In this context, investment refers to the “putting on of clothes or coverings.” Literally, a sacrificial wax object is reproduced in metal by first investing it with a covering or ceramic and then burning out the wax to leave a perfect cavity in refractory material. Molten metal is then poured into the cavity and allowed to cool and solidify, reproducing the fine details of the original wax pattern.
Investment (or lost wax) casting is an ancient process. The story of lost wax metalworking is the story of Bronze Age technological innovation. In the modern world, investment casting still has a highly active place in jewelry making. More importantly, the process is used for precision net-shape production of otherwise near-impossible objects like complex and hollow turbine blades. The mass production of such parts is achieved by first CNC machining steel molds into which the wax can be rapidly cast. This enables a degree of repeatability that could not be achieved by individually hand-made masters. This article will further discuss investment casting, how it works, its advantages, and give some examples.
What Is Investment Casting?
Investment casting is a precision casting process used to create complex and intricate metal parts with high dimensional accuracy and fine surface finishes. This casting method is ideally suited to producing relatively high-quality components with intricate details, delicate features, and tight tolerances.
Investment casting is commonly used in industries such as: aerospace, automotive, jewelry, and medical devices, in which high precision and intricate designs are essential. It also produces castings with very tight tolerances and high dimensional accuracy. Investment castings typically have smooth and fine surface finishes. Investment casting can be used with a variety of materials, including various metals and alloys. It can also produce parts with complex shapes, internal cavities, and thin walls that are challenging for other casting methods.
How Investment Casting Differs From Other Types of Casting
All casting methods use a heat-resistant cavity that is the shape of the desired part as a volume to be filled with liquid metal, which is removed once solidified. The means by which the cavity is formed is the primary differentiator of casting methodologies. Die casting uses a two-part (or more) hardened-steel cavity tool that is expensively and precisely machined from billet material. Sand casting forms a cavity by packing sand with a binding agent around a reusable pattern or master of the part. Investment casting forms the cavity by drying and then kiln baking a skin of refractory material over a pattern or master that is sacrificial.
Precision and extent of detail differ greatly between casting methods. Die casting is high precision, although gravity (poured) die casting is less precise than the various forms of pressure die casting. Pressure die casting facilitates compensation for shrinkage, which retains/reflects the shape and dimensions of the cavity more faithfully in the cast part. Pressure die-cast parts can maintain very high levels of detail, so long as that detail can be extracted from the tool features. Sand casting is of moderate precision because the process does not lend itself to forming very accurate and repeatable cavities. It can maintain only relatively thick sections and coarse details. Investment casting is renowned for its combination of precision and fine detail while avoiding the major up-front costs of die casting.
To learn more, see our guide on Casting Methods.
Industries That Use Investment Casting
Investment casting is most used in industries in which precision, complexity, and fine details are crucial, and volumes are insufficient to justify the cost of die casting. The aerospace industry uses investment casting for the manufacture of high-complexity gas turbine components for gas flow such as turbine blades and fuel components. In automotive applications, it is used to manufacture components for low-volume and race vehicles, heavy goods/construction equipment, tractors, and agricultural machinery. In the medical sector, it is used to produce parts for MRI machines, wheelchairs, hospital beds, operating room equipment, and surgical tools.
The Basics of Investment Casting
Investment casting works by pre-applying coatings to the pattern—before investment casting mold creation, or to the mold—once it is fired. This serves several important purposes. Refractory coatings are applied to the interior surface of the mold to provide a barrier between the mold material and the molten metal. This reduces oxidation, contamination, and marking. An internal stucco layer in the mold can improve the release and texture of the surface to improve cosmetics by concealing slight flaws. Parting compounds applied to the mold surfaces ease the release of the casting at breakout.
Thermal barrier coatings applied selectively to the pattern can control the cooling rate and prevent rapid solidification. Anti-penetration coatings applied to the pattern can reduce the penetration of melt into the refractory material, to improve the quality of the surface finish.
Step-by-Step Process of Investment Casting
Listed and discussed below is the step-by-step process of investment casting:
1. Create and Assemble the Wax Patterns
There are three basic routes to delivering the precision wax patterns that are the starting point for investment casting. For decorative items and one-off products such as jewelry or technical items for which precision is a lower priority, it is common to hand carve the wax master to the desired dimensions/shape. This starts with either assembling preformed wax shapes to form the part or extracting the part from a solid block by cutting or melting locally. For mass-produced items that will be investment cast in relatively large volumes, it is generally preferred to build a steel tool that forms a wax casting cavity. A more recent development has been the ability to 3D print (rapid prototype) relatively small wax parts, to allow volume production without the cost of a wax casting tool. This is particularly useful in iterative development, allowing multiple generations of small changes to be trailed without huge cost.
2. Mount the Wax Patterns
Attach a feeder structure consisting of a sprue and channel to the part to allow the fill to be successful. Attach the part and feeder structure to a casting board that forms the structure to allow the flask (the completed cast tool) to stand securely. Any areas that are liable to vent poorly require air passage features to be added. Where multiple parts are to be cast in one pour, these structures are best established as individual cavities/galleries. Feed them from a single sprue/pour point. Care and experience are required to enable effective fill when the gallery structure or part geometry is more complex.
3. Make a Mold Shell
A first immersion in the correctly formulated slurry will coat the surfaces of the pattern/sprue/support structure. Once the assembly is coated, it can be withdrawn and allowed to drip. Once drained, apply a layer of stucco—dry powder sprinkled all over to stabilize the first layer. Repeat the dip/drain/stucco steps until sufficient thickness is developed all over. The rest/drying time between layers can be several hours, to allow sufficient drying and stabilization for each layer. Set aside to completely dry, giving this enough time for the coating to become firm and rigid.
4. Remove the Wax
Bake the completed and dried flask to remove the wax and fully integrate the refractory coating. The supplier-recommended temperatures and durations for this stage are dependent on the type of material such as: water glass, clay, and silica. At the end of this baking process, the mold or flask will be fully fused into a single, strong body. The wax will have been fully volatilized or burned off. The cavity or cavities, sprue, and galleries will be clear and open. The support structure of investment and braces will be able to support the structure, ready to fill.
5. Melt and Cast the Metal
Lift the crucible with tongs and pour the contents into the upper opening to the sprue. Fill/charging should continue until the entire structure is full. This is usually confirmed by the visible presence of molten metal in the upper vents, showing good flow through.
6. Finalize the Castings
When the cast has cooled, break away the refractory material without distorting the newly cast metal. In some cases, such as for simple and robust castings in stainless steel and bronze, this can be a vigorous and rapid process. Where more delicate features and softer metals such as gold and silver are present, much greater care must be taken.
The removal of cast material from sprue, vents, and supports will damage the desired casting. Any cosmetic damage can be repaired using die grinding, sawing, and clipping followed by surface restoration by sanding and polishing as required.
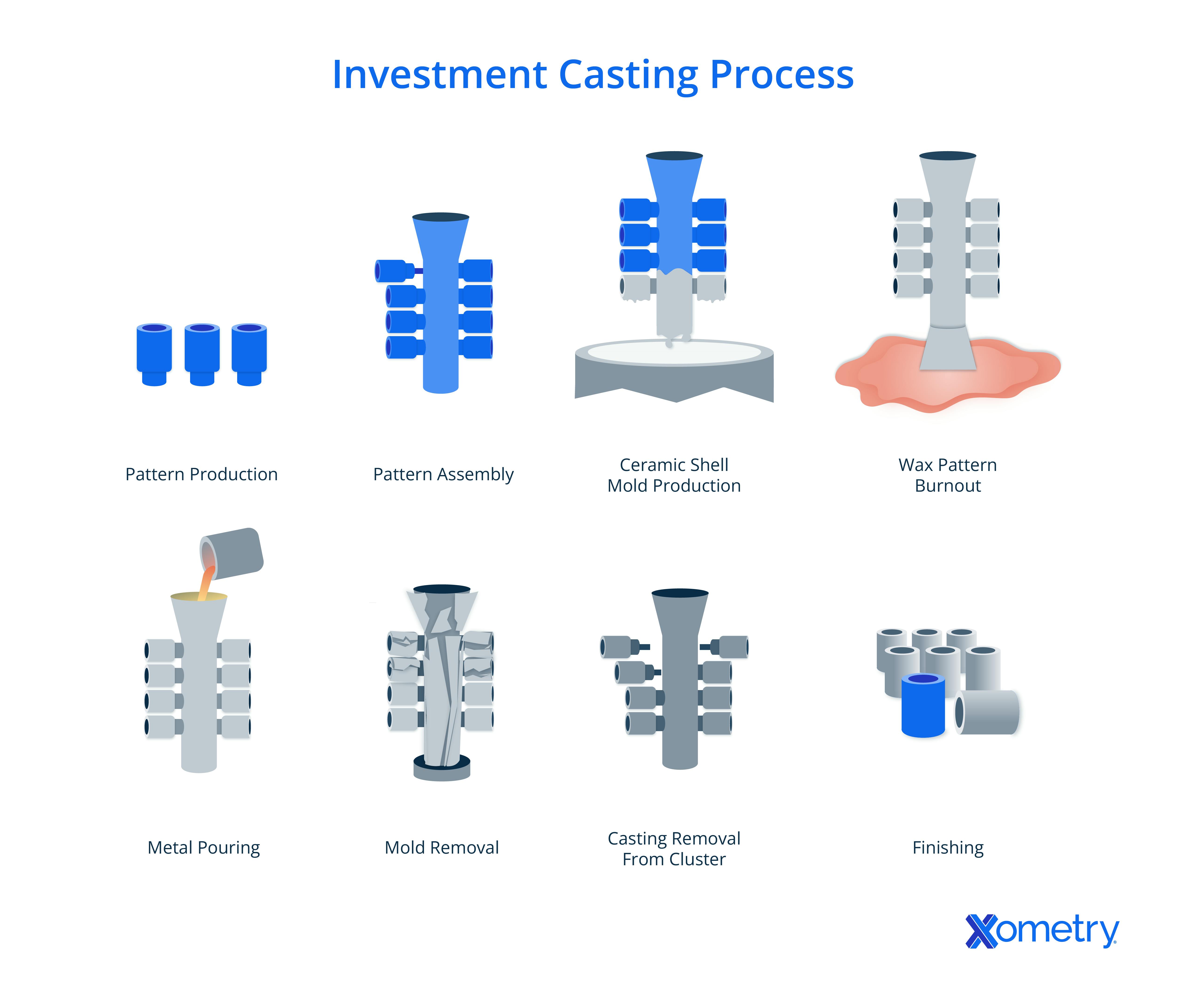
Materials Suitable for Investment Casting
1. Carbon Steel
The use of carbon steel for investment casting requires careful alloy selection.
2. Aluminum
Aluminum is well suited to high-value and moderate- to high-volume investment cast components in which the fine detail is limited and the quality level of equipment is higher than the norm.
To learn more, see our guide on Aluminum Properties.
3. Stainless Steel Alloys
Investment casting of stainless steel can sometimes result in a poor surface finish because of influences from the casting process, and material properties. The chromium and nickel content of stainless steel forms a robust oxide layer that can lead to surface irregularities and a rough finish due to chemical interaction with the refractory materials. Certain coatings and good refractory material selection can prevent much of this.
To learn more, see our guide on Stainless Steel Alloys.
4. Brass
Brass is extensively used for both functional and decorative investment castings, due to its versatility, cosmetics, and corrosion resistance. As a casting material, brass benefits from low melt temperature and viscosity and low shrinkage as it cools to solid. Brass has a bright golden appearance and is often used for decorative and ornamental applications. Brass properties in the casting process also offer some challenges. For example, zinc evaporation from the melt can lead to changes in properties. Good mold design, atmospheric oxygen control, and mold coatings can moderate this effect.
5. Glass
The investment casting of glass is an unusual technique that is used to a limited degree in art and decorative object manufacturing. It differs from the metal process in that the flask is generally charged with powdered glass, with a large hopper (also filled with glass powder) over the sprue. The whole is then placed in a kiln and the glass is melted and unified in the mold. This ensures that the air space (between powder particles) is pushed full as the glass melts. In all other regards, the process is much like investment casting metal except that the part requires considerably more care in demolding and handling.
Accuracy of Investment Casting
The investment casting process is very accurate in creating precise reproductions of the pattern when the flask has been prepared with skill and care. Pattern accuracy is highly dependent on the manufacturing process used to make it. A range of techniques can be used to improve the precision of the wax pattern. For example, if the pattern is molded in a tool, the injection pressure of the wax can be adjusted to moderate dimensional errors. Parts of the pattern requiring high precision can also be post-machined or “coined” (press molded with a precise steel cavity in two parts.
Advantages of Products Made With Investment Casting
Investment casting has various advantages that make it a critically important manufacturing process. These include:
- Complex geometries, thin walls, and fine features are relatively easy to achieve reliably, providing remarkable design freedom.
- The dimensional accuracy and repeatability of castings are very good, assuming the patterns are regular and identical.
- Surface finishes are generally good and the process can be tuned to deliver exceptional surface quality and precisely defined textures.
- Few limitations exist in material selection for casting—including: resins, ceramics, cement, most metals/alloys, and glass.
- General properties in the cast part faithfully reproduce the properties of the raw material.
- Material wastage is very low, as all feed/sprue parts can be re-used (except thermoset resins).
- Complex assemblies of multiple components can be consolidated into a single investment cast, reducing assembly time and potential failure points.
- Tooling costs are low (in comparison with die casting).
- Less post-processing is required than with typical sand casting.
Disadvantages of Products Made With Investment Casting
Investment casting is not a perfect process. Limitations and restrictions must be taken into account, including:
- Non-automated process costs are higher than for sand casting.
- Volume component costs are always higher than for die casting.
- The many steps in the process leave wide scope for error.
- The size and weight of one-piece castings are much more limited than for sand casting.
- The per-component cost is higher than for sand casting at the one-off level, with the differential eroding quickly with increased automation and volume of parts.
- Material limitations are not significant but must be taken into account.
Cost of Investment Casting
It depends. Investment cast parts can almost never be described as “cheap”, but they are very widely viewed as cost-effective. These are typical descriptors of overriding benefits:
- If cast parts would otherwise be produced by complex assemblies, investment casting is cost-effective.
- If cast parts have geometries that cannot otherwise be made in a one-stage, net-shape process, investment casting is the only logical choice.
- When quality and precision are more critical than cost, the process is widely applied for good commercial reasons.
Examples of Investment Casted Products
Investment casting is of extreme value and highly appreciated in the making of:
- Complex, hollow turbine blades in exotic alloys, for gas and steam turbines.
- Race and mass production of ICE (internal combustion engine) components.
- Turbocharger radial turbines.
- Jewelry and decorative items in one-off and limited production.
- Dental implants in volume and crown/bridge metalwork for one-off custom builds.
- Custom orthopedic implants.
How Xometry Can Help
Xometry provides a wide range of manufacturing capabilities including investment casting (requires a manual quote), CNC machining, 3D printing, injection molding, laser cutting, and sheet metal fabrication. Get your instant quote today.
Disclaimer
The content appearing on this webpage is for informational purposes only. Xometry makes no representation or warranty of any kind, be it expressed or implied, as to the accuracy, completeness, or validity of the information. Any performance parameters, geometric tolerances, specific design features, quality and types of materials, or processes should not be inferred to represent what will be delivered by third-party suppliers or manufacturers through Xometry’s network. Buyers seeking quotes for parts are responsible for defining the specific requirements for those parts. Please refer to our terms and conditions for more information.
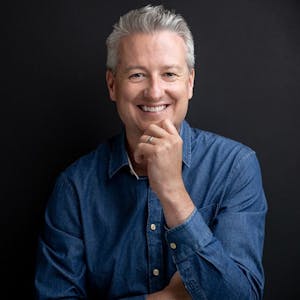