Vacuum die casting is a method for manufacturing high volumes of identical precision parts, usually with complex geometries. It is very similar to traditional die casting, but with an added vacuum system that removes almost all of the air and other gasses from the die before the molten metal is introduced. This improves product quality overall and, in particular, reduces porosity. Lower porosity leads to more consistent mechanical behavior.
This article will discuss vacuum die casting, its importance, how it works, its applications, and its advantages.
What Is Vacuum Die Casting?
Vacuum die casting is a variation of traditional die casting. Like most such methods, molten metal is injected into a metal die cavity under pressure. However, the key difference with vacuum die casting is that a vacuum system is used to remove all the air and other gasses from the die cavity before the molten metal is injected. For this reason, vacuum die casting is also referred to as gas-free die casting.
Variations of this technique, such as high vacuum die casting (HVDC) or even ultra-high vacuum die casting (UHVDC), are named for the internal vacuum’s intensity. Higher vacuum means less gas in the die, and therefore better quality casting from a material porosity perspective.
Vacuum die casting works by evacuating most of the air and other gasses from the die prior to injection. This means that there is very little gas present in the die when the molten metal is injected. The resulting parts are far less likely to have the porosity defects that plague die-cast items. The vacuum in the mold also helps draw the molten metal into every channel. An evacuated die therefore provides numerous benefits over traditional die casting.
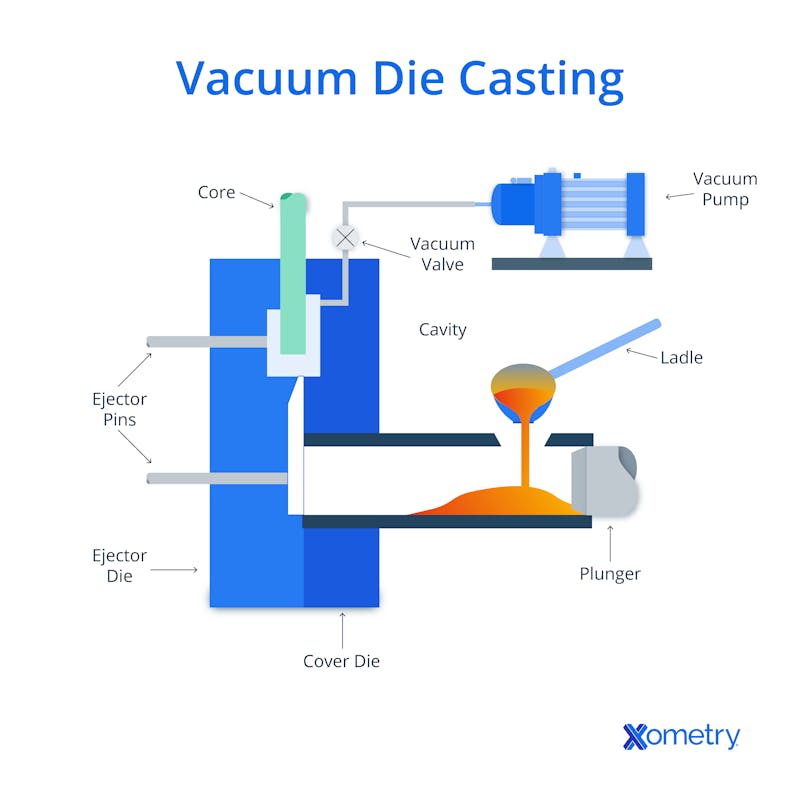
Diving in to The Vacuum Die Casting Process
The process of vacuum die casting is similar to traditional die casting and is quite straightforward. Naturally, though, the creation of a vacuum inside the die is a critical step. Let’s look at the process:
1. Melt the Metal Alloy
The first step in vacuum die casting is to melt the metal alloy. This is the source material that will later be cast. The metal needs to be molten enough to accurately fill the shape and crevices of the die.
2. Transfer the Molten Metal to the Shot Chamber Using a Plunger (Hot Chamber) or a Ladle (Cold Chamber)
The second step in the vacuum die casting process is to transfer the molten metal to the shot chamber. The transfer method depends on the type of die casting machine. For a hot chamber machine, the pot of molten metal forms part of the molding equipment. In that case, a plunger is integrated within the chamber and descends to force molten metal into the shot chamber. A cold chamber die-casting machine, by contrast, does not contain its own inventory of molten metal. The shot chamber is filled manually by transferring molten metal from a pot by use of a ladle.
This sucks nearly all the gas molecules from the die cavity to create near-vacuum conditions. The molten metal is then injected into the die from the shot chamber by a ram.
The vacuum created within the die cavity helps draw the molten metal into all of its fine channels. Removing the air allows the liquid metal to be pulled in and distribute itself evenly throughout the die—this is critical for complex geometries.
A vacuum is particularly important for thin-walled parts.
4. Allow the Metal To Solidify and Cool Down
The molten metal will immediately begin to cool within the die. Dies are manufactured with cooling channels so that coolant can be circulated to control the temperature and remove heat once the metal has been injected. An integrated cooling system in the die allows the metal to cool and solidify in a quick but controlled way.
Ejector pins move the ejector die away from the stationary cover die. The finished component can then be removed.
Metals Used in Vacuum Die Casting
The metals used in vacuum die casting usually have moderate melting temperatures and moderate densities. Most common are:
- Aluminum Alloys: The common aluminum alloys for die casting contain constituents like: silicon, magnesium, zinc, and copper. A380 is the most common aluminum alloy used in die casting.
- Magnesium Alloys: Magnesium alloys such as AZ91D are also popular for use in vacuum die casting. Typically, magnesium alloys are used to cast structural components.
- Zinc alloys: Zinc alloys include the elements of aluminum, magnesium, and copper, termed the Zamak series. Zinc alloys with high aluminum content are part of the ZA series. These alloys have a broad range of properties and fit well into the vacuum die casting process.
Applications of Vacuum Die Casting
The biggest application of vacuum die casting is the mass production of automotive parts. The process is frequently applied to manufacture engine, transmission, and suspension components. It’s most important for these components that need to be either heat-treated or welded after fabrication. Metal cast with the aid of a vacuum is far less porous than other cast metals, so welds and heat treatments are far less likely to cause blistering or other defects. Another application of vacuum die casting is in the aerospace industry, where highly accurate parts with predictable mechanical properties are required.
The automotive industry uses vacuum die casting more than any other in the world. This is for a number of reasons, such as the high volume of identical parts produced, the high strength-to-weight ratio it lends thin-walled components, and the parts’ dimensional accuracy. The alloys used for automotive manufacture — especially aluminum and magnesium alloys — are well suited to vacuum die casting.
The aerospace industry also uses vacuum die casting products, as even complex shapes can be made this way. Plus, parts can be designed with thin walls that give them good strength-to-weight ratios. Vacuum die casting machines are also used in many industries with large assembly lines that produce thousands of identical components. These include the manufacture of electrical machinery, appliances, and power tools.
Advantages and Disadvantages of Using Vacuum Die Casting for Your Parts
Vacuum die casting is a valuable process, particularly because of the following advantages:
- Very little gas can get trapped within the solidified component because the air in the die is evacuated before the molten metal is injected. This means that parts that are manufactured with vacuum die casting are far less porous than traditional die cast parts.
- Without the interference of air, the metal exhibits consistent mechanical properties throughout the part rather than unpredictably porous or weak patches.
- Consistent properties and low porosity give designers the opportunity to create thinner walls that could reliably be cast with traditional die casting.
- The much lower porosity of vacuum die cast components means that they can be welded or heat-treated without the risk of interference from dissolved gasses.
No manufacturing process is perfect, and there are some disadvantages to vacuum die casting as listed below:
- Vacuum die casting like ordinary die casting, is not compatible with all metals. Ferrous metals (any alloy with significant iron content) and those with particularly high melting points are not well suited to vacuum die casting.
- The additional equipment in the vacuum system makes it more expensive than a traditional die casting arrangement.
- The vacuum system introduces many new pumps and valves that need to be calibrated and controlled properly. This adds to the complexity of the operation.
Cost of Vacuum Die Casting
The cost of vacuum die casting a component depends on size and material, but it usually falls in the range of $10 for a small part (<1 kg) to $100 for a larger part (~20 kg). Vacuum die casting is one of the more expensive manufacturing methods, but it is well suited to producing very high volumes of identical high-quality parts.
Vacuum Die Casting vs. Other Types of Casting
Vacuum die casting compared to other types of casting has exceptionally low porosity of its completed components. This is achieved because the air is removed from the die before molten metal is introduced. There are thus very few air molecules available to create defects. Parts with minimal porosity also exhibit: more consistent mechanical properties, higher dimensional accuracy, and better surface finishes. To learn more, see our guide on Casting Types.

Summary
Xometry provides a wide range of manufacturing capabilities including CNC machining, 3D printing, injection molding, die casting (including vacuum die casting), laser cutting, and sheet metal fabrication. Get your instant quote today.
Disclaimer
The content appearing on this webpage is for informational purposes only. Xometry makes no representation or warranty of any kind, be it expressed or implied, as to the accuracy, completeness, or validity of the information. Any performance parameters, geometric tolerances, specific design features, quality and types of materials, or processes should not be inferred to represent what will be delivered by third-party suppliers or manufacturers through Xometry’s network. Buyers seeking quotes for parts are responsible for defining the specific requirements for those parts. Please refer to our terms and conditions for more information.
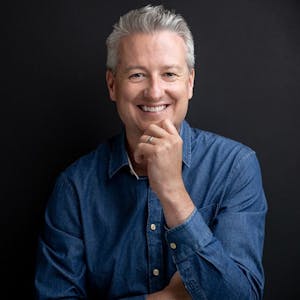