There are a lot of different ways to create a plastic part, but some methods get grouped together, whether it’s because the parts they can make are similar, their processes work in a similar way, or because they are good alternatives for one another. In the world of plastic design, injection molding often gets weighed up against thermoforming.
While you can draw a few similarities between the two, each has its differences and reasons for why you’d want to make a product with thermoforming versus injection molding. We’re going to look at how each works and where their strengths and weaknesses lie.
What Is Injection Molding?
One way you can go about making a plastic part is through a process called injection molding, which relies on a specialized machine to form molten material inside molds with multiple cavities. It works by pouring plastic pellets into an injection barrel, which will then get heated until molten. Once it reaches this ultra-hot temperature, the liquid mixture gets funneled into the molds, where pressure forms it into tight shapes, and then it will cool.
Once the products are cool, they’ll be removed and sent on to whatever future they have in store. Initially, this kind of manufacturing process was made to create small things like combs and buttons, but now it’s an enormously popular choice for a large range of items. It’s also super cost-effective when it comes to large production orders.
In the diagram below, you can see each part of an injection molding machine.
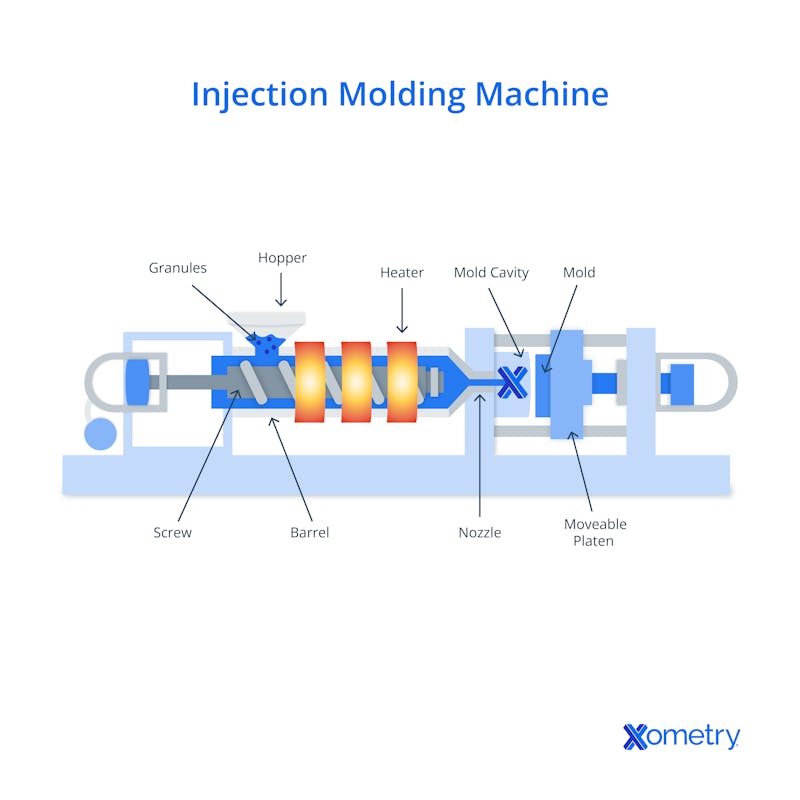
What Is Thermoforming?
Rather than pellets, this kind of plastic manufacturing technique uses sheets that are pressed into a single-sided mold to create products. These machines also use pressure to ensure the sheet fills out every bit of the mold, and vacuum forming, in particular, makes sure there are no trapped air bubbles.
Thermoforming started out by using cellulose sheets to create harder materials, and nowadays it’s a go-to choice for everything from large-scale products (like bathtubs) to smaller containers and toys.
You can see a diagram of a thermoforming machine below and what the process looks like.
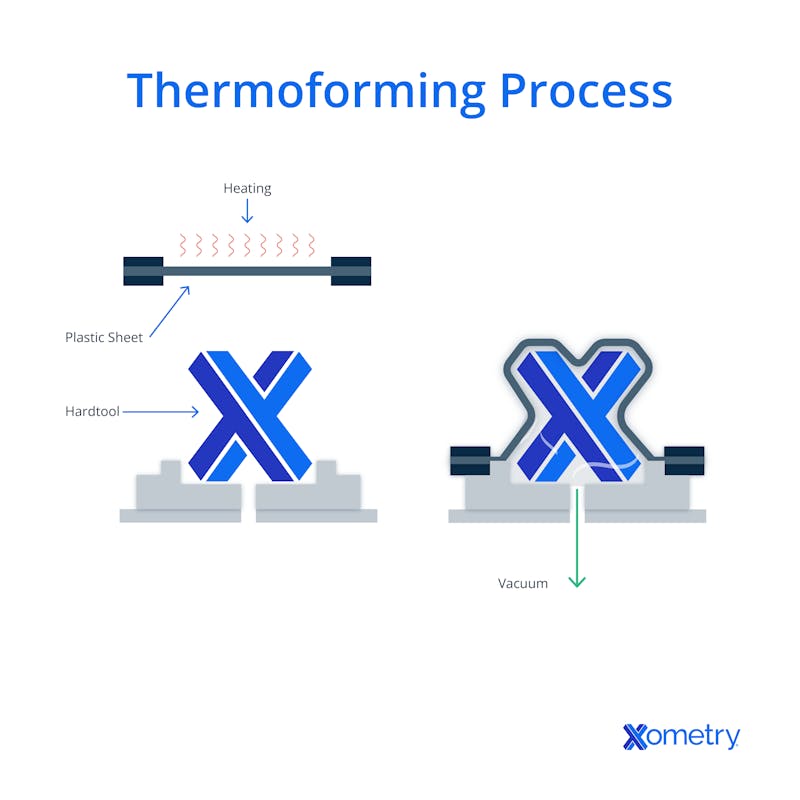
Attribute | Injection Molding | Thermoforming |
---|---|---|
Attribute Can you have high-volume production | Injection Molding Yes | Thermoforming No |
Attribute Can make small detailed parts? | Injection Molding Yes | Thermoforming No |
Attribute Can make large parts with big tolerances? | Injection Molding No | Thermoforming Yes |
Attribute Does it have low tooling costs | Injection Molding No | Thermoforming Yes |
Attribute Are processes repeatable? | Injection Molding Yes | Thermoforming Yes |
Attribute Applications | Injection Molding Gears, bottle caps, packaging, one-piece furniture, toys, bottles, consumer electronics | Thermoforming Toys, bathtubs, bottles, agricultural products, appliances, light fixtures, trays, instrument panels, displays, food containers, ducts, windshields for boats |
Attribute Waste levels | Injection Molding Minimal waste | Thermoforming Pretty wasteful since incorrect parts will have to be redone and may take several rounds |
Attribute Materials | Injection Molding Various plastics in pellet format (polyethylene, polycarbonate, and PVC as examples) | Thermoforming Various plastics in sheet format (polyethylene, polycarbonate, and PVC as examples) |
Attribute Production speed | Injection Molding Capable of rapid production | Thermoforming Capable of rapid production (final product design is faster because it’s easier to change the tooling with thermoforming) |
Attribute Volume | Injection Molding Higher production volume than thermoforming, especially with molds that have more cavities | Thermoforming One part per molding cycle |
Injection Molding vs. Thermoforming Attributes
What are some good alternatives to injection molding and thermoforming?
Blow molding and extrusion molding are great alternatives if you’re after a replacement for the likes of injection molding and thermoforming. They can also whip up plastic products in large quantities, and you can repeat the process with ease. Blow molding is superb for containers and bottles, whereas extrusion molding is a good choice if you’re after weather seals, pipes, and door frames, which are easily made with extrusion molding.
How are injection molding and thermoforming similar?
Injection molding and thermoforming have quite a lot of differences, but you’ll find they’re similar in two main ways—they both use thermoplastics, and you can repeat processes without too much struggle when you’re making high-quality parts.
Is injection molding or thermoforming more expensive?
Injection molding tends to be more expensive than thermoforming. That’s because thermoforming has lower tooling costs and cheaper parts since it won’t experience the same pressure levels as injection molds. Injection molding machines need components made of quality materials like P20 or H13 steel, and tooling can be more complex.
How Xometry Can Help
Producing plastic parts is more than possible at Xometry, and we have a long list of manufacturing services you can get instant quotes for depending on your needs, including for plastic injection molding and customized services like thermoforming. Take a look at our plastic 3D printing, plastic extrusion, and plastic laser cutting pages for more information.
Disclaimer
The content appearing on this webpage is for informational purposes only. Xometry makes no representation or warranty of any kind, be it expressed or implied, as to the accuracy, completeness, or validity of the information. Any performance parameters, geometric tolerances, specific design features, quality and types of materials, or processes should not be inferred to represent what will be delivered by third-party suppliers or manufacturers through Xometry’s network. Buyers seeking quotes for parts are responsible for defining the specific requirements for those parts. Please refer to our terms and conditions for more information.
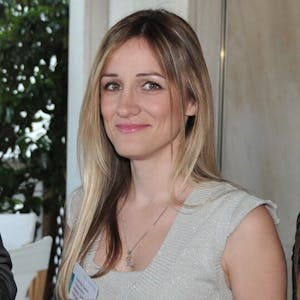