You’ll be hard-pressed to find a construction site, automotive factory, electronics facility, or medical manufacturing plant that doesn’t rely on a computer numerical-controlled cutting router or mill (or a whole row of them). Otherwise known as CNC routers and CNC mills, these machines play vital roles when it comes to creating accurate components and customized design work.
If you’re curious about the difference between the two machines, we’ve broken down how each works and where their strengths and weaknesses lie. You’ll also learn more about the services Xometry offers in the arena of CNC milling & routing.
CNC Routers and How They Work
When you need to shape soft metals, plastic, and wood, a CNC router may be the perfect machine for the job. These swift tools are operated through settings that you’ll input into a computer before it jumps into action.
The rotating tool on the machine is usually moved around using three or more axes. These are usually X, Y, and Z axes. As it runs, it works from G-code that is generated via software and CAD, which commands the cutting tool to move along and carve a workpiece sitting atop the work table into the design that matches a corresponding 3D CAD model. The more axes, the more complex maneuvers it can make. It’s a wonderful example of automation that spans numerous sectors — whether you’re a furniture designer or a manufacturer working on billboards or signboards.
You can also use various tools with a CNC router for different effects, finishes, and angles, like face mills, drill bits, end mills, V-bits, chamfer bits, and ball nose end mills. Xometry also offers resources that’ll help you better understand machining design, including a guide that covers all there is to know about CNC routers.
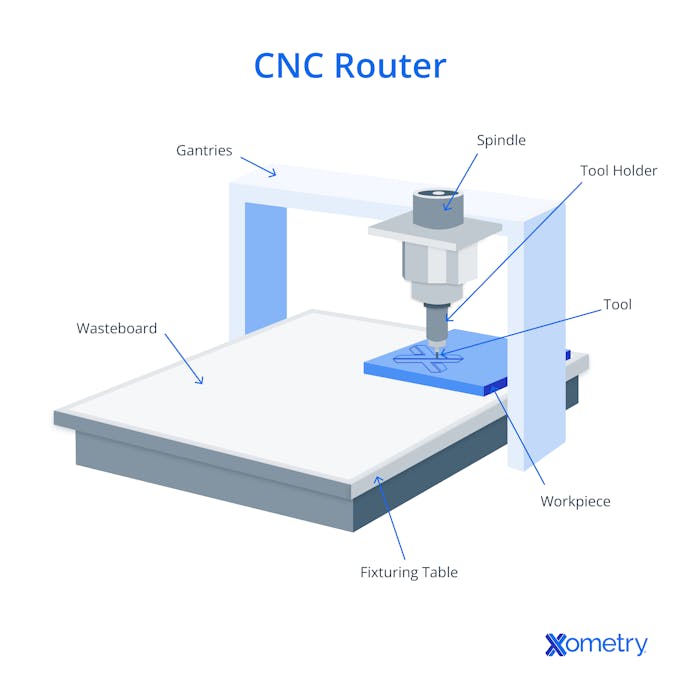
Materials for CNC Routing
CNC routers aren’t as strong as CNC mills, and specific materials, including plastic, wood, and softer metals like aluminum and brass, are better reserved for these machines. Using the wrong material can lead to a damaged machine, unworkable parts, or, worst case, safety hazards.
Applications
Xometry and its manufacturing facilities can use CNC routers to create things like:
- Furniture: including legs, shelves, doors, ornamental carvings and cabinetry.
- Advertising tools: signboards and logos can be created with a router.
- Musical instrument parts: including bodies for guitars and violins.
- Prototypes: for folks in architecture, construction, and engineering who need detailed models.
Advantages and Disadvantages
There are several advantages that a CNC router provides. Here are a few you should note:
- High accuracy: CNC routers can whip up top-tier, accurate designs in less time than manual methods. The standard numerical tolerance level for a CNC router is ± 0.005 inches or 0.13 mm.
- Complex and intricate designs: Even basic CNC routers are great for crafting intricate designs that require relief sculpting, such as a 2.5D topographical terrain model. More advanced machines can go further and reach more complex angles to create things like sculptures.
- Less waste: Because you can specifically program where the router makes its cuts, they are more efficient, and less waste is created than with manual methods.
- Space-saving design: CNC routers are usually more compact than other machines that provide similar services, making them a great addition to workshops that have space considerations to make.
Along with advantages, a CNC router comes with several disadvantages, too:
- Noisy machines: The vacuum and extraction systems, as well as the spindle movement, lead to a loud operation, so be sure to wear hearing protection.
- Dust creation: Even with their extraction systems, CNC routers can still produce quite a lot of dust, so put measures in place to manage this.
- Less accurate than mills: While they can be accurate, CNC routers don’t provide the same level of accuracy and detail that mills can achieve.
- Depth of cuts is shallower: CNC routers can’t get the same level of depth in their cuts as mills do.
- Material limitations: It’s best to use softer materials with CNC routers, as routers can’t safely and effectively slice through harder workpieces.
CNC Mills and How They Work
Mills are another machine you’ll come across in the world of CNC machines, and they’re well known for their ability to cut through tougher materials and create more precise features and finishes. It’s also a helpful machine when you’re working on larger-scale projects or need to reproduce components quickly.
Like a router, a CNC mill works by running a spinning cutting tool on several axes across raw material. A combination of CAD and CAM software is used to create the G-code and toolpaths that the machine uses to create parts.
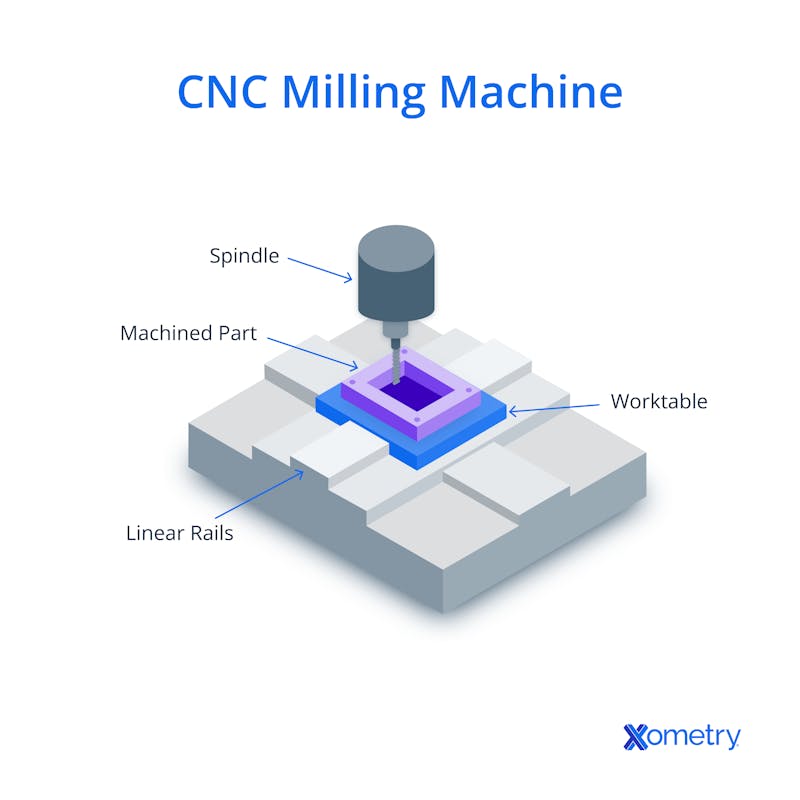
Xometry also has CNC milling services, which include rapid prototyping in a range of plastics, metals, and other materials you can choose from, precision machining at industry standards, design feedback, and advanced capabilities (for all those five-axis and right-angle milling needs).
Materials for CNC Milling
CNC mills can slice through soft materials like butter, but their real specialty lies in tougher materials that CNC routers can’t get through. These hard materials include tool steel, stainless steel, titanium, Inconel, composites, ULTEM, brass, and copper.
Applications
There are many uses for why you’d want to use a CNC mill. Here are a few Xometry has helped its customers with:
- Automotive parts like cylinder heads, camshafts, control arms, rotors, intake manifolds, and more.
- Medical devices such as surgical tools, implants, and prosthetics.
- Aerospace parts like landing gear, housings, customized fasteners, and brackets.
- Tooling, such as molds for injection molding and die-casting.
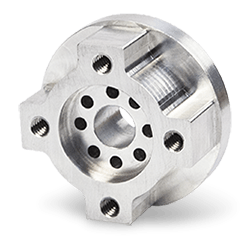
Advantages and Disadvantages
If you’re considering working with a CNC mill, here are some of the best benefits of doing so:
- Extremely precise: CNC mills can cut with very high accuracy and create precise parts you won’t be able to get as easily (or if at all) from a router. Xometry often mills parts with feature tolerances of +/- 0.001" or less.
- More material opportunities: CNC mills have the power, speed, and adaptability to remove chunks from tougher materials. Routers simply don't have the horsepower or tooling options to cut tough and hard materials.
- Easy automation: You can automate the production and processes for a CNC mill, leading to far less manual labor for you or your team. For example, some of Xometrys manufacturing partners use robotic pallet loaders to achieve lights-out production.
- Deeper cuts: With a CNC mill, you can create deeper cuts and up spindle speeds to improve the material removal rate.
There are also a few disadvantages that come with working with a CNC mill:
- Expensive upfront costs: CNC mills are far more expensive than CNC routers, and you’ll be looking at several thousand dollars to purchase one on the lower end. They can cost up to $150,000 or more, whereas routers can start around a couple hundred dollars.
- Skilled operators are required: CNC mills, especially ones with more than three axes, are complex machines. Running them requires proper training and experience to unlock their full capabilities.
- Larger footprint: Although desktop size machines exist, CNC mills generally require more square footage than routers do. They may also have higher energy requirements, such as 240V to 400V+ three-phase connections.
How Xometry Can Help
Our in-house and global manufacturing network allows us to offer virtually limitless potential when it comes to CNC projects. From quick turnaround one-offs and prototypes to higher volume production runs using parallel production to 5-axis milling and more, we have the solutions to meet your project's needs.
Best of all, we can automatically quote most CNC projects instantly. You can start by uploading your 3D CAD files to the Xometry Instant Quoting Engine® to get your instant quote today!
Disclaimer
The content appearing on this webpage is for informational purposes only. Xometry makes no representation or warranty of any kind, be it expressed or implied, as to the accuracy, completeness, or validity of the information. Any performance parameters, geometric tolerances, specific design features, quality and types of materials, or processes should not be inferred to represent what will be delivered by third-party suppliers or manufacturers through Xometry’s network. Buyers seeking quotes for parts are responsible for defining the specific requirements for those parts. Please refer to our terms and conditions for more information.
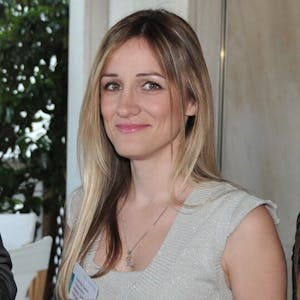