Case Study: Satellite Displays Builds On-the-go Live Captioning Badge with Xometry Injection Molding
Satellite Displays, a startup founded to ease communication barriers for deaf and hard-of-hearing individuals, used Xometry to build custom parts for a smart badge that live captions your speech in settings from hospitals to grocery stores.
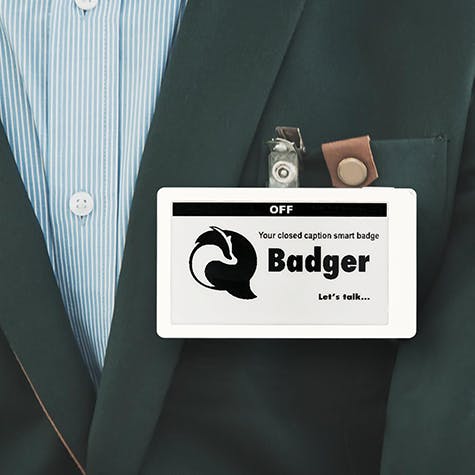
Industries | Manufacturing Services Utilized | Project Brief | Solution |
---|---|---|---|
Industries
| Manufacturing Services Utilized
| Project Brief Communication challenges for those who are deaf and hearing-impaired arose during the COVID-19 pandemic. Mike Williston and Peter Sprague theorized that a smart badge with multilingual speech-to-text capabilities could give any speaker instant closed captions, even while wearing a mask or despite other environmental impediments. They needed the right manufacturer to mold the company’s design without compromising on price or design. | Solution Via its diverse manufacturing network, Xometry found the right manufacturer to mold Satellite Displays’s five mating components. Xometry produced parts that hit a critical wall thickness to keep the device lightweight. Satellite Displays can now scale up production of the smart badge’s components with a Xometry mold at cost-effective per-unit pricing. |
Can a World Exist with Seamless Communication for All?
It’s a common story of late: with a global imperative to don face masks and prevent the spread of the novel coronavirus, some 455 million people worldwide who are deaf or hard of hearing have been left out of the conversation. From hospital settings to grocery stores, it’s become difficult for deaf people to communicate when opaque face coverings impede their ability to read lips and facial cues. Innovative products like ClearMask™ help mitigate this problem, but what happens when you don’t have a product like this on hand?
Long before the pandemic began, Mike Williston had considered this problem. Williston, as well as his grandmother, father, and sister, all have hearing loss, which puts them in dangerous situations such as being unable to understand medical operating procedures. Williston had witnessed deaf and hearing-impaired community members faced with inefficient and expensive solutions such as in-person, phone, or video interpreters or even sticky notes. Was there a communication device that could be used at all times to aid communication in medical settings and beyond? After gathering a team of engineers and software developers, Williston landed on a perfect solution: a closed caption smart badge.
Satellite Displays’s Smart Badge at Work
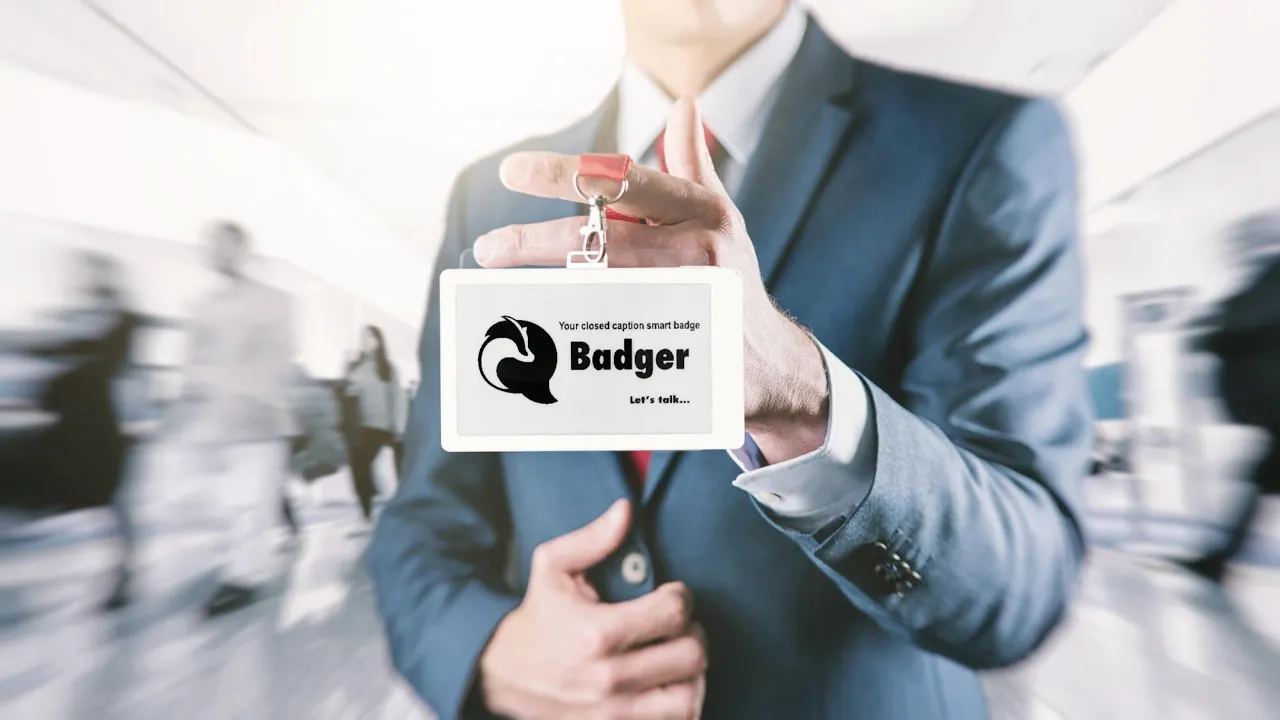
Building a Better Way for Masked Communication
The smart badge product, aptly named Badger by Satellite Displays, is a wearable device for seamless integration into everyday life; most professionals wear one as a part of their daily uniform. The badge is a source of communication away from the face, so others can read what you are saying with live closed captions. This circumvents the issue of muffled speech or facial expressions and lip movements that are covered by an opaque face mask.
Satellite Displays created a sophisticated device to satisfy several requirements. The ID badge continuously displays a person’s face to confirm the wearer’s identity and affiliation with an organization or at an event. The badges also incorporate RFID capabilities to allow a person’s safe entrance and passage via badge scanning. Williston and his team combined RFID technology with an efficient e-ink display that, even after 40 hours of speech translation, shows a person’s ID without battery power.
For the badge’s main technology, the company uses a superior speech-to-text phone application—similar to the likes of Alexa or Siri—combined with a microphone that can pinpoint and isolate the speaker’s voice from above. Badger uses Bluetooth to connect to your smartphone, transmitting speech to the phone app, and then receiving text back at high speed. To use the badge, users simply press a button or use a voice activation cue. Users can also use the phone app for easy software and firmware updates.
With the main badge technology designed and tested, the next step in getting the product to market was to find a manufacturing partner who could create ultra-thin and durable housing for maximum wearability.
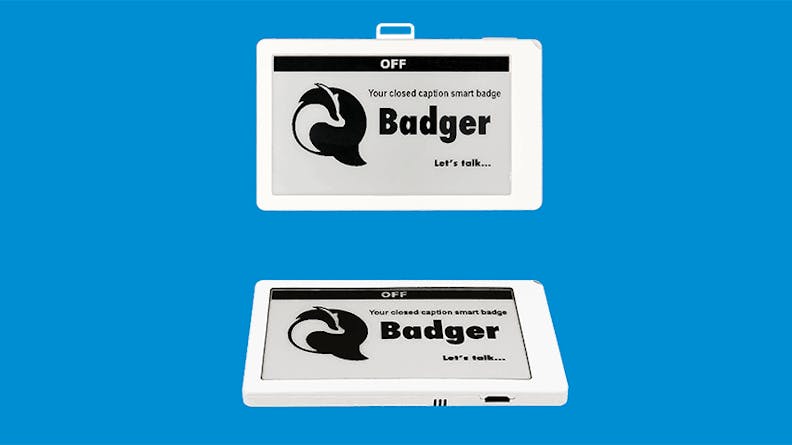
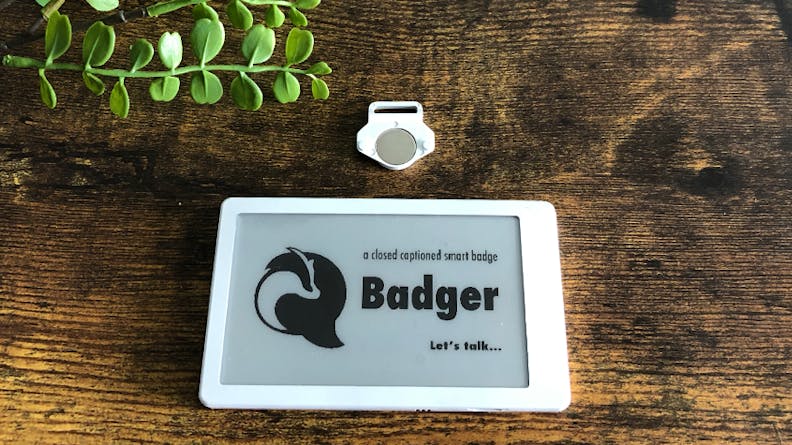
Satellite Displays’s badge housing created by Xometry
Manufacturing Considerations
Satellite Displays had a few major considerations at the manufacturing stage. The company needed its badges to come in at a maximum weight of 2 oz (57 g) or less to ensure user comfort. To do this, the five components of the badge’s housing and joining parts had to be as thin and lightweight as possible. The magical number for the team was 0.5 mm (0.020”) wall thickness—a task that every company except Xometry turned down. Lucas Taylor, the mechanical engineer for Satellite Displays, said, “Our project with Xometry had some very challenging parts for any molder, and they got it done without requiring us to compromise the design intent. Other rapid tooling shops seem to only accept the very simplest part geometries.”
At this size, the case pushed the boundaries of what even industrial 3D printing could do since the parts had various small mating features. However, Xometry found within its huge Manufacturing Supplier Network an overseas manufacturer who could guarantee the parts at the right dimensions for the right price. “I didn’t have the connection to the right manufacturer and Xometry gave us that connection,” says Williston.
Before scaling up, the team needed to validate the fit and function of the product with a prototype. They desired greater confidence in the parts before making the investment in an injection mold tool. Since Xometry offers eight types of 3D printing, the Xometry team recommended high-resolution stereolithography for the prototype. The SLA prototype was printed and shipped out within a week, and the team gained the confidence they needed to move ahead with a steel injection mold.
Xometry’s Injection Molding Solution for Satellite Displays
At the molding stage, Xometry’s molding supplier was able to adapt the mold to accommodate a novel friction pin closure system in the badge design. “One of the manufacturing challenges was making the clamshell housing optimized for manufacturing, assembly, and industrial design. We wanted iPhone looks on a startup budget and there were a hundred ways for our strategy to fail. Xometry worked with us to make the first run parts with steel-safe features so that we could fine-tune the fit after the tooling was made. In the end, we achieved an excellent final result that checked all of our boxes on our critical-to-quality metrics. I have worked with many molders, and I can say that Xometry deftly handled our technical challenges,” said Taylor.
Once the T1 samples from the mold tool were approved, Xometry manufactured five connecting components out of ABS with finishes ranging from an SPI-A1 to SPI-D3. These components are sleek yet protective of the advanced internal components. The final assembly allows users to press a button at the top to cue the live speech captioning. You can also say, “Hey Badger, caption, ...” then sit back and chat with your patient, client, colleague, or friend in over 50 languages.
Xometry’s On Demand Manufacturing Service
Badger, Satellite Displays’s inaugural product, is a symbol of the progress we’ve made as a society. In bringing static ID badges to life, Badger enables almost 455 million deaf and hearing-impaired people worldwide to access their basic right to clear communication. These badges allow people across all languages and backgrounds to connect without distractions and without confusion. The smart speech-to-text badges can be subsidized by government healthcare benefits and have the potential to revolutionize not only the medical industry, but corporate businesses, conferences, and even grocery stores.
As the product scales up and finds its market hooks, Williston and the team at Satellite Displays believe that without Xometry’s on-demand manufacturing solutions, their technology would not have achieved a successful market launch. “Xometry’s hardware enables crucial wearable functionality. Products like these are all about usability and comfort,” says Williston. He adds that working with Xometry was easy and comfortable. “From your salesperson to the engineering team, you guys felt like a part of our team. You felt like family.”
Xometry continuously strives to support the development of medical devices and electronic products that serve individuals of all abilities and applications of all types. To get started, get an instant quote by uploading a CAD file to the Xometry Instant Quoting Engine℠.
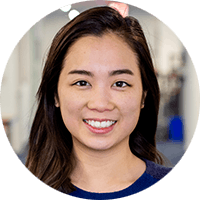