Injection molding is a manufacturing process that produces plastic components. It is a popular method for low-volume production, pilot-run, and prototyping of designs. Injection molding has two main types of mold designs: hot runner and cold runner. A hot runner mold uses a heated runner to transfer molten thermoplastic or polymer to the mold cavity where the final product takes on its shape. A cold runner mold uses an unheated runner channel to transfer the molten material from the machine nozzle to the mold cavity.
While these two methods both produce plastic parts, hot runner mold and cold runner mold systems differ in terms of cost, speed, and accuracy of the molded parts. Hot runner molds are more expensive to set up and maintain than their cold runner counterparts. But, hot runner molds produce parts with a higher degree of tolerance and have a shorter lead time. A cold runner mold, on the other hand, is more affordable and works with a vast array of thermoplastic materials including heat-sensitive types.
This article will compare hot runner vs. cold runner, examine their advantages and disadvantages, as well as discuss the alternatives to both. Both setups are shown in the figure below:
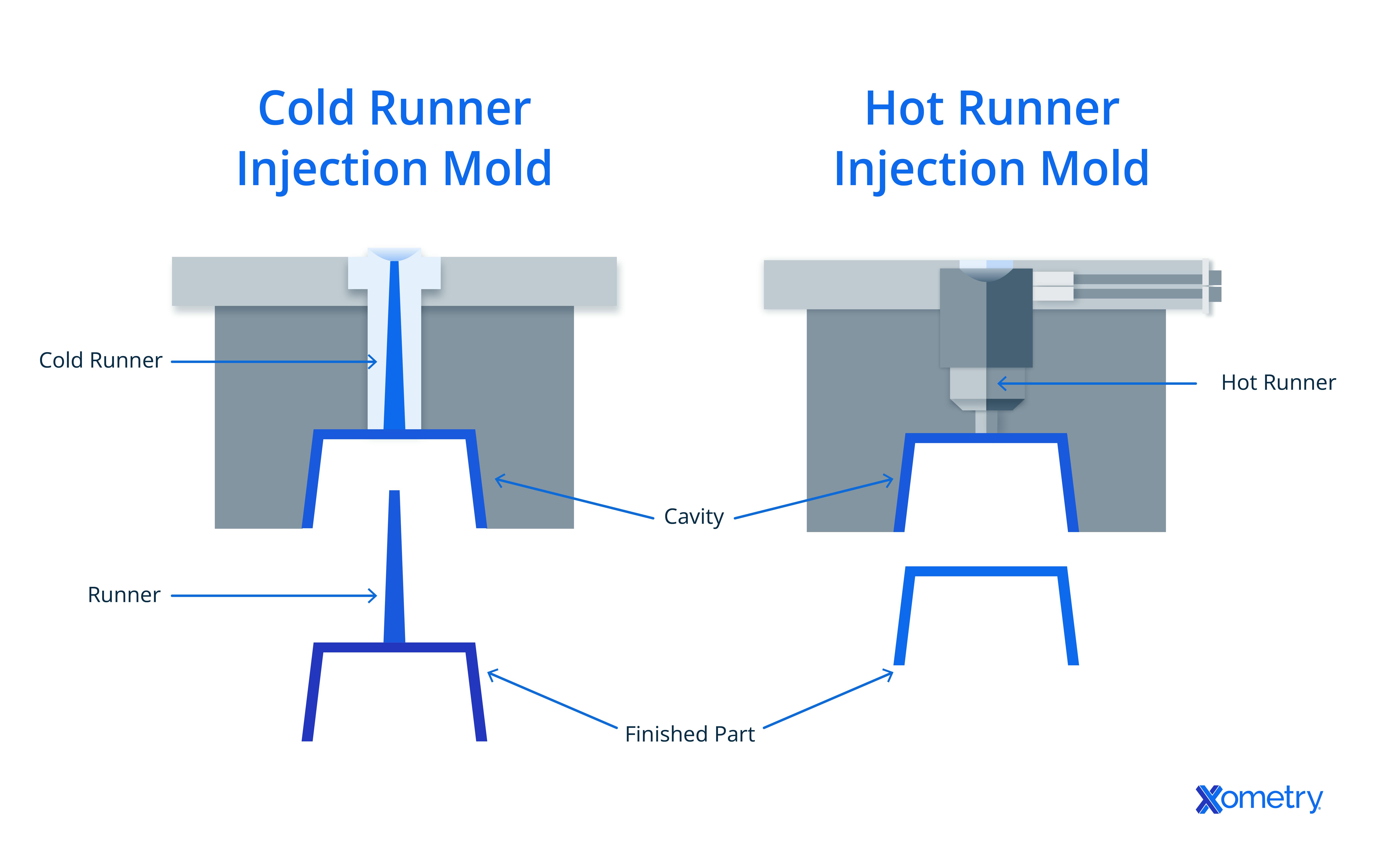
Hot Runner Definition and Comparison to Cold Running Molds
A hot runner is an injection molding system that utilizes a manifold as the heating element. It was first manufactured and commercialized by Mold-Masters Ltd in 1963. The runner, which is made up of two plates, is heated along with the molten thermoplastic. As the molten plastic flows through the runner, the manifold ensures uniformity in the temperature of the heating cylinder and the runner. The molten plastic is fed to the nozzle, which in turn fills the mold cavity. Afterward, the molded plastic is ejected free of the runner. Compared to the cold runner mold, the hot runner mold produces more parts per unit time. To learn more, see our guide on What is a Hot Runner.
The Advantages and Disadvantages of Hot Runner Compared to Cold Running Molds
Some advantages of hot runner vs. cold running molds are:
- Hot runner molds do not need the help of robotics to separate the runner from the mold, unlike the cold runner mold.
- The parts produced by hot runner molds are more precise in their dimensions than those from cold runner molds.
- Larger volumes and sizes of parts can be produced by hot runner molds.
Some of the disadvantages of hot runner vs. cold running are:
- Hot runner molds have higher maintenance costs compared to cold running molds.
- Hot runner molds do not suit some heat-sensitive thermoplastic materials compared to cold running molds.
- It is difficult to make color changes in hot runner molds.
Cold Running Molds Definition and Comparison to Hot Runner
Cold running molds use unheated runners to convey molten thermoplastic material from the nozzle to the mold or cavities. These are made up of two or three plates, depending on the design. When the process is complete, the runner comes out attached to the molded part. A cold running mold is sometimes preferred over a hot runner mold because of the low setup and maintenance cost.
The Advantages and Disadvantages of Cold Running Molds Compared to Hot Runners
Some advantages of cold running molds compared to hot runner molds are:
- Cold running molds accommodate a variety of thermoplastics compared to hot runner molds.
- Cold running molds are cost-effective compared to hot runner molds.
- Cold running molds allow for quick changes in design or color.
The disadvantages of cold running molds compared to hot runner molds are:
- Cold running molds produce more waste than hot runner molds.
- Cold running molds produce parts with lower tolerances than those of hot runner molds.
- The production process of cold running molds is slower than hot runner molds. Therefore a lesser number of parts can be produced via cold running molds.
Attributes | Hot Runner | Cold Runner |
---|---|---|
Attributes Allows quick changes in design or color | Hot Runner No | Cold Runner Yes |
Attributes The high degree of tolerance | Hot Runner Yes | Cold Runner No |
Attributes Works with a variety of thermoplastics | Hot Runner No | Cold Runner Yes |
Attributes High maintenance cost | Hot Runner Yes | Cold Runner No |
Attributes Produces large volume of parts | Hot Runner Yes | Cold Runner No |
Attributes Uses unheated runner | Hot Runner No | Cold Runner Yes |
Attributes Molten thermoplastic or polymer is used | Hot Runner Yes | Cold Runner Yes |
The hot runner mold produces parts with a tighter tolerance than those of a cold running mold. However, when changes in design or color are required, a cold running mold is the best option.
Cost Comparison
Hot runner molds have a higher setup and maintenance cost. It is generally a more expensive alternative to cold runner molds. However, in some cases, the high rate of waste production in cold runner molds counterbalances any potential cost savings. The improper management of waste can raise the overall cost of production.
Speed Comparison
A hot runner mold produces more parts per unit of time than cold runner parts. This is because cold runner molds need to separate the runner from the mold and grind and recycle the runner to avoid waste. In contrast, hot runner molds are not affected by any of these factors, so the lead time is shorter.
Volume Comparison
A larger volume of parts can be produced with hot runner mold than with cold runner molds, as the use of the hot runner eliminates the need to separate the runner from the part. This reduces the cycle time and allows for faster processing of materials.
Materials Comparison
When comparing hot runner vs. cold runner with regard to the types of thermoplastic materials used, it is helpful to realize how negatively hot runner molds impact thermal-sensitive resin or polymers. Materials that are particularly sensitive to heat should not be used in this system. The elimination of the heating element in cold runners makes them compatible with a large number of polymers or thermoplastics including thermal-sensitive options.
How Xometry Can Help
Xometry provides a wide range of manufacturing capabilities including CNC machining, 3D printing, injection molding, laser cutting, and sheet metal fabrication. Get your instant quote today.
Disclaimer
The content appearing on this webpage is for informational purposes only. Xometry makes no representation or warranty of any kind, be it expressed or implied, as to the accuracy, completeness, or validity of the information. Any performance parameters, geometric tolerances, specific design features, quality and types of materials, or processes should not be inferred to represent what will be delivered by third-party suppliers or manufacturers through Xometry’s network. Buyers seeking quotes for parts are responsible for defining the specific requirements for those parts. Please refer to our terms and conditions for more information.
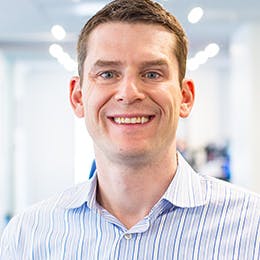