Plastic injection molds last from hundreds to over a million cycles. A plastic injection mold lifespan depends on its environment, maintenance, structure, SPI classification, and other factors.
Factors that affect plastic mold durability include environment, materials, maintenance, molding conditions, and structure design. You can maintain injection molds to extend their lifespans by inspecting, maintaining, and coating the mold, as well as ensuring the mold operates under appropriate conditions. Using SPI classification will help with this. Be sure to avoid part defects including sink marks, surface delamination, flow lines, burn marks, and flashing, since these will damage or indicate damage of the mold.
The Factors That Affect Plastic Mold Durability
Factors that affect plastic mold durability include environment, materials, maintenance, molding conditions, and structure design. Injection mold tool life refers to the total number of molding cycles the mold can be subjected to before it fails. Failure here means any deformation that would affect the quality of the parts produced.
Surface finishes will naturally show signs of wear much earlier than the bulk of the mold.
Certain factors affect the speed at which this wear occurs, both on the surface level, as well as on the general design of the mold. The most important factors can be found below.
1. Environment
Greater environmental cleanliness allows molds to last longer. The conditions a plastic mold operates in can heavily affect not only the health of the mold itself, but also the health of the parts produced. Harsh, dirty environments will lead to a shorter life expectancy because of the additional wear such conditions apply to the mold. On the opposite end of the spectrum, molds used in very clean environments (for example clean rooms) can last decades.
2. Materials
Stronger materials like steel make a plastic mold more durable, while plastic materials used in the mold can also wear it down. Materials the mold is made of can vary depending on the particulars of the injection molding process related to the desired part. Molds made of harder materials, such as steel, will wear down much more slowly than ones of equivalent design made in softer materials, such as aluminum.
When talking about materials, the ones used in the manufacturing process can also play a role in the degradation of the plastic injection mold. Small, intrusive elements (aka impurities) may interfere with the injection mold itself if the machine used to create the mold exhibits some sort of degradation that can alter the structure of the mold. Additionally, the end product (the part) can also be affected by any corrosive or abrasive ingredients used in the molding process. In other words, impurities in the mold can cause issues with the part, if they are not detected beforehand.
FREE Injection Molding Design Guide
3. Proper Maintenance
Proper maintenance enhances mold durability as it expands the mold's lifespan. This is the main tool you can use to make sure the injection mold has as long of a lifespan as possible. It is good practice to plan a schedule where inspections are carried out on the mold. Even if it has to be temporarily taken out of operation to conduct these inspections, one or two days may be worth years of its lifespan in the future. Additionally, all records of the services (cleaning, stripping, etc.) and the repairs done on the mold should be archived, as it may help with detecting possible issues and sources of errors in case defects appear. This bookkeeping can also aid in pinpointing the period in which said defect occurred.
4. Cycle Time and Other Molding Conditions
Slower cycle times enhance plastic mold durability, as does appropriate clamp force. Slow cycle times are generally more helpful in prolonging injection mold life. High-speed production cycles, even though they are necessary in some situations, have a higher chance of introducing defects in the mold. “Faster” settings used to speed up production are another source that could introduce errors. Premature clamp openings or vents and decoupling of pins before the prearranged time are examples of such errors. Excessive clamp force is another problem, introducing the possibility of deformations. Temperature control during the process also helps to lengthen lifespan.
5. Mold Structure Design
Proper mold structure design extends mold lifespan thanks to increased efficiency. This includes designing efficient gating systems and cavities.
Molding components (plates, cavities, etc.) constructed using high-grade tool steel will provide greater wear resistance and superior molded part finishes over components constructed of lesser metals. This aspect is vital to preserving the desired part structure, especially roughness.
For more information on the different injection molding technologies, see our article: What are the types of Injection Molding Technology?
Maintaining Injection Molds To Extend Their Lifespan
You can maintain injection molds to extend their lifespans by making sure the mold meets the part's requirements, using appropriate operating conditions for the mold, periodic cleaning of the mold, periodic inspections of the mold, and using coatings for the mold.
- Make Sure the Mold Meets the Part’s Requirements: This means the core and cavity of the mold should have appropriate hardness (greater than 52HRC, as a reference), so it can be used in the processing of plastic materials.
- Use Appropriate Operating Conditions for the Mold: Make sure to use the mold in the environment and in the processes it was originally planned to operate to ensure there are no additional stresses and wear sources. Using SPI classification will help with determine the appropriate operating conditions of the mold.
- Periodic Cleaning of the Mold: Exact cleaning and maintenance can vary based on the type of mold, but the most common activities include periodic cleaning, finishing, coating, and greasing of the mold. The frequency of maintenance also depends on the resin used in the injection process. For instance, when injecting abrasive resins, such as glass-filled variants, more frequent cleaning and maintenance should be expected.
- Periodic inspections of the Mold: Related to maintenance, visual inspections of the mold in question is the bare minimum when talking about inspections. This can be done as frequently as once every few days. Checking for wear and detecting it in its early stages will save both money and future headaches.
- Using Coatings for the Mold: Coatings can help limit wear and damage to the mold. Using mold coatings has the effect of reducing the need for mold maintenance, reducing part downtime, and improving performance of the mold. Carbon-based coatings are a quite common option, especially for moving parts, due to the lubricity they add to the part. Besides the sliding wear resistance (very useful in the case of ejector pins for example), coatings can help protect against corrosion and seizure.
Mistakes That Reduce the Lifespan of Injection Molds
Injection mold damage can be indicated and in some cases increased by mistakes in the parts being made. These mistakes include sink marks, surface delamination, flow lines, burn marks, and flash. In more detail:
1. Sink Marks
Sink marks are a source of further damage that can be inflicted on the mold, further reducing lifespan. These are small depressions localized in the thicker areas of the mold and are caused by incorrect cooling time. The plastic does not cool sufficiently while it is inside the mold, an issue that is usually related to inadequate pressure inside the cavity or too much heat.
2. Surface Delamination
Surface delamination can decrease mold lifespan by increasing wear over the long term. This issue involves thin layers of materials that appear on the part surface and is caused by contamination with unintended materials or release agents. Adjusting the ejection mechanism may remove the need for the use of release agents.
3. Flow Lines
Flow lines indicate either flow rate problems or bad mold design. Flow lines are patterns or lines that appear on parts. Usually caused by varying flow rates which cause the molten plastic to solidify at different rates, this issue is fixed by adjusting injection speed and pressure in order for the cavity to be filled evenly. In more serious cases, this issue can be a sign of bad mold design, in which case the mold must be redesigned.
4. Burn Marks
Burn marks reduce injection mold lifespan over the long term with the burned material, though the overheating won't directly damage the mold. As the name suggests, burn marks are rust-colored discolorations that appear on injection mold parts and are caused by either the degradation of the plastic material (excessive heating) or inappropriate injection speed.
5. Flash
Flash introduces wear to mold clamps around where extrusion occurs, which can lead to the need for replacement clamps. Flash is a defect that occurs when molten plastic escapes the cavity, creating extrusions that stick to the finished product. Injection speed, pressure, and mold temperature should be adjusted to avoid this. Mechanical inspections of the extrusion part should also be conducted to ensure the problematic region is not permanently deformed.
SPI Mold Classifications Used to Estimate the Expected Life of a Mold
SPI (Society of Plastics Industry) mold classifications estimate the expected life of a mold by indicating how many cycles a mold can perform. The SPI Mold classification encompasses 5 classes of injection mold:
1. SPI Class 101 Mold – Extremely High Volume
SPI Class 101 molds are expected to be used in over one million cycles, which is the case in extremely high production activities. Molds in this category are also the most expensive since they are manufactured with the highest quality material. Some properties of this class are:
- Minimum hardness of tool structure components 28 RC (RC refers to the Rockwell scale, also known as Rockwell Hardness. It’s used as a unit of measure for hardness.)
- Minimum hardness of cavity and cores of 48 RC
- Guided ejection
- Slides (or sliders) should be equipped with wear plates
Note: Wear plates are used to reduce the friction caused by slider movement. Not all injection molding processes involve a sliding mechanism though. A slider (or slide, as these terms are used interchangeably) refers to a sideways movement in the injection molding process used to form complex geometries.
A more complete explanation of how and where wear plates are used can be found here.
2. SPI Class 102 Mold – High Volume
Class 102 molds are expected to be used in medium to high production manufacturing. The number of cycles is expected to be in the range of 500,000 – 1 million. Most properties of class 101 apply here too, with some differences such as plated cavities and corrosive resistant temperature control channels not being mandatory.
3. SPI Class 103 Mold – Medium Volume
Class 103 handles medium-volume production manufacturing activities with cycles under 500,000 and not very stringent requirements, such as:
- Detailed tool design is recommended
- Cavity and cores must have minimum 28 RC
- Tool structure components should have a minimum hardness of 18 RC
4. SPI Class 104 Mold – Low volume
Class 104 is aimed at molds expected to last less than 100,000 cycles, characteristic of low-volume manufacturing. The base of these molds can be made of aluminum and mild steel. The same can be applied to cavities and cores.
5. SPI Class 105 Mold – Prototypes
Reserved for less than 500 cycles, class 105 usually refers to mold prototypes, which are the least expensive type out of this list. They can be manufactured out of cast metal or even epoxy, the focus being the manufacture of mold in the least expensive way possible.
Remember that SPI mold classifications indicate, but do not guarantee, quality. Aluminum molds could last for years and even decades while it is possible for class 101 molds to rapidly decay, due to inappropriate maintenance. Activities that seek to prolong lifespan are of such vital importance to the injection molds regardless of the classification of the molds.
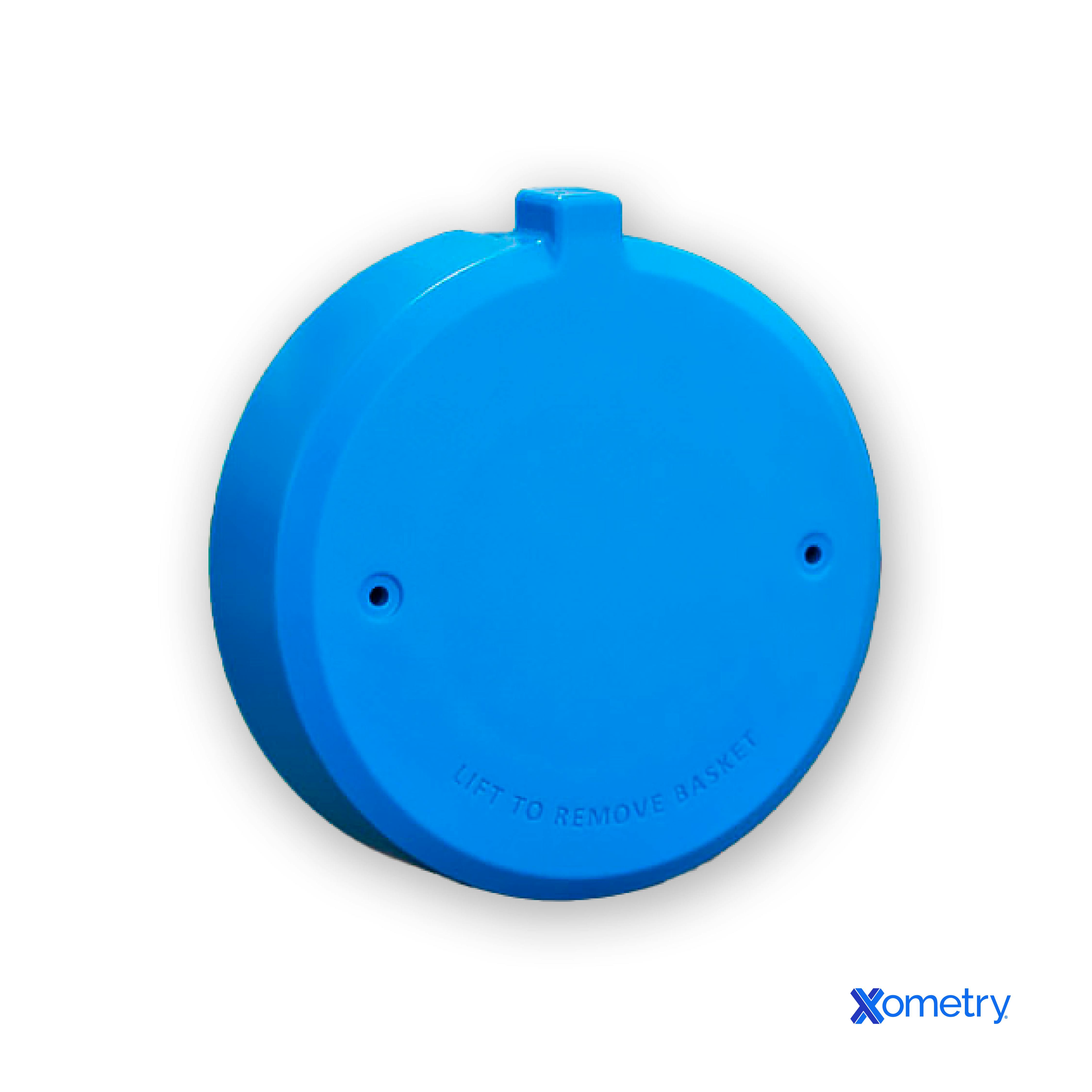
Conclusion
In this article we discussed lifespan of injection molds. The lifespan of injection molds can be affected by factors such as environment, materials, maintenance, molding conditions, and structure design. The life expectancy of injection molds can be extended by making sure the mold meets the part's requirements, using appropriate operating conditions for the mold, periodic cleaning of the mold, periodic inspections of the mold, and using coatings for the mold. The SPI Classifications serve to classify molds based on their optimal operating conditions, but regular maintenance should be performed regardless of SPI Mold Class.
About Xometry Injection Molding Services
Xometry can assist you with developing a long-lasting mold for your injection molded parts. Our Instant Quoting Engine makes it easy to get started: all you need is a 3D CAD model. Our injection molding experts will work with you to understand your needs and take the steps necessary to ensure your mold will last the lifetime of your project.
Disclaimer
The content appearing on this webpage is for informational purposes only. Xometry makes no representation or warranty of any kind, be it expressed or implied, as to the accuracy, completeness, or validity of the information. Any performance parameters, geometric tolerances, specific design features, quality and types of materials, or processes should not be inferred to represent what will be delivered by third-party suppliers or manufacturers through Xometry’s network. Buyers seeking quotes for parts are responsible for defining the specific requirements for those parts. Please refer to our terms and conditions for more information.
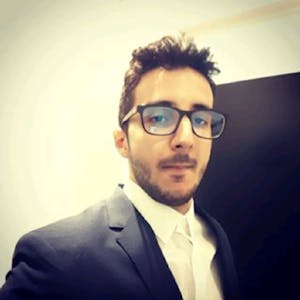