Die casting is one of Xometrys many production-capable manufacturing processes. Today we’re going to explore a specific method of the process, gravity die casting. It is an old but serviceable and enduring manufacturing technique that holds a prominent place in modern industry and may be the key to making your product cost-effective and profitable. The gravity die casting technique involves making both simple and highly complex metal components by simply pouring molten metal into a reusable, steel cavity mold tool. Gravity die-cast parts can be of great quality and have very low porosity when the process is executed correctly.
Many Xometry customers ought to be considering the appealing simplicity of gravity die casting, so we are here to make it clear how easy and productive this process can be when used right.
What Is Gravity Die Casting?
Gravity die casting is a manufacturing process you can specify to produce high-quality metal parts with complex shapes and a relatively good surface finish. It's a type of die casting method because it uses a die, but it differs greatly in complexity from the pressurized and squeeze-cast methods. One of its major advantages is the simplicity of the equipment and the potential to use it in traditional and very low-tech foundry conditions.
It is widely viewed as an effective mass-production tool for producing metal components with moderate dimensional accuracy, consistent quality, and relatively short cycle times. This assertion is supported by the extensive use of the process across many moderate and high-volume sectors of manufacturing. The process is well-suited for demand ranging from 250 to 50,000 units per annum. Using cast iron or steel molds provides greater repeatability, lower labor, and improved cost-effectiveness in comparison to other casting methods, such as sand casting.
Gravity Die Casting Step By Step
Gravity casting works by allowing molten metal to flow gently into a permanent mold under the influence of gravity alone. Listed below, you’ll find a detailed breakdown of the steps involved in gravity die casting:
1. Preheat the Die and Coat the Mold Cavity
Before starting the gravity die casting process, the die (also known as the mold) is preheated to a certain temperature to suit the charge metal. This prevents cold spots and ensures uniform solidification of the fill. This step helps to reduce thermal shock, improving the longevity of the die. Additionally, a release agent or coating is commonly applied to the inner surfaces of the die cavity. This coating helps facilitate the removal of the solidified part once the casting process is complete, by reducing sticking. Dies erode due to molten metal contact, especially in turbulent flow areas, because some casting metals can be quite abrasive. Die coating reduces this erosion, maintaining surface integrity for more cycles, whereas otherwise, the roughness would increase casting stick and defects.
2. Pour Molten Metal Into the Cavity
Once the die is preheated and coated, it is securely clamped together. Molten metal, typically aluminum or other non-ferrous alloys, is then poured into a pouring basin or runner system that leads to the die cavity. The molten metal enters the mold cavity under the force of gravity alone, hence the name "gravity die casting." The carefully controlled pouring process helps minimize turbulence and air entrapment, resulting in better-quality castings. Filling from below allows the smooth upward rise of the charge meniscus and assists in driving out air and maintaining low turbulence.
3. Allow the Metal To Solidify
As the molten metal is introduced into the mold cavity, it cools rapidly. Solidification starts first when the charge contacts the relatively cooler surfaces of the mold and progresses inward toward the center of the casting cross-section. The metal fill cools rapidly in the mold cavity, solidifying first at the cooler mold surfaces and thinner sections, progressing inward. Preheated molds ensure consistent solidification rates, preventing premature solidification in thin sections that could block metal flow. Solidification time varies with metal type and part design. Mold preheating benefits include avoiding thermal shock, maintaining molten metal temperature for proper flow, and reducing thermal stress in solidifying casting. The time required for solidification depends heavily on the type of metal being cast, the mass of the tool and charge, and the design of the part.
4. Open the Die and Remove the Part
After the charge has fully solidified within the die cavity, the clamps holding the die closed can be released. The opened die reveals the solidified casting that will precisely mirror the cavity it fills, with good dimensional accuracy and great repeatability between casts. The application of the release agent during the initial steps should allow the easy removal of the casting from the die.
5. Machine the Part if Needed
Once the casting is removed from the die, it may undergo further processing, such as machining, to achieve the desired final shape and surface finish, remove vent, fill and flash attachments, and improve local precision in areas of higher tolerance than the casting method can achieve. The decision to machine the part depends on its intended use and the required level of precision, as well as the quality of the die machining/fit.
The production speed of the gravity die casting process varies widely as a consequence of various factors, including the material being cast, the complexity of the part's design, and the size of the casting. The entire gravity die casting process typically takes anywhere from a few minutes for simpler castings to several hours for larger or more intricate parts that have longer cooling times. Cycle times can be reduced somewhat, although not without the potential for quality risks. Careful design of the casting process parameters, die design, and material selection allow for the balance of production and casting quality.
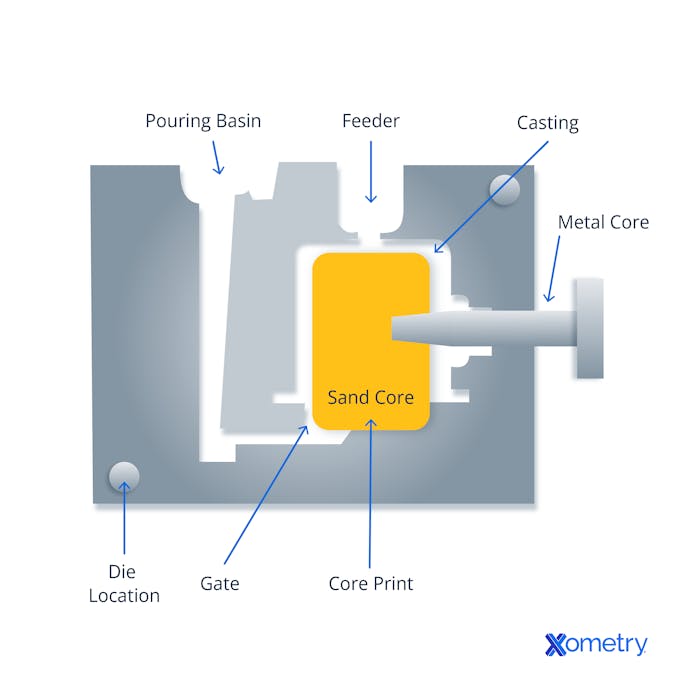
Suitable Materials for Gravity Die Casting
A number of materials are compatible with gravity die casting. Some of the most common are listed below:
1. Steel
Certain low-alloy steels with relatively lower melting points can be used for gravity die casting applications where specific mechanical properties are required. That being said, steel is rarely used to create die-cast parts. Instead, steel is most often used in the mold making step of the process. Steel's elevated melting point and retention of physical properties when hot make it well-suited for casting molds.
2. Magnesium
Magnesium and magnesium-aluminum alloys are commonly used with gravity die casting due to their low density, very high strength-to-weight ratio, and excellent machinability. This results in strong components with low mass for weight-critical applications across multiple industries: automotive, sporting goods, aerospace, and more. Magnesium castings offer considerable advantages in market sectors where lightweight components are crucial, providing performance benefits in fuel consumption and acceleration. However, the intense and vigorous flammability hazard that heated magnesium presents is a huge process risk and must be carefully managed using either a flux or a nitrogen atmosphere to exclude oxygen.
3. Aluminum Alloys
At Xometry and across the industry as a whole, aluminum and its broad range of alloys are the most commonly exploited materials for gravity die casting due to their relatively low melting point, good fluidity when molten, relatively low cost, and favorable mechanical properties in the finished product. These make it an ideal choice for a wide range of applications. Aluminum gravity castings are extensively employed in automotive parts, aerospace structural and actuator components, consumer electronics, and industrial components. To learn more about this material, see our guide on Aluminum Alloy.
4. Cast Irons
Cast iron is appreciated for its low raw material cost, toughness, and excellent wear resistance. It also offers good heat resistance and vibration-damping properties. It can be cast using gravity die casting, but because of its high liquefaction temperature and generally more complex casting process, it is now uncommon to die-cast it compared to other materials.
5. Copper Alloys
Copper alloys are widely used in gravity die casting, particularly for parts requiring good electrical conductivity or excellent thermal conductivity, such as bus bars, switch gear, and interconnect components in electrical systems. Copper's high melting point and greater thermal conductivity present some challenges during the casting process, requiring careful control of the casting parameters to enable high-quality copper alloy castings to be produced consistently.
6. Zinc
Zinc and zinc alloys, such as ZAMAK, are widely used in gravity die casting due to their relatively low melting points, very low viscosity in the melt, and the naturally good surface finish they produce. Zinc castings find applications in a number of industries, including electronics, decorative hardware, and automotive/industrial components. The ability to reproduce the fine details of a mold makes zinc, especially ZAMAK alloys, a popular choice for decorative items. At Xometry, we primarily offer ZAMAK 2 (ZA-2) and ZAMAK 3 (ZA-3) alloys for our zinc die-cast materials.
The Cost of Gravity Die Casting
One major drawback of gravity die casting is that it can be quite costly, given the cost to machine accurate dies and the relatively high labor cost in the process. Providing an exact estimate of what the process will cost is impossible because the price per part will differ on a project-by-project basis by weight of shot, volume of product required, and degree of post-processing. The complexity of the part being cast plays a crucial role. Intricate designs, thin walls, and undercuts will tend to result in higher costs as they’ll need more specialized tooling and slower and more cautious production processing.
The tooling costs for gravity die casting varies hugely, between possibly a few hundred dollars for a part requiring a simple mold to $100,000 and more for complex castings such as engine blocks and gearbox housings, which require much more elaborate tooling setups.
A primary alternative to die casting is sand casting; however, the cost benefit really depends on volume. Sand casting has considerably lower establishment/tooling costs but much higher per-unit production costs compared to gravity die casting, given the extensive use of skilled labor in the sand process. Sand-cast products are typically not as dimensionally accurate as their gravity die-cast equivalents. To learn more, see our guide: What is Sand Casting.
Need Metal Die Casted Components?
The Advantages of Gravity Die Casting
There are a lot of advantages associated with gravity die casting, including:
- The process is used to create typically high-quality castings, characterized by good surface finish, good repeatability, and fair-to-good dimensional precision.
- It consistently yields components of good quality, when the process is reliably and consistently executed and parameters and alloys remain stable.
- It delivers a cost-efficient approach for manufacturing on a moderate scale (250 to 50,000 per annum) and is more cost-efficient than pressure die-casting at lower volumes.
- Gravity die-casting results in less scrap compared to other (non-die) casting methods, delivering repeatable castings with minimal defects and porosity, once operational protocols are established.
- It can work with an extensive array of materials, encompassing aluminum, brass, bronze, zinc, magnesium, and copper, and a wide array of their alloys.
The Disadvantages of Gravity Die Casting
While there are a lot of advantages associated with gravity die-casting, there are also some difficulties and restrictions to accommodate:
- The process has distinct requirements that impose limitations on design flexibility. These molds are designed to allow molten metal flow driven solely by gravitational forces, in contrast to low-pressure and high-pressure die casting, which employ external pressure for mold filling. Achieving specific design features, like thin walls and intricate geometries, can be challenging within the confines of this method. This is particularly true in that the cavity must split in two and release the finished part, because undercuts are essentially impractical in gravity die-casting tools.
- It necessitates a moderately high initial investment in terms of tooling and equipment — primarily the tooling cost, if the foundry is already established. This is much lower than pressure die casting, which requires higher-cost tooling and considerable equipment investment. Establishment costs are also significantly higher than sand casting which is typically very low cost in setup and pattern making.
- In comparison to alternative casting methods, gravity die casting typically involves longer lead times. Fabrication of the permanent molds can take considerably longer than making wooden or rapid prototype patterns for sand casting or 3D printed wax masters and ceramic dip coating to make ceramic shells.
- Gravity die casting is most suitable for producing relatively small aluminum and zinc alloy castings. The method is less appropriate for manufacturing larger components, as the cost of the die is such that low- or high-pressure casting methods become in-range for cost.
A Few Examples of Gravity Die-Cast Products
Some examples of products that can be manufactured using gravity die casting include:
- Automotive parts such as engine blocks, cylinder heads, pistons, intake manifolds, and transmission housings
- Industrial machinery parts such as gearboxes, pump housings, and valve bodies
- Aerospace components like aircraft engine parts, brackets, and housings
- Decorative and functional lighting fixtures, such as lamp bases, housings, and ornamental components
- Parts for household appliances, including washing machine components, oven parts, and refrigerator components
- Kitchen utensils such as pots and spoons
- Enclosures for electronic devices, including computer chassis, audio equipment housings, and server rack components
The lifespan of these products varies considerably due to material selection, casting quality, environmental conditions in the use scenario, maintenance practices, applied loads, and applied surface treatments. The material selected for the casting process must relate to requirements in corrosion resistance and mechanical properties first, and cost considerations second. Long-term durability of the parts may not be an issue, for temporary or single-use components. The quality of the casting itself also influences product longevity. High porosity can destroy mechanical properties in invisible ways, or allow accelerated corrosion due to increased surface area.
While there is no fixed lifespan for gravity die-cast products, the molds are expected to last about 100,000 cycles on average before they need to be replaced.
Gravity Die Casting Compared to Other Forms of Casting
Gravity die casting distinguishes itself from other casting methods in several key aspects, including its process, materials used, and purpose. To help you dig deeper into these distinctions and understand the relative advantages of each process, let's compare gravity die casting with these other casting processes using the table below:
Casting Process | Metals | Tolerance | Surface finish (RMS) | Min thickness | Typical tooling cost |
---|---|---|---|---|---|
Casting Process Gravity Die Casting | Metals Cu, Al, Zn, and cast irons | Tolerance Standard +/- 0.015" to 1" then add +/- 0.002" /inch | Surface finish (RMS) 150–300 | Min thickness 0.188" | Typical tooling cost $10000 to $100000 |
Casting Process Sand Casting | Metals All Metals | Tolerance Standard +/- 0.030" up to 6", Add +/- 0.002" for every inch over 6 | Surface finish (RMS) 500–2000 | Min thickness 0.150" | Typical tooling cost $2000 to $40000 |
Casting Process Low-Pressure Die Casting | Metals Al, Cu, Zn, Mg | Tolerance Standard +/- 0.015" to 1" then add +/- 0.002" /inch | Surface finish (RMS) 150–300 | Min thickness 0.188" | Typical tooling cost $10000 to $300000 |
Casting Process High-Pressure Die Casting | Metals Al, Zn, and Mg | Tolerance Standard +/- 0.010" to 1" then add +/- 0.001" /inch | Surface finish (RMS) 32–63 (Zinc); 63–250 (Aluminum) | Min thickness 0.030"(Mg) to 0.060" (Aluminum) | Typical tooling cost $10000 to $300000 |
Casting Process Investment Casting (lost wax casting) | Metals Al and Steel | Tolerance Standard +/- 0.005" to 3" then add +/- 0.003" /inch | Surface finish (RMS) 63–250 | Min thickness 0.060" | Typical tooling cost $3500 to $25000 |
Casting Process Squeeze Casting | Metals Al | Tolerance Standard +/- 0.010" to 1" then add +/- 0.001" /inch | Surface finish (RMS) 90–500 | Min thickness 0.30" | Typical tooling cost $10000 to $300000 |
Table Credit: https://cmtimports.com/foundry-101/process-selection-comparison-table.html
Alternatives to Gravity Die Casting
Although gravity die-casting is a widely employed method for the production of non-ferrous components, there are several alternatives available:
- High-Pressure Die Casting: This is a casting method where molten metal is forced into a mold cavity at speed, under considerable pressure. This process is optimal for producing parts with complex shapes, requiring tight tolerances, and great surface finish. The high setup costs, short production cycles and minimal post-processing suit high-volume components. The process is not suitable for all parts, and tooling costs tend to be significantly higher than alternative processes.
- Low-Pressure Die Casting: This is a process in which molten metal is introduced into a mold cavity under low but non-zero pressure. The mold is typically preheated, and a pressurized casting setup is used to fill the mold cavity. This method is appreciated for its ability to reduce fill turbidity and gas entrapment during filling, delivering improved casting quality compared to some other applicable processes. Low-pressure die casting tends to deliver better structural integrity than gravity die casting.
- Sand Casting: This provides a low-tech, moderate-skill alternative for creating parts, particularly those with three-dimensional hollows and details or volumes that don’t suit the capabilities and costs of gravity die casting. In particular, this process doesn’t have the material temperature limitation of die-casting, making it a preferred option for iron and steel castings, even in moderate volumes. Sand casting is versatile and can handle more intricate designs, it also incurs the lowest cost of setup even though it has longer production cycles compared to other methods.
- Investment Casting: This is a viable alternative when high precision and intricate detailing are required and is suitable for both small and large production runs — requiring some degree of automation to enable larger volumes to be commercially feasible. Investment casting offers a streamlined, automated filling process that reduces errors and the need for extensive post-processing, but this involves a high cost to set up.
- Centrifugal Casting: This involves rotating a mold at speed while pouring molten metal into it. Centrifugal force pushes the metal towards the mold walls, resulting in a denser and more uniform casting. It is often used for cylindrical parts like pipes and tubes.
- Squeeze Casting: This is a hybrid process that combines elements of die casting and forging. Molten metal is poured into a mold cavity, and then pressure is applied to the mold to further compact the metal as it solidifies. This results in improved mechanical properties compared to most other casting methods.
How Xometry Can Help
We hope this article has helped you get a grasp on the gravity die casting process.
If you’re seeking custom die-cast parts, Xometry is happy to work with you on your project! Through our global partner network, we have various die casting capabilities. To learn more about how Xometry can help you with your die casting projects, check out our die casting services page and start a quote today!
Disclaimer
The content appearing on this webpage is for informational purposes only. Xometry makes no representation or warranty of any kind, be it expressed or implied, as to the accuracy, completeness, or validity of the information. Any performance parameters, geometric tolerances, specific design features, quality and types of materials, or processes should not be inferred to represent what will be delivered by third-party suppliers or manufacturers through Xometry’s network. Buyers seeking quotes for parts are responsible for defining the specific requirements for those parts. Please refer to our terms and conditions for more information.
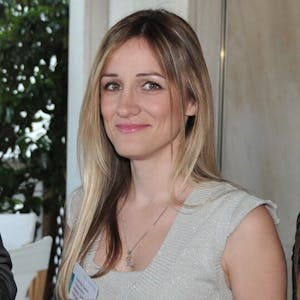