Carbon steel is essentially iron with varying levels of carbon as the main alloying element. Carbon steel is one of the most widely used manufacturing materials due to its formability, weldability, strength, and ability to be heat treated to precisely modify its mechanical properties. Apart from carbon, an extra amount of manganese is also included in most alloys. Sulfur and phosphorus are also present however these are typically undesired and seen as impurities.
This article will describe what carbon steel is, the various types of carbon steel, and their advantages, disadvantages, and physical properties. The maximum operating and melting temperatures of carbon steel will also be reviewed. 1020 carbon steel rods are shown in Figure 1 below:
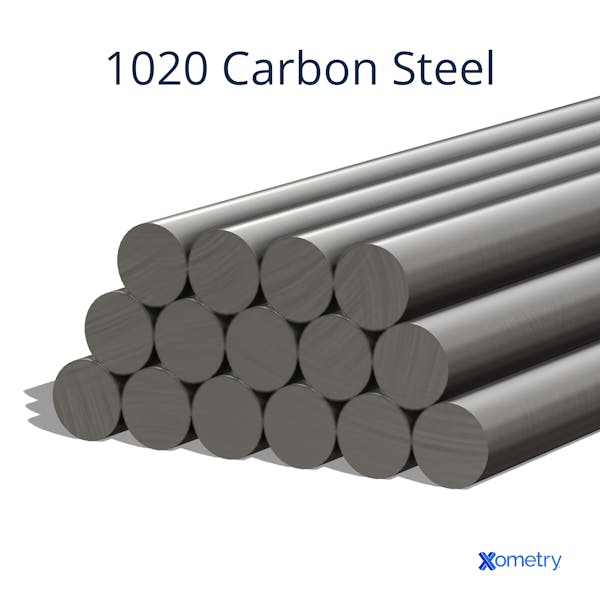
What is Carbon Steel?
Carbon steel is a series of iron alloys whose main alloying element is carbon. Carbon steels are widely used in almost every industry and are generally classified into low, medium, and high-carbon varieties. Carbon content has a strong influence on the mechanical properties of steel. As the carbon content increases, the steel will typically have higher strength and lower ductility. Medium and high carbon steel are readily heat treated, which can further improve their mechanical properties.
Carbon steel consists of iron alloyed with small amounts of carbon (typically below 1 %, though it can be as high as 2 %), manganese, and silicon, with sulfur and phosphorus present mostly as impurities. Each element added to plain carbon steel plays a specific role in the final properties. For example, manganese is added primarily to help desulfurize steel. However, it can be added in slightly larger quantities, up to 1%, as a substitutional solute to help strengthen the steel. Silicon, on the other hand, is added primarily as a deoxidizer, and is primarily present as a residual element, though it can be added in small amounts for strengthening.
Different Types of Carbon Steels
Plain carbon steels are often classified as low, medium, or high carbon steels based on the weight percent carbon in the alloy. The exact carbon levels for these three categories are not universally accepted and different standards-issuing organizations define slightly different category boundaries. However, this article sticks with the divisions defined by ASM International:
- Low-Carbon Steel: Low-carbon steel is any steel with a carbon content of less than 0.2 %. Low-carbon steel, also referred to as mild steel, is one of the most common grades of carbon steel. This grade cannot be heat treated and can only be hardened by cold working. Low-carbon steel is readily welded. It is highly ductile, which can make it difficult to machine due to galling (a type of wear caused by adhesion between sliding surfaces) and the formation of long chips. Adding a small, controlled amount of sulfur can increase its machinability.
- Medium-Carbon Steel: Medium-carbon steel refers to steel with a carbon content between 0.2 and 0.5 %. Medium-carbon steel has a good balance between strength, ductility, and wear resistance. This grade can be heat treated for additional strength. The higher the carbon content, the more heat-treatable the alloy. It can also be welded. However, special pre- and post-heating weld procedures are required to avoid forming brittle martensite in the heat-affected zone of medium-carbon steels.
- High-Carbon Steel: High-carbon steel refers to steel with a carbon content larger than 0.5 % but less than 1 %. High-carbon steel, a type of tool steel, has the highest level of carbon content. This means it has the highest strength and hardness among the plain carbon steels. However, these properties come at the cost of increased brittleness. High-carbon steels are difficult to weld because of their propensity to form large amounts of brittle martensite in the weld heat-affected zone, increasing the potential for weld cracking.
Properties of Carbon Steel
Carbon steel is an umbrella term used to describe a wide variety of steel compositions. The mechanical properties of a specific grade from each carbon steel category (cold-rolled carbon steel) have been listed in Table 1 below using the AISI numbering convention:
Low Carbon (AISI 1020) | Medium Carbon (AISI 1040) | High Carbon (AISI 1095) | |
---|---|---|---|
Low Carbon (AISI 1020) Modulus of Elasticity (GPa) | Medium Carbon (AISI 1040) 186 | High Carbon (AISI 1095) 200 | 205 |
Low Carbon (AISI 1020) Brinell Hardness | Medium Carbon (AISI 1040) 121 | High Carbon (AISI 1095) 201 | 293 |
Low Carbon (AISI 1020) Yield Strength (MPa) | Medium Carbon (AISI 1040) 350 | High Carbon (AISI 1095) 415 | 570 |
Low Carbon (AISI 1020) Ultimate Tensile Strength (MPa) | Medium Carbon (AISI 1040) 420 | High Carbon (AISI 1095) 620 | 965 |
Low Carbon (AISI 1020) Elongation at Break (%) | Medium Carbon (AISI 1040) 15 | High Carbon (AISI 1095) 25 | 9 |
Low Carbon (AISI 1020) Shear Modulus (GPa) | Medium Carbon (AISI 1040) 72 | High Carbon (AISI 1095) 80 | 80 |
Table Credit: matweb.com
Applications of Carbon Steel
The applications for carbon steel are almost limitless. Every industry, from automotive to consumer goods makes use of a carbon steel part in some form or another. Some notable examples of the applications of carbon steel are listed below:
- Shafts
- Cables
- Structural members
- Wire
- Ball bearings
- Ship building
- Piping
- Springs
- Pressure vessels
- Pulleys
- Gears
- Cutting tools
- Fasteners
Carbon Steel Strength
The strength of carbon steel depends on its carbon content, the level of additions of Mn and Si, which can be solid solution strengtheners, as well as the heat treatment performed on it. The higher the carbon content, the higher its strength. For that reason, high-carbon steel has the highest strength. High-carbon steel is typically used for cutting or forming tools due to its strength and hardness. However, high-carbon steel is brittle and can crack and break if exposed to impact loads.
Advantages and Disadvantages of Carbon Steel
Carbon steel is one of the most widely used steels due to a variety of advantages as listed below:
- Low Cost: Carbon steel consists of low-cost iron and carbon, making carbon steel significantly cheaper than alloy steel, for example. Alloy steel makes use of more expensive elements like nickel and chrome.
- Heat Treatable: Medium and high-carbon steels can have their properties significantly improved through various heat treatment regimens. Heat treatment can increase ultimate tensile strength, wear resistance, ductility, or hardness.
- Weldability: Carbon steels, especially low-carbon steel are readily weldable. Weldability can be further improved by using lower carbon grades and following appropriate procedures (preheating, stress relief heat treatment, etc) for the steel grade being welded.
Despite the prevalence of carbon steel, there are still some disadvantages that must be considered before making use of carbon steel, as listed below:
- Poor Corrosion Resistance: Carbon steels have poor corrosion resistance and must be surface treated to impart corrosion resistance. These surface treatments are typically painting and hot-dip galvanizing.
- Poor Formability: High-carbon steel is strong but brittle. Its reduced ductility makes this grade of carbon steel difficult to form.
- Not Heat-Treatable (Low-Carbon Steels): Low-carbon steel is easy to form but cannot be strengthened with heat treatment. However, it can be cold-worked to improve its properties.
Operating Temperature of Carbon Steel
Carbon steels generally have a maximum operating temperature of 427 °C. Above this temperature, carbon steels experience a significant reduction of strength due to embrittlement, caused by the graphitization of carbides in the steel. The rate of corrosion also increases with temperature, so carbon steels exposed to corrosive environments at elevated temperatures will typically have a low maximum operating temperature.
Listed in Table 2 below are the solidus (melting onset) and the liquidus temperature (melting completion) for three common grades of carbon steels:
Low Carbon (AISI 1020) | Medium Carbon (AISI 1040) | High Carbon (AISI 1095) | |
---|---|---|---|
Low Carbon
(AISI 1020) Solidus (°C) | Medium Carbon
(AISI 1040) 1420 | High Carbon
(AISI 1095) 1420 | 1410 |
Low Carbon
(AISI 1020) Liquidus (°C) | Medium Carbon
(AISI 1040) 1460 | High Carbon
(AISI 1095) 1460 | 1450 |
Table Credit: makeitfrom.com
Carbon Steel vs. Mild Steel
There is no difference between carbon steel and mild steel. Mild steel is a colloquial name used to refer to low-carbon steel. Mild steel is simply a type of carbon steel.
Disclaimer
The content appearing on this webpage is for informational purposes only. Xometry makes no representation or warranty of any kind, be it expressed or implied, as to the accuracy, completeness, or validity of the information. Any performance parameters, geometric tolerances, specific design features, quality and types of materials, or processes should not be inferred to represent what will be delivered by third-party suppliers or manufacturers through Xometry’s network. Buyers seeking quotes for parts are responsible for defining the specific requirements for those parts. Please refer to our terms and conditions for more information.
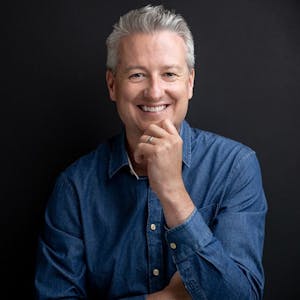