The flexural modulus of a material is a critically important calculation because it helps engineers quantify the load an item can bear in bending to design safe components and structures. An error in the calculation of the flexural modulus of a material can have dire consequences. Therefore, it’s important for engineers and builders to understand what flexural modulus is, in order to avoid potentially catastrophic situations. This article will define the flexural modulus, show how it is calculated, and describe its importance in engineering design.
What Is Flexural Modulus?
The flexural modulus (sometimes referred to as the bending modulus or tangent modulus) of a material is a mechanical property. It describes its stiffness or resistance to a bending action or its ability to deform in bending. Specifically, the flexural modulus is the ratio of stress (the force applied over a certain area) to strain (the change in length over the original length) experienced by a material during bending where tension and compression occur on opposite sides of the material. The flexural modulus of a material is dependent on its chemical composition and the arrangement of atoms throughout its structure. A higher flexural modulus indicates a material is more resistant to bending, while a lower flexural modulus indicates a material has a higher tendency to bend when a given amount of bending stress is applied.
How To Determine the Flexural Modulus of a Material
The flexural modulus of a material can be determined using the standard ASTM (American Society for Testing and Materials) procedure D790. This standard describes the testing method for determining the flexural properties of reinforced and unreinforced plastics (including thermoplastics and thermosets), composites, and electrical insulation materials.
ASTM D790 details the method for a 3-point bending test used to determine the flexural modulus of a material. A bar of the test material is supported at each end, and a force is applied to it at a point halfway along its length. The stress (y-axis) is graphed against the strain (x-axis) as increasing force is applied. The relationship between stress and strain is linear until the yield stress (the highest stress that can be experienced by a material before deformations become permanent) is exceeded. This linear portion of the graph is used to calculate the flexural modulus of the material. By dividing the value of the stress at the end of the linear portion by the value of the strain at that point, the flexural modulus can be determined.
What Is the Formula for Flexural Modulus?
The formula for flexural modulus is given below:
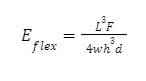
Flexural modulus formula.
Where:
- L is the length of specimen
- F is the force applied
- w is the width of the specimen
- h is the height of the specimen
- d is the deflection
For isotropic materials, Eflex is equal to Young’s Modulus of the material due to the derivation of the elastic beam theory and the second moment of inertia for a rectangular beam.
What Are the Units of Flexural Modulus?
Flexural modulus has the same units as stress, typically MPa or psi. The flexural modulus is the ratio of stress to strain. Since strain is a unitless value, the flexural modulus ends up with units of MPa or psi.
What Is the Symbol for Flexural Modulus?
The letter “E” denotes the flexural modulus of a material. However, the letter “E” also refers to another value: the modulus of elasticity (Young’s modulus). If both the flexural modulus and the modulus of elasticity are described in the same document, the flexural modulus is differentiated by using the term Eflex .
What Is the Importance of Measuring Flexural Modulus?
Measuring flexural modulus is important because it helps engineers to quantify a material’s resistance to bending. Certain designs may require materials to be strong and rigid to provide structural support. Other applications may require materials to be flexible. Understanding how the flexural modulus affects the mechanical behavior of a material in a structure is essential to designing safe and efficient products and structures.
What Is the Flexural Modulus of Plastics?
The flexural moduli of plastics vary greatly. Some plastics, like LDPE (Low-density Polyethylene), are more flexible while others, such as fiber-reinforced Nylon 12, are more rigid. The flexural modulus for LDPE is 335 MPa, while the flexural modulus for fiber-reinforced Nylon 12 is 13,700 MPa. The flexural modulus for most plastics falls between these two values.
What Is the Flexural Modulus of Steel?
As for the case of plastics, the flexural modulus for steel differs depending on the particular steel of interest. For steels, the flexural modulus can vary from 16,400 MPa to 106,000 MPa, depending on the steel’s composition and heat treatment condition, as well as its thickness.
Is There a Device Used To Measure Flexural Modulus?
Yes, there is a device used to measure the flexural modulus. Material testing systems such as tensile test machines or compressive test machines can be used to measure flexural modulus.
How Does Flexural Modulus Relate to 3D Printing?
The flexural modulus of different 3D printing materials and their print orientation has a huge impact on the ability of a 3D-printed part to bend. Ensure the print layers are made perpendicular or normal to the direction of the intended force when 3D-printing a part that may be subjected to varying loads. This is to improve the rigidity of the part and its resistance to bending.
Considering a 3D-printed horizontal bar with a force centrally applied at a point along its length, the points that experience the highest amounts of stress are the top and bottom surfaces of the part. Because the part’s layers are printed normally to the direction of the applied force, it will be more resistant to bending and thus, have a higher flexural strength. Conversely, if the part’s layers were made parallel with the applied force, it would be easier for the layers to delaminate and rupture - consequently destroying the part.
Do I Need To Test the Flexural Modulus of 3D Printing Materials?
No, it’s not necessary to test the flexural modulus of 3D printing materials. Many filament and photopolymer manufacturers publish flexural modulus data on their 3D printing materials.
What Are the Two Types of Flexural Modulus Tests?
There are two types of tests for determining the flexural modulus of a material. They are described below:
1. 3-Point Bending Test
A 3-point bend test set-up consists of two fixed supports, one at each end of a test specimen, and a rounded contact point to transmit force through a load cell to the mid-span of the test bar. The specimen bends in the shape of a “V” as the applied force increases. The 3-point bend test is often used for homogenous materials that yield or break at less than 5% strain. This includes materials like non-fiber-reinforced plastics.
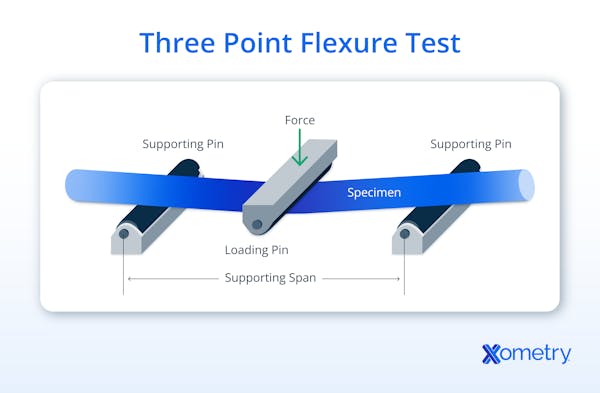
2. 4-Point Bending Test
The 4-point bend test is also performed on a test specimen supported on two opposite ends. But rather than a force being applied at a single point at mid-span, force is applied at two points. This causes the specimen to bend in the shape of a “U”. The 4-point bend test is suitable for non-homogenous materials that must exceed 5% strain to break or yield. This includes materials such as composites and wood.
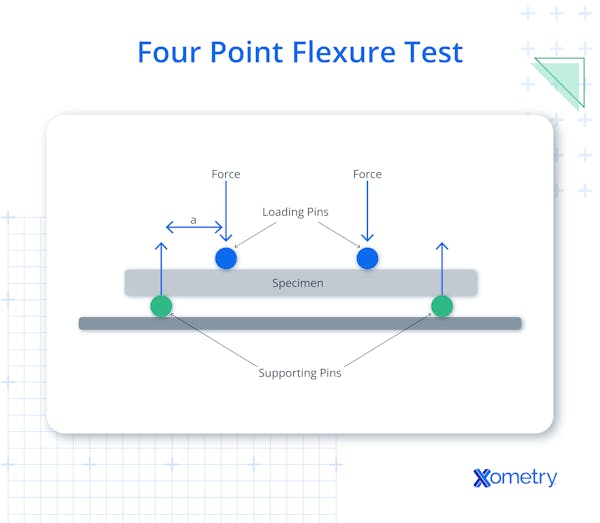
What Does a Lower Flexural Modulus Mean?
A material with a lower flexural modulus is flexible or less resistant to bending than one with a higher flexural modulus. A lower value for this characteristic means that a material deforms more in response to a given applied stress.
What Does a Higher Flexural Modulus Mean?
A higher flexural modulus indicates that a material is rigid or more resistant to bending than one with a lower flexural modulus. A higher flexural modulus means a material deforms less in response to a given applied stress.
What Materials Are Commonly Tested for Flexural Strength?
Flexural strength is not the same as flexural modulus but is obtained using the same methods. Flexural strength is the strength, or stress, at which a material breaks during bending. The materials commonly tested for flexural strength are listed below:
1. Concrete
Concrete is a material that is commonly tested for flexural strength due to the loading conditions it experiences in its typical applications and its extensive use in various construction projects. It is commonly used for beams, bridges, and sidewalks where bending is common due to the loads applied. The flexural strength of concrete is often estimated to be 10-20% of its compressive strength. Flexural strength for concrete is determined using the 4-point test method.
2. Ceramics
Ceramics, like concrete, are materials that tend to break at lower stresses compared to materials like plastics and metals. The flexural strength of ceramics is often tested because of the types of stresses they experience in their typical applications. Ceramics are often used for structural applications such as bricks, roof tiles, and floor tiles. Flexural strength for ceramics can be obtained using the 4-point bending test. Flexural strength values range from 5 to 70 MPa.
3. Composites
Composites are materials that have several constituents. This includes materials such as: plywood, reinforced concrete, and reinforced plastics. Composites are often tested for flexural strength due to their extensive use in various structural and load-bearing applications such as building columns, beams, and frames. The flexural strength of composites can be determined using 4-point bending tests. Values for the flexural strength of composites vary depending on the material being examined. For example, a composite material composed of fiber-reinforced 65% Nylon 6,6, 30% polypropylene, and 5% glass-fiber has a flexural strength of 32 MPa.
4. Plastic Materials
The flexural strength of plastics is commonly tested because of the types of loads plastics experience in applications where a certain degree of flexibility or stiffness is required. Flexible plastics are used in many more applications, including: weather seals, diving equipment, medical catheters, and cell phone cases. Rigid plastics are used in automotive parts, gears, furniture, plumbing systems, and other items. Flexural strength for plastics can range from 40 to 1000 MPa, depending on the type of plastic.
Is Flexural Modulus the Same As Tensile Modulus?
No, flexural modulus is not the same as tensile modulus. Flexural modulus refers to a material’s ability to resist deformation in bending while tensile modulus (Young’s Modulus) refers to a material’s ability to resist deformation when in tension or compression.
What Is the Difference Between Flexural Modulus and Shear Modulus?
Flexural modulus describes a material’s resistance to deformation in bending, while shear modulus describes a material’s resistance to deformation due to shear stresses. Shear stress arises from shear forces, which are forces that are applied parallel to a material’s cross-section.
What Is the Difference Between Flexural Modulus and Tensile Modulus?
The primary difference between flexural modulus and tensile modulus is that one is related to a material’s resistance to bending (flexural modulus) while the other is related to a material’s resistance to tension or compression (tensile modulus).
Summary
This article presented flexural modulus, explained what it is, and defined the formula needed to calculate it. To learn more about flexural modulus, contact a Xometry representative.
Xometry provides a wide range of manufacturing capabilities, including 3D printing and other value-added services for all of your prototyping and production needs. Visit our website to learn more or to request a free, no-obligation quote.
Disclaimer
The content appearing on this webpage is for informational purposes only. Xometry makes no representation or warranty of any kind, be it expressed or implied, as to the accuracy, completeness, or validity of the information. Any performance parameters, geometric tolerances, specific design features, quality and types of materials, or processes should not be inferred to represent what will be delivered by third-party suppliers or manufacturers through Xometry’s network. Buyers seeking quotes for parts are responsible for defining the specific requirements for those parts. Please refer to our terms and conditions for more information.
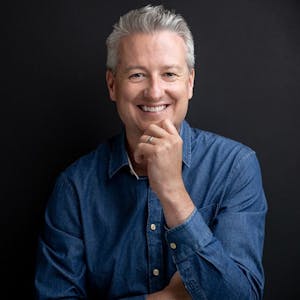