High-pressure casting is a method of production in which molten metal is injected into a two-part mold at high pressure and temperatures. The part produced by high-pressure casting is of high quality and strength when compared to other manufacturing methods. Due to the high repeatability and initial costs, high-pressure casting is used for large-scale production of high-quality parts including: engine blocks, car chassis, and airframe parts.
This article discusses the step-by-step process of high-pressure casting, its applications, how it compares to other manufacturing methods, and what characteristics the process imparts to the products it makes.
What Is High-Pressure Casting?
High-pressure casting is a process in which molten metal is injected under high pressures and speeds into a die cast. High-pressure casting is used in the large-scale production of high-quality metal parts. Metals including aluminum, zinc, and magnesium are used in high-pressure casting to produce parts for the automotive, aerospace, and medical industries.
What Is the History of High-Pressure Casting?
The origins of high-pressure die casting come from the printing industry. In the mid-1800s, Sturges began the mixing of lead and tin which was poured into casts to create keys for printing machinery. Sturges was awarded a patent for the die-casting process, although others including Barr, Pelize, and Dusenbury all started die-casting around the same time. The practice soon spread to other industries. Post-1914, the process used zinc and aluminum alloys which are still used today. Most of the alloys used to this day were also used in die casting since the mid-1930s.
What Is the Importance of High-Pressure Casting in Manufacturing?
High-pressure casting is an important process in the industry as it can produce a high volume of light alloy parts with a high speed and efficiency. This results in low production costs over a large production run. This method of casting also produces parts with very small variability and excellent surface finish. All of these properties make high-pressure casting a great option for the manufacture of large-batch production runs.
How Does High-Pressure Casting Work?
High-pressure casting works by injecting molten metal into a two-part die-cast mold tool at high pressure and speed. The molten metal then solidifies and the die tool can be opened. The die cast has one stationary and one moving part which are both attached to the machine platens.
What Makes High-Pressure Casting Stand Out Among Other Types of Casting?
High-pressure casting stands out from other forms of casting, such as low-pressure casting and gravity casting, as it provides superior characteristics. High-pressure casting can create parts with finer tolerances, thinner walls, better surface finish, and with less-tapered walls. High-pressure casting can achieve all this while producing parts at a faster rate with an increased tool life. High-pressure casting can produce up to 500,000 parts per year with a single tool, whereas gravity casting may only produce around 50,000 parts a year with a tool only lasting 100,000 parts.
Is High-Pressure Casting Better Than Die Casting?
Yes, high-pressure casting is better than die casting, even though they are very similar processes. The main difference is that high-pressure die casting uses pressures of up to 10 tons to inject the mold, whereas regular die casting is gravity fed. High-pressure casting can create parts that are stronger, more thermally stable, and with finer tolerances. This is because high-pressure die casting can create a denser part through the control of injection flow patterns and fling rates. The drawback of high-pressure casting is the larger initial investment, and therefore it is only used for larger production runs.
What Is the Process of High-Pressure Casting?
The process of high-pressure casting involves mold preparation, injection, removal, and trimming. There can sometimes be additional steps which may include vacuum die casting, slow fill die casting, and semi-solid metal processing. However, they all follow the basic four steps listed below:
1. Prepare the Mold
Before casting, the mold must be cleaned of all impurities and then lubricated with a release agent. This achieves two things—it prevents impurities from contaminating the part and aids the removal of the part post-injection. Dust, grease, and other small particles can contaminate the mold surface in between uses, which will affect the surface finish of the product. So, the mold is cleaned before use. During casting, the casting material not only adheres to itself but also to the walls of the mold. So, the mold must be lubricated with a release agent to aid the removal of the part after casting.
2. Inject the Material
The two-part mold is then sealed together and injected with the molten metal. There are two ways in which this is achieved: hot chamber and cold chamber injection.
In the hot chamber method, the plunger chamber is submerged into the molten metal and then the plunger forces the molten metal into the die cavity. The hot chamber method is used for metals including: zinc, magnesium, and lead.
For the cold chamber method, molten metal is poured either by hand or machine into the injection chamber and then a plunger forces the metal into the die cavity. The plunger can be operated in either a horizontal or vertical position. The cold chamber method is suited for metals including: aluminum, brass, and magnesium.
Hot chamber injection is used for small and intricate parts as it is restricted by the size of the injection chamber submerged in the molten-metal furnace. Both processes happen within less than a second at pressures ranging from 1,500 to 25,000 psi. After the molten metal is injected, it is left to solidify for a short period.
3. Remove the Cavity
Once the part is solidified, the two-part cast can be opened and the part removed. Typically, actuated ejector pins are used to push the part out of the mold. The ejector pins are located in positions where they operate through the mold wall to make contact with the part.
4. Trim the Excess Material
The last step is to trim the part with a post-processing technique which can involve a saw and/or grinding. There is often excess material where the two parts of the die meet as well as where the metal is injected. The excess metal at the injection point is referred to as the spruce. The spruce can be cut off and remelted for use in another casting.
What Are the Metals Used To Cast in High-Pressure Casting?
There are many metals used in high-pressure casting. Three of the most common are listed and discussed below:
1. Magnesium
Magnesium is one of the lighter metals that is commonly used in high-pressure die casting. It is predominately cast using hot chamber casting, however, it can also be cast using the cold chamber method. Cast magnesium has a better surface finish than aluminum and can be used to create thinner walls than aluminum. It is also lighter than zinc. However, it is not as strong or corrosion-resistant as aluminum and is not as stiff or formable as zinc.
2. Zinc
Zinc is die cast using the hot chamber injection method. Zinc is usually chosen as a material due to its generally superior mechanical properties. It also results in a tool life ten times longer than aluminum. Zinc also has a lower melting point which increases the speed of production. One drawback is that zinc is far more prone to defects than magnesium and aluminum.
3. Aluminum
Aluminum, unlike magnesium, is produced using cold chamber injection. This results in a longer cycle time than magnesium. However, aluminum is cheaper than magnesium casting. Aluminum also has a higher strength-to-weight ratio and operating temperature than zinc. However, zinc has high corrosion resistance. For more information, see our guide on What Type of Metal is Aluminum.
Can Stainless Steel Be Used as a Casting Metal for High-Pressure Casting?
Yes, stainless steel can be used as a casting metal in high-pressure casting. Not only can it be used in high-pressure casting, but it may be desirable to do so. High-pressure casting offers more-accurate dimensions, better surface finish, thinner wall sections, and low cost when compared to other stainless steel casting methods. For more information, see our guide on Stainless Steel Material Properties.
What Is High-Pressure Die Casting Used For?
High-pressure die casting is used for large production runs of metal components. Examples of the parts produced by this method include: infusion pumps, airframes, jet engine thrust reversers, engine blocks, oil sumps, car crossbeams, gearbox casings, and engine mounts.
What Industries Use High-Pressure Casting Products?
Various industries use high-pressure die casting including: automotive, aerospace, and medical, with the automotive industry being the biggest user. The automotive industry uses high-pressure die casting for: chassis, bodywork, drive trains, engines, interiors, and wheels. The aeronautical industry uses high-pressure die casting for airframes and engine components. The medical industry uses the technique for surgical equipment including: forceps, scissors, and clamps as well as for x-ray equipment and even heat sinks for certain implants.
What Is the Quality of High-Pressure Casting Products?
High-pressure casting produces high-quality parts. Compared to other casting methods, high-pressure casting produces finer tolerances (+/-0.1 mm compared to gravity casting’s +/-0.4 mm) and a better surface finish (1.5 µm compared to gravity casting’s 10 µm). High-pressure casting also produces stronger and more durable parts than other casting methods.
Are the High-Pressure Casting Products Durable?
Yes, high-pressure casting products are highly durable. One of the main advantages of high-pressure die casting is that the process can create parts that are as thin as 1 mm while retaining high strength and durability.
Are the High-Pressure Casting Products Heat-Resistant?
No, high-pressure casting products are not heat resistant. One big disadvantage of high-pressure casting is that it creates porosity internally in the metal. This means that if the cast part is exposed to high temperatures then the surface is prone to blistering.
What Is the Accuracy of High-Pressure Casting?
High-pressure casting is very accurate with critical dimensional tolerances of +/-0.1 mm, which is very accurate compared to the +/-0.4 mm and +/-1 mm tolerances achieved by gravity and sand casting, respectively. This tolerance is also repeatable on up to 500,000 parts.
What Is the Life Span of High-Pressure Casting Products?
A mold tool used for high-pressure casting may have a lifespan of anywhere up to 500,000 parts. This is very high when compared to gravity and sand casting methods which can achieve a life span of 100,000 and 5,000 parts respectively.
What Are the Advantages of High-Pressure Casting?
One major advantage of using high-pressure casting is the high strength and durability of parts created by the process which is not possible with other casting processes. There are several other advantages of high-pressure casting as listed below:
- Fast production rates.
- Good surface finish and dimensional tolerances.
- Ability to create thin walls.
- Long-lasting tools.
- Ability to create complex geometry.
- Low cost for large-scale production.
What Are the Disadvantages of High-Pressure Casting?
By far, the biggest disadvantage of high-pressure die casting is the initial investment cost both for machine and tooling. This is definitely outweighed if the production is on a large enough scale. Some other drawbacks as listed below:
- The higher rate of air inclusions compared to low-pressure casting.
- Not suitable for metals with a high melting point.
- Size limitations.
- Long lead time for tools, stalling initial production.
- Creates porosity internally in the metal.
How Much Does High-Pressure Casting Cost?
High-pressure die casting tooling cost is much higher, but the price per part is much lower than other casting methods. For a sand casting method, the tooling may cost approximately $1,900, whereas a high-pressure tooling may cost approximately $27,000. However, sand-casting tooling may only last for 5,000 parts, and high-pressure tooling may last for 500,000 parts. Bringing the cost of tooling per part to $0.38 for sand casting tooling, and $0.05 for high-pressure tooling (using the theoretical, example figures given).
What Is the Alternative to High-Pressure Casting?
There are alternatives to high-pressure casting. However, none will exactly match all of the qualities of a high-pressure cast product. Alternatives include:
- Centrifugal Casting: Centrifugal casting spins a hollow body to create centrifugal pressure and is used for hollow tube production.
- Continuous Casting: Continuous casting is a method whereby molten metal is continually fed into a mold in which it cools and is then fed out the other end of the mold. It produces high-quality castings and is used for large-scale production but cannot create the same thin walls as high-pressure casting.
- Sand Casting: Sand casting uses silica sand as the mold tool, which is cheaper than high-pressure tooling but is also labor intensive and results in poor material strength.
- Low-Pressure Casting: Similar to high-pressure casting, low-pressure casting can create high-quality parts at an economical rate. However, it is not as good at producing thin walls and it cannot be used for stainless steel.
- Extrusion: Extrusion is the continuous forming of metal into a particular cross-section. Extrusion is good at creating complex cross-sections for a low cost. However, its limiting factor is its inability to create varying geometries perpendicular to its cross-section.
What Is the Difference Between High-Pressure Casting and Low-Pressure Casting?
High-pressure casting and low-pressure casting have more differences than just the pressure at which they are carried out. High-pressure casting is the more common practice—being used for 50% of all light metal casting, whereas low-pressure casting makes up 20% of all light metal casting. Low-pressure casting is carried out at low pressure and low injection speeds, for metals with low melting points. It is used for thicker materials with a minimum thickness of 3.0 mm. High-pressure casting occurs at high speed and is used for softer metals including zinc and aluminum. It can produce thinner wall sections below 0.4 mm and a high-quality surface finish. However, high-pressure casting has high investment and operating costs.
Summary
This article presented high-pressure casting, explained it, and discussed its various applications and advantages. To learn more about high-pressure casting, contact a Xometry representative.
Xometry provides a wide range of manufacturing capabilities, including casting and other value-added services for all of your prototyping and production needs. Visit our website to learn more or to request a free, no-obligation quote.
Disclaimer
The content appearing on this webpage is for informational purposes only. Xometry makes no representation or warranty of any kind, be it expressed or implied, as to the accuracy, completeness, or validity of the information. Any performance parameters, geometric tolerances, specific design features, quality and types of materials, or processes should not be inferred to represent what will be delivered by third-party suppliers or manufacturers through Xometry’s network. Buyers seeking quotes for parts are responsible for defining the specific requirements for those parts. Please refer to our terms and conditions for more information.
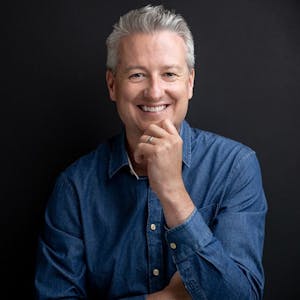