper: Its pure form, as well as alloys like CuCP and CuCrZr, can all be printed through DMLS. You’ll usually find it made into heat exchangers and induction coils because of its thermal and conductivity properties.
- Case-Hardening Steel (20MnCr5): As its name says, this kind of steel can be hardened, which is ideal for DMLS printed parts that need to have serious wear resistance (like gear wheels).
- Cobalt-Chrome (CoCr): If you’d like the same corrosion resistance and great strength at high temperatures without the nickel content of Inconel 718, this is the material for you.
The following image shows a stainless steel part we printed through DMLS.
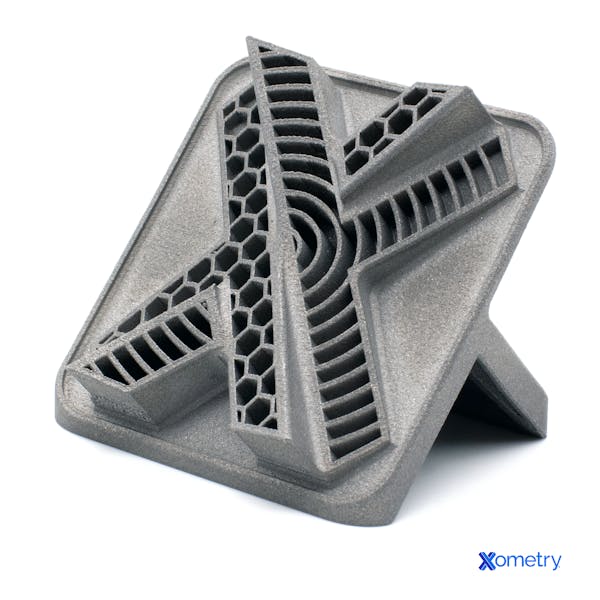
Uses for DMLS and Part Creation
For complex metal parts that can’t as easily be made through other common manufacturing processes (like CNC machining or metal injection molding), DMLS comes in handy. Manufacturers often turn to it for products that’ll be used in the aerospace, medical, turbomachinery, and automotive industries. It’s possible to create separate parts as well as monolithic components that don’t need to be assembled down the road.
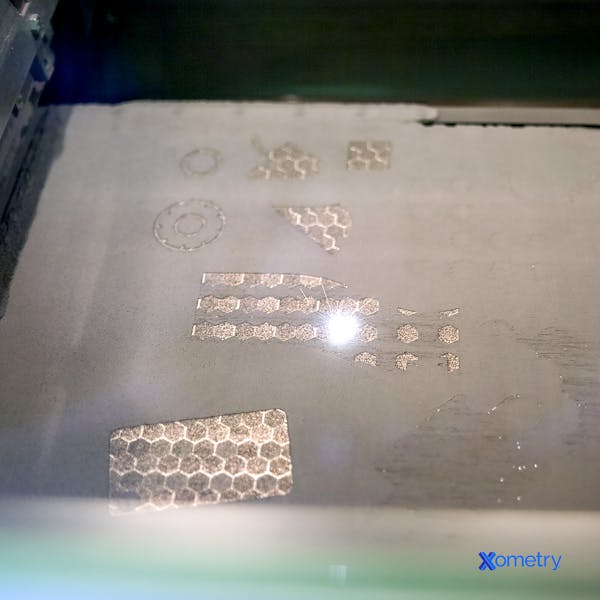
DMLS and SLM 3D printing: What’s the difference?
Both of these 3D printing types involve using powder-bed fusion technology. The main difference is that SLM printing often uses even more high-powered lasers than DMLS and is better for high quantities of products. DMLS is best for smaller production runs and parts that require complex details.
What are the advantages of DMLS printing?
There are plenty of upsides to using a DMLS printer for your products. The main advantages are that it can print parts using a variety of metals and even mixtures of plastic and metal. Its high resolution also makes it easier to create very small, detailed portions of components.
What are the disadvantages of DMLS printing?
We can’t give you all the information on this handy 3D printing type without mentioning a couple of little snags. These printers need support materials while they’re printing parts because of how heavy metal can be. Parts are also subject to internal stresses because of how hot the manufacturing process is. Lastly, DMLS printers are strong, but have much lower power lasers than SLM or EBM printers. Therefore, they’re not the best for products that need to be printed quickly and have high layers.
How Xometry Can Help
Aside from DMLS printing, our team at Xometry has numerous other 3D printing services we offer to businesses. Get a free quote from our website for options such as plastic 3D printing, fused deposition modeling, selective laser sintering, and carbon DLS.
Copyright and Trademark Notices
- Inconel® is a registered trademark of Huntington Alloys division of Special Metals Corp., Huntington, WV.
Disclaimer
The content appearing on this webpage is for informational purposes only. Xometry makes no representation or warranty of any kind, be it expressed or implied, as to the accuracy, completeness, or validity of the information. Any performance parameters, geometric tolerances, specific design features, quality and types of materials, or processes should not be inferred to represent what will be delivered by third-party suppliers or manufacturers through Xometry’s network. Buyers seeking quotes for parts are responsible for defining the specific requirements for those parts. Please refer to our terms and conditions for more information.
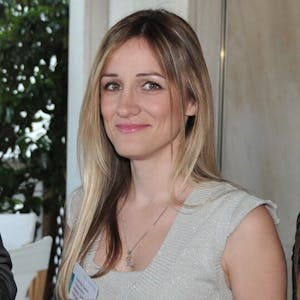