Plastic injection molding uses an injection molding machine, melted plastic material, and a highly designed tool mold to mass-produce plastic parts. However, plastic is not the only material that can be injection molded; this article will show that more and more materials will be able to function in this profitable manufacturing process as technology continues to develop. In present-day industry, injection molding finds a wide range of uses in consumer, commercial, and industrial products large and small, and significantly contributes to the material successes of the modern world. This might seem hyperbolic—but everything from electronics to appliances to cars relies on injection molding to offer highly repeatable, strong, and complex parts.
This article highlights five pretty cool types of injection molding. Each offers a different set of materials and results, as well as cost reductions in specific applications. Each of these types of injection molding technologies comes with its own type of injection molding machine, which is fitted with suitable components for both its intended material and desired end-product.
See the types of injection molding technologies below:
1. Gas-Assisted Injection Molding
In gas-assisted injection molding, a pressurized inert gas (typically nitrogen gas) is injected into the mold right after the molten plastic, forcing the material into the mold walls and leaving a cavity where the gas once was. This gas allows for built-in hollow sections in a mold, but it also promotes cooling and prevents distortions by evening out wall thicknesses, especially in thick walls in an injection mold. Uses for gas-assisted injection molding include material reduction in large parts, hollow products, and other porous designs.
The benefits of this type of plastic injection molding revolve around its ability to reduce material usage and cooling time. The gas pocket will fill thicker sections, resulting in less warping and faster cooling times as the molten plastic flows towards the colder mold walls. The pressure also causes less shrinkage to occur when cooling and minimizes the chance of sink marks from appearing. Gas-assisted injection molding also requires lower clamping forces and overall residual stresses, leading to a more stable injection molding process.
Gas-assisted injection molding does not come without its limitations; it can only really be applied to single-cavity molds, otherwise, the gas channeling becomes too complicated (this is exacerbated if the multiple cavities are unique from each other). Also, some materials may react with the gas or become foggy due to the nature of the gas interfacing with the material's surface. Clear plastics are especially prone to this effect, and so are not usually capable of being gas-assisted injection molded.
Materials commonly used in gas-assisted injection molding are:
- Acrylonitrile butadiene styrene
- Polycarbonate
- High impact polystyrene
- Nylon
- Polybutylene terephthalate
- Polyethylene terephthalate
- Polypropylene ether
- Polypropylene
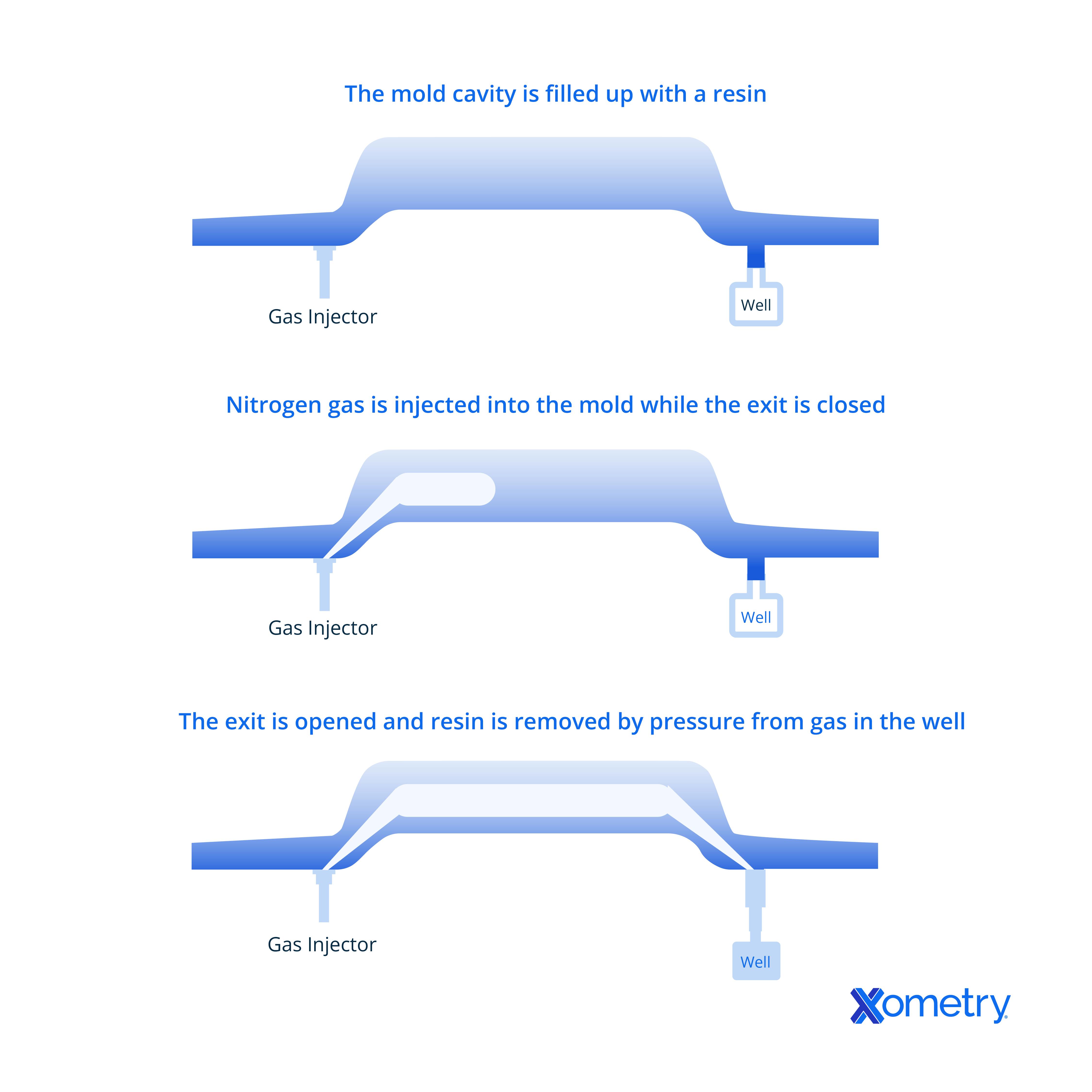
2. Thin-Wall Molding
In thin wall molding, parts maximize material and cost savings by utilizing thin wall thicknesses relative to the part’s overall size. Thin wall molding allows for 1-2mm thick walls that both decrease cycle time but increase needed injection pressure. Specialized thin wall injection molding machines have the highest precision specifications among injection molding machines, as thin-wall molding is often used for small parts. Uses for thin-wall injection molding are small, tight-tolerance applications like electronic parts, enclosures, medical device components, tubing, etc.
The advantages of thin-wall injection molding, as previously mentioned, are cost savings and speed. Thin wall plastic parts require less material, resulting in lower material costs and overall resource consumption when compared to traditional injection molding methods. Cycle time is also drastically reduced, and parts result in fewer emissions from shipping due to their decreased weight. A thin-wall injection mold can also be made of recyclable plastics, and thin-wall parts reduce weight (and therefore emissions) in fuel-based applications like heavy equipment and automotive vehicles.
The disadvantages of thin-wall injection molding are that thin wall injection molds and molding machines are more expensive, and their operation requires trained molding technicians. There is little room for error because thin wall injection molds require extreme precision and low tolerances. Technicians and designers must scour the project for sources of defects and potential optimizations, leading to longer lead times on molds and the overall project. Thin walls also require higher pressures, which means machines must be fitted with stress-resistant components that need to run smoothly over thousands and thousands of cycles.
Materials commonly used in thin wall injection molding are:
- Nylon
- Polypropylene (PP)
- Polyester
- Polystyrene
- Cellulose plastic
- POMs
and other good fluidity plastic material.
3. Liquid Silicone Injection Molding
Liquid silicone injection molding allows for the mass production of silicone rubber products. This type of injection molding is distinct from others in that silicone rubber is technically a thermoset rubber, therefore it will require vulcanization (the process that provides rubber its beneficial material properties like durability and flexibility). Opposite to typical injection molding where molten plastic is injected into a colder mold, cold silicone rubber is injected into a heated mold cavity and vulcanized. This injection molding technology requires specialized equipment such as mixers, metering units, perfectly sealed molds, and other components. Uses include products for sealing applications, connectors, over-molding for other plastic products, infant products, biocompatible medical products, baking equipment, insulating products, and more.
Liquid silicone injection molding has several unique advantages. The material does not require any melting and can be kept in its liquid form, ready to use. Silicone is generally quick to solidify and produces little to no burrs/waste if the machine is engineered correctly. This injection molding technology typically automates the injection process to reduce operator errors and offers a lower risk process as at no point is the material hot except inside the mold. Silicone products are one of the only biocompatible materials and are impressively resistant to chemicals, temperature, and electricity, making them a unique offering from an otherwise thermoplastic-laden injection molding selection.
Liquid silicone injection molding is not perfect; the vulcanization of silicone material is an irreversible process, meaning once a part is set, there is no going back. There is no recycling of silicone products, and if a mistake is made, the material cannot be turned back into stock as with other types of injection molding. Also, liquid silicone requires its own unique equipment that may be more difficult to procure and regularly maintain.
Materials commonly used in liquid silicone injection molding are:
- Standard silicone
- Medical grade silicone
- Resistant silicones
- Optical silicone
4. Structural Foam Molding
Structural foam molding allows for the mass-production of very large parts, thanks to the introduction of a composite material formed from a polymer mixed with an inert gas (such as nitrogen) or a chemical blowing agent. Material is kept separate in liquid state and then mixed inside the mold. The gas/ chemical blower is then added to the mixture, causing a change in the chemical reaction that results in the formation of a low-density, rapid expansion of foam. As the foam expands and cures, the interior retains its high porosity core while the surface interface between the foam and the mold collapses, forming a high-density protective skin on the outside of the part. The resulting injection mold is a lightweight, flexible, and strong foam product. Uses for structural foam molding include car roofs, housings for medical equipment, skis, interior and exterior automotive parts, and other large parts.
The advantages of structural foam injection molding lie in its ability to make large, lightweight, strong, and cost-effective parts. Structural foam parts can expand to the size of car roofs and other large products and use less material thanks to their inherent porosity. Also, this porous nature contributes to weight reduction with no tradeoff for strength; structural foam parts are strong, durable, and up to 8 times stiffer than solid polymers. Structural foam injection molding is easy to mold, as it easily conquers variable thickness walls, experiences less stress during the process, is resistant to warping, and has a lower incidence of damaging molds and machines. Structural foam parts are also quick to produce, easily painted, and are largely unaffected by temperature differentials.
The disadvantages of structural foam molding are mainly a result of the foam material, as surface finishes are rough, wall thicknesses cannot be under ¼ inch thick, and generally require more post-processing than other types of injection molding. Also, structural foam molding has lower production speeds than other injection molding techniques.
Materials commonly used in structural foam injection molding are:
- Polyurethane
- Polycarbonate
- Polyphenylene oxide (Noryl)
- Polybutylene terephthalate
- Acrylonitrile butadiene styrene
and other plastic materials that can work in a foam.
5. Metal Injection Molding
Probably the newest and most unique type of injection molding, metal injection molding allows for the production of injection-molded metal products. In the process, metal powder and binder are mixed and granulated. This so-called “feedstock” is then shot into an injection unit, where the raw product is molded. After molding, the part is cleaned in a solvent and thermally debonded of its binder material, leaving behind a fully metal (yet still porous) product. The debonded product is further strengthened in a sintering oven where metal particles coalesce into a solid matrix (typically under vacuum to reach high solid density), and the part is then ready for additional post-processing procedures like finishing, heat treatment, etc. This process is used to mass-produce small (<100g) metal components in a single step such as hand tool heads, mechanical components, linkages, automotive and aerospace parts, and more.
Metal injection molding has the advantage of being able to create metal parts that were previously impossible to produce using more traditional methods. Also, a high volume of parts can be molded in one step, which can rival the more common casting process for small metal parts. It also offers high fidelity features for the final product such as knurling, holes, and other fine details. Wall thicknesses can be made with narrow dimensional tolerances (hundreds of micrometers) and there is virtually no waste (a significant benefit when compared to all other metal manufacturing techniques).
The major downside to this injection molding technology is that it is somewhat expensive and limited to lower volumes and sizes of parts. The equipment needed for metal injection molding is quite expensive, and so far, the uses of metal injection molding are in high-end applications requiring incredibly complex and detailed metal parts.
Materials commonly used in metal injection molding include:
- Stainless steel
- Tungsten carbides
- Various alloys
- Cobalt-chrome
- Titanium
- Nickel super alloys
- Molybdenum-based metals
- Composites
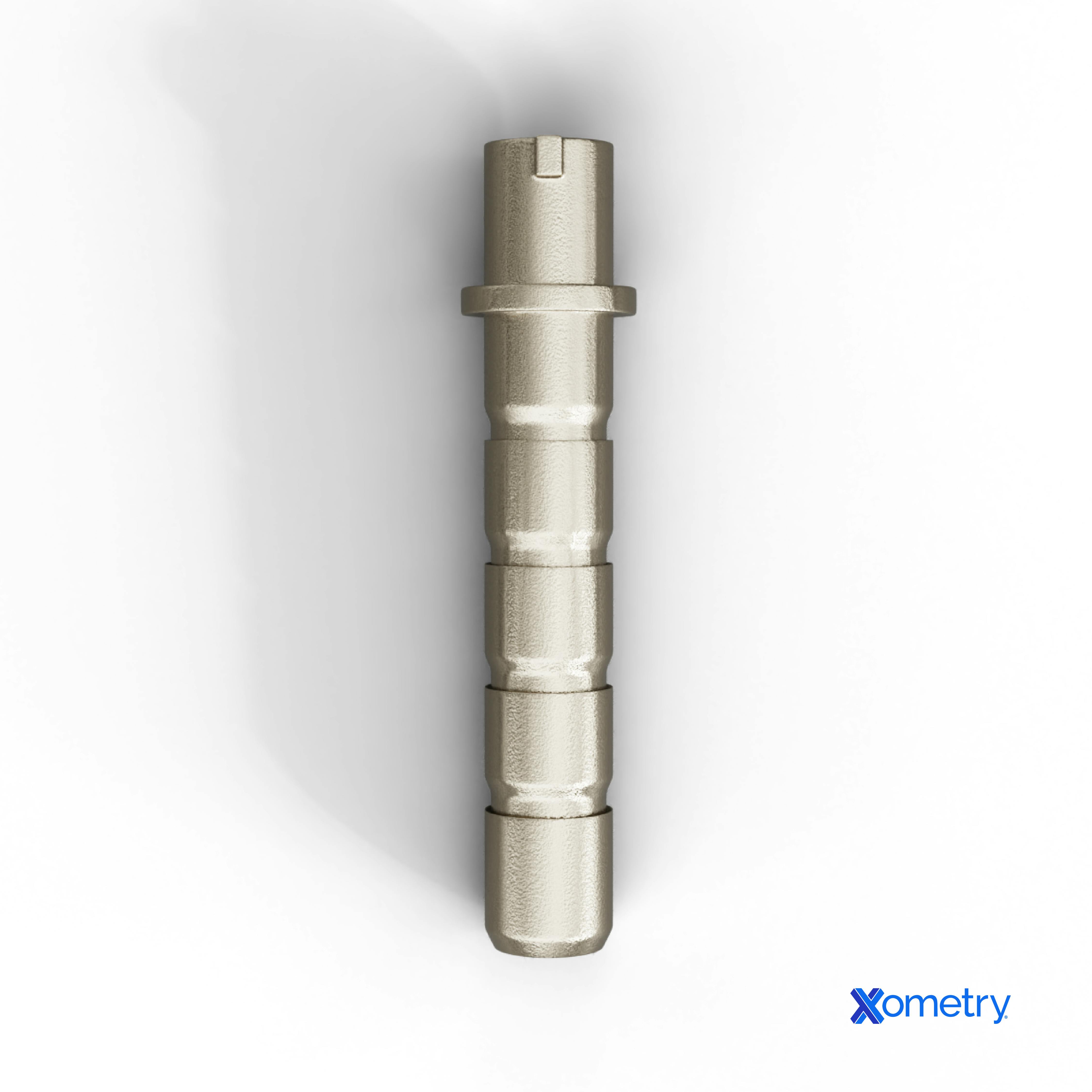
Applications of Injection Molding
Plastic injection molding is used throughout industry as a means of manufacturing plastic parts in high volumes. Its applications are theoretically endless given the various types of injection molding available combined with its popularity. Still, there are some core usages for which the injection molding process particularly excels. Examples of injection molding applications include (but are not limited to):
- Automotive components
- Food and Beverage packaging
- Stock materials (spools, bar, tube, etc.)
- Toys and figurines
- Furniture components
- Fixtures and fasteners
- Mechanical components (gears, valves, pumps, linkages, etc.)
- Electronic hardware and housings
- Medical device components
- General plastic parts
Regardless of specific application, injection molding is a highly effective, low waste, low-post processing procedure. Most parts are ready for use right out of the mold, and if they are not, it will only take minor post-processing steps to get them finalized. The turnover rate of injection molding is truly impressive, with thousands to tens of thousands of parts molded in a typical workday (depending on design). Injection molding is widely distributed throughout the industry because of its effectiveness, where it brings high volume, high repeatability, and high reliability to manufacturers, which ultimately results in steady profits over the long term.
Advantages of Using Injection Molding Technologies For Part Production
The advantages of using injection molding technologies are:
- Injection molding is incredibly cost-effective, especially in high-volume applications where thousands to tens of thousands of parts are printed in a workday.
- Injection molding offers many different materials, both general use, and specialty.
- Injection molding provides immense design freedom to product developers and is only held back by mold design, material specifications, and cost.
- Injection-molded parts can be as small as a grain of rice (or smaller) or can be as large as a car dashboard, depending upon the specific type of injection molding being used.
- Injection molding can produce highly complex parts that would otherwise be too time-consuming or difficult to produce with traditional subtractive manufacturing methods.
- Injection molding is a low/no waste manufacturing method, and waste can typically be 100% recycled and reground into stock material for a new injection mold.
For more information, see our article on Advantages of Injection Molding.
Types of Machines Used in Injection Molding
The machines that are used in injection molding technologies may be characterized into three main types:
- Hydraulic machines: Hydraulic machines were the first type of injection machines developed and are principally powered by hydraulic drives. They offer large clamping forces and are the most conventional injection molding machines with various new and used markets available for machines and parts. Hydraulic injection molding machines are typically used for thick-walled, large-scale applications for the automotive and heavy industries.
- Electric machines: Electrical machines (also known as all-electric or servo machines) are driven by servo motors and offer unparalleled control on all axes. They are an update to hydraulic models and are more energy-efficient, cleaner, accurate, and quieter. They are more expensive to purchase and repair but last longer on average than hydraulic models. Electric injection molding machines are commonly used in cleanroom applications for small to medium-sized parts for biomechanical, pharmaceutical, and medical device products.
- Hybrid machines: Hybrid machines use a combination of hydraulic and electric machine technology to provide the best of both systems. Their clamp forces are higher than all-electric models, but their control and accuracy are better than purely hydraulic machines. Their efficiency, reliability, controllability, and maintenance requirements are on par with or better than either of the previous machines. While more expensive and more challenging to operate and repair, hybrid injection molding machines are quickly gaining traction and lowering in price. Their applications include high-volume production of medical products, heavy equipment, and general and industry-specific uses in small and large sizes.
Summary
Xometry provides a wide range of manufacturing capabilities including CNC machining, 3D printing, injection molding, laser cutting, and sheet metal fabrication. Get your instant quote today.
Disclaimer
The content appearing on this webpage is for informational purposes only. Xometry makes no representation or warranty of any kind, be it expressed or implied, as to the accuracy, completeness, or validity of the information. Any performance parameters, geometric tolerances, specific design features, quality and types of materials, or processes should not be inferred to represent what will be delivered by third-party suppliers or manufacturers through Xometry’s network. Buyers seeking quotes for parts are responsible for defining the specific requirements for those parts. Please refer to our terms and conditions for more information.
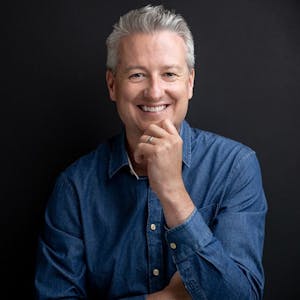