As one of the most popular and commonly used metals in manufacturing, aluminum is loved for its low weight and strength-to-weight ratio. To make aluminum suitable for use in different industries, the metal is combined with other elements to form alloys. Aluminum alloys come in many different forms and are used in all kinds of products, including consumer electronics, packaging, and vehicle and plane parts.
In this article, we’ll look at what an aluminum alloys is, its definition, traits, categories, characteristics, and uses, as well as a little on its history.
What are Aluminum Alloys?
Aluminum is a metal that can be combined with specific amounts of other elements including copper, magnesium, silicon, zinc, and manganese, to alter its mechanical and physical qualities, making it suitable for different applications. This combination makes it an “alloy”. Just as an example, if you mix aluminum with magnesium, you’ll get a strong and lightweight alloy that’s great for use in aerospace and automotive. It has low density, is corrosion resistant, and has good thermal conductivity. Many different items, including metal enclosures, automobiles, and aircraft components, are made from aluminum alloys. Xometry offers many different types of aluminum alloys available for automatic quoting on our platform via our CNC machining, sheet metal fabrication, sheet cutting, and other manufacturing processes. For more information on this versatile metal, have a look at our in-depth guide on Aluminum.
A Brief History of Aluminum Alloys
Naturally occurring compounds that contain aluminum have been known since antiquity, but aluminum’s elemental nature as a metal wasn’t confirmed until 1825 as a result of the combined efforts of German chemist, Friedrich Wöhler, and Danish physicist, Hans Christian Ørsted. It was soon realized that aluminum was a hard material to process, and it was also expensive—at the time, it cost more than gold! The price of aluminum alloy only started to go down in 1856 when Henri Étienne Sainte-Claire Deville, a French chemist, found a way to make it on a large scale. Fifty years later, duralumin (the first structural aluminum alloy with a good amount of strength) was created and developed for military and industrial purposes.
Characteristics of Aluminum Alloys
Aluminum alloys are characterized by several things. Perhaps their most famous attribute is their low weight that makes them ideal for use in areas where reduced weight is important. A natural oxide layer forms on the aluminum alloy’s surface, making it corrosion resistant and keeping it protected in all different environments. In spite of their low density, they are strong and durable, factors that make them useful in projects where strength and weight have to be carefully balanced. They can also be easily shaped and formed, making them a versatile material for those in manufacturing to work with. For example, aluminum 5052 is especially malluable and a popular alloy with our sheet metal customers, where aluminum 6061 is extremely popular for CNC machined parts due to its machinability and balanced characteristics.
Traits can differ greatly from alloy to alloy, so it’s best to refer to the relevant data sheet for precise characteristic information.
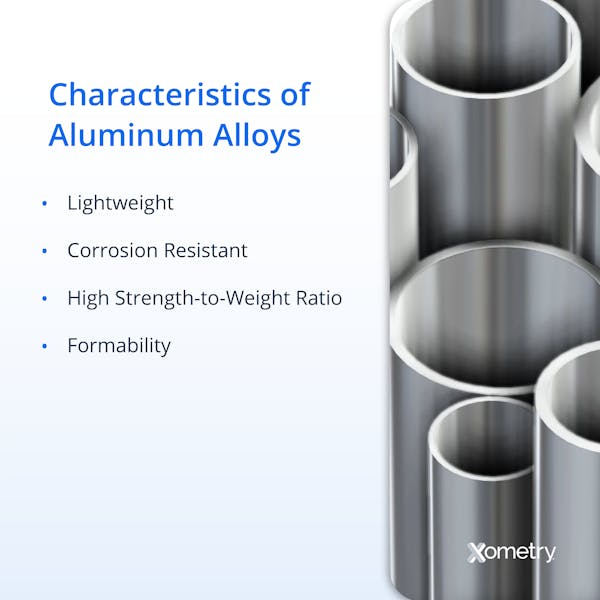
Aluminum characteristics.
Different Types of Aluminum Alloys
Aluminum alloys come in seven different categories, according to their chemical makeup, primary alloying elements, and physical characteristics. These are:
- 1000 Series (Pure)
- 2000 Series (Copper)
- 3000 Series (Manganese)
- 4000 Series (Silicon)
- 5000 Series (Magnesium)
- 6000 Series (Magnesium and Silicon)
- 7000 Series (Zinc)
Here’s a more in-depth look at each of these alloy series.
1000 Series: Pure aluminum makes up at least 99% of the 1000-series alloys’ composition, with only traces of other elements. The precise composition and impurity content of the various alloys in the 1000 series is what differentiates them from one another. These alloys are very thermally conductive, highly ductile, and corrosion-resistant, and are used in products like chemical tanks, conductive bus bars, and rivets.
2000 Series: The primary alloying element in the 2000 series is copper, which provides higher strength, but the exact amount of copper and other trace elements vary from one 2000 series alloy to another. Copper alloys can be machined, heat-treated, and withstand high temperatures. They’re often used in military, aerospace, and other high-performance applications. For more information on this material, see our guide on Copper.
3000 Series: Manganese improves the metal’s corrosion resistance and formability. 3000 series alloys have moderate strength but are not heat-treatable. They are used in cookware, automotive parts, and construction materials, and also work well when welding and anodizing.
4000 Series: Silicon gives this aluminum alloy excellent molten fluidity and minimal shrinkage when it solidifies, making it a great candidate for casting applications. It has good machinability and corrosion resistance and a moderate amount of strength. It is usually used for engine blocks and other auto parts that need to disperse heat efficiently.
5000 Series: The main alloying element in the 5000 series is magnesium. These versions of aluminum can be found in vehicles, pressurized vessels, and bridges. Specifically, aluminum 5052 is a very common choice among our customers for bent sheet metal parts.
6000 Series: Featuring both magnesium and silicon as the main alloying elements, this series of metals offers good strength, resistance to atmospheric corrosion, and are machinable. They are commonly used in structural components for the aerospace, automotive, and construction industries. Aluminum 6061 is one of the most commoditized materials available, making it a popular low-cost choice for machined components.
7000 Series: This is a heat-treatable alloy with zinc and smaller amounts of copper, magnesium, and other elements. It has high strength, good toughness, and fatigue and corrosion resistance. These alloys are used in aircraft and aerospace, as well as in high-performance sporting goods. They can be welded, but care is needed to avoid cracking.
Get Instant Pricing for Custom Aluminum Parts Today!
Properties of Aluminum Alloys
Depending on the alloying element and specific composition, aluminum alloys have different physical and chemical properties. We’ve prepared the below tables to summarize some of these common properties.
Physical Properties of Aluminum Alloys
These are the physical properties of the most common types of aluminum alloys.
Aluminum Alloy Type | Density (g/cm³) | Thermal Conductivity (W/mK) | Electrical Conductivity (%IACS) | Coefficient of Thermal Expansion (10^-6/K) | Specific Heat Capacity (J/kg K |
---|---|---|---|---|---|
Aluminum Alloy Type 1100 | Density (g/cm³) 2.71 | Thermal Conductivity (W/mK) 222 | Electrical Conductivity (%IACS) 61.8 | Coefficient of Thermal Expansion (10^-6/K) 23.6 | Specific Heat Capacity (J/kg K 904 |
Aluminum Alloy Type 2024 | Density (g/cm³) 2.78 | Thermal Conductivity (W/mK) 121 | Electrical Conductivity (%IACS) 49 | Coefficient of Thermal Expansion (10^-6/K) 23.2 | Specific Heat Capacity (J/kg K 875 |
Aluminum Alloy Type 3003 | Density (g/cm³) 2.73 | Thermal Conductivity (W/mK) 190 | Electrical Conductivity (%IACS) 40 | Coefficient of Thermal Expansion (10^-6/K) 23.1 | Specific Heat Capacity (J/kg K 893 |
Aluminum Alloy Type 5052 | Density (g/cm³) 2.68 | Thermal Conductivity (W/mK) 105 | Electrical Conductivity (%IACS) 35 | Coefficient of Thermal Expansion (10^-6/K) 23.8 | Specific Heat Capacity (J/kg K 880 |
Aluminum Alloy Type 6061 | Density (g/cm³) 2.70 | Thermal Conductivity (W/mK) 152 | Electrical Conductivity (%IACS) 43 | Coefficient of Thermal Expansion (10^-6/K) 23.2 | Specific Heat Capacity (J/kg K 897 |
Aluminum Alloy Type 7075 | Density (g/cm³) 2.81 | Thermal Conductivity (W/mK) 130–150 | Electrical Conductivity (%IACS) 37 | Coefficient of Thermal Expansion (10^-6/K) 23.6 | Specific Heat Capacity (J/kg K 714.8 |
Table Credit: https://www.matweb.com/
Aluminum Alloy Type | Composition | Corrosion Resistance | Weldability | Machinability | Anodizing Response |
---|---|---|---|---|---|
Aluminum Alloy Type 1100 | Composition 99.95% Al,
0.05–0.20% Cu,
Iron: 0.95% max. | Corrosion Resistance Good | Weldability Good | Machinability Good | Anodizing Response Poor |
Aluminum Alloy Type 2024 | Composition 93.50% Al,
4.3–4.5% Cu,
0.5–0.6% Mn,
1.3–1.5% Mg | Corrosion Resistance Poor | Weldability Poor | Machinability Good | Anodizing Response Poor |
Aluminum Alloy Type 3003 | Composition 98.60% Al,
1.20% Mn,
0.12 Cu | Corrosion Resistance Good | Weldability Good | Machinability Good | Anodizing Response Poor |
Aluminum Alloy Type 5052 | Composition 97.25% Al,
2.50% Mg,
0.25% Cr | Corrosion Resistance Good | Weldability Good | Machinability Poor | Anodizing Response Good |
Aluminum Alloy Type 6061 | Composition 97.90% Al,
0.60% Si,
1.0% Mg,
0.2% Cr,
0.28% Cu | Corrosion Resistance Good | Weldability Good | Machinability Good | Anodizing Response Good |
Aluminum Alloy Type 7075 | Composition 90.00% Al,
5.60% Zn,
2.50% Mg,
1.60% Cu | Corrosion Resistance Poor | Weldability Poor | Machinability Fair | Anodizing Response Good |
Table Credit: https://www.matweb.com/
Aluminum Alloys—Applications
The excellent characteristics of aluminum alloys, including their low density, high strength, resistance to corrosion, and good formability, make them useful across multiple industries. Here are just a few of the most popular uses for aluminum alloys.
1. Transportation
Since aluminum alloys are light in weight and corrosion resistant, they are a popular option for boats and ships, engine blocks, body panels, and structural components in the railway, automotive, and marine industries.
2. Electrical
Aluminum alloys are often used as conductors in power transmission lines, electrical wires, and electronic components thanks to their low density, as well as in electronic devices due to their excellent heat dissipation and thermal management. Generally speaking, aluminum alloys can make for affordable, durable, and capable electrical components.
3. Consumer Goods
Many consumer goods are made with aluminum alloys, again, thanks to their minimal weight, ability to resist corrosion, durability, strength, and recyclability. Automobile parts, cookware, electronics, and beverage cans are just a few of the products that are usually made of aluminum.
4. Medical Equipment
Many medical devices and equipment need to be made from durable, strong, and corrosion resistant, making aluminum alloys a perfect fit, and commonly used to make wheelchairs, hospital beds, and surgical instruments. As it’s biocompatible, it’s also used in medical implants, like bone plates and screws.
5. Construction
Aluminum alloys are ideal in abrasive outdoor environments because they are strong, lightweight, and resist corrosion. They can be easily formed into a variety of shapes and sizes, giving architects and those in construction a lot of flexibility. They’re used to make windows, doors, roofing, siding, and framing.
Benefits of Aluminum Alloys
Aluminum alloy offers a great many benefits—there must be a good reason for its mass popularity, after all. Aluminum is much lighter than other metals, which makes it ideal for use in applications where low weight is important. Aluminum alloy has a high strength-to-weight ratio, and is much stronger than many other materials of a similar density. They’re great for marine and industrial settings, or other harsh environments, as they have excellent corrosion resistance. Most are also highly ductile, allowing them to be easily shaped without breaking or cracking. Finally, aluminum alloys make good thermal conductors as they can efficiently transfer heat.
Limitations of Aluminum Alloys
It’s worth noting that aluminum alloys do have some limitations. For one, they have a lower melting point than most other structural metals, which means they won’t be the best fit for high-temperature tasks. They’re not as hard as other metals, so won’t likely survive as much wear and tear. Certain alloys can also be quite expensive, so they might not be as cost-effective as other materials in certain situations.
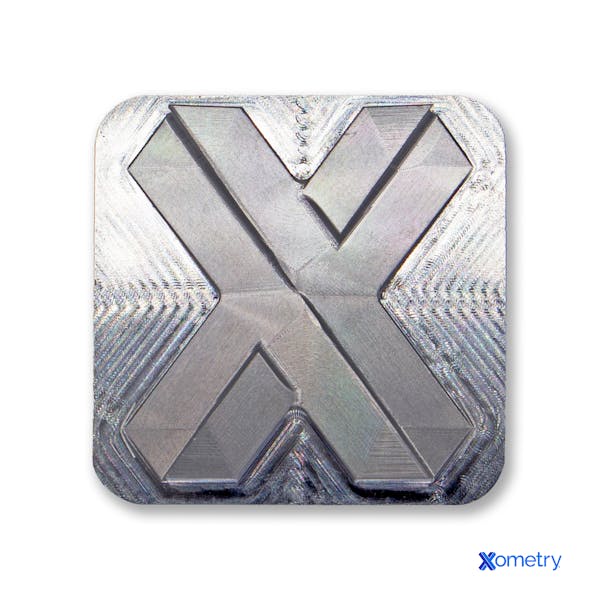
Xometry X-Tile CNC Machined from Aluminum 6061.
Aluminum Alloy—Summary
This article offered an in-depth look at aluminum alloys, what they are exactly, their pros and cons, the different types of aluminum alloys available, and their various applications and benefits.
At Xometry, we offer a wide range of aluminum alloys, from the 1000 series up to the 7000 series. You can get an instant quote for custom parts made from these and many other alloy materials directly in the Xometry Instant Quoting Engine® today! Just upload your CAD to get your instant quote.
Disclaimer
The content appearing on this webpage is for informational purposes only. Xometry makes no representation or warranty of any kind, be it expressed or implied, as to the accuracy, completeness, or validity of the information. Any performance parameters, geometric tolerances, specific design features, quality and types of materials, or processes should not be inferred to represent what will be delivered by third-party suppliers or manufacturers through Xometry’s network. Buyers seeking quotes for parts are responsible for defining the specific requirements for those parts. Please refer to our terms and conditions for more information.
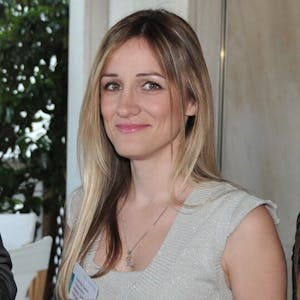