Casting is an ancient practice that’s managed to stick around in our lives for the last 7,000 years. As the saying goes, if it’s not broke, don’t fix it—and that can very much be applied to this popular manufacturing procedure today. Even after all these centuries, it’s hard to find a replacement for such a varied and customizable method for making products.
This is because casting involves adding molten metal to a cavity in the shape of your part. The net shape made with casting may only require light secondary processing. This has advantages over CNC machining where all the features require material removal from a larger metal billet. Also, nearly any metal can be used for casting which opens up an incredible diversity of applications and industries.
Casting can be broken up into several different processes, which we’ve briefly explained below. Each one is a form of casting, but they all involve slightly different materials, tools, machinery, and execution. Here are 14 techniques you can consider for your own parts.
Common Items in Casting
Regardless of the casting method, there are common factors that will help you navigate the processes below. These include:
- The Pattern or Master Pattern is a reusable or sacrificial shape of the final part used to form the cavity where the molten metal will pour. Most processes, such as sand casting and investment casting, require a pattern. The exception is when a tool or die is used.
- Die Tools are reusable metal portions common in processes like die casting. These are akin to the tooling that can be used in our injection molding services, only designed for liquid metal versus thermoplastic.
- Gates, sprues, and vents are channels where molten metal flows into the cavity. They may also be strategically placed where an air pocket would occur within a cavity. Adding exit holes in these locations will allow for the metal to fill that cavity and flow into the sprue, being trimmed after casting.
- Flash is the excess metal that seeps into the areas where a core, cavity, or die interacts. It can be ground off or trimmed after casting.
- Net shapes are the outcome of most casting processes due to the metal’s shrink rate and cavity surface. Critical surfaces, details like threaded holes, sealing surfaces, and tightly toleranced features are typically added via secondary machining.
Now, on to our types of casting!
1. Sand Casting
Sand might seem fragile and crumbly, but with the right type, it can form quality, single-use molds that allow you to create all kinds of castings. You’ll find that sand casting is mainly used for forming hot liquid metal or alloys into intricate objects. The molds are made of sand and are typically use multiple halves or cores. Sand molds look like impressions of parts from different angles, and when combined make the final shape of the part. Features are added to allow molten metal to be poured in as well as flow through the designs. It’s an enticing choice for manufacturers because you can shape alloys with high melting temperatures, like steel, nickel, and titanium, which often can’t be cast with other methods. Sand casting is not limited to high temperature metals, however, and can be applicable for softer alloys like aluminum, bronze, or zinc.
The sand used in sand casting is slightly different from the kind you’d find on the beach; it is made of silica (a popular casting sand), chemically bonded sand, or green sand. After casting, the mold may be reused or destroyed depending on the design created. The metal shape can then be post processed through grinding and machining to remove sprues, flashing, and add details or tightly toleranced features. You can use sand casting for all kinds of products at medium to high volumes, such as marine flywheels and engines, barbecue grills, skin fittings for ships, and jewelry.
To learn more, see our guide on Sand Casting Manufacturing.
A sand casting diagram is below:
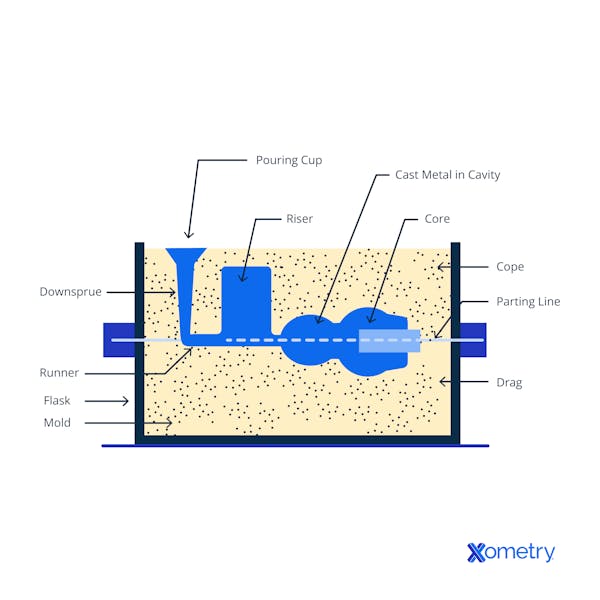
Sand casting diagram
2. Die Casting (Metal Die Casting)
While sand casting can melt alloys with high melting temperatures, you can look to die casting for forming metals that have lower melting points. Once you’ve turned your materials from solids to hot, molten liquids, you can inject them into long-life die-casting molds made of hardened steel. These tools consist of a cavity, core, and sometimes inserts. Unlike plastic injection molding, it is sometimes more feasible to machine side features after casting versus using a side action. Die casting traces back to the 19th century. Since its arrival on the manufacturing scene, there have been two types of procedures developed that you can use. The first is hot chamber, which features a built-in furnace within the machinery that melts the materials. If you use the cold chamber process, the second procedure, you’ll melt materials in a separate furnace and then move the molten material into the injection chamber afterward. You can implement die casting to make aerospace and automotive components in high quantity production, as well as toys, furniture, and electronics. Die casting is offered through Xometry’s core services and quotes can be created through the Instant Quoting Engine.
To learn more, see our guide on What is Die Casting Used For.
3. Investment Casting
We’re not talking about financial investments here, but rather the older term for the word that means covering up or putting on clothes. This is where investment casting gets its roots, harkening back to the Bronze Age, but it still remains a popular technique today if you want to make a wide range of products, including MRI machines, jewelry, and gas turbines. It’s a great choice, too, if you want to create near-identical copies at a large scale. Investment casting works by using wax patterns that are enveloped in ceramic. The ceramic takes on the surface and shape of the wax pattern (with added features for material or treeing). Afterward, they get pushed into a sand and slurry mix. At this point the wax has done its job and will be evaporated via heat, then molten metal is poured in to create the finished products. Like sand casting, investment casting can use a variety of materials. You can see how the process works in the image below.
In prototyping or low volumes, an investment pattern can be made using 3D printed wax or low-ash polymers. Low-ash is important because any remaining ash in the cavity may cause blemishes or defects on the cast component. In production, injection molding is used to rapidly create wax patterns that can be treed together to build multiple components at once. Like other metal casting processes, parts go through secondary trimming and finishing before completion.
To learn more, see our guide on What is Investment Casting.
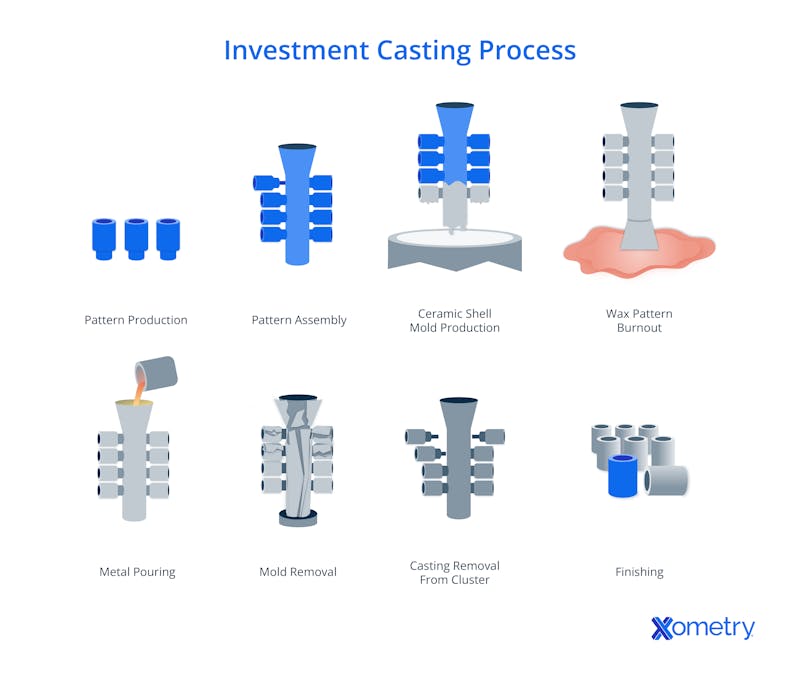
4. Gravity Die Casting
This process takes advantage of the physics law we experience every day. Gravity die casting has you coat a mold’s cavity, pour hot metal in, and wait for gravity to do its job, which is directing the material to flow in and down, and allowing it to cool and solidify. Whether manually or automatically done, this process takes a little bit longer than others, but you’ll find it’s relatively cheaper and ideal for creating smooth finishes. It’s a great choice if you want to manufacture small parts that work well in kitchenware, lighting, and automobiles. You can see how it works in the image below.
To learn more, check out our in-depth guide on Gravity Die Casting.
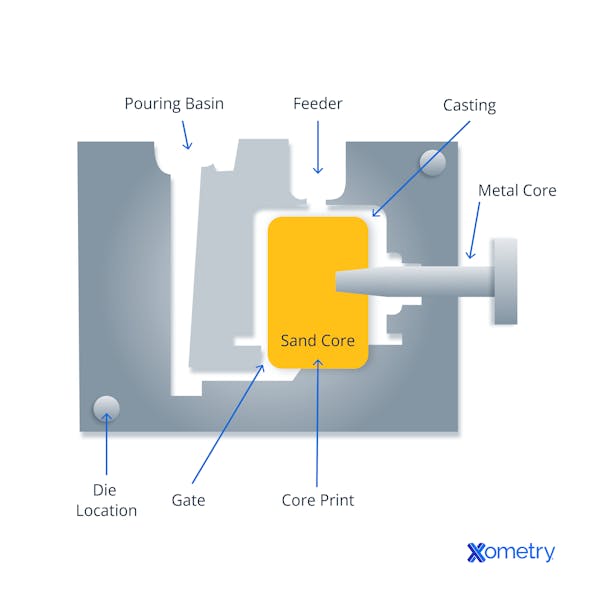
Gravity die casting diagram
5. Continuous Casting
This process gets its name from the steady flow of molten metal you’ll control going in and out of the molds and the continuous metal products it produces, like tubes, slabs, and bars. You can get high-quality shapes with this type of casting because of the quick cooling process and low risk of contaminants getting in. Like gravity die casting, you’ll notice that continuous casting also uses gravity to keep a steady flow of material coming. Continuous casting has a very high upfront cost and setup, making it ideal for producing high volumes of raw materials but not for any low volume applications.
6. Shell Molding
You know of sand casting, but we can keep the beach theme going with shell molding, which has some similarities to the former. Its name points to the process, which involves molding a silica sand and resin shell around a heated metal pattern. You can then remove the shell, and pour molten metal into the cavity. You might be curious why you’d choose this over sand molding, especially seeing that it’s more expensive in some instances. Shell molding can give you more accurate dimensions on products, nicer finishes, and larger quantities with less labor.
7. Lost-Foam Casting
Foam and molten metal don’t sound like they could mix, but this relatively newer process shows it’s possible to a certain extent. With lost-foam casting, you’ll inject molten metal into a foam mold that’s surrounded with support sand. The polystyrene foam will burn away and gas will disperse through the sand, leading to a cooled, formed shape. It’s a fantastic option if you need thin-walled products or items that are more intricately shaped. You’re not limited by industry, as this method works for creating all kinds of things like art sculptures, automotive parts, and circuit boards.
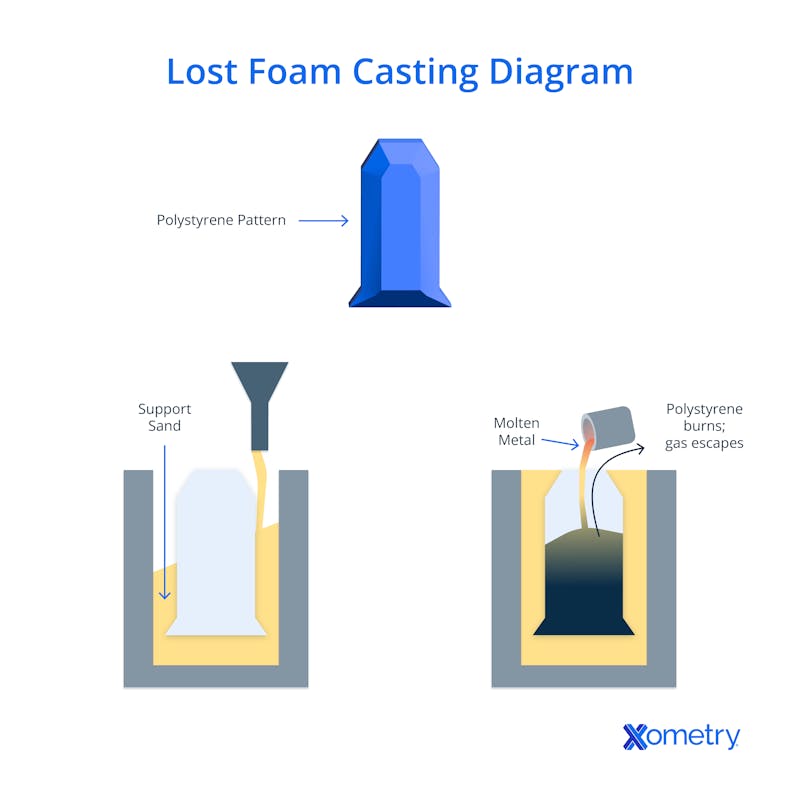
8. High Pressure Die Casting
This method makes the most of high pressure, speed, and heat, which makes it a suitable option for any industry you might be in. High pressure die casting funnels molten metal quickly into a mold under certain pressure and capacity settings, leading to a product that’s free of flaws, efficiently made, and easy to reproduce. You’ll need to be highly aware of getting the settings right on the machinery to ensure the shape fills and cools properly and turns out as you need it to. There are numerous applications you can use high pressure die casting for, from making toys to manufacturing parts for cars or appliances. High pressure die casting is a standard service at Xometry for metal production parts.
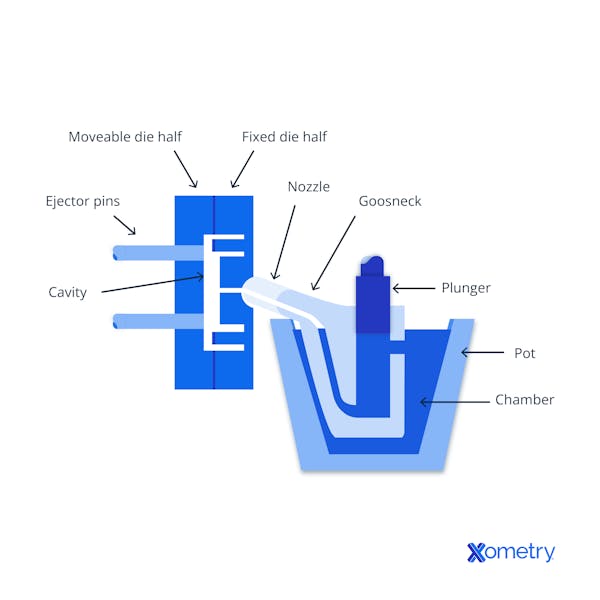
Pressure die casting schematic
9. Centrifugal Casting
You may also find centrifugal casting under the name of roto casting, and both are hints at what this process entails. This works by rotating a permanent mold and pouring molten material in at the same time, resulting in a cylindrical product (see below). All sorts of materials can be melted and poured into this shape, like glass, metal, and concrete, and it’s perfect for making large batches of standardized products in the same shape, such as pipes, flywheels, and cylinder liners.
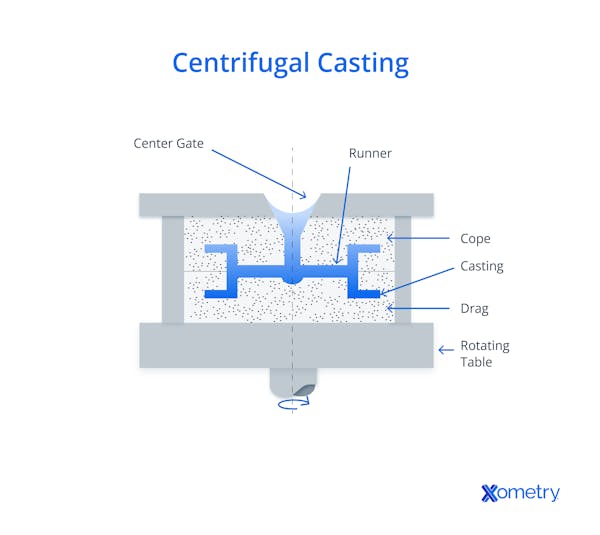
Centrifugal casting diagram
10. Permanent Mold Casting
There are casting processes fit for making low quantities of intricate shapes and processes built for basic shapes in high quantities, but what if you need an abundance of complex products? That’s where permanent mold casting comes in. With this method, you’ll use a clamped mold that allows for molten metal to shimmy in and harden. When you’re working in the aerospace or automotive industry and need precise products and lots of them with clean finishes and precise parts, this is the way to go. It’s more expensive than other options, but your choice of alternatives is limited.
To learn more, see our guide on Permanent Mold Casting.
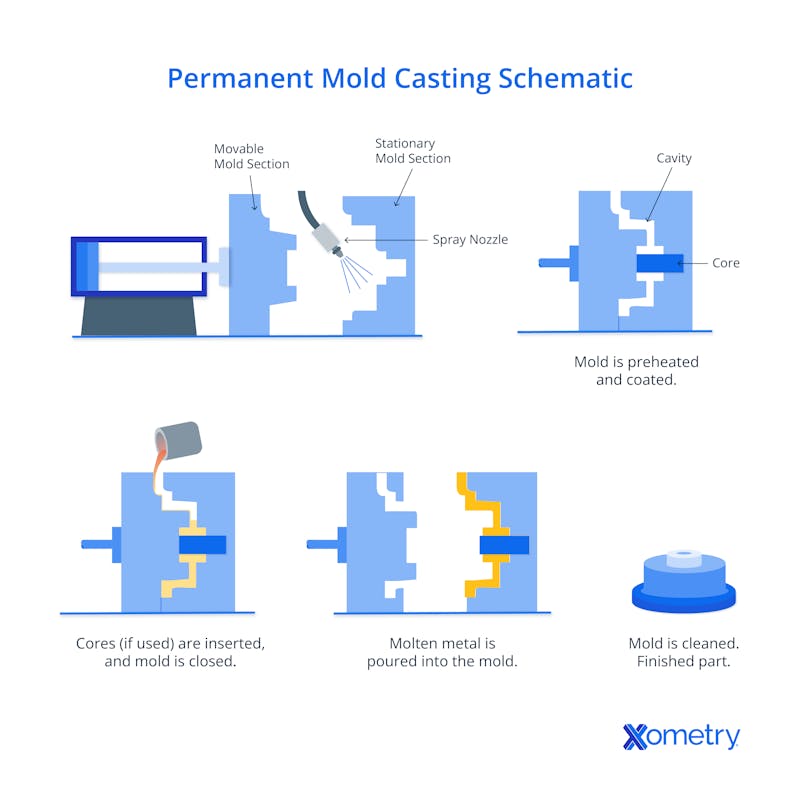
11. Vacuum Casting
Like other types of casting, vacuum casting uses super hot, molten materials and high pressure to create a hardened, finalized part or component. Where you’ll find it differs is where this all takes place, in a vacuum. It’s a fast way to make prototypes and complex parts if you only need a small quantity. The vacuum helps keep air, gas, and contaminants out of the silicone molds, leading to rubber and plastic parts that don’t have bubbles or large pores. This is not to be confused with urethane casting, which may use a vacuum to create polymer parts in silicone cavities.
See our guide on Vacuum Casting to learn more.
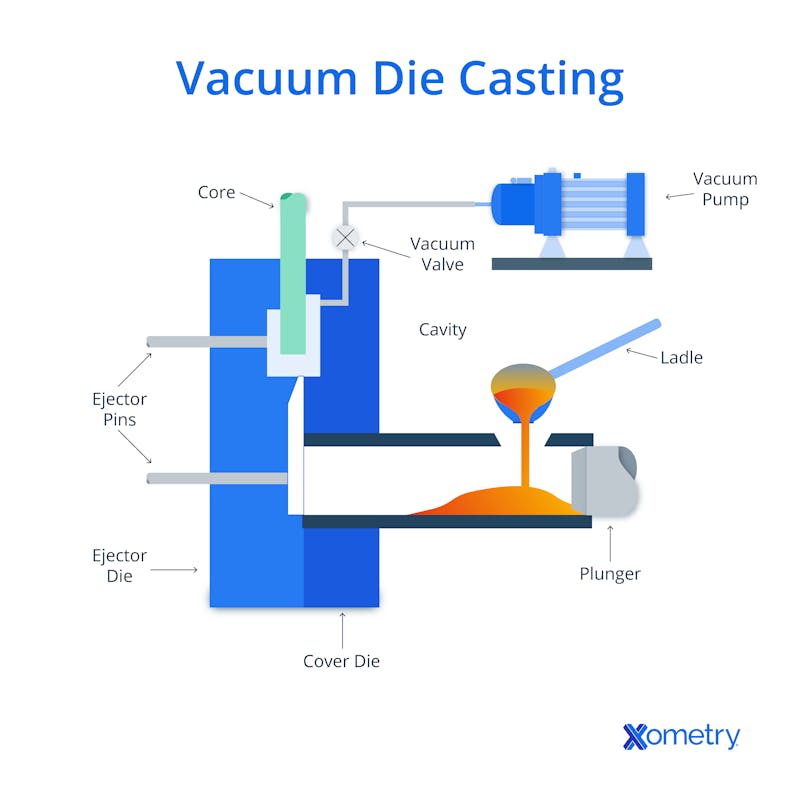
12. Low-Pressure Casting
In contrast to its high-pressure counterpart, in low-pressure casting you’ll use lower pressures to mold and cool molten metal. It’s great for creating stronger, more durable parts and because of the continuous flow of material, it maintains an accurate shape and even fill. If intricacy, smoothness, and sharp edges and contours are important to you, this could be a helpful option. Although if you need thin walls and quick product times, low-pressure casting might not be the best choice. That said, it’s still capable of producing many types of parts, whether you need kitchen pressure cookies, wheels, or cylinder heads.
13. Squeeze Die Casting
Squeezing, pressing, melting, and forging are a few of the functions that take place in the squeeze die casting process. If you’re looking to whip up pore-free, highly dense objects, this casting methodology shouldn’t be overlooked. There are two types, direct and indirect die casting, which feature pouring molten metal into molds that are then pressed between high-pressure hydraulic plates. Indirect works like high pressure die casting, funneling metal into molds under high pressure, whereas direct also includes pressing it under pressure. You can use squeeze die for automotive parts, aircraft components, architectural domes, and car wheels.
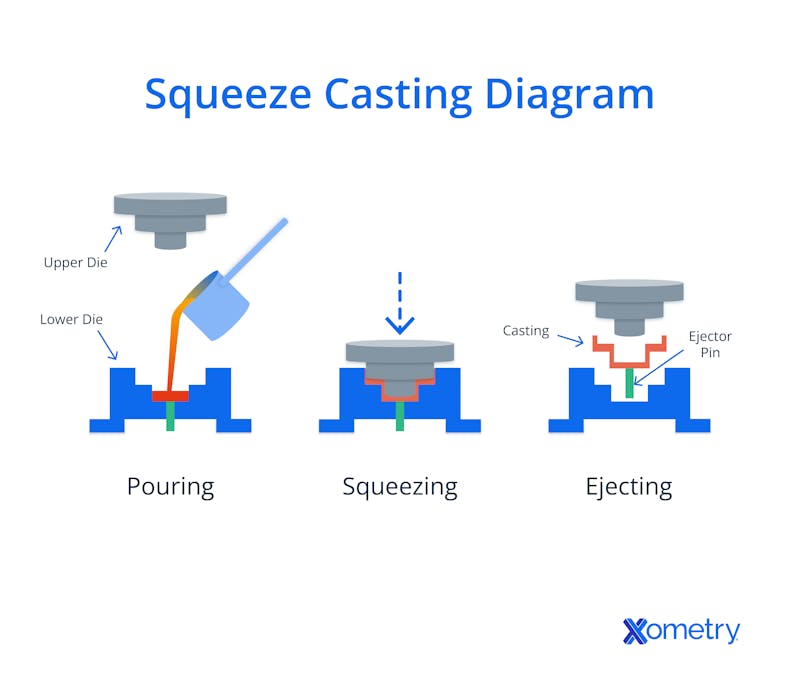
14. Plaster Casting
Another form of casting you can consider is one that sits under investment casting - plaster casting. Plaster casting may remind you of the Plaster of Paris molds kids use to create fake fossils or toys, and it’s made of the same thing, gypsum. At the manufacturing level, you can use this method to create prototypes, gears, ornaments, and valves. To plaster cast, you’ll coat a rubber or metal pattern with adhesive then pour in the materials that will set, cool, and be removed.
How Casting Works
Casting is a type of manufacturing process that forms materials into different shapes through hot materials and molds. Each casting process has its own unique steps and details that make it stand out from others, but in general, you’ll find that any type of casting involves the pouring or injecting of molten materials into a mold, which then cools and hardens into a finished product.
When it comes to producing intricate goods or large quantities of them, you’ll probably investigate casting as an option. It’s used across many different industries, whether you’re after extremely complex aerospace parts or basic toys.
Xometry Senior Solutions Engineer Jake Thompson says he helps clients choose the right type of casting process by asking the following questions: "1) What is the alloy? 2) What is your volume? 3) What is the part size? 4) Is there a tooling budget we need to stay under?"
Materials Used in Casting
It all depends on the type of casting you’re looking to do, but these are the most common materials you’ll use when it comes to these casting methods:
- Metals: Certain casting methods will be able to accommodate metals you want to melt, such as iron, aluminum, copper, and zinc.
- Alloys: Whether you use sand casting or metal die, all kinds of alloys like bronze and brass can be melted and molded.
- Ceramics: These materials are popular for pottery applications and can include clay or porcelain.
- Plastics: These bendable materials can be molded through casting, too.
- Composite materials: Resin and fiber mixtures and other composites are another suitable choice you can use in casting processes.
- Rubber: For parts with elasticity and flexibility, you can use rubber in casting.
- Glass: If you need artistic objects or thin-walled items, glass can be funneled into certain casting processes.
- Concrete: This is a common choice when you’re making architectural products and decorative castings.
Xometry offers the following metals for its die casting production services:
- Aluminum alloys: A360.0, A380.0, A383.0 (ADC12), and A413.0
- Zinc alloys: Zamak-2, Zamak-3
Summary
As you can see, casting isn’t limited to just one methodology or industry. With these 14 processes, you can cover a wide range of industries and make a series of precise, intricate products in a slew of materials.
Xometry provides a wide range of manufacturing capabilities, including casting and other value-added services for all of your prototyping and production needs. Get a free, no-obligation quote today.
Disclaimer
The content appearing on this webpage is for informational purposes only. Xometry makes no representation or warranty of any kind, be it expressed or implied, as to the accuracy, completeness, or validity of the information. Any performance parameters, geometric tolerances, specific design features, quality and types of materials, or processes should not be inferred to represent what will be delivered by third-party suppliers or manufacturers through Xometry’s network. Buyers seeking quotes for parts are responsible for defining the specific requirements for those parts. Please refer to our terms and conditions for more information.
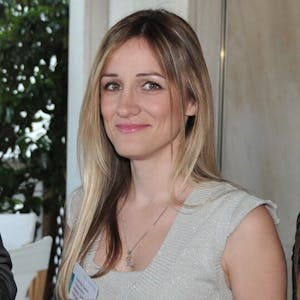