It’s not a complicated process, but mold casting is a precision method without the cost of more premium processes, like die casting. It’s efficient and can make smooth final products. It can even combine multiple parts into a single piece. Perhaps this is a process you’ve considered for your own manufacturing needs or you’re interested in learning more about how it works in general; either way, read on to learn more about it in our rundown of this specific mold casting type.
What is Permanent Mold Casting?
Permanent mold casting uses two-part reusable molds made of steel or cast iron to shape metals with lower melting points (like aluminum). This is no new tech—it’s been around since before the Bronze Age—and because of its effectiveness, quality, and replicability, it’s still happily used by many manufacturers and fabricators today. With it, you get a decent level of control over the filling and solidification and post-processing can provide products with sleek surfaces.
The high-quality finishes you can expect with permanent mold casting are mainly thanks to the fact that you can control several factors within the process. Manufacturers are able to oversee the pouring process, and check how it’s cooled, which is something that’s not always possible with sand casting. Of course, as with any manufacturing process, the material’s expected shrinkage, tooling, the part’s complexity, and who is controlling the process can have an impact on the end result. It’s also one of the methods that not everyone can have a go at; operators need to be trained and highly skilled.
In industry nowadays, permanent mold casting is used to make transmission housings, intake manifolds, lower-stress suspension parts, cylinder heads, engine blocks, heat exchangers, propellers, plumbing fittings, valves, machinery, pump, and gearbox components, and parts for turbines, and HVAC systems. The process can make products with less turbulence, porosity, and air pockets. You can get decent mechanical properties like strength and hardness from most permanent mold casting methods, and the molds are reusable, too. It works with a wide range of materials—although not all of them because there’s a lower melting temperature and mold temperature.
You won’t want to rely on permanent mold casting for very complex or intricate parts/components, as small details can be missed in the filling process. But it’s rather hard to beat when it comes to simpler castings that need to look good, have dimensional accuracy, consistent quality, and great mechanical properties. This process has a mid-range cost that’s cheaper than die casting, but more expensive than sand casting. While you can start production quickly, and it's easy to ramp up the speed and product quantity, cycle and lead times tend to be longer than with other casting processes, and often there are higher tooling costs than if you were to use sand casting. Tweaks and edits to the initial design with this process can also be more expensive, and harder than with sand casting. Molds can eventually wear down and need maintenance, and/or replacing.
How it Works
This is a brief breakdown of the steps required for permanent mold casting, and you can get a good visual of the process in the image below.
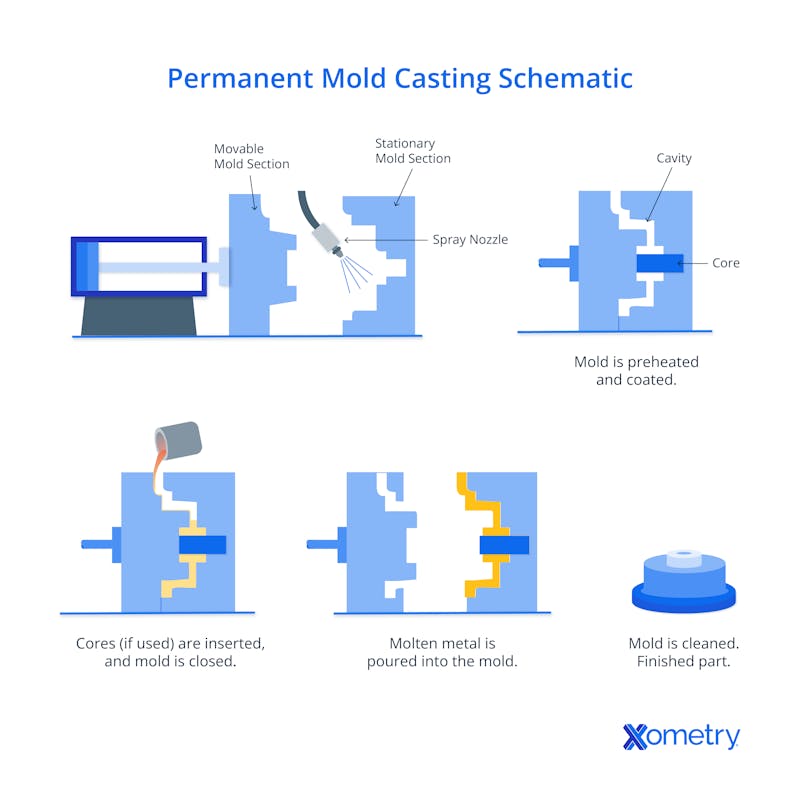
The permanent mold casting process
1. Preheat
The mold is first preheated to the appropriate temperature for the material being handled—the temperature controls the solidification and cooling—then the surface is coated with a mold release spray that’ll help later with removing the casting.
2. Insert split parts
The split parts need to be assembled, and the cores of the mold clamped. It can either be done by an operator or with automated programming that will kick in if it’s a larger production run and get them ready for filling.
3. Pouring
This step is either done by an operator who pours the molten metal into the mold carefully to make sure it’s completely filled, or a metered system (with someone on close watch) that does it through a gate.
4. Cooling
The cooling process doesn’t need much manual labor—you just leave it there to cool—but it does take the longest time. But there are some additional processes, like water-cooling, that can be used to speed this part up.
5. Removing
When the piece is cool, hard, and ready, the operator has to open the mold and either they or an automated system will remove it.
6. Post-processing
Some parts need post-processing treatments, like gate trimming, flash removal, or surface finishing, so they’ll be sent off for further work.
Types of Permanent Mold Casting
The three types of permanent mold casting are:
Low-pressure: The melted metal comes from a feeder that leads into a sprue at the top of the machine and is pulled down just with gravity. This needs bottom feeding (other types use top feeding), so lessens the chance of air bubbles, and sometimes even shrinkage.
Vacuum: Using a bottom feeding method, but with a vacuum at the top that brings the molten material into the cavity—usually at a faster rate, this type offers good repeatability and uniform products. There are also no air bubbles and very little turbulence.
Slush: Used for products that don’t need to be heavy-duty, slush casting involves filling a cooler mold with material, which then forms a thin skin/shell in the desired shape. The remaining material will be flushed out.
Metals Used for Making Parts
There are a few metals manufacturers will typically rely on for making permanent mold castings listed below, as well as one material that’s important but not for the end products themselves.
- Zinc: These alloys are practically made for this style of mold casting because they melt at lower points and aren’t extremely abrasive on the tools used during the process. Using zinc also results in pretty strong objects.
- Aluminum: This material creates accurate dimensions, quickly and easily melts, and cools without too much turbulence or porosity. But you can’t use pure aluminum, it has to be some type of alloy.
- Copper alloys: These metals, like brass, bronze, and Muntz, are usually made into decorative objects, and low-stress/tension items, with slush casting.
- Iron: This is rarely used for the actual casts, but can be chosen for the mold material.
How Xometry Can Help
Xometry has helped countless clients with numerous casting processes and many types of molds. If you need any more information on this (or any other) manufacturing method, feel free to reach out to one of our representatives. You can also get the ball rolling and request a free instant quote on our site for services like plastic injection molding, bridge molding, zinc die casting, and quick turn molding.
Disclaimer
The content appearing on this webpage is for informational purposes only. Xometry makes no representation or warranty of any kind, be it expressed or implied, as to the accuracy, completeness, or validity of the information. Any performance parameters, geometric tolerances, specific design features, quality and types of materials, or processes should not be inferred to represent what will be delivered by third-party suppliers or manufacturers through Xometry’s network. Buyers seeking quotes for parts are responsible for defining the specific requirements for those parts. Please refer to our terms and conditions for more information.
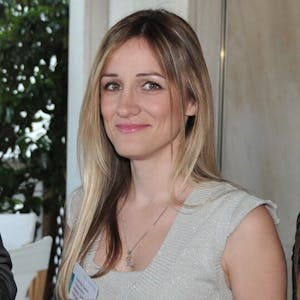