The injection molding industry is very widespread for several reasons. Injection-molded products can be produced in high volumes, at low cost, and using a range of plastic materials. The production volumes and cost per unit cannot be matched by any other manufacturing technology, and as a result, many industries find creative ways to use plastic injection molding. These benefits are all made possible by highly capable industrial injection molding machines. This article will focus on nine of the most common industries in which injection molded parts are used and will describe their use cases and advantages.
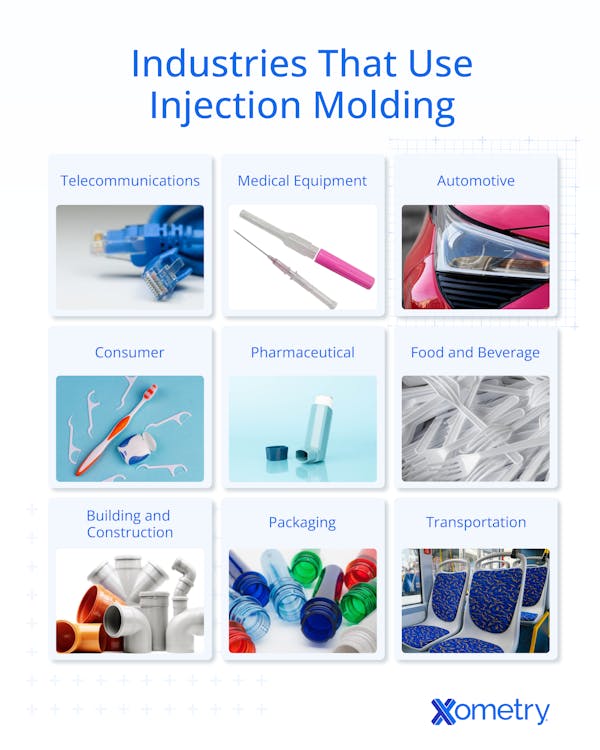
1. Telecommunications Parts via Injection Plastic Molding
The telecommunications industry comprises companies that facilitate communications through technological means. This industry can include companies that make cell phones, landlines, internet equipment, and telecommunications infrastructure such as cell towers and fiber optic cables. Some associated plastic injection molded components include:
- Cell phone bodies and cases
- Wifi router housings
- Cable connections like those on the ends of LAN cables
Our interconnected society demands massive amounts of telecommunication equipment. Injection molding processes’ high outputs help meet this demand. In addition, non-conductive and antistatic plastics can be used to protect sensitive electronics.
2. Plastic Injection Molding Usage in Medical Equipment
The medical industry requires a lot of specialized equipment. Healthcare professionals administer medical treatment using purpose-built devices that meet stringent guidelines. Examples of injection molding applications in the medical industry are listed below:
- Test swabs
- Implants
- Prosthetics
A key advantage of injection-molded plastic products for medical treatments is that production can be quickly scaled up to meet global healthcare demands. The need for COVID-19 test kits made it clear that demand can skyrocket in a hurry.
3. Plastic Injection Molding in the Automotive Industry
Modern automotive manufacturers produce immense numbers of plastic parts, each with careful tolerances. Vehicles are commonly clad in a great deal of plastic and have even more polymer components under the hood and in the cabin. The automotive industry is one of the primary industries using plastic injection molding. Typical applications of injection molding in the automotive industry are listed below:
- Bumpers
- Headlights
- Hose fittings
- Door handles
- Dashboard buttons and switches
Besides cost savings, the key advantage of molding these components from plastic is that they are lightweight and can therefore reduce the total mass of the vehicle. This translates directly into improved fuel efficiency. In addition, injection molded parts can have excellent surface finishes, making them ideal for cosmetic components. Furthermore, these plastic injection molded components are durable and will not rust as with metallic parts.
FREE Injection Molding Design Guide
4. Plastic Injection Molding Usage in Consumer Products
The consumer products industry manufactures a wide array of products for society at large. The items serve functions from entertainment to convenience to hygiene and everything in between. Each one has a specific function. Typical examples of injection-molded plastic consumer products include:
- Kitchen appliances
- Furniture
- Toothbrushes
- Toys
- Wall decorations
Injection molding allows for the manufacture of components in nearly any shape and can create mirror-like surface finishes. These are important factors that help improve the desirability of consumer products.
5. Pharmaceutical Usage of Plastic Injection Molding
The pharmaceutical industry is primarily concerned with the development and manufacture of medications and drugs. Those medications often need plastic accessories such as:
- Drug-eluting devices
- Test tubes and beakers
- Solid oral dosage forms
Injection molded parts can be manufactured from bio-compatible plastics with high levels of inter-part consistency. This consistency is important due to the high levels of precision required by pharmaceutical devices. In addition, injection molding can produce small, complex parts for drug-releasing implants.
6. Plastic Injection Molding for Food and Beverage Purposes
The food and beverage industry is focused on safely delivering food and drinks to customers. Food-safe plastic injection molded parts make convenient containers and utensils. They help prevent cross-contamination during transport and offer simple solutions for takeout restaurants. Below are some examples of food-related applications:
- Utensils
- Container caps and lids
- Food storage
Plastic is especially beneficial in the preparation of foods and beverages as it does not easily react with foodstuffs and keeps these products uncontaminated by outside bacteria or ingredients. In addition, many injection-ready plastics have been approved for culinary use by international standard bodies.
7. Usage of Plastic Injection Molding for Building and Construction Purposes
The construction industry is an umbrella term for businesses that build, maintain, and repair structures. The structures themselves may range from individual houses to huge dams. While concrete is by far the most heavily used construction material, plastic industrial products serve important supporting roles. Some typical injection molding applications within the building and construction industry include:
- Window and door hardware
- Construction tools
- Pipe and electrical fittings
Injection-molded parts are good thermal insulators and help make construction projects more eco-friendly and sustainable when recycled plastics are incorporated, such as for roof tiles or as a filler for concrete. Products made by injection molding are also robust and can easily last the lifespan of the structure.
8. Plastic Injection Molding Usage for Packaging
Disposable packaging makes extensive use of injection molding and injection blow molding. The injection molding process is ideal for the manufacture of thin-walled packaging. Examples of applications are:
- Food packaging containers
- Consumer product packaging
- Bottle blanks
Thin-walled packaging is a lightweight method of protecting consumer products or foodstuffs from damage or contamination. Packaging is typically less than 1 mm thick and is a very effective barrier to outside contamination.
9. Transportation-Focused Plastic Injection Molding
The transportation industry is primarily concerned with the conveyance of large quantities of raw materials through rail, air, or sea. Mass public transportation also falls under the umbrella of the transportation industry. Typical applications of injection molded products in transportation can include:
- Train seats
- Train fairings
- Overage baggage containers
As is the case with the automotive industry, the lightweight nature of plastics can result in tangible fuel savings. This effect gets compounded for cases when the vehicle travels long distances.
How is Injection Plastic Molding Being Used in Industries?
Injection plastic molding is used as a manufacturing tool to achieve very high volume production. In fact, it is only cost-effective at high volumes – between 10,000 and 1,000,000 units. As such, this process is ideal for industries with large customer bases. It can scale easily and produce parts inexpensively with very little waste.
What are the Advantages of Plastic injection Molding?
The advantages of plastic injection molding include:
- Unbeatable low unit cost
- Wide selection of available plastic materials for injection molding
- High rate of production
- Consistency throughout the production run
- Low energy consumption per unit item produced
For more information, see our article on the advantages of injection plastic molding.
What are Injection Molding Companies?
Typical industrial molding companies can manufacture almost any component using a wide range of plastic materials. Some specialize in small plastic molded components such as medical implants, while others focus on large items such as car bumpers. The diversity of the process’ capability explains why there are so many industries using plastic injection molding. Many injection molding companies will also help you understand their DFM (Design for Manufacturing) guidelines for injection molded parts. The guidelines work to assure that the product being produced is of high quality and helps to keep industrial mold prices in check. In addition to DFM guidelines, top injection molding companies handle mold maintenance to ensure mold quality, thereby reducing the overall cost of the mold over the course of its operational lifetime.
Summary
This article provided a look at the use of plastic injection molding across different industries, as well as examples of the types of products that are produced and the advantages of the process.
Xometry offers a full range of injection molding capabilities to help with your production needs. Visit our website to explore the full range of our capabilities or to request a free, no-obligation quote.
Disclaimer
The content appearing on this webpage is for informational purposes only. Xometry makes no representation or warranty of any kind, be it expressed or implied, as to the accuracy, completeness, or validity of the information. Any performance parameters, geometric tolerances, specific design features, quality and types of materials, or processes should not be inferred to represent what will be delivered by third-party suppliers or manufacturers through Xometry’s network. Buyers seeking quotes for parts are responsible for defining the specific requirements for those parts. Please refer to our terms and conditions for more information.
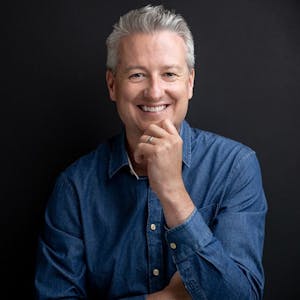