As one of the most popular manufacturing techniques for mass production, plastic injection molding can be used with many different thermoplastics to make parts with complicated designs that would be nearly impossible to create with any other method. If you’d like to know how it works and how it measures up to 3D printing, keep on reading.
How it Works
Before we go into the ins and outs of the injection molding process, you’ll first need to know about the machine’s various components and what they do.
Components
All the important parts of an injection molding machine are shown in the image below, with descriptions of each in the table further down.
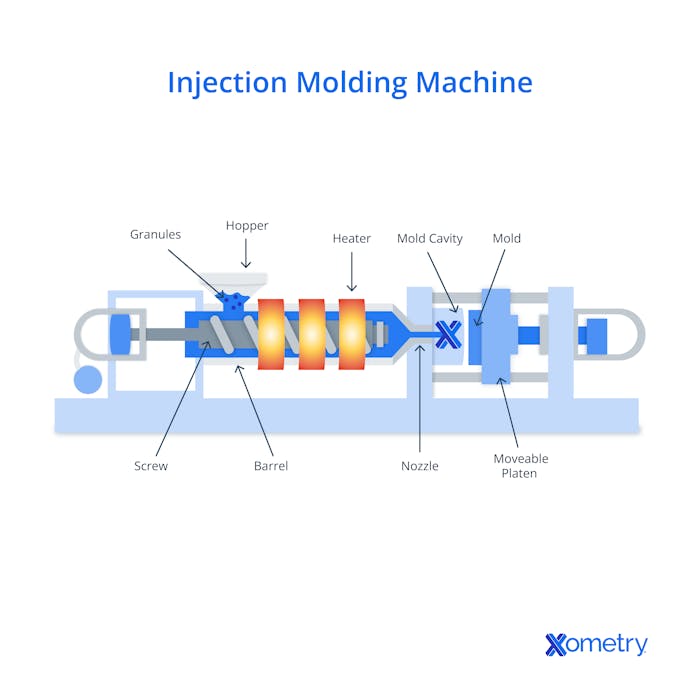
Part | Location | Job | Appearance |
---|---|---|---|
Part Barrel | Location In the middle of the machine, houses reciprocating screw | Job Holds, melts, and mixes plastic pellets, ensuring uniformity and maintaining pressure during injection | Appearance Long cylindrical tube wrapped in heater bands, with a heated nozzle tip |
Part Gates | Location Between runners and mold cavity | Job Control the flow of molten plastic into the cavity | Appearance Small openings |
Part Heaters | Location Outside the barrel | Job Provide thermal energy to melt the pellets, control the temperature in the barrel | Appearance Metal bands around the barrel |
Part Hopper | Location Top of the machine, near the barrel | Job Feeds material into the barrel, sometimes includes a dryer to remove moisture that could damage parts | Appearance Funnel-shaped opening |
Part Mold | Location Attached to the stationary and movable platens | Job Shapes the molten plastic into the final part | Appearance Metal block, typically two halves (stationary and movable), includes the mold cavity, ejector pins, cooling channels, and vents |
Part Mold Cavity | Location Inside the mold | Job Creates the final shape of the molded part, has vents for good airflow, and lets air escape | Appearance Hollow space shaped like the desired part includes runners, sprues, gates, and vents |
Part Movable platen | Location Linked to the core of the mold | Job Moves to clamp the mold halves tightly and release the core when the part is done | Appearance Flat, rectangular metal plate |
Part Nozzle | Location At the end of the barrel, facing the mold | Job Directs molten plastic into the mold cavity, prevents it from cooling as it enters sprues and runners | Appearance Tapered, heated outlet |
Part Pellets | Location Inside the hopper and barrel | Job Raw plastic material for molding, commonly thermoplastics like ABS, PP, or nylon, and sometimes with dyes and/or other additives | Appearance Small, plastic granules of the same size |
Part Reciprocating screw | Location Inside the barrel | Job Mixes, compresses, and forces the pellets through the barrel as they melt, pulls back to allow more material in for the next cycle | Appearance Corkscrew-shaped rod |
Part Runners | Location Channels within the mold | Job Direct molten plastic from the sprue to the gates for even flow and minimal waste, often removed after molding | Appearance Long, narrow pathways |
Part Sprue | Location Central channel that connects the nozzle to the runners, the entry point of molten plastic | Job Guides molten plastic from the nozzle to the runner | Appearance Cone-shaped channel |
Injection Molding Machine Components
The Process
Plastic injection molding uses thermoplastic pellets, which need to be melted first. These are fed into the hopper and make their way to the barrel, where the reciprocating screw pulls back to make room for them to get through. The screw then goes forward again to force the plastic through the nozzle. The pressure from the platen makes sure that no plastic can get away by bringing the nozzle and mold closely together tightly. Here, the melted plastic is pressurized, something that makes it go into all the mold cavity’s parts, taking up the space that the air previously occupied. As the plastic fills every single crevice (including the sprues and their buddies, runners, and gates), the air that was in that empty space now comes out of the mold vents.
The mold has to stay steadily at a temperature that aligns with the specific material’s melting point so that the part inside can cool and harden evenly. In addition, the holding pressure also has to be constant so that there’s no backflow of material into the barrel. This also keeps the shrinking under control. More pellets are then put in the hopper so there’s no downtime—once the part is cooled and taken out, it’ll be ready to go again. The platen opens when it’s time to eject your creation, and the screw does its job again—allowing room for material before pushing it through… it basically works like this on a loop.
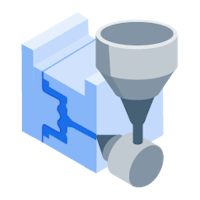
FREE Injection Molding Principles E-Book
Getting Started
Before you see all your wonderful products being made, you need to take care of two important things: your mold design and the actual mold.
Design
First things first, your product needs to be designed. This is typically done as a CAD file or other transferable format, and you’ll follow the necessary design guidelines for the particular injection molding process you’re using. For the best chance of success with injection molding your plastic parts, try to include features like bosses for threaded inserts or fasteners, hollow cavities for thicker sections, rounded edges, ribbed supports for extra strength, snap-fit joints, or friction fits as joining features, living hinges where you need some flexibility, and draft angles on vertical walls. You’ll also want to make sure that wall thicknesses are consistent (or as much as possible) and avoid features that can lead to defects. These include overly thin/thick walls, sudden changes to the shape, i.e., sharp corners, randomly placed holes, badly designed ribbing, and undercuts or overhangs.
Tooling mold
The tooling mold is undoubtedly the star of the show in the whole injection molding process. Making this, however, is no walk in the park—it’s the longest and most expensive part of the whole process and needs to be done by professional machinists who know exactly what they are doing. Based on your design, these experts craft the “tool” (that’s what those in the know call a tooling mold), then make their own blueprint that has all the necessities (cavity, sprues, gates, ejector systems, etc.). If you think that you’ll get your mold on next-day delivery, think again; the process of making the mold (including approvals) can take 20 weeks… sometimes more! So imagine how long you’ll have to wait (and how much it’ll cost) if you need to make changes to the mold… Suffice it to say, it’s important to get the design right before handing it over.
Material | Resistant to | Not Resistant to | Characteristics/Applications |
---|---|---|---|
Material Polypropylene (PP) | Resistant to Chemicals, moisture, fatigue, moderate impact, moderate heat (100–120°C) | Not Resistant to UV light, high heat | Characteristics/Applications Moderate strength, lightweight, flexible; containers, automotive parts, textiles |
Material High-density polyethylene (HDPE) | Resistant to Chemicals, moisture, weather, high impact, moderate heat (70–120°C) | Not Resistant to UV light, high heat | Characteristics/Applications Tough, fairly hard, durable; pipes, bottles, and toys |
Material Polystyrene (PS) | Resistant to Stiffness, machinability | Not Resistant to Impact, chemicals, low heat (<100°C) | Characteristics/Applications Brittle, clear or opaque, easy to mold; packaging, disposable cups, and insulation |
Material Polyethylene (PE) | Resistant to Chemicals, moisture, high impact, low to moderate heat (70–120°C) | Not Resistant to UV light, high heat | Characteristics/Applications Tough, flexible; bags, containers, and insulation |
Material High-impact polystyrene (HIPS) | Resistant to Moderate impact, machinability, low to moderate heat (<100°C) | Not Resistant to UV light, high heat, solvents | Characteristics/Applications Moderately strong, tough, versatile; signs, toys, and casings |
Material Polyvinyl chloride (PVC) | Resistant to Chemicals, flame, moderate impact, moderate heat (60–82°C) | Not Resistant to High heat, solvents | Characteristics/Applications Fairly tough, rigid, durable; pipes, flooring, and cables |
Material Acrylic (PMMA) | Resistant to UV light, weathering, scratches | Not Resistant to Impact, chemicals, low to moderate heat (~100°C) | Characteristics/Applications Fair strength, brittle, transparent; lenses, windows, and displays |
Material Acrylonitrile butadiene styrene (ABS) | Resistant to Impact, chemicals, moderate heat (100–110°C) | Not Resistant to UV light, solvents | Characteristics/Applications Tough, machinable; car parts, toys, and casings |
Material Polycarbonate (PC) | Resistant to High impact, UV light, high heat (~135°C) | Not Resistant to Abrasion, solvents | Characteristics/Applications High toughness, hard, transparent; eyewear, electronics, and automotive parts |
Material Nylon (PA) | Resistant to Wear, fatigue, moderate impact, moderate to high heat (120°C) | Not Resistant to Moisture, acids | Characteristics/Applications High strength, tough, low friction; gears, bearings, and textiles |
Material Polyurethane (TPU) | Resistant to Abrasion, fatigue, moderate impact | Not Resistant to Heat (>80°C), chemicals | Characteristics/Applications Very flexible; seals, wheels, and footwear |
Material Polyetherimide (PEI) | Resistant to Heat (170–200°C), chemicals, low to moderate impact | Not Resistant to Impact | Characteristics/Applications Strong, rigid; aerospace components, medical devices |
Material Polyether ether ketone (PEEK) | Resistant to Heat (260°C), chemicals, low to moderate impact | Not Resistant to UV light | Characteristics/Applications High strength, rigid; aerospace parts, medical implants |
Material Polyphenylene sulfide (PPS) | Resistant to Chemicals, heat (280°C), low to moderate impact | Not Resistant to Impact | Characteristics/Applications Moderate strength, hard, dimensionally stable; electrical components |
Injection Molding Compatible Materials
FAQs About Injection Molding
How do I choose the best plastic for the process?
With the thousands of options on the market, it can be hard to choose the right one for your needs. Many of these won’t even work for the intended purpose, so you’ll need to do some research. To narrow down the list of potential materials, you’ll need to consider:
- The part’s intended use and the stresses it will face (this will also tell you what mechanical and chemical properties it will need)
- The part’s aesthetics and how long you want it to last you overall
- Your personal budget
- The material’s reaction to air, chemicals, heating/cooling, other plastics, etc.
The material you choose will also depend on the product, i.e., its intended use and how complex the design is. If your part is structural and needs to be resistant to various things like chemicals and harsh environments, look to PEEK and Nylon. On the other hand, if the product will have some bendier bits, PP will provide both strength and flexibility.
What material can the mold be made from?
Considering that these molds need to potentially withstand upwards of 100,000 of these heavy-duty cycles, they’ll need to be made from capable and hardy materials. The most common metals that can withstand the task are aluminum (6063), steel (P20, H13), and stainless steel (420).
How do plastic injection molding and 3D printing differ?
While they’re both useful additive manufacturing processes, 3D printing and injection molding are very different in many aspects. 3D printing makes the part, the design of which is uploaded to the machine with a special program, one layer at a time by depositing the filament or resin. In injection molding, the melted plastic is pushed or injected at high pressure into the cavity of the mold, and it makes the product all in one go. Here are some more of their differences:
3D Printing
- Supports for overhangs and voids are printed with the part, as well as additional features to reduce warping/defects
- A long process, taking a minimum of several hours (sometimes days)
- Can be used with thermoplastics, thermosets, impregnated plastics, ceramic powder, and metal/alloy powder
- Medium to high initial investment cost, medium to high cost per part
- Able to make 1-10 parts per day, with fast overall lead times
- Build space is restricted, so can only make parts no bigger than a cubic meter
- High waste output
- Very easy, rapid design changes are possible
Plastic Injection Molding
- Molds come out with suitable surface quality, ready for application
- Works with mainly thermoplastics (though newer processes can accept thermosets, impregnated materials, some metal powders, and some types of ceramics)
- High initial investment cost, low cost-per-part
- Can make 1,000s–10,000s parts a day, with slow initial lead times for mold creation but fast production lead times
- Both very small and large parts can be made
- Low to no waste, and waste can be reground back into stock
- It’s hard to make design changes, and it takes a long time
How Xometry Can Help
We hope this article answers all your questions on this manufacturing process, but if you have any more, please reach out to one of our representatives. Xometry offers a full range of injection molding capabilities to help with your production needs. You can get started today by uploading your designs to the Xometry Instant Quoting Engine® to get your free, no-obligation quote.
Disclaimer
The content appearing on this webpage is for informational purposes only. Xometry makes no representation or warranty of any kind, be it expressed or implied, as to the accuracy, completeness, or validity of the information. Any performance parameters, geometric tolerances, specific design features, quality and types of materials, or processes should not be inferred to represent what will be delivered by third-party suppliers or manufacturers through Xometry’s network. Buyers seeking quotes for parts are responsible for defining the specific requirements for those parts. Please refer to our terms and conditions for more information.
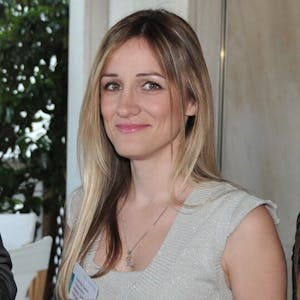