Melton Machine & Control Company (MMCC) is an industrial automation solution provider. The company plays a key role at the beginning of the value chain, building tools, fixtures, and machines to hold parts in place while they are being welded. These custom machines and fixtures are then integrated into their customer’s entire production ecosystem to mass-produce assemblies. These assemblies range from automotive exhaust to ride control components to heat exchangers to semi-truck axles.
The company’s bread and butter is the automotive industry where they work with Tier 1 suppliers to all the major automotive OEM’s. They provide machines and fixtures that allow their customers to weld the exhaust for the car you are probably driving today. Weston Miller, mechanical design engineer at MMCC, refers to the company as a “quiet giant,” saying, “there’s a good chance that almost any exhaust in America has touched MMCC equipment for at least one [manufacturing] process.”
Some of the machines they produce contain robots to perform the welding. These robots are programmed to aim a weld torch at the same point every time, which means if the parts move between the time the machine operator loads them in the fixtures, exits the machine, and presses the start button, the parts can end up with a defective weld. MMCC ensures their fixtures hold parts in the same spot every time so the robot can weld them at a 100% accuracy rate.
These fixtures use various types of sensors to see if a clamp is open or closed or if a part is present or missing. Since each customer’s machine is custom built to their production needs, the switches used in combination with the clamps may vary. For example, one of MMCC’s customers requires the use of an NPN switch, but the clamp’s standard is a PNP switch. MMCC came up with a robust solution of using two proximity switches outside of the clamp to indicate whether it is open or closed.
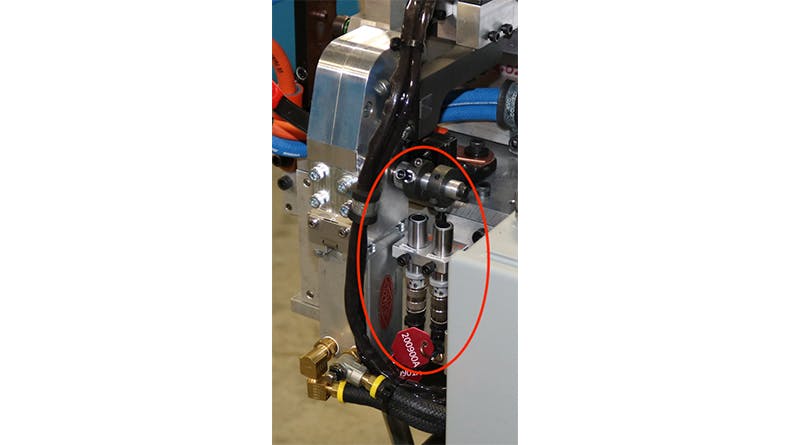
Clamp used with original switch mounting circled in red
However, since welding produces high temperatures and “spatter,” the new switch assembly experienced deviation and began to wear out. Miller needed to design a better, more durable solution. He would also need to source a switch with specific geometry so it could fit inside the specified clamp. Miller, who is well-trained in 3D Printing, chose SLS to print his switch housing since he knew SLS Nylon 12 would provide strong thermal properties and the ability to resolve tiny features. He got an instant quote from Xometry, consulted with project engineers about his project, and became a Xometry convert.
After receiving a first test batch, Miller found that his design had been successful. “You tell most people that you’re going to put a thermoplastic in a hot welding environment and they’ll laugh at you.” Miller predicted Nylon 12 could withstand the environmental conditions of its specific application, and it worked. He placed another, larger order to implement the switch housing solution at a wider scale.
So far, the switch housing is holding up well—ten customers across the US and Mexico have had no issues in the year since the solution has been deployed. The project signals a greater future to Miller as the first (and certainly not last) use of 3D printing implemented in an MMCC fixture.
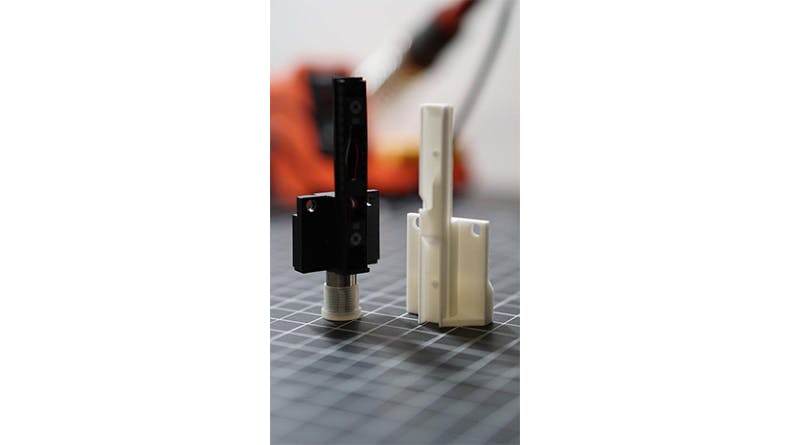
Left: Original switch housing. Right: SLS printed switch housing to be used as an end-use, fixture component.
Miller found the quality and shipping speed of the parts to be a key advantage to using Xometry. When a coworker needed a solution—he realized the ferrous metal used to mount his switches was causing false readings—he decided to try plastic. Since CNC Machining plastic production parts would take too long, he asked Miller how he could get his custom proximity mounts sooner. Miller recommended Xometry, and a week later the coworker received the parts.
After multiple successful experiences with Xometry’s SLS printing, the engineers at MMCC decided to put Xometry to the test for a very unique part. When MMCC Employee Owner Keith Straatmann, longtime mentor to Miller, announced his retirement, his department decided to surprise him with a miniature version of a machine and fixture he designed. The miniature machine is about 5 inches tall by 6 inches wide, with “Melton” printed in tiny letters across the top. The printed machine was mounted onto a plaque and proudly presented to Straatmann.
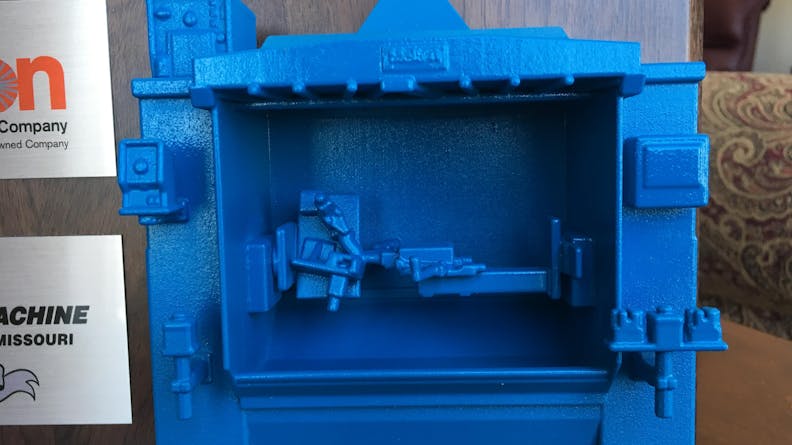
SLS 3D printed miniature machine
With Xometry’s SLS offering, Miller loves being able to concentrate on function instead of machinability when designing production pieces. While Miller can prototype using in-house FDM printers, he prefers to outsource final prototyping to Xometry using SLS. Since SLS uses a laser beam to sinter 3D powder, instead of building thicker layers via extrusion nozzle, Miller can design small fixture parts with thinner walls and increased geometric complexity.
Miller worked with other 3D printing bureaus before settling on Xometry, and deems Xometry’s service “top-notch.” He cites Xometry’s fast turnaround times, incredible prices, and customer service as major competitive advantages.
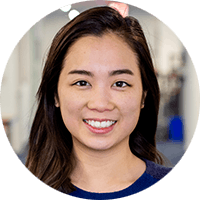