Chromic acid anodizing is an electrochemical treatment used to provide aluminum (and other metals) with an attractive, long-lasting, corrosion-resistant oxide finish. While titanium and magnesium can also be used, aluminum is the best nonferrous metal for anodizing because it is the easiest material to anodize.
Anodizing is divided into three primary types: Type I (chromic acid anodizing), Type II (sulfuric acid anodizing), and Type III (hard anodizing/hard coat). This article will discuss Type I (chromic acid) anodizing, which was the first anodizing technique developed. It is also known as the Bengough-Stuart procedure. Of the three anodizing methods, Type I anodizing produces the thinnest film layer, making it ideal for precision parts. Typical film thickness from chromic acid anodizing is in the range of 0.03-0.1 mil (0.08–0.25 µm). Chromic acid anodizing finds application mainly in the aerospace and defense industries.
What Is Chromic Acid Anodizing?
Chromic acid anodizing, or Type 1 anodizing, is an electrochemical process that is used as a protective treatment for aluminum. During this process, chromic acid is used to form an amorphous, corrosion-resistant layer of aluminum oxide. This is achieved by passing a current through the parts to be coated, which are attached to the anode and placed in an electrolyte of chromic acid.
Chromic acid anodizing produces the thinnest surface oxide layer of the three principal anodizing methods. In spite of this, Type 1 anodized coatings are as effective at protecting the aluminum from corrosion as the thicker Type II and Type III coatings, when properly sealed.
For more information, see our guide on Anodizing.
What Is the Purpose of Chromic Acid Anodizing?
Chromic acid anodizing produces a finish on aluminum that protects it from oxidation and corrosion in both atmospheric and saltwater environments. Anodizing, as opposed to other finishes, enables aluminum to keep its metallic appearance. The process also offers improved scratch resistance and durability which adds to the longevity of the material. Overall, the process significantly increases the lifespan of the material.
Where Is Chromic Acid Anodizing Used?
Chromic acid anodizing is largely employed in the defense and aerospace industries, as well as in other fields where subsequent painting, adhesive bonding, or crack detection is necessary. Applications include:
- Components used in the defense industry, particularly those that use explosives, propellants, or pyrotechnics that require the total removal of electrolytes for safety reasons.
- Preparation for painting, particularly in aerospace applications.
- Components with tiny blind holes.
- Landing gear
- Precision machinery.
How Does Chromic Acid Anodizing Work?
Chromic acid anodizing is an electrochemical technique that uses a controlled level of DC electrical current and a chromic acid electrolytic solution to oxidize the aluminum surface and generate a thin, dense, flexible, and hard coating of aluminum oxide. The process is used to speed up the natural oxidation process of the metal to protect the metal’s surface.
High levels of oxygen are released at the surface of the aluminum as a result of the passage of the electrical current. This assists in the controlled production of the oxide layer. These procedures convert the surface aluminum to aluminum oxide, which is referred to as metal oxide adhesion. This process creates an oxide film that is typically dark gray in color and somewhat thin.
To anodize a component, it has to be connected to the positive terminal (anode) of an electrical circuit. The component should then be placed in the chromic acid bath. The chromic acid will then dissociate, or ionize, into positive and negative ions, as seen in the equation below:
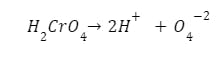
Chromic acid anodizing formula.
Typically, The cathode is then connected to a metal electrode (sheet or wire), submerged in the acidic bath.
The working principle of chromic acid anodization is as follows: when a voltage is supplied to the circuit, the aluminum part draws negative oxygen ions from the solution. The cathode draws positive ions from the aluminum. The surface of the part becomes porous as positive aluminum ions are released from it. The part then interacts with the negative oxygen ions to form an aluminum oxide coating/film.
What Are the Benefits of Chromic Acid Anodizing?
The benefits of chromic acid anodizing include:
- Anodizing is cheap.
- The coating thickness is below 5 μm.
- Resistant to corrosion in saltwater and atmospheric environments.
- The dielectric aluminum film makes it a good choice for electrical insulation.
- The rough oxide surface provides a chemically active surface for painting.
- Adhesive bonding capability is enhanced by providing a rough surface for the glue to stick to.
- Can be used to protect welded parts and assemblies.
- Chromic acid anodized films are durable and scratch and corrosion-resistant.
What Are the Limitations of Chromic Acid Anodizing?
The following are some of the limitations of chromic acid anodizing:
- Chromic acid-anodized coating is limited as a decorative finish because it absorbs less color when dyed compared to other anodizing methods.
- Touch-ups of damaged sections can be more visible compared to air-dry paint touch-ups of painted surfaces.
What Are The Materials Needed To Perform Chromic Acid Anodizing?
The following materials are required to perform chromic acid anodizing:
- Power Source: A power source is needed to generate the electric current required for the electrochemical reaction to take place.
- Chromic Acid Bath: Chromic acid is used as the electrolyte.
- Aluminum Parts To Be Anodized: These parts form the anode when placed in the acid bath.
- Distilled Water: This is used to rinse parts after pre-treatment.
- Degreaser: This is used to pretreat and clean parts before anodizing.
- Acid Neutralizer: This is used to neutralize the acid after the anodizing step.
- Lye: Lye is used for stripping anodized aluminum.
- Cathode: Metal plates or wires are used as a cathode.
How Long Will Chromic Acid Anodizing Last?
A chromic acid-anodized surface should last at least 10–20 years, depending on the anodized layer’s thickness and porosity.
How Long Does It Take To Perform Chromic Acid Anodizing?
Chromic acid anodizing, and anodizing in general, is not a very time-consuming process. From start to finish, the process can be completed in under 1 to 2 hours, including the pre-treatment of the metal and finishing the process by sealing the aluminum oxide coating. In the coating step, the processing time is mainly determined by the coating thickness. Since Type 1 anodizing has the thinnest coating thickness (below 5 μm), the coating can be performed in only a few minutes.
Are Chromic Acid Anodized Materials Prone to Rust?
No, chromic acid-anodized materials are not prone to rust. Aluminum, in particular, does not rust, but it can oxidize or corrode. Chromic acid anodizing is performed to protect the metal against rust. However, despite the fact that anodizing results in a very regular and homogeneous coating, corrosion can nevertheless occur in the coating's microscopic fissures. Additionally, the coating is prone to chemical dissolution in the presence of low and high-pH service environments, which can cause the coating to be stripped off and the substrate to corrode.
Is Chromic Acid Anodizing Permanent?
No, chromic acid anodizing is not permanent. Because anodize literally "grows" out of the base aluminum alloy, it is fairly permanent and durable. However, it can be worn off and removed with an acid wash. It can also be worn away during any sliding contact with other surfaces.
Are Chromic Acid-Anodized Materials Conductive?
No, chromic acid-anodized materials are not conductive. Chromic acid anodizing produces an electrically non-conductive surface with increased scratch and corrosion resistance.
Summary
This article presented chromic acid anodizing, explained what it is, and discussed when it's used and how it works. To learn more about chromic acid anodizing, contact a Xometry representative.
Xometry provides a wide range of manufacturing capabilities and other value-added services for all of your prototyping and production needs. Visit our website to learn more or to request a free, no-obligation quote.
Disclaimer
The content appearing on this webpage is for informational purposes only. Xometry makes no representation or warranty of any kind, be it expressed or implied, as to the accuracy, completeness, or validity of the information. Any performance parameters, geometric tolerances, specific design features, quality and types of materials, or processes should not be inferred to represent what will be delivered by third-party suppliers or manufacturers through Xometry’s network. Buyers seeking quotes for parts are responsible for defining the specific requirements for those parts. Please refer to our terms and conditions for more information.
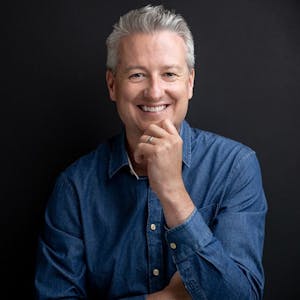