NADCAP (National Aerospace and Defense Contractors Accreditation Program) is a unique industry-managed program that evaluates and accredits specialized processes used in the manufacturing, testing, and maintenance of aerospace and defense components and systems. This program brings together technical experts from prime contractors, suppliers, and government representatives to establish unified requirements for approving suppliers. NADCAP certification is often required by major aerospace and defense contractors and by government agencies when selecting suppliers.
In this article, we will explore the importance of NADCAP certification in the aerospace and defense industries. We will discuss the benefits of NADCAP certification for companies, including operational improvements, market recognition, and customer trust. Additionally, we will examine the industries and companies for which NADCAP certification is relevant and the specific areas of evaluation and accreditation covered under the program.
What Is NADCAP Certification?
NADCAP certification is a global accreditation program designed to ensure the quality, reliability, and consistency of products and services provided by suppliers in the aerospace and defense industries. NADCAP certification is granted to suppliers who demonstrate compliance with specific industry standards and requirements. The certification is awarded by the Performance Review Institute (PRI), an independent organization that administers NADCAP.
The NADCAP certification process involves a thorough audit of a supplier's manufacturing processes, equipment, personnel, and quality management systems. The audit is conducted by qualified experts who assess the supplier's ability to meet the stringent requirements of the respective industries. The areas typically covered in the audit include materials testing, heat treating, chemical processing, nondestructive testing, and other specialized processes relevant to the industry.
By obtaining NADCAP certification, suppliers demonstrate their commitment to maintaining high standards of quality, safety, and reliability in their products and services. This certification is highly regarded in the aerospace and defense sectors and is often a prerequisite for doing business with major companies in these industries. It helps suppliers differentiate themselves, gain credibility, and expand their market opportunities within the aerospace, defense, and related sectors.
For Which Industries and Companies Is NADCAP Relevant?
NADCAP is primarily relevant to the aerospace and defense industries. It is designed to ensure the quality and reliability of products and services within these sectors. The program focuses on specialized processes used in the manufacturing, testing, and maintenance of aerospace and defense components and systems.
Types of NADCAP Certifications
The following are types of NADCAP certifications:
- Aerospace Quality Systems (AQS): Focuses on ensuring that aerospace suppliers have effective quality management systems in place. It verifies compliance with industry-specific standards like AS/EN9110 and AS/EN/JISQ9100, which encompass various quality control aspects, document control, risk management, and continuous improvement processes. ISO 17025 accreditation is also applicable to testing laboratories, including those conducting nondestructive testing. Additionally, the ISO 17025 accreditation must be obtained from an approved NACLA (National Cooperation for Laboratory Accreditation) or ILAC (International Laboratory Accreditation Cooperation) accreditation body. AQS certification is relevant for companies involved in the design, manufacturing, and supply of aerospace products and services.
- Aerostructure Assembly (ASA): This is specific to companies engaged in the assembly and integration of aerospace structures. It covers processes related to the assembly, joining, bonding, and installation of structural components such as airframes and fuselages.
- Chemical Processing (CP): Focuses on ensuring proper handling, treatment, and application of chemicals in aerospace manufacturing. It includes processes like surface treatment, plating, chemical cleaning, anodizing, and conversion coating. CP certification is relevant for suppliers providing chemical processing services to the aerospace industry, ensuring adherence to strict quality and safety standards.
- Coatings (CT): This pertains to the application of protective and functional coatings on aerospace components. It covers various coating techniques such as painting, powder coating, thermal spray, and surface modification. CT certification is essential for suppliers involved in coating processes for aerospace parts and equipment, ensuring high-quality and durable coatings.
- Composites (COMP): Focuses on the manufacturing and processing of composite materials in the aerospace industry. It encompasses processes such as lay-up, curing, bonding, and machining of composite structures. COMP certification is relevant for suppliers engaged in the production and assembly of composite components used in aerospace applications, ensuring compliance with strict quality standards for composites.
- Conventional Machining as a Special Process (CMSP): This is specific to the machining of aerospace components using conventional machining techniques like milling, turning, drilling, and grinding. It ensures that suppliers have the necessary equipment, processes, and controls in place to meet aerospace requirements for precision machining. CMSP certification demonstrates the supplier's capability to consistently deliver high-quality machined components.
- Elastomer Seals (SEAL): This is for suppliers involved in the manufacturing and testing of elastomeric seals used in aerospace applications. It focuses on the material properties, design, manufacturing processes, and performance characteristics of elastomer seals. SEAL certification ensures that suppliers produce reliable and compliant elastomeric seals for aerospace use.
- Electronics (ETG): Pertains to the manufacturing, assembly, and testing of electronic components and systems used in aerospace applications. It ensures compliance with industry standards and specifications for electronic manufacturing, such as IPC-A-610. ETG certification is relevant for suppliers involved in electronics manufacturing for the aerospace industry, ensuring the production of reliable and high-quality electronic components.
- Fluids Distribution (FLU): Focuses on the design, installation, maintenance, and testing of fluid distribution systems in aerospace applications. It covers areas such as fuel systems, hydraulic systems, lubrication systems, and associated components. FLU certification is relevant for suppliers involved in the manufacturing and installation of fluid distribution systems, ensuring the safety and reliability of these critical systems.
- Heat Treating (HT): Specific to companies providing heat treatment services for aerospace materials. It ensures compliance with industry standards and specifications for heat treatment processes, including techniques like annealing, quenching, tempering, and stress relieving. HT certification is relevant for suppliers engaged in heat treatment operations for aerospace components. It demonstrates their ability to perform heat treatment processes with precision, consistency, and in accordance with industry requirements.
- Materials Testing Laboratories (MTL): Applicable to testing laboratories involved in the evaluation and analysis of materials used in the aerospace industry. It covers a wide range of testing techniques, including mechanical testing, chemical analysis, metallurgical evaluation, nondestructive testing, and more. MTL certification ensures that testing laboratories possess the necessary expertise, equipment, and quality control measures to accurately assess material properties and performance.
- Measurement & Inspection (M&I): Focuses on ensuring the accuracy and reliability of measurement and inspection techniques in the aerospace industry. It includes dimensional inspection, metrology, calibration, and adherence to standards such as ASME Y14.5 and ISO 17025. M&I certification is relevant for suppliers involved in measurement and inspection activities, ensuring the precision and traceability of measurements and inspection documentation.
- Metallic Materials Manufacturing (MMM): Pertains to the manufacturing and processing of metallic materials used in the aerospace industry. It encompasses various processes such as casting, forging, heat treatment, and machining of metallic components. MMM certification ensures that suppliers meet the stringent requirements for producing high-quality metallic materials that meet aerospace specifications and performance criteria.
- Nonconventional Machining and Surface Enhancement (NMSE): Focuses on specialized machining and surface treatment techniques used in the aerospace industry. It includes processes like electrochemical machining, laser machining, abrasive flow machining, shot peening, and surface coatings. NMSE certification verifies a supplier's capability to perform nonconventional machining and surface enhancement operations with precision and compliance.
- Nondestructive Testing (NDT): Specific to companies involved in conducting nondestructive testing methods such as ultrasonic testing, radiography, magnetic particle inspection, eddy current testing, and liquid penetrant inspection. NDT plays a crucial role in detecting flaws, defects, and irregularities in aerospace components without causing damage. NDT certification ensures that suppliers have qualified personnel, proper equipment, and robust processes to perform reliable nondestructive testing.
- Nonmetallic Materials Manufacturing (NMMM): Focuses on the manufacturing and processing of nonmetallic materials used in aerospace applications. It includes materials like composites, plastics, elastomers, and ceramics. NMMM certification ensures that suppliers meet the stringent requirements for producing nonmetallic materials that meet aerospace standards in terms of performance, durability, and safety.
- Nonmetallic Materials Testing (NMMT): Applicable to testing laboratories specializing in the evaluation and analysis of non-metallic materials used in the aerospace industry. It covers a range of testing techniques specific to nonmetallic materials, such as mechanical testing, chemical analysis, thermal analysis, and environmental testing. NMMT certification verifies the competency and reliability of testing laboratories in assessing nonmetallic material properties.
- Sealants (SLT): For suppliers involved in the manufacturing, application, and testing of sealants used in aerospace applications. It focuses on the material properties, application methods, and performance characteristics of sealants used for sealing joints, gaps, and interfaces. SLT certification ensures that suppliers produce reliable and compliant sealants that meet the stringent requirements of the aerospace industry.
- Welding (WLD): Focuses on the welding processes used in the aerospace industry. It ensures that suppliers have the necessary capabilities, procedures, and controls in place to perform welding operations on aerospace components. WLD certification covers various welding techniques such as gas tungsten arc welding (GTAW), gas metal arc welding (GMAW), resistance welding, and more. It verifies the supplier's competence in producing high-quality welds that meet the stringent requirements for strength, durability, and integrity in aerospace applications.
What Are the NADCAP Audit Criteria?
Specific NADCAP audit criteria may vary depending on the process being evaluated and any specific customer or industry requirements. The Performance Review Institute (PRI), which administers the NADCAP program, provides detailed checklists and guidelines for each step, to ensure consistency and thoroughness in the audit process. The following are the 17 Special Processes along with the industry standards or audit criteria used to demonstrate compliance in each task group:
- Aerospace Quality Systems: AS/EN/JISQ9100 and AS/EN9110 standards
- Chemical Processing: AC7108 series of checklists
- Coatings: AC7109 series of checklists
- Composites: AC7118 series of checklists
- Conventional Machining as a Special Process: AC7126 series of checklists
- Elastomer Seals: AC7115 series of checklists
- Electronics: AC7119, AC7120, and/or AC7121 series of checklists
- Fluid Distribution Systems: AC7112 series of checklists
- Heat Treating: AC7102 series of checklists
- Materials Testing Laboratories: AC7101 series of checklists
- Measurement & Inspection: AC7130 series of checklists
- Nondestructive Testing: AC7114 series of checklists
- Nonconventional Machining and Surface Enhancement: AC7116 checklist for nonconventional machining and AC7117 checklist for shot peening
- Nonmetallic Materials Manufacturing: AC7124 series of checklists
- Nonmetallic Materials Testing: AC7122 series of checklists
- Sealants: AC7200/1 and AC7202 series of checklists
- Welding: AC7110 series of checklists
Specific checklists are available on eAuditNet for each accreditation area. Depending on the subprogram and your specific processes, additional checklists may apply.
In terms of the accreditation process, if an acceptable quality system approval is already in place, it is important to provide this information when requesting an audit. If you don't have a quality system approval yet, AC7004 (aerospace quality systems) or AC7006 (for laboratories) will be added to the standard accreditation process. AS9100, AS9120, and AS9110 are important standards related to quality management systems in the aerospace industry, each with specific requirements for different aspects of the industry.
The NADCAP Audit and Accreditation Process
At the supplier's request, PRI (Performance Review Institute) schedules audits and assigns auditors approved by the industry to conduct NADCAP audits based on established and agreed-upon industry standard checklists. If any nonconformances are identified during the audit process, a nonconformance report is issued, and PRI manages the closure of these reports.
Upon completion of the audit, the audit package is presented to a special process task group, which consists of industry members. This task group reviews the audit findings and votes on the acceptability of the package for approval. Once all nonconformances have been addressed and closed, accreditation is granted.
The overall NADCAP process can be summarized in the following steps:
- Submit an application to NADCAP, indicating the specific process or processes for which accreditation is sought. This involves providing detailed information about the company, its capabilities, and the scope of work.
- Prime contractors and suppliers agree on the core audit criteria that suppliers must meet for NADCAP accreditation.
- Prime contractors include NADCAP accreditation as a requirement for supplier approval, making it necessary for suppliers to seek accreditation.
- Accreditation-seeking suppliers schedule and pay for their special process audits.
- PRI contracts with industry-approved auditors who conduct on-site audits using approved checklists managed by the industry.
- The auditors document their findings, including any nonconformances or areas for improvement. These findings are communicated to the company, providing an opportunity to address and resolve identified issues.
- The company is responsible for implementing corrective actions to address any identified non-conformances. These actions aim to resolve deficiencies and bring the processes in line with the required standards.
- The auditors review the company's corrective actions to determine if they are satisfactory and effective in addressing the identified issues. This may involve additional documentation or evidence provided by the company.
- Following the completion of the on-site audit and the submission of corrective actions by the company, the audit findings and associated documentation are reviewed by PRI staff members. This review is conducted to ensure consistency and accuracy in the audit process and to validate the effectiveness of the corrective actions implemented.
- The PRI staff members evaluate the audit findings, corrective actions, and supporting evidence provided by the company. They assess whether the nonconformances have been adequately addressed and whether the company's processes align with the required standards.
- Based on the PRI staff review, a final decision regarding accreditation is made. If the company's corrective actions are deemed satisfactory and the processes meet the necessary standards, NADCAP accreditation for the specific process or processes is granted. The company is officially recognized as meeting the industry's stringent requirements.
- Accreditation is not a one-time event. NADCAP conducts regular surveillance audits to ensure ongoing compliance and to monitor the company's adherence to the established standards. These surveillance audits may occur annually or at defined intervals.
How to Prepare for an Audit?
NADCAP makes the audit process very easy. They offer multiple sources of information relating to the process, some of which are listed below:
- Audit Check Sheets: All of the relevant audit check sheets and reference material are made available before the audit via the eAuditNet portal. A partial list of these special processes is shown in Table 1. Additional checklists relating to sub-processes may also be applicable.
- Pre-Assessment Audit: A pre-assessment audit can be requested to help the supplier identify any non-conformances that they may have missed in their internal preparation process.
- Training: NADCAP offers training that covers a range of topics, including root cause corrective action, how to prepare for an audit, and how to implement an efficient internal audit process.
List of NADCAP Auditable Special Processes
Number | Special Process | Relevant Standard/Checklist |
---|---|---|
Number 1 | Special Process Aerospace Quality Systems Standard | Relevant Standard/Checklist AS/EN/JISQ9100, ISO 17025 |
Number 2 | Special Process Chemical Processing | Relevant Standard/Checklist AC7108 |
Number 3 | Special Process Coatings | Relevant Standard/Checklist AC7109 |
Number 4 | Special Process Composites | Relevant Standard/Checklist AC7118 |
Number 5 | Special Process Conventional Machining as a Special Process | Relevant Standard/Checklist AC7126 |
Number 6 | Special Process Elastomer Seals | Relevant Standard/Checklist AC7115 |
Number 7 | Special Process Electronics | Relevant Standard/Checklist AC7119, AC7120/AC7121 |
Number 8 | Special Process Fluid Distribution Systems | Relevant Standard/Checklist AC7112 |
Number 9 | Special Process Heat Treating | Relevant Standard/Checklist AC7102 |
Number 10 | Special Process Materials & Testing Laboratories | Relevant Standard/Checklist AC7101 |
Number 11 | Special Process Measurement & Inspection | Relevant Standard/Checklist AC7130 |
Number 12 | Special Process Non-Metallic Materials Testing | Relevant Standard/Checklist AC7122 |
Number 13 | Special Process Non-Metallic Materials Manufacturing | Relevant Standard/Checklist AC7124 |
Number 14 | Special Process Non-Destructive Testing | Relevant Standard/Checklist AC7114 |
Number 15 | Special Process Non-Conventional Machining & Surface Treatment | Relevant Standard/Checklist AC7116, AC7117 |
Number 16 | Special Process Sealants | Relevant Standard/Checklist AC7200/1, AC7202 |
Number 17 | Special Process Welding | Relevant Standard/Checklist AC7110 |
List of Nadcap auditable special processes with the corresponding standards from the eAuditNet portal.
What Are the Benefits of NADCAP Certification?
Obtaining NADCAP certification offers several benefits to companies in terms of operational improvement, market recognition, and customer trust. The certification process allows companies to gain valuable insights and enhance their work practices. By undergoing NADCAP audits, companies can identify areas for improvement and receive acknowledgment for their existing strengths. This evaluation, combined with input from a global network of technical experts, contractors, suppliers, and government representatives, helps companies assess outdated processes, streamline workflows, and prioritize key process indicators.
When Are NADCAP Certifications Required?
NADCAP certifications are typically required in the aerospace and defense industries for suppliers who provide products or services to major aerospace and defense contractors. The specific instances when NADCAP certifications are required can vary depending on customer requirements, contractual obligations, and industry standards. Some common scenarios where NADCAP certifications may be necessary are: customer requirements, prime contractor requirements, government contracts, and industry standards and specifications.
What Accrediting Body Issues NADCAP Certifications?
NADCAP certifications are issued by the Performance Review Institute (PRI), an independent organization responsible for managing the NADCAP program. PRI is a global provider of accreditation and certification services, specializing in industries such as aerospace, defense, and related sectors.
As the governing body for NADCAP, PRI oversees the entire certification process, including application review, audit planning, on-site audits, evaluation of findings, corrective action verification, and accreditation decision-making. They ensure that the NADCAP program operates in accordance with industry standards, best practices, and customer requirements.
Certifications and Accreditations Similar to NADCAP
While NADCAP (National Aerospace and Defense Contractors Accreditation Program) is a widely recognized and industry-specific accreditation program, there are several other certifications and accreditations that are relevant to various industries. Some similar certifications and accreditations include:
- ISO 9001: This is a globally recognized quality management system standard applicable to organizations across all industries. ISO 9001 focuses on ensuring consistent quality of products and services, customer satisfaction, and continuous improvement. While it is not specific to aerospace and defense, ISO 9001 certification is often a prerequisite for NADCAP accreditation.
- AS9100: AS9100 is an aerospace-specific quality management system standard based on ISO 9001. It incorporates additional requirements specific to the aerospace industry, including regulatory compliance, risk management, configuration management, and supply chain controls. AS9100 certification is highly valued in the aerospace and defense sectors.
- ISO/IEC 17025: This accreditation is for testing and calibration laboratories. ISO/IEC 17025 sets out criteria for competency, impartiality, and consistent operation of laboratories. It ensures the accuracy and reliability of test results and calibration data. This accreditation is relevant for laboratories providing services in areas such as materials testing, chemical analysis, and nondestructive testing.
- ITAR (International Traffic in Arms Regulations) Compliance: ITAR is a set of regulations enforced by the United States government on the export and import of defense-related articles and services. ITAR compliance certification is essential for companies involved in the manufacture, export, or transfer of defense articles and services.
These are just a few examples of certifications and accreditations similar to NADCAP that are relevant to industries worldwide.
Summary
This article presented the NADCAP certification, explained it, and discussed its audit and accreditation process. To learn more about certifications, contact a Xometry representative.
Xometry provides a wide range of manufacturing capabilities and other value-added services for all of your prototyping and production needs. Visit our website to learn more or to request a free, no-obligation quote.
Disclaimer
The content appearing on this webpage is for informational purposes only. Xometry makes no representation or warranty of any kind, be it expressed or implied, as to the accuracy, completeness, or validity of the information. Any performance parameters, geometric tolerances, specific design features, quality and types of materials, or processes should not be inferred to represent what will be delivered by third-party suppliers or manufacturers through Xometry’s network. Buyers seeking quotes for parts are responsible for defining the specific requirements for those parts. Please refer to our terms and conditions for more information.
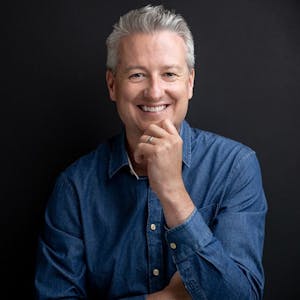