Best Practices for Prototyping in the Age of Advanced Manufacturing
The prototyping process isn’t just getting faster; it’s also getting more fractured. No one’s approach is the same anymore, and everyone’s looking for an edge. The tools to transform prototyping are available to the manufacturer willing to utilize them.
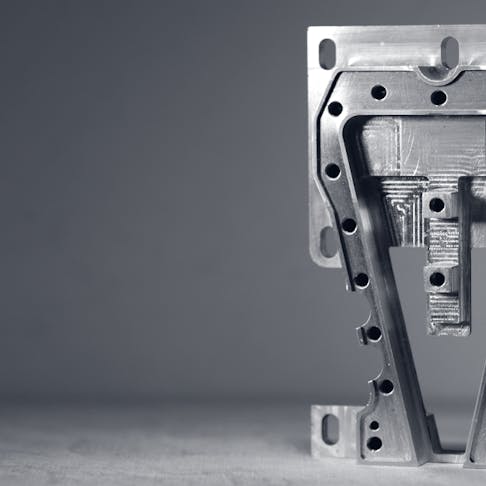
When the phrase, “advanced manufacturing,” first burst onto the scene a few years ago, few of us knew what to make of it. Did it apply literally to how things were made, like with CNC machining or 3D printing? Was it a reference to robotics and other trends affecting the changing factory floor like wearables and AR? Or did it mean the increasing amount of new-fangled, high-tech products manufacturers were making? The shift of business operations into the cloud? The coming Industrial Internet of Things?
The concern over a solid definition wasn’t a philosophical one. Like all things in the manufacturing business, shifting realities always result in shifting markets and profit margins. If manufacturing was advancing, we needed to figure out how to leverage that advance for competitive gain. Of course, leveraging what you don’t quite have a bead on isn’t easy.
Thankfully, the passage of time has a way of making things clear. Since we first began fretting over it, “advanced manufacturing” has ceased to be a buzzword and morphed convincingly into a game plan. Robots, cloud computing, wearables, Jetsons-like products, data mining and analytics, machine learning, IIoT, AR — it’s all advanced manufacturing. It’s all leverageable, and it’s all just getting warmed up.
Which brings us — believe it or not — to prototyping.
Prototyping: A New Odyssey in Space and Time
A lynchpin of any manufacturing endeavor, prototyping is at once a hallowed and a harried effort. A process as much as an end result, anyone who’s spent time designing, developing, engineering or otherwise signing-off on or overseeing the process knows yielding a working prototype is something that tends to go poorly before it goes well. In the age of advanced manufacturing, that truism continues to hold firm (for now), but the pace of the process and its methods have changed considerably.
Rapid prototyping and other tools have dramatically reduced the production timeline. 3D printing and online CNC machining services can iterate on designs in mere hours as opposed to weeks. Fast-paced logistics providers can deliver those iterations at something approaching the speed of sound. Simulations and models make it possible to forego early-stage, physical prototyping entirely, as manufacturing software, data analysis, and machine learning make it possible to work out bugs, kinks, and shady tolerances long before a real part sees the light of day.
As a result, the prototyping process isn’t just getting faster; it’s also getting more fractured. No one’s approach is the same anymore, and everyone’s looking for an edge. The skillsets of the people involved and the technologies on which they depend are in flux.
While prototyping has long included an element of chaos — creative work always does — the rapid rate of change that’s one of the hallmarks of advanced manufacturing has introduced a level of chaos that can be unnerving. Slow down, and you risk being beaten to market by a competitor. Keep pace, and you risk running off the rails.
It’s a dilemma that isn’t going anywhere, and manufacturers are employing different strategies to manage it. While vertical integration is making a comeback in some companies, most would be wise to partner with a company that excels at a new type of prototyping. From establishing order to extracting new value from a process that once seemed an end in itself, here’s a look at prototyping best practices in the age of advanced manufacturing.
If It's Gotta Be Fast, It Better Be Smart
The desire for more and more speed in prototyping is a given, but speed that comes with nothing beyond itself is too short-sighted in today’s manufacturing environment. Why just aim to get into production faster when you could get into production faster armed with data and insight?
Thanks to advanced manufacturing, the speed of your prototyping can be tempered and informed by the intelligence you gain. Through the cloud, digital iterations and revisions have meaning they’ve never had before. Fast prototyping should no longer be the goal. Smart prototyping should be.
But what, exactly, is that?
As big data and analytics finally come of age, they offer a chance to machine, design, manage and measure in a way that’s brand-new. Gone are the days of plodding notions of incremental improvement. Big data, because it isn’t bound by what humans can measure and imagine, can pave a path that reinvents your wheel by turning it into a jetpack.
Don’t settle for speed. Intelligent tools are a mainstay of advanced manufacturing, and the smarter your prototyping gets, the better everything else along your production lifecycle will be, too.
A Team is Only as Good as Its (Means of) Collaboration
Here in Kentucky Wildcat country — where one of Xometry’s 3 offices is located — we relish seeing stellar basketball players do stellar things, but it’s the moments of mind-blowing teamwork that really makes us swoon. While it’s true that pulling off a CNC machined or 3D printed prototype doesn’t have a lot in common with NCAA basketball, the level of collaboration required for success in both arenas is similar. Far too often, prototyping teams lack ready access to one another and relevant information when they most need it. Not only does this reality hamper decision-making; it also slows the process down unnecessarily.
For collaboration to excel, it’s not enough to resolve to do better. The means to do better must also be present. Getting that revised CAD file from Steve’s laptop isn’t that big of a deal until you add in the time it took to track down Jennifer’s signature on the P.O. and the time you and Ahmad spent hunting through your email for that thread about the next revision.
What’s needed is a collaboration tool tailored to manufacturers’ needs. By enabling the product, design and process team to keep all their files, notes, comments and revisions in a cloud-based and secure location, collaboration could be streamlined exponentially, saving time and bypassing the miscommunication that’s more common when communication is scattered among devices and services.
Aim to Manufacture a Great Production Process
It goes without saying that a prototype, whether you’re utilizing a 3D printer or an online CNC milling machine, is not the end goal of prototyping. The goal, of course, is to transition into production and crush your competition by getting your wildly innovative and desirable new product to market in record time.
Except almost every manufacturer approaches production as an entirely separate process from prototyping. While the reasons for doing so have historically had practical validity — a supplier suited to running high-precision prototypes is rarely the right supplier to churn out 100,000 units of your final design — the age of advanced manufacturing has rendered those reasons moot.
There are a couple reasons as to why.
First, when your prototyping process includes the collection and analysis of actionable data, you stand to benefit far beyond just ending up with a workable, quality prototype. While traditional prototyping must move first into bridge production in order to transition into mass production, data-fueled prototyping can skip the bridge and move straight into production. After all, the information necessary to successfully run production is digital. With enough of the right kind of data on your side, the muscle memory to CNC machine or 3D print parts at high quantities resides with the trail of information embedded in your part’s digital files — not in the machine or machinist.
Of course, being able to move right into production from prototyping can’t happen with just the free flow of data alone, and this reality brings us to our second reason advanced manufacturing has managed to make prototyping and production part of the same process: distributed manufacturing.
The flexibility and ubiquitous connections provided by the cloud have made it possible to have access to a wide variety of diverse suppliers. When a manufacturer has access to a distributed manufacturing base — especially one that’s already vetted — moving from a shop that specializes in prototyping to one that specializes in production is as easy as clicking a button online.
It’s time to advance. Employing best practices for prototyping that reflect our new and transforming technological reality is a must in today’s global and highly competitive environment. From leaning harder on data to making collaboration easier for your prototyping team, the tools to transform are available to the manufacturer willing to utilize them.
Find out more about how partnering with Xometry for prototyping can speed your path to production.
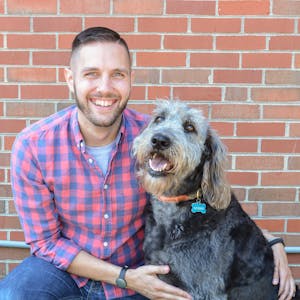