Juggling different 3D printing methods and determining which is right for the products you want to make isn’t easy. There are so many options, and it’s sometimes easiest to break it down by subcategory, whether by technology type or print attributes. That’s what we’re doing with SLS and DMLS printing. These two types of powder bed fusion methods work with different materials and don’t necessarily share the same benefits and disadvantages. Let’s get into it below.
What Is Selective Laser Sintering (SLS)?
SLS is a powder bed fusion technology that works with plastic powders and was originally developed in the mid-1980s. It’s often compared to other methods like FDM and, of course, DMLS. It uses one or two types of lasers, most usually a CO2 laser, to trace out the cross-section of a part and sinter the plastic particles together. Once every layer is formed, you have your final build. For a visual example, you can see a photo of one of our SLS machines at Xometry in action below.
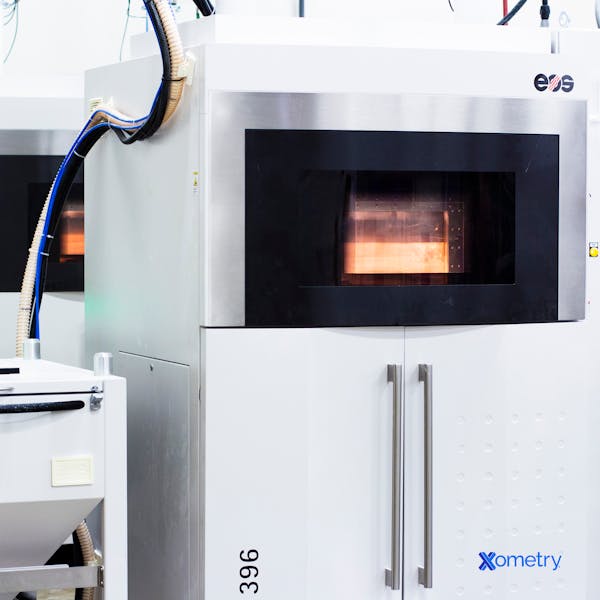
What Is Direct Metal Laser Sintering (DMLS)?
Like SLS, DMLS involves powder bed fusion tech and sintering, but it works with metals instead of plastics. It became a commercialized process back in 1995 and works by lasering metal powder particles together until every layer is complete. These printers also have a chamber that fills with inert gas to cut down on the possibility of combustion and oxidation. You can see a diagram showing the parts of a DMLS printer below.
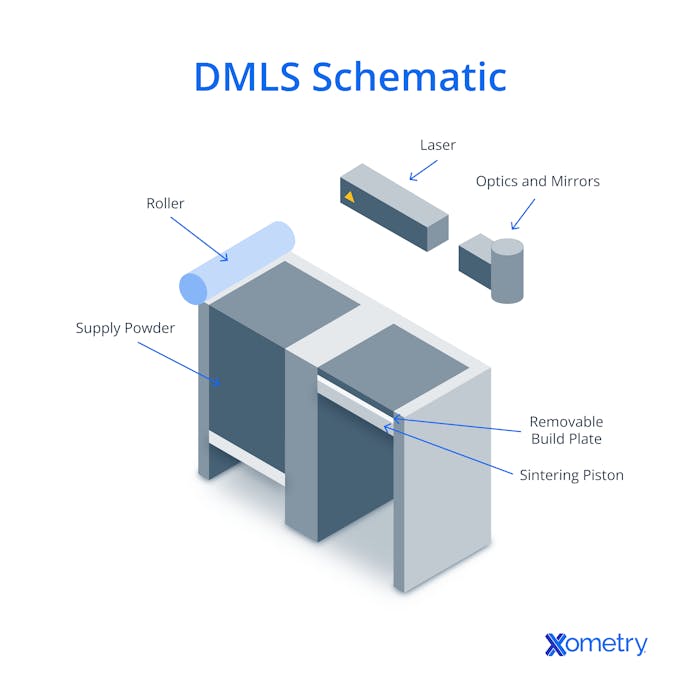
Attribute | SLS | DMLS |
---|---|---|
Attribute Typical layer height | SLS 100–120 microns | DMLS 30–40 microns |
Attribute Typical tolerance standards | SLS ± 0.015” or ± 0.002" per inch — whichever is greater* | DMLS +/- 0.005” for the first inch, plus +/- 0.002” for every inch that comes after |
Attribute Typical build volume | SLS 330 x 330 x 580 mm | DMLS 250 x 250 x 250 mm |
Attribute Minimum recommended feature size | SLS 1 mm | DMLS 0.5 mm |
Attribute Parts need support structures | SLS No | DMLS Yes |
Attribute Has isotropic material properties | SLS Yes | DMLS Yes |
Attribute Material types | SLS Thermoplastics like polyamides and nylons, metal, ceramic, and glass | DMLS Metals and alloys such as aluminum, copper, and stainless steel |
Attribute Print volume | SLS Can print builds around 2 feet in length | DMLS Smaller builds, around a 10-inch cube in size |
Attribute Can print in metal | SLS No | DMLS Yes |
Attribute Advantages | SLS
| DMLS
|
Attribute Disadvantages | SLS
| DMLS
|
* The tolerances we’ve listed for SLS are when working with nylon 12 material, but tolerances will differ depending on what material you choose for printing.
Alternative Methods
While SLS and DMLS have their fair share of perks, there are a couple of alternative printing options you can consider depending on the project you have in mind.
- Multi-jet fusion (MJF): This is also a type of powder-bed fusion process (and one that we offer, too). MJF is a good alternative for SLS because it works with similar polyamide materials but uses a printer head that deposits the materials more like an inkjet printer as opposed to the laser that SLS uses.
- Metal binder jetting: We also offer metal binder jetting, which also involves working with metal like DMLS. It also uses a print head to lay out a binding agent that fuses metal layers together, and then it’s left to cure and later sintered or infiltrated with bronze. It’s much cheaper than DMLS but has a higher chance of shrinkage and more pores (and often not as fine of features).
FAQs About SLS and DMLS
What are the costs for SLS and DMLS printing?
When you compare the prices of SLS and DMLS printing, you’ll find that DMLS is almost always more expensive than the former. This is because printing with metal powder is much more expensive than printing with other materials, like plastic.
How do the surface finishes compare between SLS and DMLS?
With both SLS and DMLS printing, you can expect pretty rough and matte surface finishes. DMLS tends to have a slightly smoother finish because of the finer layer height that the printer produces, but both will usually need post-processing done, whether through bead blasting, tumbling, or polishing.
How Xometry Can Help
You won’t be short of custom 3D printing options here at Xometry. Speak to our team for customized help or use our online quote generator to get pricing for metal 3D printing, carbon digital light synthesis, stereolithography, and more.
Disclaimer
The content appearing on this webpage is for informational purposes only. Xometry makes no representation or warranty of any kind, be it expressed or implied, as to the accuracy, completeness, or validity of the information. Any performance parameters, geometric tolerances, specific design features, quality and types of materials, or processes should not be inferred to represent what will be delivered by third-party suppliers or manufacturers through Xometry’s network. Buyers seeking quotes for parts are responsible for defining the specific requirements for those parts. Please refer to our terms and conditions for more information.
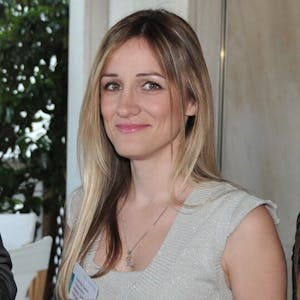