Ceramic mold casting is a production method that uses expendable molds to create precise metal parts. The mold’s ability to support intricate patterns and designs makes it good for everything from home foundry castings to complex industrial components. The process of ceramic mold casting starts by applying ceramic slurry to a mold pattern and allowing it to dry into a mold. Ceramic mold casting's distinctive advantages lie in its ability to handle high-temperature pours, intricate and creative designs, and mass production. The resulting parts need little or no extra finishing, so it’s a good choice for alloys that are hard to machine. However, it is important to note that the ceramic mold itself is destroyed upon removal of the metal part.
This article discusses ceramic mold casting, its definition, historical importance, working process, wide-ranging applications, and the myriad advantages it offers to different sectors.
What Is Ceramic Mold Casting?
Ceramic mold casting is a versatile casting process that finds applications in both simple foundry casting and intricate industrial castings. This manufacturing process is used to create tools and parts with fine details and high dimensional accuracy. It employs ceramic materials to form molds for casting end-use items (mainly metal casting processes). The ceramic molds themselves are expendable, so they must be recreated each time with the help of reusable and cost-effective patterns made from materials such as metals, plastic, wood, or rubber.
What Is the Origin of Ceramic Mold Casting?
The origin of Ceramic molding can be traced to the time when humans first discovered that fire was useful. At some point, they learned that the heat causes clay to harden. The resulting items were the first ceramics. Ceramics have been employed for millennia, and evidence suggests that even the Neanderthals utilized them. The combination of clay and fire allowed ancient civilizations to create functional items and intricate works of art. Over time, pottery-making evolved, and the use of ceramics extended beyond simple vessels to encompass more sophisticated applications such as ceramic mold casting.
Ceramic molding and casting techniques got refined over centuries. Today, even with so many newer manufacturing techniques on offer, ceramic mold casting remains an essential manufacturing process. It delivers fine detail, smooth surfaces, and accurate dimensions to a host of products.
What Is the Other Term for Ceramic Mold Casting?
Ceramic mold casting can also be referred to as ceramic molding. The process is essentially a combination of investment mold casting and plaster mold casting.
What Is the Importance of Ceramic Mold Casting in Manufacturing?
Ceramic mold casting is important because it’s versatile and has advantages over many other manufacturing techniques. One key benefit is the ability to create intricate designs with fine details, ensuring precision in the final products. The process also yields smooth surface finishes. Moreover, even though the ceramic mold is discarded each time, the reuse of a single pattern makes its products almost endlessly reproducible — output is consistent even on a mass-production scale. Yet ceramic mold casting is also perfect for bespoke and customized production.
How Does Ceramic Mold Casting Work?
Ceramic mold casting is used to create intricate and detailed metal or alloy parts. It begins with the creation of a pattern shaped as an exact replica of the desired part. A ceramic slurry, a mixture of fine ceramic particles and liquid binder, is then applied to the pattern's surface to form a thin coating. The slurry solidifies, creating a ceramic shell or mold over the pattern. After eliminating volatiles through low-temperature heating, the mold gets fired in a high-temperature furnace to strengthen it. Molten metal is poured into the mold, taking the shape of the pattern. The material cools and solidifies within the mold. Once fully solidified, the ceramic shell is broken and removed to reveal the final cast item.
What Makes Ceramic Mold Casting Stand Out Among Other Types of Casting?
Ceramic mold casting stands out among other types of casting due to its ability to create intricate and complex designs with exceptional detail. The end products are very dimensionally accurate, meeting tight tolerances and specific design requirements.Another standout feature is the variety of metals, metal alloys, and other materials this process can support. Furthermore, ceramic mold casting accepts materials with great heat-resistance capabilities. The smooth surface finish obtained through the casting process adds to the overall aesthetics of the products and reduces the need for additional surface treatments.
What Is the Process of Ceramic Mold Casting?
The process of ceramic molding involves steps such as: refractory, binder, mixing, pattern, stripping, burnoff, baking, and lastly, casting. This process is further discussed below:
1. Apply and Solidify Ceramic Slurry on the Mold Pattern
The first step is to create a pattern of the desired item, typically made of rubber, wood, plastic, or metal. This pattern represents the final shape and design of the metal component to be cast. The pattern is dipped or otherwise coated with a ceramic slurry mixture. This slurry is made from ceramic materials like silica, zircon, or alumina mixed with a liquid binder to give it a paste-like consistency.
2. Remove the Dried Slurry to Create a Mold for the Desired Item
Once the ceramic slurry is applied, it is left to dry and solidify. As it dries, it forms a ceramic shell around the mold pattern. After drying, the solidified slurry becomes the mold for the desired item.
3. Eliminate Volatiles by Placing the Mold in a Low-Temperature Oven or Using a Flame Torch
Prepare the mold by eliminating any remaining volatiles or moisture. This is typically done by placing the mold in a low-temperature oven or using a flame torch. The heat helps to drive off any remaining moisture and ensures the mold is fully dried and ready for casting.
4. Harden the Mold in a High-Temperature Furnace
After the elimination of volatiles, the mold is further processed to achieve greater strength and stability. It is placed in a high-temperature furnace where it undergoes a firing process to harden the ceramic shell. This is typically done at a temperature of around 1000 °C. This hardening step is crucial to ensure that the mold can withstand the high temperatures of the casting process.
5. Pour the Desired Material, Such as Steel, Into the Mold
Once the ceramic mold is prepared, the two halves, known as the cope and drag sections, are joined together to create a complete mold for the metal casting. To enhance the mold's strength, fireclay material may be used to support both sections. In some cases, the ceramic mold is preheated before the molten metal is poured into it.
With the mold now properly prepared and hardened, the desired metal is melted and brought to a suitable pouring temperature. The molten material is then carefully poured into the ceramic mold. It is left to cool and solidify into its final shape within the mold. Note that the ceramic mold itself will be destroyed in order to remove the finished metal casting. As a result, a new mold must be prepared for each casting.
What Are the Types of Ceramic Mold Casting Processes?
Ceramic mold casting processes come in two varieties. The choice between them depends on your specific casting requirements, the material being used, and the level of intricacy in the final product. These two types are further discussed below:
1. Shaw Process
The Shaw process or ethyl silicate variation, first forms a consistent slurry by blending a liquid catalyst, graded refractory filler, and hydrolyzed ethyl silicate. This slurry is then poured into the pattern before being allowed to set. Subsequently, the mold is removed from the pattern and subjected to heating with a pressurized gas torch. Once cooled, the mold is assembled and then fired before the introduction of the molten metal. There are instances when the Shaw process is combined with the lost wax process to harness the advantages of both techniques.
2. True Ceramic Molding
True Ceramic Molding involves the initial bonding of refractory grain with ammonium or calcium phosphates. Ceramic molds are usually created using the dry pressing method. A clay mixture with a specified moisture percentage is pressed into dies using a pressure of around 1-10 tons per square inch. After being removed from these dies, the molds are ready to be baked in furnaces at temperatures ranging between 899°C and 1316 °C.
Is Ceramic Mold Casting Expendable?
Yes, ceramic mold casting generates expendable molds. The mold used to shape the molten metal is typically destroyed or consumed after the piece solidifies. This means you must create a new mold for each casting. The whole process of applying ceramic slurry and allowing it to set must be repeated.
What Are the Metals Used in Ceramic Mold Casting?
A range of metals can be cast in ceramic molds. Some common examples include:
1. Zinc Alloys
Zinc alloys, such as Zamak, are often used in ceramic mold casting due to their fluidity and dimensional stability. These alloys show up in small to medium-sized intricate castings such as automotive components, decorative hardware, and electrical connectors.
2. Copper
Copper is favored for its high thermal and electrical conductivity, making it suitable for electrical components, heat exchangers, and plumbing fittings. To learn more, check out our guide on the Physical Properties of Copper.
3. Titanium
Titanium and titanium alloys are used in ceramic mold casting for specialized applications that require high strength-to-weight ratios, corrosion resistance, and biocompatibility. Industries such as: aerospace, medical, and marine often use titanium castings for specific components.
4. Aluminum
Aluminum and its alloys are widely used in ceramic mold casting due to their low density, excellent machinability, and corrosion resistance. These alloys are common in automotive parts, aerospace applications, and consumer goods. To learn more, read our guide on Aluminum Characteristics.
5. Magnesium
Magnesium alloys are used in ceramic mold casting for applications that require strong but lightweight components. The automotive and aerospace industries are some of the key users of magnesium castings.
Can Steel be Used as a Casting Metal for Ceramic Mold Casting?
Yes, steel can be cast in ceramic molds. Ceramic mold casting offers several advantages for casting steel. The process allows for the creation of detailed patterns and molds with accurate dimensional tolerances and smooth surface finishes. Additionally, the ceramic mold casting process provides better control over the cooling rate than most steel production methods. It can result in minimal internal stresses and better mechanical properties in the final metal structure.
However, it is worth noting that steel is harder to cast in ceramic molds than other metals like zinc or copper. Steel requires higher pouring temperatures and longer solidification times, which may necessitate specialized equipment and expertise. To learn more, check out our guide on Steel Metals.
Can Silicone Molds be Used for Ceramic Mold Casting?
No, silicone cannot be used in the ceramic molding process. Silicone cannot tolerate the sorts of temperatures demanded by molten metal. The extreme heat can cause the silicone to degrade, melt, or release harmful fumes, making it unsuitable for these metal casting processes.
What Are the Applications of Ceramic Mold Casting?
Ceramic mold casting finds wide use across various industries. Among its common applications is the production of kitchenware and tableware items in the form of pots and pansIn the industrial sector, ceramic mold casting is instrumental in crafting components such as impellers, gears, valves, and cutting tools. Moreover, the versatility of ceramic mold casting extends to art and decorative objects, where its results can be seen in captivating sculptures, art pieces, and other decorative items. It is also used to make jewelry such as: rings, pendants, earrings, and brooches.
What Industries Use Ceramic Mold Casting Products?
Some of the industries that utilize ceramic mold casting products include:
- Industrial Equipment: Manufacturers of pumps, valves, gears, and other industrial equipment benefit from ceramic mold casting's ability to produce precise and durable components.
- Jewelry: The process gets used to craft intricate and detailed jewelry pieces, including rings, pendants, earrings, and brooches.
- Art and Sculpture: Intricate designs and complex shapes are easy to reproduce across many iterations of an artistic design.
- Consumer Goods: Kitchenware and tableware items such as pots and pans may receive unique designs and decorative elements that would be hard to achieve any other way.
What Is the Quality of Ceramic Mold Casting Products?
As with any manufacturing process, the quality of ceramic mold casting products can be influenced by factors such as: the expertise of the casting team, the quality of materials used, the design of the mold, and the control of process parameters. To ensure consistent and high-quality results, you need skilled craftsmanship and effective process control throughout the ceramic mold casting process.
Are the Ceramic Mold Casting Products Heat Resistant?
It depends. The heat resistance of the ceramic mold casting product depends on the specific metal used. The ceramic mold casting materials, however, are known for their heat resistance properties. The ceramic materials used in the casting process can withstand high temperatures without losing their structural integrity or shape.
What Is the Accuracy of Ceramic Mold Casting?
Similar to plaster mold casting, ceramic mold casting gives you great dimensional accuracy with tolerances between 0.002 and 0.10 inches. The process is also capable of producing parts with thin sections and excellent surface finishes, eliminating the need for post-processing steps.
What Is the Lifespan of Ceramic Mold Casting Products?
The lifespan of ceramic mold casting products can vary depending on several factors, including the material, the design complexity, the application, and the operating conditions. Generally, ceramic mold casting products are known for their durability.
Products such as decorative items, art pieces, and jewelry — things that are not subjected to heavy wear and tear — can survive for decades or even centuries with proper care. On the other hand, the lifespans of industrial tools and components that are subjected to harsh operating conditions may be shorter, especially if the products experience high levels of stress, abrasion, or corrosion.
What Are the Advantages of Ceramic Mold Casting?
Ceramic mold casting can become a manufacturer’s top choice for several reasons. Some of the key advantages include:
- The process can produce items with intricate and complex designs with high dimensional accuracy.
- Cast parts have smooth surface finishes, reducing the need for post-casting machining or finishing.
- It can be used with a range of metals and alloys, including zinc, copper, aluminum, titanium, and more.
- The ceramic mold material itself helps reduce porosity in the cast metal, giving it better mechanical properties and overall performance.
- This method can accommodate high-temperature alloys like steel.
- Since the mold is destroyed, there’s typically no need for careful draft angles.
- Ceramic mold casting offers versatility in design.
What Are the Disadvantages of Ceramic Mold Casting?
Despite its many advantages, ceramic mold casting also comes with some disadvantages:
- The size and weight of castings have distinct limitations. Large and heavy castings may not be feasible due to the fragility and handling constraints of ceramic molds.
- It can be a time-consuming process, especially for complex designs.
- The initial setup cost for creating ceramic molds can be higher than for other casting methods.
- Molds can be fragile, and they’re likely to break if mishandled or stored improperly.
- Although ceramic mold casting allows for intricate designs, certain highly complex shapes and geometries may not be achievable.
- While ceramic molds are suitable for small- to medium-sized production runs, they may not be the best choice for high-volume production due to long lead times and cost considerations.
- Ceramic molds are expendable.
How Much Does Ceramic Mold Casting Cost?
The cost per ceramic mold can range anywhere from about $7 to several thousand dollars. It can vary significantly depending on: the size and complexity of the part, the type of material being used, the number of parts being produced, and the specific requirements of the casting process. Ceramic mold casting tends to be more expensive than some other casting methods due to its labor-intensive nature and the need to create individual ceramic molds for each part.
Is Ceramic Mold Casting More Expensive Than Die Casting?
The cost comparison between ceramic mold casting and die casting can vary depending on several factors such as: the complexity of the part, production volume, and the specific materials involved. In general, die casting is considered more cost-effective for high-volume production runs due to its production speed and repeatability. Steel dies are difficult and expensive to create, but they’re only made once. That’s advantageous for mass-production efforts.
On the other hand, ceramic mold casting can be more suitable for lower production volumes or for parts with complex designs that cannot easily be die-cast. Ceramic molds are more labor-intensive because they must be recreated each time. If the production run is limited, though, it may be more worthwhile to repeatedly create molds than to make steel dies.
To learn more, check out our guide on What is Die Casting.
What Is the Difference Between Ceramic Mold Casting and Investment Casting?
Ceramic mold casting and investment casting are two distinct processes used in the manufacture of intricate metal components. Ceramic mold casting uses a mold made from a mixture of ceramic materials like clay, silica, and alumina. This mold material is applied to reusable and cost-effective patterns made of rubber, wood, plastic, or metal. The process is capable of producing components with good surface finishes and intricate details.
On the other hand, the investment casting process starts with a wax pattern which is coated with a ceramic slurry to create a ceramic shell. The wax is then melted out, leaving a cavity in the ceramic shell which is later filled with molten metal. Investment casting is renowned for its ability to produce complex and detailed components. It is ideal for aerospace, automotive, medical, and other industries where precision and intricate details are critical.
What Is the Difference Between Ceramic Mold Casting and Plaster Mold Casting?
Ceramic mold casting and plaster mold casting are very similar processes. The main difference is that ceramic mold casting is able to cast materials at much higher temperatures. Besides this, the obvious difference between the two processes, as their names suggest, is that plaster molding makes use of plaster as a molding material for metal casting whereas ceramic molding makes use of refractory ceramics.
Summary
This article presented ceramic mold casting, explained it, and discussed how it works and its various applications. To learn more about ceramic mold casting, contact a Xometry representative.
Xometry provides a wide range of manufacturing capabilities, including casting and other value-added services for all of your prototyping and production needs. Visit our website to learn more or to request a free, no-obligation quote.
Disclaimer
The content appearing on this webpage is for informational purposes only. Xometry makes no representation or warranty of any kind, be it expressed or implied, as to the accuracy, completeness, or validity of the information. Any performance parameters, geometric tolerances, specific design features, quality and types of materials, or processes should not be inferred to represent what will be delivered by third-party suppliers or manufacturers through Xometry’s network. Buyers seeking quotes for parts are responsible for defining the specific requirements for those parts. Please refer to our terms and conditions for more information.
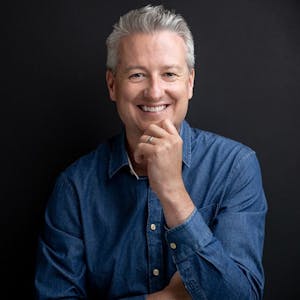