Injection molding is the process of injecting molten material into metal molds at high pressure. The finished part is automatically ejected after it has sufficiently cooled. The process is highly automated and can produce large product volumes, especially plastic parts. Regular preventative maintenance of injection molding tools is required to achieve these large volumes. Mold maintenance is critical to keeping tools ready for production. Poorly maintained molds may create parts that fail to meet specifications, thus causing extra downtime, wasting raw materials, and affecting the bottom line.
This article will describe some key items to include in an injection mold maintenance checklist.
What Are the Basic Mold Maintenance Tips?
The basic mold maintenance tips are ones that are designed to ensure the efficient production of injection molded parts. These tips include preventive maintenance techniques that allow for the identification and correction of injection molding problems before they pose a risk to production. Listed below are some common basic injection mold maintenance checklist items that can be used to extend mold life, minimize injection molding repairs, and maintain consistent part quality.
1. Perform Basic Maintenance Checks Before and After Each Production Cycle.
Before starting a new production cycle, it is important to thoroughly inspect the injection molds. Examine the surfaces of the injection molding die to make sure they are free of plastic or contaminants. Any foreign debris may cause interference when the tool clamps down and cause the plastic to seep into the parting area during mold injection. You should also be on the lookout for anomalous marks or damage on the mold’s surfaces.
It is also good practice to inspect the final part from the previous cycle. This will be a good indicator of the mold’s performance. For example, excessive flash on the parting line may mean that the injection mold cavity and core are not clamping down correctly.
Make sure the shot counter is working correctly. This counter keeps track of the total cycles and indicates when to perform major maintenance activities.
2. Clean the Mold Core and Cavity.
Clean your mold after each production cycle to prevent the build-up of foreign materials. Cleaning can be done with the injection mold tool in the press or on the bench. Press mold cleaning is done after each production run, while on-bench cleaning takes place alongside major injection molding maintenance activities and is not done as frequently. Some resins will foul the molds quicker than others, so your cleaning cycle will depend heavily on the resin used. Wipe down the mold with a standard degreaser or mild solvent using a cotton cloth. Other techniques like dry ice blasting can help you clean the mold in place without leaving any residue.
If the plastic molding tool has been removed from the machine for more extensive maintenance, it must be disassembled, and each part cleaned individually. One of the more efficient methods for doing so is to clean the parts in an ultrasonic bath. This allows you to clean every surface—even cooling channels and mold vents—that are hard to reach. The mold material must be carefully considered as some materials are not conducive to ultrasonic cleaning. In this case, traditional cleaning techniques must be employed.
FREE Injection Molding Design Guide
3. Blow Out Dust, Dirt, and Water With Compressed Air
It is important to remove any dirt or dust that has settled on the mold surface during cleaning. The water used to clean the mold can also leave stubborn scale marks when it dries, especially on highly polished molds. The molds should be dried as soon as possible after cleaning. An injection molding technician can use compressed air to accomplish this. Cooling channels must also be blown dry as water can easily get trapped in these channels.
Anti-rust coatings will make debris like dust or cotton fibers stick to the injection mold die surface. They may later end up on the injection molded parts, so care should be taken to carefully inspect the mold surfaces afterward.
4. Check the Mold's Runners, Sprues, and Other Places
It's important to inspect the quality of the mold runners, sprues, gates, and vents. All these features are critical to efficient production. Wear and material build-up are two of the most common failure modes and can cause parts to stick to the injection molding tools. Molds are most likely to wear at the plastic’s entry gate, so this area should be thoroughly inspected. Make sure there are no plastic buildup or surface blemishes on the runner or sprue, as these may impede the flow of plastic and cause sticking. Scratches from previous attempts to remove stuck plastic can further exacerbate the problem, causing future plastic to stick more easily. Sprues and runners must be cleaned and re-polished if flaws are found. Check that the hot runner nozzle tips are free of burrs.
5. Examine the Mold's Connectors and Hardware
Check all cooling water hoses, pipe connectors, and threads to ensure that there are no leaks. Remove pipes and fittings and clean off any potential build-up of calcium or other deposits. If the mold is not removed, ensure that all the bolts connecting the mold to the platen plates are properly torqued. If the mold is removed, inspect the platen plates for warping and rusting. Dents and burrs on the platen can damage the mold and reduce its effective lifespan. Any small burrs or other defects must be removed with a polishing stone or similar tool. Due to the softer metal of the platen, the mold fastening hole threads can get damaged over time, so these should be periodically checked. The use of a torque wrench is recommended to prevent over-tensioning damage to the threads. Check the platen for any deformation.
6. Before Storing the Mold, Make Sure It's Totally Dry
If the mold is to be stored for an extended period, it must be fully dried and protected beforehand. Moisture can cause corrosion even if the mold is sealed. Drying can be done with compressed air. An additional rust inhibitor is then needed—spray the entire mold to protect it from atmospheric moisture.
7. Make a Note of the Date and Scope of Your Mold Cleanup Efforts
All maintenance activities should follow a maintenance plan and each step should be properly logged. An injection mold maintenance checklist is the perfect place for this logging. Any faults or anomalies must also be listed as these can be used to narrow in on the root causes of any future failures.
What Are the Advanced Mold Maintenance Tips?
Listed below are some more advanced mold maintenance tips that can further expand the useful life of an injection mold.
1. Examine the Mechanics and Ejection Pins
Ejector pins that get bent may not eject parts properly. This condition can cause the part to get stuck in the tool or may damage the part after mold injection. Major maintenance consists of measuring the alignment features and checking them against the mold's original tolerances. Any major deviations will require you to add material and re-machine the mold to put it back within tolerance. On complex multi-part molds, the action of the various mechanisms must be checked, and moving parts must be lubricated and checked for smooth operation.
2. Examine Each Component of the Mold
If you find defects in your parts, it’s tempting to remove the mold tool right away. However, the best idea is to leave it attached until you’ve completed your injection mold troubleshooting. Problems usually stem from a combination of factors, so you want to track them all down. Once the mold has been removed from the machine, it can be disassembled, and each part thoroughly inspected for wear or other damage. All o-rings or sealing elements should be replaced. Cooling channels should be checked for scale build-up or corrosion from acidic water.
Common FAQs on Injection Mold Maintenance
What are the Benefits of a Properly Maintained Mold?
The benefits of a properly maintained mold are that the injection molding process using that mold will create parts of more consistent quality and with fewer major failures. These benefits translate directly into cost savings—you’ll have less downtime and fewer scrapped parts. A thorough preventative maintenance plan is indispensable in modern injection molding facilities.
Does Mold Maintenance Increase the Lifespan of Injection Molds?
Performing maintenance of injection molds will increase the lifespan of the mold. It is important to know that molding costs are dominated by the price of the injection molding tools themselves. A plastic molding tool’s cost is factored into the unit cost of each part being produced. Long-lasting molds mean increased profit per part. The only way to increase the lifespan of an existing mold is to implement a preventive maintenance plan. Your continuous and regular inspections will find and resolve any faults before those result in expensive injection mold repairs and the need to scrap defective parts.
Summary
This article provided a summary of the basic and advanced maintenance steps used to maintain injection molds to assure top performance and maximize the mold's useful life.
Xometry offers a full range of injection molding capabilities to help with your production needs. Visit our website to explore the full range of our capabilities or to request a free, no-obligation quote.
Disclaimer
The content appearing on this webpage is for informational purposes only. Xometry makes no representation or warranty of any kind, be it expressed or implied, as to the accuracy, completeness, or validity of the information. Any performance parameters, geometric tolerances, specific design features, quality and types of materials, or processes should not be inferred to represent what will be delivered by third-party suppliers or manufacturers through Xometry’s network. Buyers seeking quotes for parts are responsible for defining the specific requirements for those parts. Please refer to our terms and conditions for more information.
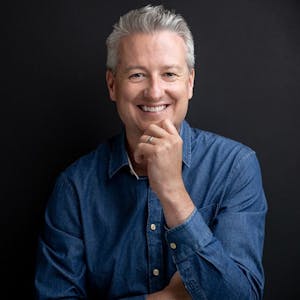