Plastic injection molding is a method used to produce plastic parts at an extremely high rate. As such, it should be no surprise that injection molding is the go-to technology for most plastic consumer products.
The parts of an injection molding machine can be seen below:
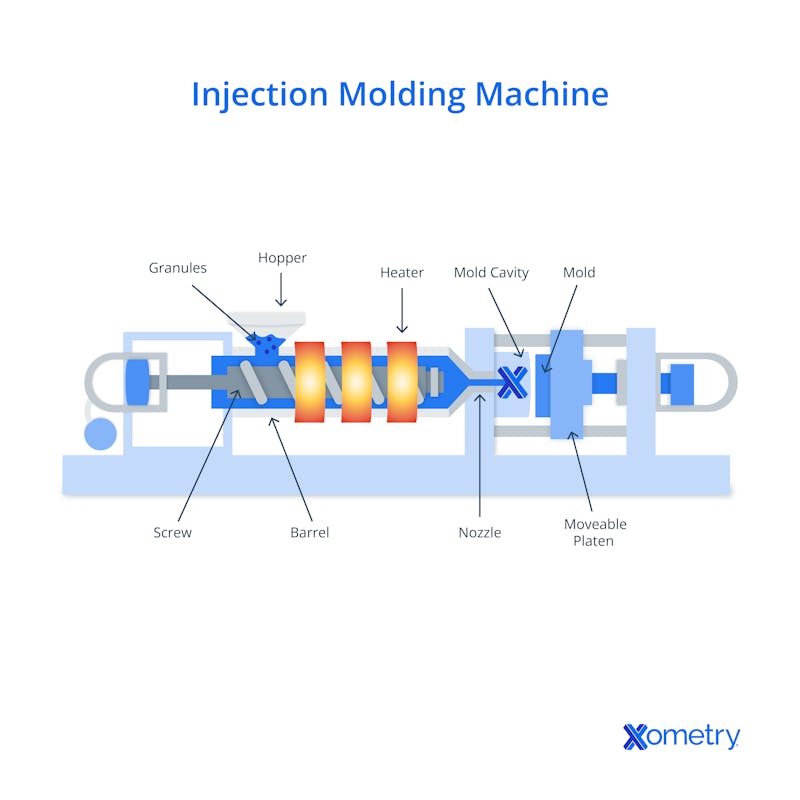
Plastic injection molding advantages include, but are not limited to, the following.
1. Plastic Injection Molding Provides Complex Part Design
Injection molding can handle highly complex parts, provides uniformity, and offers the ability to make millions of virtually identical parts. The effectiveness of high-volume injection molding and maximization of precision and quality of parts means taking key design elements into account.
The part design must be created to maximize the efficiency inherent in high-volume molding. With the ideal design, parts can be made with quality without sacrificing complexity.
2. Plastic Injection Molding Provides High Efficiency and Fast Production
There are a few good reasons that this is the most common and most efficient form of molding. First, the injection molding process is rapid compared to other methods, and the high production output rate makes it even more effective.
The speed is subject to the complexity and size of the mold, but only about 15-120 seconds pass between each molding cycle. With the short period between cycles, more injection molded parts can be produced in a given production time.
3. Plastic Injection Molding Provides Enhanced Strength
The strength and durability of plastics have significantly increased over the years. Modern lightweight thermoplastics can endure even the harshest environments on par with metal parts and, in some cases, may surpass metal.
In addition, there are more than 25,000 engineered materials that can be used for complex injection-molded applications. High-performance plastic blends and hybrids can also be created to meet particular part requirements and characteristics, such as high tensile strength.
4. Plastic Injection Molding Provides Flexibility in Color and Material
The plastic injection molding process provides flexibility. This flexibility can be in such things as the properties of the plastic being used or in the ability for OEMs to make custom color choices to meet specific project requirements. The benefit of plastic injection molding is the freedom in design choices that it affords to OEMs, especially when compared to metal. Many materials can be used.
The molding process can create clear parts or various colors by aligning plastics, additives, and biocompatibility to achieve the wanted coloration. However, when multiple colors are often needed in one product, this can be accomplished using overmolding.
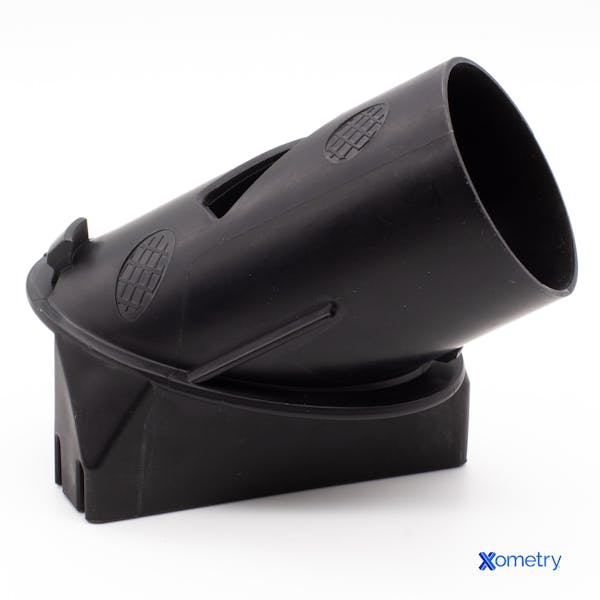
5. Plastic Injection Molding Can Reduce Waste
The plastic injection molding process produces very little post-production scrap relative to traditional manufacturing processes. Any waste plastic typically comes from the sprue and runners. Any unused or waste plastic, however, can be reground and recycled for future use.
6. Plastic Injection Molding Has Low Labor Costs
Labor costs for injection molding operations are relatively low compared to other types of molding processes. The capacity to produce the parts at a very high level with a high output rate helps reduce manufacturing costs through its efficiency and effectiveness.
The molding equipment usually flows with a self-gating, automated process tool to keep operations streamlined and mass production ongoing with minimal supervision.
7. Plastic Injection Molding Provides Multiple Finishes
Most injection-molded parts have a smooth surface finish close to the desired final look. However, a smooth appearance isn’t suitable for every application. Depending on the physical and chemical properties of the plastic material used, the plastic injection molding manufacturing process creates surface finishes that don’t require secondary operations. The process provides finish flexibility, from matte finishes and unique textures to engraving.
8. Plastic Injection Molding Creates Lightweight Products
Although they are most widespread in the automotive industry, OEMs use lightweight plastic injection molded products in many industries. Using plastic parts helps reduce weight compared to the use of metal parts. Today, high-strength, lightweight thermoplastics can replace metal components with virtually no difference in strength or durability, only in weight.
9. Plastic Injection Molding Has the Ability to Use Multiple Types of Plastic
Complex part designs often require components made of different materials. While this may seem simple, safely combining plastics can be tremendously complicated. By guaranteeing compatibility under all circumstances, plastics expertise from the molder’s project engineers mitigates defects, injury risks, and warranty claims.
10. Plastic Injection Molding Provides Consistency
Producing high-output yet complex plastic parts requires a consistent, repeatable process to achieve designs with tight tolerances. The injection molding production process helps ensure consistent quality by continually using the same mold for each part, backed by an injection molder’s continuous improvement practices that incorporate current leading-edge technologies.
11. Plastic Injection Molding Can Create Precision Products
Modern high-speed injection mold equipment that is appropriately maintained allows for the mass production of precision molded plastic parts. For the production of plastic components such as connectors and gears that require high precision production, this molding process is the best choice and offers tolerances as tight as +/-0.0002”.
12. Plastic Injection Molding Provides a Shortened Product Development Timeline
Different skill sets of injection mold engineers can help OEMs achieve a shorter product development timeline. Doing so ensures faster production cycles and getting defect-free parts to market faster — a decided competitive advantage for manufacturers.
This article summarized 12 key advantages of the plastic injection molding process.
About Xometry
Xometry offers a full range of injection molding capabilities to help with your production needs. Visit our website to explore the full range of our capabilities, reach out to us for help with your injection mold design questions, or to request a free, no-obligation quote.
Disclaimer
The content appearing on this webpage is for informational purposes only. Xometry makes no representation or warranty of any kind, be it expressed or implied, as to the accuracy, completeness, or validity of the information. Any performance parameters, geometric tolerances, specific design features, quality and types of materials, or processes should not be inferred to represent what will be delivered by third-party suppliers or manufacturers through Xometry’s network. Buyers seeking quotes for parts are responsible for defining the specific requirements for those parts. Please refer to our terms and conditions for more information.
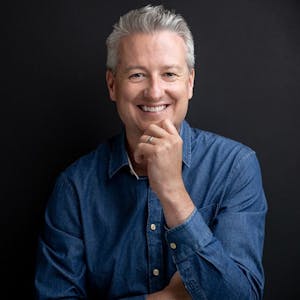