Both PolyJet and MultiJet (MJP) 3D printing are additive manufacturing methods that build parts by depositing and curing photopolymers that react to ultraviolet (UV) light. They can both be used for proof of concept and functional prototypes and can make complex parts, some of which are often found in the dental and medical sectors, specifically for things like molds for crowns and braces. Despite these commonalities, these two processes have some key differences that make one able to print with composite materials and the other better for small-to-medium production. Read on to find out which.
What is PolyJet Printing?
First developed in 2000 by Objet Geometries and acquired by Stratasys, who now owns its trademark rights, PolyJet printing works similarly to an inkjet printer. “PolyJet is a process by which material is jetted onto a print plate layer by layer,” says Christian Tsu-Raun, the Team Lead at Xometry’s Manual Quoting. “It’s relatively slow but very accurate, and good for small, nonfunctional prototypes.” In the process, tiny drops of photopolymers are released in areas that have been programmed beforehand to create 2D layers on top of each other. It then uses a UV light to harden those drops and set each layer’s shape. PolyJet is known for retaining a high level of detail and can print in layers as thin as 16 microns; however, Xometry typically prints at a layer height of 25 microns.
The photopolymer will only become dimensionally stable when it’s cured. That’s why support materials are laid down at the same time as the main polymer part, which enhances its dimensional accuracy and provides a sort of frame for the photopolymer to be held in until it’s cured. These support materials resemble a slightly rigid gel-like substance encasing the part by the end of the process. When the part is finished, it’s washed with a water jet and, soaked in a chemical solution to remove the supports, then left to dry. The following is an image of a Xometry rainbow logo made with PolyJet printing:
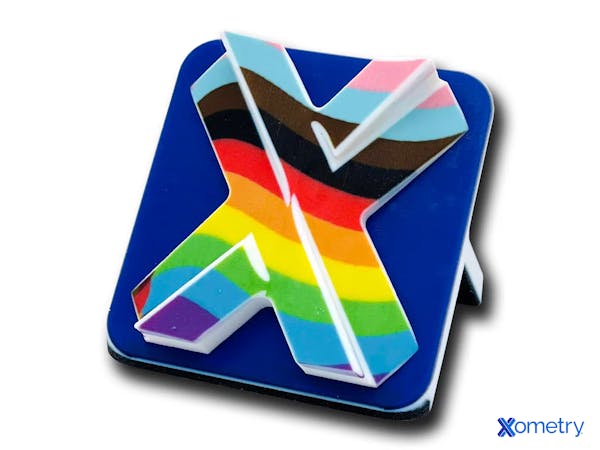
PolyJet is a method that allows you to print using various materials in one job, and parts will usually maintain their material properties after being post-processed. Materials of different properties can even be mixed simultaneously to simulate different material properties, such as mixing different ratios of rubber-like with rigid photopolymers to create pieces with different durometer ranges. The downsides to using this technique, though, are that the parts tend to be very fragile and fine features can easily be broken during or after post-processing. We do not recommend using PolyJet for end-use parts. The printing and post-processing can also take longer compared with MJP, which can affect overall cost. Learn more about PolyJet 3D printing in our dedicated article.
What is MultiJet 3D Printing?
MultiJet’s creation is attributed to the company 3D Systems, and it’s another type of 3D printing that works kind of like an inkjet printer. Like the first method we discussed, MJP uses a printing head that creates parts layer by layer using either UV-curable photopolymer or casting wax droplets. It can also create layer thicknesses of as small as 16 microns, but compared to PolyJet, it has limited multi-material mixing capabilities, if any at all, depending on the machine. Support structures for this technique are made from paraffin wax, so when a part is finished, it’s put in an oven or placed into a warm mineral oil bath to melt the wax away. Post-processing MJP parts is generally easier than PolyJet printing, but care must be taken when melting the wax to prevent the heat from affecting the properties of the main build material.
The potential downsides of using MJP include the fact that you cannot produce intricate full-color components or mix a range of materials such as rubber-likes, rigid, and transparent materials simultaneously to simulate different material properties as you can with PolyJet printing. Also, MJP parts run the risk of their material properties changing during post-processing if proper procedures and care are not taken.
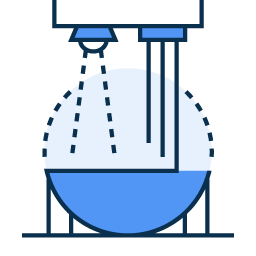
Frequently Asked Questions on PolyJet vs. MultiJet
How much do these machines cost?
As these are high-end machines meant for industrial settings, they do not come cheap. PolyJet printers can run anywhere between $150,000 and $500,000, and MJP machines are quite similar, typically ranging from $150,000 to $400,000. This is why services like those Xometry offers are useful, as you can take advantage of these high-end systems without the upfront investment setting up and running them entails.
Are there any alternatives to PolyJet and MJP?
Carbon DLS™ (Digital Light Synthesis™) is a comparable 3D printing method that also produces high-resolution and precise parts. Like PolyJet and MJP, DLS cures liquid photopolymers to build new parts, but it does so with projected light and a continuous liquid interface for production. In addition, DLS prints seamless parts continuously, upside down.
What’s the difference between PolyJet and SLA?
SLA (stereolithography) 3D printing uses a laser to cure liquid resin into solid parts. It’s good for making functional prototypes and parts, and, depending on the specific machine and setup, it could have even better resolution than PolyJet. SLA prints are high-quality and often made into molds and tooling, such as master patterns for casting applications.
What’s the difference between MJP and MJF?
Both methods seem similar even by the name, with MJF being an abbreviation for multi-jet fusion. “MJF is a process by which a fusing agent is applied to successive layers of powdered material,” Tsu-Raun tells us. “It is relatively fast and produces parts in production thermoplastics, but is less accurate than PolyJet." The method is also really good at making complex shapes and durable, end-use parts. One of the main differences is that MJF uses a polymer powder and a fusing system to produce parts, allowing it to work in popular engineering materials such as Nylon, TPU, and Polypropylene.
How Xometry Can Help
Xometry offers instant access to a variety of 3D printing technologies, including PolyJet, Multi-Jet Fusion, SLA, and more! Best of all, we offer instant quoting and feedback through the Xometry Instant Quoting Engine®, allowing you to quickly get high-quality 3D-printed parts in your hands.
Disclaimer
The content appearing on this webpage is for informational purposes only. Xometry makes no representation or warranty of any kind, be it expressed or implied, as to the accuracy, completeness, or validity of the information. Any performance parameters, geometric tolerances, specific design features, quality and types of materials, or processes should not be inferred to represent what will be delivered by third-party suppliers or manufacturers through Xometry’s network. Buyers seeking quotes for parts are responsible for defining the specific requirements for those parts. Please refer to our terms and conditions for more information.
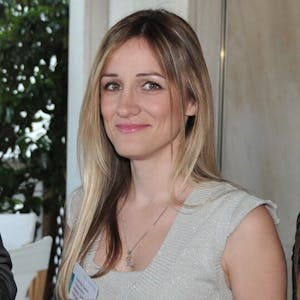